Cellulose or blown-in fiberglass?

I have a 1939 house in northern NJ and am planning a re-siding project. While the siding is off I want to dense pack the walls with cellulose or John Manville fiberglass Spider insulation. Which is better?
Also, I was told to use Tyvek drain wrap as a WRB under 1 inch of foam board with siding over it. I plan on taping the seams on the drain wrap, but do I need to tape the seams on the 1 inch foam board? Is 1 inch extruded foam enough in NJ’s climate zone?
GBA Detail Library
A collection of one thousand construction details organized by climate and house part
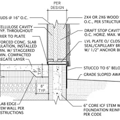
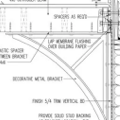
Replies
Michael,
Choose either insulation. It's not a question of "which is better?" It's up to you.
I think it's a good idea to tape the foam seams. Although there are questions concerning the longevity of the tape and the stability of the foam, it never hurts to tape the seams. It will improve airtightness and limit water penetration (at least until the tape fails).
One inch of XPS should be enough to keep you out of trouble in your climate. Read more here:
Calculating the Minimum Thickness of Rigid Foam Sheathing
I disagree with Martin. There is no question of which is better.
Fiberglass has a high embodied energy and is a known carcinogen (probably moreso with the much finer fiber size of Spider, which is closer to asbestos).
Cellulose is almost entirely recycled paper with boric acid as a fire retardant. The use of cellulose insulation reduces one of the largest contributors to landfills - newspapers. Cellulose has almost no embodied energy or global warming contribution. The boric acid (don't use product with ammonium sulfate) is an insecticide and fungicide as well as an effective fire retardant (allowing cellulose to function as a firestop) but is completely non-toxic to humans and pets.
Cellulose deadens sound better than fiberglass, stops convection better than fiberglass (though Spider is close), and it buffers changes in relative humidity as well as protecting the wood framing from excessive moisture accumulation.
There is simply no comparison in the overall quality of the two materials, though the quality of installation is also critical to proper function.
Most sidings should not be installed directly over foam board, as this prevents breathing and drying to the back. You can either install a drainwrap WRB over the foam board or use a rainscreen to create a capillary break and some breathing room, which will also provide a better nailbase for the siding.
I read up on those 2 options and apparently the tests which the JM uses to brag up their product are rather skewed. I'd have used cellulose, but my house is on wheels and it is HEAVY!
I hate to ask this but here goes..... Martin would you ever use blown in spider instead of cellulose and if so why? I think you mentioned elsewhere that cellulose can wick moisture over a larger area than spider, so IF enough moisture gets in the walls to do damage, with spider you stand a somewhat better chance of noticing a little bit of localized damage early on, compared to a later discovery of a much larger area of damage with cellulose. Is there any other reason you might use spider in a given application?
My question is: if it were not for that issue, is there any reason you might still use spider and if so why?
Steve,
I would use cellulose. But many builders I respect, including Michael Chandler, have tried both and prefer Spider. They are happy with the performance of blown-in fiberglass. Blown-in fiberglass performs much better than fiberglass batts.
Many green builders spend a lot of time defending their choice of insulation material (and, in some cases, attacking builders who choose other types of insulation). I'd rather not go down that path. Insulation is good; there is no one type of insulation that is best for all applications or all builders.
I'd rather not go down that path too. Since I'm about to insulate my house with one or the other, I'm trying to get my own list of variables to consider. My passion in other threads notwithstanding, I think I can filter out the noise if I know the issues. I know the wicking factor because it was subject to (unfortunately) heated debate previously.
What I would like to know is whether there are any OTHER factors that drive that choice by those other builders? I realize that if anyone posts one of those reasons here they are risking attack. But I assure you I am not trolling. I have to make a choice and want to know their ((((matter of fact)))) reasoning. Hopefully anyone who disagrees can provide their matter-of-fact reasons for disagreement.
Anybody? Is the wicking issue the only factor that tips the scale?
One of the reasons that we switched from BIBS to spray cellulose 8 or 10 years ago was the somewhat inconsistency density of the BIBS fill as revealed by infrared scan and the improved consistency of the spray cellulose systems, It seems as though that the BIBS approach depends on the installer to calculate density as they proceed and because of the nature of the system it is a bit of a challenge to hit it all the time. I'm not sure that the spider system has the same issues but it seems likely that that is the case. Of course a skilled installer always makes a difference no matter which system you use.
Sorry I realize that the case in point is not an open cavity situation and thus may not have the same issues.
