Chances of this wall assembly having any issues?

I’ve been working full time on a new construction build as the sider/misc. framer/fix subs less than quality work. The owner builder is a friend and works as a PM in commercial construction (I work for this company as a carpenter in the field) so he knows how he wants stuff done but also is pretty “old school” in his thinking of how stuff should work. The last house he built was 20 years ago. The house is in climate zone 5. New England.
His wall assembly is hardie siding>zip sheathing>blown in fiberglass>poly vapor barrier (not taped/sealed at any seams or outlet boxes, just stapled on and cut around penetrations)>gypsum board
His other wall assembly is brick veneer>1 inch ventilation gap>Zip sheathing>Blown in fiberglass>poly (installed the same way)>gypsum board.
I know I have read from martin’s posts that poly shouldn’t be used in climates running AC more than 1 month a year and I also advised him that poly on the brick veneer walls isn’t recommended for our climate zone. But I also have read that even when wall systems aren’t ideally constructed most houses won’t have moisture issues.
He said his last house had poly with vinyl siding and was just fine the whole time he lived there and poly is just how people do it here.
I’m young and learning this all as I go and trying to take in as much information as possible through this experience for when I build. So back to my title question, what are the odds that these wall assemblies in our climate zone will have any issue?
GBA Detail Library
A collection of one thousand construction details organized by climate and house part
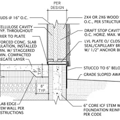
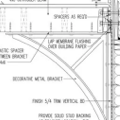
Replies
The biggest difference between his last house and his new one is siding.
Vinyl siding has enough gaps that it acts somewhat like a drained and ventilated cladding. It's also not a moisture reservoir, so between these two characteristics, it doesn't provide an avenue for inward solar driven moisture.
Hardie plank is somewhat of a reservoir cladding and will not perform as well as vinyl without furring to provide a gap. I'd strongly encourage him to at least do that, 3/4" plywood strips is fine, or anything that's easy to keep consistent for aesthetic purposes that's at least 3/8" and less than 2".
The poly, if not detailed impeccably, doesn't really help anything. He could get away with painting the drywall and detailing it as an air barrier instead.
Ultimately, the best thing to do would be to use exterior insulation. But if he's not willing to do that, then it is probably worth his time to add a ventilated and drained gap to the hardie plank and figure out another way of going about controlling vapor drive from the interior to the exterior. Even then, it's probably still risky.
https://www.nrel.gov/docs/fy13osti/56709.pdf ; See page 23
https://basc.pnnl.gov/sites/default/files/resource/Lstiburek%20Moisture%20Control%20for%20Residential%20Buildings%20Final%2010-23-20.pdf ; see relevant chapter for climate zone 5
I can't put odds on these walls having issues. There have certainly been well-publicized failures of walls with interior polyethylene (you've probably read Martin's Six Rules for Polyethylene and other GBA articles on this topic). There have also been lots of houses built like this that are doing just fine, albeit very inefficiently in CZ5.
One variable that maybe matters more (?) than the parts of the assembly is the quality of the details. These walls have exterior air barriers - the ZIP sheathing. Was it installed well? Is the air barrier continuous to other parts of the building? Are the windows and doors installed well? Is all the flashing done correctly? In other words, the walls have to get wet to fail and the two most common ways they get wet are from water and air. So any wall with excellent water management and air sealing has better odds of being problem-free than one that leaks. And I think it is safe to say that this goes for all assemblies. The reason drying potential is so important is because it is likely that at some point all walls will leak.
I agree with Andy. Improvements would be a rainscreen detail on the Hardi wall, enough exterior insulation to mitigate thermal bridging and keep the sheathing warm, and a more forgiving interior vapor retarder, either a variable-perm membrane or perhaps just the painted drywall, if there is adequate R-value of continuous exterior insulation.
Brian raises great points about the detailing. Any assembly is unlikely to be safe if bulk water detailing is poor as he said, and the air barrier details matter too.