Cellar floor retrofit

I am continuing to tackle some home improvement projects on our old Greek revival farmhouse in upstate NY. With cold weather here I’m turning my attention to the cellar. There are several tree trunk support posts that I plan to replace with metal support posts. I will be pouring new footers (12″ thick x 24″ square) for each post since the existing footers are either undersized or simply large rocks. Eventually I would like to pour a new slab throughout the entire cellar. I plan to excavate the existing slab, which is relatively thin and always damp, in order to keep the current headroom that’s down there. I’ve done 2 or 3 radon tests over the years with results that indicate no mitigation is needed. I definitely want to put down a vapor barrier under the future slab which brings a few questions to mind.
- What is the best material for a vapor barrier under a concrete slab? I’ve read that the poly sheeting commonly used degrades over time and isn’t the best option. Is EPDM ever used under a slab? Resource Conservation Technology carries a polyethylene sheeting for use under slabs that they say is superior to standard films.
- It makes sense that the vapor barrier should also be placed under the footers. How should I detail that?
- I was thinking I’d have the tops of the footers level with the new slab. Is this best practice or should the slab be poured over the footer?
- With all the work that is involved, would it be wise to go a little further and add the appropriate piping for radon mitigation?
- Should I consider adding insulation under the new slab? We think the house was built around 1850. The fieldstone foundation is in decent shape and the one floor drain works well. Unfortunately, one of the places I started digging for a footer was over a clay tile – maybe 6″ or so under the current slab. I want to avoid disturbing any of that if possible.
- The existing slab was poured directly over the dirt floor. Should I excavate enough for adding crushed stone under the new slab?
Many thanks for the help.
-Jodi
GBA Detail Library
A collection of one thousand construction details organized by climate and house part
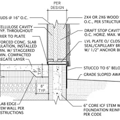
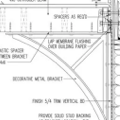
Replies
Jodi,
Martin has an excellent article (https://www.greenbuildingadvisor.com/article/fixing-a-wet-basement) that will answer some of your questions.
2> pouring the footers into forms lined with 10 mil polyethylene would be a good start. Also mixing in a waterproofing admixture (eg: Zypex, Krystol Internal Membrane, etc ) into that concrete mitigates capillary draw by quite a bit.
3> it's more usual to have the footers for lally columns slightly above the slab for drainage away from the steel or wood, but flush with the slab is fine. It's also possible to put the top of the footer below slab level, and pour it around the column, but installing it flush or above the slab and putting in expansion joint material between the slab & footer to keep it from stressing/cracking the slab if it settles or moves a bit is probably better.
4> In any of the radon-red counties it's probably "worth it" to just go ahead:
https://www.epa.gov/sites/production/files/2014-08/documents/new_york.pdf
Of course it doesn't cost much to test it BEFORE starting the project to get a handle on it.
5> In NY the deep subsoil temperatures are WELL below the summertime outdoor dew points, which causes basement slabs to accumulate moisture from the room air over a summer. It doesn't hurt the concrete, but it does encourage mold growth on anything resting atop the slab. A couple inches of reclaimed roofing EPS is pretty cheap and will keep the slab much warmer both summer and winter, reducing the amount of summertime moisture accumulation in the slab to help keep the "musty basement smell" at bay. From an energy use point of view 2" of EPS would "pay off" eventually even if it were virgin stock full-retail goods. If using reclaimed EPS (or XPS, but NOT polyiso) even 3" is a no-brainer. There are multiple vendors of used foam in NY state, many of the advertising here:
https://albany.craigslist.org/search/sss?query=rigid+insulation
https://buffalo.craigslist.org/search/sss?query=rigid+insulation
https://syracuse.craigslist.org/search/sss?query=rigid+insulation
(Just because they're advertising polyiso doesn't mean they don't handle EPS- call and ask.)
6> Yes- a few inches crushed stone would help in several ways, including drainage & radon abatement. Depressurizing a slab for radon abatement over crushed stone takes a MUCH smaller fan and less electricity that depressurizing a slab poured directly on clay soil.
Jodi,
In addition to the replies above, I think these articles would be worth reading and help you understand the details and implications of the work you are getting into:
https://www.greenbuildingadvisor.com/article/all-about-basements
https://www.greenbuildingadvisor.com/article/all-about-foundations
https://www.greenbuildingadvisor.com/article/all-about-radon