I'd have to back Robert in his approach to these discussions. I don't think he is over complicating things for the following reason:
We are proponents of insulation because of energy efficiency.
We are proponents of energy efficiency not for energy efficiency sake but because it reduces the impact on the environment of our want of a mechanically conditioned enclosures.
The production of insulation materials also has an effect on the environment outside its thermal resistance properties so these are important aspects of insulation choices to discuss as well.
I can't speak to economics of cost in NJ, but in OH cellulose is the best way to go for minimizing convective air flow in relation to money spent. The mechanics of the insulating material allow cellulose to perform better as an insulator when compressed to also minimize airflow. Fiberglass, by its own name glass fibers, relies on space between the fibers to confuse the flow of heat. Glass fibers pressed tightly against one another to minimize airflow are going to transmit heat more readily through conduction, and still not prevent airlfow as well as good old dense packed cellulose. Again, check pricing, but I would bet that per inch of thickness the cellulose yields a better R at a lower cost.
I'm determined to keep this objective.... and I agree that every factor is an important factor for an objective list, including the impact of manufacture. While we're at it, let's add the eco cost of disposal after the materials service lifetime.
So on the list I've heard here and elsewhere:
Price
Availability (both of material and necessary skill for installation)
Weight (for ceiling applications)
Ph (depending on other materials used in conjunction)
Wicking (mentioned briefly earlier in this thread)
Then there's lots of opinion about which packs in around obstacles, and ultimately does "better" for R value, convective looping.... and _____?
Anything else? (Eco cost of manufacturing-install-disposal is already listed)
I don't want to re-invigorate the battle so I will only say that it would be a good idea to check the prices on the Spider Bibb vers Spider damp-spray and Cellulose Dense Pack and damp-spray from several different installers remembering that installers who are not certified to install Spider Damp-Spray are often more economical at higher installed R-value than the damp-spray certified guys.
In northern NJ the moisture moderating qualities of Cellulose are more beneficial than they are down here in the southeast and you are less subject to hurricane and ice storm damage than we are down here so the leak detection of a non-reservoir insulation is slightly less of an issue. Given that you're building in the winter the idea of using thermal imaging to inform quality control is pretty compelling with either product. Installation quality is a very significant issue with all types of insulation. Paul Eldrenkamp has had some interesting things to say on the subject of installer training and quality control. I'd love to encourage him to join the conversation here at GBA.
If you want to focus on embodied energy content and life cycle analysis then you may also want to look at the embodied energy of the concrete and aluminum components of the house.
I Thank everybody for their suggestions I I did not mean to start a heated debate over cellulose Vs fiberglass. . I will be using as mentioned above tyvek drainwrap as a WRB with 1 inch of dow extruded foam over that with the seams of the wrb as well as the foam taped. Do I need to use a rainscreen between foam and vinyl siding. I hired a contractor to install siding and did not specify a rain screen.Is it necessary. Thanks
Mike, I am doing the same as you and I apologize for butting into your thread.... . be assured you didn't START anything, the war has been raging and will continue to rage long after we do our projects. Amidst the noise I'm just trying to understand everyone's perspective well enough that I can faithfully articulate it from their point of view.
Michael Z,
The experts will tell you that most (if not all) vinyl siding does not require ventilated rainscreen, for it is inherently ventilated.
I should add that vinyl siding is not moisture sensitive, thus back-venting is not an issue.
There is no "war", no "battle", and no "heated debate" about this issue. There are, however, a broad spectrum of issues, based on objective building science and hygrothermal properties of materials, as well as ecological considerations that make this a very one-sided debate.
The moisture redistribution issue is commonly misunderstood. If there is a leak in a wall, a given amount of water will penetrate regardless of which type of fibrous insulation in in the cavities. With any type of fiberglass, because it is hydrophobic, liquid water will drain to the bottom plate where it will accumulate and concentrate in the framing, potentially causing mold and/or rot. This condition will be dramatically exacerbated if there is also exterior foam insulation which will not only dramatically slow outward drying but also maintain higher cavity temperatures that are conducive to mold and decay organism growth.
Cellulose, because of its highly hygroscopic property, will quickly redistribute that same volume of moisture over a much larger volume and cavity area. It will safely store that water until it can diffuse either outward or inward. And, by absorbing and redistributing the water, it will drastically reduce the local concentration of water at the framing, thereby significantly lowering the probability of accumulation and consequent problems in the wood. The boric acid fire retardant in the cellulose is also a very effective fungicide and will prevent mold growth in the damp insulation.
