Cellulose and foam board combination on attic floor

My location is 13420.
My roof design is a cape with a drop ceiling: from the top plate the sloped portion of the ceiling extends 5′ to the drop ceiling which runs 17′ to the slope at the opposite rake edge of the roof. Rafter ends at the plate are vented (2″) and the ridge is vented. I’d planned on closed cell in the slopes.
My questiin is this: for the flat portion of the ceiling I’m considering dense packed cellulose – I have 7″ deep collar ties that I’d then cover with 3″ of reclaimed polyiso. Seams all sealed. The finished 2nd floor ceiling is ship lap pine that’ll get an appropriate finish.
Is this a viable plan?
Thanks, Daniel
GBA Detail Library
A collection of one thousand construction details organized by climate and house part
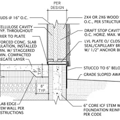
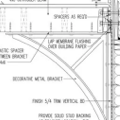
Replies
Hi Daniel,
This article will answer your R-value questions:
https://www.greenbuildingadvisor.com/article/how-to-build-an-insulated-cathedral-ceiling
Here are some questions that we'll need you to answer to help with some of the other details:
Is that a zip code? How about just giving us a city and state or a climate zone. Here's a map to refer to: https://www.greenbuildingadvisor.com/article/climate-zone-map-including-canada
What dimension are your roof rafters?
Are you planning to drywall the ceiling before installing the paneling?
Sorry, that's my zip. Climate zone 6.
My question is regarding the stack up on the flat - not the slope. Sorry for the confusion.
From below: 3/4 pine shiplap, 7"dense pack cellulose, 4" polyiso.
My question is if this stack up is viable in terms of moisture from the living space. Thanks
Couple things I should clarify: I mistakenly said dense pack in between the collar ties. I'm just having 7" installed, not dense packed.
Also the second floor ceiling - shiplap pine - is finished with two coats of shellac. I am not installing sheetrock to ceiling prior.
Last, I have access to both reclaimed polyiso and xps and am aware of the temperature's effect on polyiso.
Dense packed or loose filled, the ship lap is NOT an air barrier, which is one major moisture transport issue. There needs to be a reliable air barrier between the ship lap and fluff.
The second issue is that in climate zone 6 with highly vapor retardent foam on top of the cellulose the R-value of the foam needs to exceed that of the cellulose layer. You're probably looking at 2x8s (?) which are 7.25" deep, so even with loose filled cellulose it would run R25- R27, which would call for a minimum of 5" of polyiso to have any margin, even if the ship-lap were air-tight.
Thirdly, if the cellulose is NOT dense packed and the ship lap is NOT air tight and there is only a bare MINIMUM of R27 foam, the seasonal moisture cycling into and out of the cellulose will be fairly high, with a high likelihood of settling over time, leaving a potential thermal bypass gap between the foam & cellulose.
Daniel,
Dana's got you covered on the R-values. I just want to stress the point that you need a good air barrier. If this is a design, not a built house, install airtight drywall before installing the wood ceiling. That way, your insualtation can perform.
Thanks for the replies. The collar ties are milled to 7" and the original plan had been to install closed cell through the attic: sloped section as well as flat. I'd like to minimize the extent of sprayed-in foam, but an alternative seems possibly out of reach given the limitations/obstacles of completed construction. My last alternative may be to cut and fill the ties with reclaimed foam and then cap the entirety as well.
I do have to respectfully question the suggestion of installing drywall prior to a pine finished ceiling. Though I understand the function of it as an air barrier the redundancy and subsequent materials, labor, and related expenses seem absurd when - unless I'm mistaken- a product like Intello would offer the same benefit.
Thanks, Daniel
>"The collar ties are milled to 7" ..."
At 7.0" rather than 7.25" of cellulose you're talking ~R24.5 - R26, which doesn't really move the needle on how many inches of polyiso it's going to take.
I'm at loss as far as a viable alternative to closed cell foam given my construction. At this point, considering the current design, does cut and fill with reclaimed polyiso and covering the entire collar tie assembly with two inches of the same make the most sense?
Thanks, Daniel
Aside from cutting and filling with foam is there any other approach that's makes sense to filling the voids and capping off the ties?