The significant moisture redistribution, storage and release function of cellulose, which no form of fiberglass shares, is just one of the long list of advantages of cellulose over blown fiberglass. From an ecological or indoor air quality perspective, there is simply no contest between the two. And, since the insulative qualities and convection-mitigating qualities are roughly the same with dense-pack cellulose and Spider fiberglass, there is no reason for a green builder to choose the proprietary Johns Manville product over locally-recycled newsprint.
TO BUILDERS WHO SOMETIMES BLOW FIBERGLASS INSTEAD OF CELLULOSE IN EXISTING WALLS:
Do you ever pick that material for any reason that is not already listed in this thread?
I suppose we should add to the list "customer preference";
I would add the reliance of bromate additives for fireproofing and personal experience with a neighbors small house fire smoldering and re-igniting hours after the fire department and home owners left. I have heard many stories of small electrical fires due to over heated wires, especially in older homes, going out of control due to cellulose insulation .
I understand that today's cellulose is different from cellulose made ten years ago though and that they may have better fire retardants in use now. But fiberglass naturally doesn't support fire and is easier to deal with when extinguishing a minor house fire. Similarly, comparing the new micro-filament fiberglass to obsolete fiberglass batts is not a relevant comparison.
I know that it may sound foolish to design a house to be easy to repair in case of a leak or a house fire but after thirty years in the industry I've seen a lot of crazy slow leaks and candle fires and electrical malfunctions and I prefer to think proactively about these events.
The Hell with courtesy
We all need to get a thicker skin and wear goggles.
I think the anonymous posters are cowards.
Also the "experts" who post thru Martin or Post and run away
As far as Building Science goes... I am leaning toward Robert's version
Once again, reformatted because there is neither an edit function or a simple way to highlight text.
At least while we're installing fiberglass!
And, I would add, don't inhale or wear your clothes home to your family.
I wonder how the fire retardants in cellulose hold up after 50 years of seasonal ups and downs of temp and humidity? After 100? Same question about pesticides. Opinions are great.... studies are better. Anybody?
Actually, opinions are worthless unless they're well-informed by either objective science or extensive experience and not influenced by commercial considerations or biased by conflicts of interest.
Studies can be useful, but it's been demonstrated that the findings of studies are almost always influenced by the funding source (or other financial or career interests of the participants).
Often, however, all that is required to answer simple questions like this one is a basic understanding of chemical, physical and mechanical principles.
Borates are highly effective but water soluble. So they will remain in a porous material until they are washed out. If cellulose becomes saturated by water (> 30% by weight), then it must be removed and replaced. But if that much water enters a structure, the cavities must be opened and dried regardless of the insulation type. The damp cellulose can go right into the compost pile, be tilled into the garden or used as a binder for clay plasters or earthen floors.
You are assuming that loss of fire retardation can ONLY occur when borates are 'washed out' after a saturation event and under NO other circumstances. One hundred years of seasonal temp and humidity cycles and whatever chemistry might take place in any given wall assembly might hold a surprise. I agree objective science is a good thing.
I neither "assumed" that nor stated it.
It's also possible that the sun won't rise tomorrow either because of unknown events or as yet undiscovered principles of astrophysics.
While it's true that "the absence of evidence is not the evidence of absence", this argument is often used (by the likes of Cheney and Rumsfeld, for instance) to support a predetermined ideological conclusion.
The only thing that is clear from the direction this thread has taken is that Steve El is reaching for straws to find something to undermine the obvious green insulation choice or to justify the use of toxic and environmentally-irresponsible materials such as fiberglass.
Robert, on the end-of-service issue, I certainly agree that biodegradable cellulose is the obvious no-brain winner over nonbiodegradable fiberglass. No argument there.
As an organic veggie farmer I would never apply cellulose insulation direct to my crops. First, you can't be certain that the stuff is what you think it is. Consider all the lead painted childrens toys from China recently, or a study not long ago that showed 20% of marketed goats milk is actually from cows (I don't know the reference... and MD told me about it). Its nice to assume that the source material is just wood fiber and soy ink but you don't really KNOW and so I would not add it to my organic fields. Then there's the insecticides and anti fungal agents. I work hard to build my soil, and I certainly don't want to go backwards. Lots of bugs and fungi are my friends. Finally there is the issue of available nitrogen in the soil. I don't till in sawdust and so why would I till in insulation?
We completely agree that biodegradability of the cellulose is a strong argument in favor of that insulation. I'd be interested in the opinions among your expert farmer friends whether they'd apply the stuff to their crops after considering these issues.
Steve,
You can't be certain about anything you purchase unless you exercise due diligence.
Why would an organic farmer buy toys or drywall from China? Would a farmer buy goats milk without knowing the source?
I use only cellulose from National Fiber, which uses only clean, hand-sorted surplus newsprint and natural mineral borates and is made not far from here in Western MA. I use their product because I trust the manufacturer.
I didn't say that wet cellulose is necessarily an appropriate soil amendment for every garden (why must you repeatedly distort my arguments?). But it can be disposed of on one's own land, taking responsibility for one's wastes, rather than going to a landfill. And - wasn't this the topic you asked for? - after getting saturated it will likely have a good part of the borates washed out, so that should not be a major consideration in determining appropriate disposal or recycling options. Borax is, after all, non-toxic to humans and cellulose would improve the tilth of the soil.
Because it CAN BE recycled into the soil does not imply that it SHOULD be in all situations. A little logic goes a long way.
Fiber glass is not a “known carcinogen.” Tens of millions of dollars of research has been conducted at leading independent laboratories and universities in the United States and abroad. Many scientific review groups have concluded that this research shows no association between exposure to glass fibers and respiratory disease or cancer in humans.
In October 2001, an international expert review by the International Agency for Research on Cancer (“IARC”) re-evaluated the 1988 IARC assessment of glass fibers and removed glass, rock and slag wool fibers from its list of substances “possibly carcinogenic to humans.” All fiber glass and rock and slag wools that are commonly used for thermal and acoustical insulation are now considered not classifiable as to carcinogenicity to humans (Group 3). IARC noted specifically:
Epidemiologic studies published during the 15 years since the previous IARC Monographs review of these fibres in 1988 provide no evidence of increased risks of lung cancer or mesothelioma (cancer of the lining of the body cavities) from occupational exposures during manufacture of these materials, and inadequate evidence overall of any cancer risk.
IARC based this decision on new and better data on fiber glass. IARC also retained its Group 3 classification for continuous glass filaments and the Group 2B “possible carcinogen” classification for certain special purpose glass fibers.
The IARC revision is consistent with the conclusion reached by the U.S. National Academy of Sciences, which in 2000 found “no significant association between fiber exposure and lung cancer or nonmalignant respiratory disease in the MVF [man-made vitreous fiber] manufacturing environment.”
IARC’s comprehensive review of the extensive studies published over the past 15 years indicates that some of the prior reviews now need to be updated. Most of these earlier reviews do not consider the new and better scientific data. For example, the U.S. Department of Health and Human Services (HHS, Shalala 1994) included fiber glass on its list of possible carcinogens based primarily on the 1988 IARC classification.
Similarly, the California listing of fiber glass as “known to the state to cause cancer” in 1990 was based principally on the old IARC classification.
This is confirmed by the Agency for Toxic Substances and Disease Registry (“ATSDR”). Specifically, ATSDR stated:
In 2002, the International Agency for Research on Cancer (IARC) considered all of the evidence regarding the possible carcinogenicity of synthetic vitreous fibers. Much of the evidence was collected in the 1990s and was not available for earlier assessments made by the U.S. Department of Health and Human Services (DHHS). FN1
(FN1 Toxicological Profile for Synthetic Vitreous Fibers (U.S. Department of Health and Human Services, Public Health Services, Agency for Toxic Substances and Disease Registry), September 2004, p. 7.)
The U.S. Department of Health and Human Services, National Toxicology Program (NTP 1998, 2000, 2002) classified glass wool (respirable size) as reasonably anticipated to be a human carcinogen, based on sufficient evidence of carcinogenicity in experimental animals. This assessment was originally prepared in 1993-1994 for the 7th Report on Carcinogens (NTP 1994), but has not been updated since then in the 8th, 9th, or 10th Reports on Carcinogens (NTP 1998, 2000, 2002). FN2
(FN2 Ibid. at p. 217.)
In 2002, NAIMA petitioned the National Toxicology Program (“NTP”) to delist fiber glass insulation from its Report on Carcinogens (“RoC”). In what has been an extremely lengthy bureaucratic process, NTP is close to issuing its final decision. What has happened along the way is consistent with what IARC did in 2001. Specifically, in 2009, the NTP Expert Panel, a group of fiber experts selected by NTP for their special expertise in fiber toxicology and the absence of industry ties, unanimously recommended that fiber glass be delisted from the RoC. Approximately a year later, NTP issued its Draft Substance Profile on the Petition to Delist Fiber Glass, specifically concluding that the majority of glass fibers are not carcinogens. In fact, 99 percent of all glass fibers under consideration by NTP do not cause cancer, but a small 1 percent of special purpose fibers are classified as a possible carcinogen. A possible carcinogen is significantly different from a known carcinogen because the scientific evidence for “known” is definitive and conclusive whereas possible carcinogens, which include coffee, are open to debate and the evidence is not conclusive.
In June 2010, the Board of Scientific Counselors reviewed the Draft Substance Profile, and the minutes of that meeting provide further concurrence of IARC’s 2001 decision with that recognition that 99 percent of the glass fibers reviewed by NTP are not carcinogens. Importantly, NTP senior staff explained to the Board of Scientific Counselors that they intended to follow the European Union’s (“EU”) approach of allowing fibers (individual fibers) to be exonerated. Under this scenario, many of the glass fibers are already exonerated under the EU criteria, so these fibers would not be considered a carcinogen by NTP.
The weight of the scientific evidence shows no evidence of carcinogenicity in glass wool insulation. This scientific evidence has been reviewed by the international scientific community and the most authoritative bodies. These bodies historically have been predisposed to classify and list substances as carcinogens on limited evidence, yet fiber glass has been determined to be a non-carcinogen by IARC, the National Academy of Sciences, the NTP’s Expert Panel, and NTP senior staff. ATSDR and many other governmental bodies outside the United States have reached similar conclusions that fiber glass is not a carcinogen.
Angus Crane
Executive Vice President, General Counsel
North American Insulation Manufacturers Association
It certainly puts my mind to rest that, after years of extensive lobbying, NAIMA was finally able to reverse the previous findings of governmental agencies charged with protecting public health.
And this new "consensus" apparently determined as irrelevant, such studies as the one sponsored by (and apparently cancelled by) NAIMA on hamster mesothelioma in a Swiss lab that showed precancerous conditions after only 6 months of the 2-year study (and hamsters are nose breathers with good filtration mechanisms, unlike humans who breathe through their mouths).
And this "consensus" apparently deemed irrelevant the NIOSH study which determined that glass fibers disrupt DNA in a manner that can lead to cancer. And, because it was not cancer-related, this consensus wasn't interested in the Cornell study which associated mineral fibers with Sick Building Syndrome (NAIMA, of course, labelled it "flawed science").
It's curious that "no evidence of increased risks of lung cancer or mesothelioma" in recent studies (which apparently contradict earlier studies) "from occupational exposures during manufacture of these materials" (ignoring long-term occupant exposures and acute short-term exposures of renovation contractors) equates to "inadequate evidence overall of any cancer risk".
In other words, absence of evidence is not evidence of absence, particularly when a powerful industry trade group is doing its damndest to influence the interpretation of evidence.
And this "consensus" ignores significant anecdotal (at least) evidence of multiple toxic effects of exposure to fiberglass, including:
• persistent, dry, hacking "barking" cough
• sore throat, bloody taste in throat or blood in sputum
• bloody nose
• persistent, occasionally very severe, sinusitis and rhinitis which does not respond to common medical treatment
• especially treatment for allergies
• persistent, occasionally severe respiratory infections which, again, do not respond to common medical treatment
• headaches, nausea, dizziness, insomnia, irritability, depression
• asthma-like breathing attacks or constant wheezing
• other allergy-like symptoms (which do not respond to allergy treatment)
• "reactive airway disease"
• swollen, red, watery, infected eyes
• skin infections, ranging from mild to very severe, requiring hospitalization
• extreme sensitivity to everyday amounts of ambient pollutants, especially: cigarette smoke, car exhaust, perfumes and colognes, some cleaning products, paints and varnishes, new paneling, cabinetry or furniture made with particle board or strand board, new cars and other new plastic, foams used for furniture and bedding, new carpeting
Angus Crane,
The search for evidence was flawed. Breathing fiberglass insulation is bad for your health, period.
How do you explain the severe symptoms that follow exposure and breathing of fiberglass?
The symptoms and discomfort are the bodies natural way of telling you that this stuff is bad for you.
I can't believe that you would make such a lame post. This stuff kills people. Get real !
In energy auditing, the useful life of blown in insulation (both fiberglass and celulose) is typically 15 years. I would like some input on why that might be. I read everywhere that cellulose, unlike fiberglass, breaks down over its useful life, but nowhere can i find where it specifies what the useful life is, or why.