Ceiling hydronic heating and cooling

I am building a house in Washington, DC. (Zone 4a). The design hasn’t been finalized yet but a preliminary Manual J has it slightly heating-dominant, about 10 Btu/hr/sf for heating and about 8 Btu/hr/sf for cooling. About 10% of the cooling load is latent, which seems low to me. My intention is to seal and insulate better than code and have a nice tight house.
I have been reading John Siegenthaler’s articles about ceiling hydronic systems, here:
https://www.pmmag.com/ext/resources/PM/2014/June/016-020-0614-Siggy.pdf
Tantalizingly, his last sentence is:
“By the way, with suitable system controls, this ceiling panel is ideal for radiant cooling applications.”
How can he leave us this way!
In this article he goes into more detail, but still doesn’t get everything:
https://www.pmengineer.com/articles/93157-looking-up-to-radiant-cooling
He makes the point that well-insulated, modern houses need much “gentler” heating and cooling systems than traditionally. He advocates for minimizing thermal mass (which would have been heresy 20 years ago) to maximize responsiveness. I also really like the idea of eliminating (or minimizing) ductwork and the bulkheads, noise and drafts that come with it.
His recommended ceiling construction is 7/16″ OSB, 3/4″ poly-iso, then 1/2″ pex tubing in aluminum heat transfer plates with the tubing facing up, and the whole thing covered in drywall which is attached to the studs with 2 1/2″ screws.
What I’ve figured out is that you’d have to have separate dehumidification to avoid condensation on your ceiling. The recommended control seems to be to have a thermostat and a humidistat in each zone, and to turn off ceiling cooling if the humidity rises so that the dew point is above the water temperature. Let the dehumidifier run and take out the humidity and then turn the ceiling back on again.
Since my house is going to require active ventilation it seems relatively straightforward to integrate ventilation, dehumidification and air circulation in a single shaft that runs from the basement to the top floor.
He recommends a ceiling temperature of 110F (115 supply and 105 return) which gives an output of 30 btu/hr/sf with a room temperature of 70. That would be ample for my house. Using chilled water with a 45 supply and 55 return at a room temperature of 75 would give about 20 btu/hr/sf of sensible cooling in the same assembly, which is still about 2.5 times what it needs to be but lower than for heating. So the assembly would be sized for cooling and about 15-20% oversized for heating, which I think would work. An alternate strategy would be to right-size it for heating and use some of the ventilation shaft/latent cooling to also provide cooling to the rest of the house.
It will probably take me a few posts to lay out the details, I’ve been thinking about this quite a bit. I’m curious in your feedback.
Thanks.
GBA Detail Library
A collection of one thousand construction details organized by climate and house part
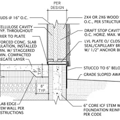
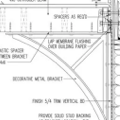
Replies
What will you use to heat/cool the water? I'd look into using fan coils (which handle sensible and latent).
In my opinion radiant cooling lives on the bleeding edge of failure if you cannot grow cactuses in your yard. Not that radiant cooling can work in a swamp it will not be cheap or easy.
I am all in for DIY but not when you are living on the bleeding edge of failure. I say if you are committed to this type of system the smart move is to pay the engineers to design it and find an experienced installer.
My wild guess is you will require more tons dehumidifier plus and heat pump than a conventional system.
Walta
I’m pretty familiar with the weather conditions in the metro DC area as I’m out there frequently. I would NOT NOT NOT use radiant cooling in that climate!!! You’re going to have condensation on the inside of your ceiling and PROBABLY OUTSIDE TOO, even with the 3/4” of polyiso. This is a recipe for moisture problems. The reason is that you have very hot and extremely humid summers and those conditions persist for long periods of time. The moisture in the air will condense out on both sides of your radiant panels.
If you want to put in a radiant heating system, go for it. They are very nice for comfort. Stick with a conventional forced air cooling system though. You can get air conditioning only air handlers if you don’t need the heating function.
Bill
I appreciate the frank advice from Bill and Walter, but I want to probe a little deeper. Do you think I will be unable to maintain low interior humidity through dehumidification, or do you think that low humidity will not be sufficient to prevent condensation problems?
Thanks.
Humidity is notoriously difficult to control, and also to accurately measure. Dehumidifiers operate by heating the air and then blowing it over a cold coil. The units have small refrigeration systems inside to move the thermal energy from the cold coil to the warm coil. Think of dehumidifiers as closed-system air conditioners with the hot air from the usually outdoor condenser (hot) coil ducted directly to the intake for the normally indoor evaporator (cold) coil.
If nothing else, you’d be wasting energy since the energy consumed by the dehumidifier contributes heat to the house that the radiant cooling system then has to remove. In a normal forced air air conditioning system, you get dehumidification “for free” as a byproduct of the cooling process. No extra energy is needed to run a separate dehumidifier.
Running a dehumidifier also doesn’t help you with condensation on the EXTERIOR side of your radiant panels. In the typical DC summer climate, the dew point for the outdoor air will be fairly high. What this means is that even with the exterior side of your radiant panels insulated, you can still have the exterior side of that insulation get cold enough to drop below the dew point. As soon as you have a surface drop below the dew point for the air around it, you get condensation on that surface.
Wet surfaces in your attic are an invitation for mold. If you get enough condensation, the water will start pooling up and running off, and now you can start having mold in the walls (and anywhere else the water goes), and possibly even drywall or structural rot issues if there is enough water produced.
I see a lot of risk in such a system which is why I don’t recommend trying it. Another issue you’re likely to have is finding a reasonably priced chiller of sufficiently small size. I work with chillers all the time professionally, and they are usually used in LARGE cooling systems (big office buildings, malls, places like that), and process cooling systems (cooling off molds to get the injection molded plastic parts to set, for example). There aren’t a lot of options for chillers in the single-digit tonnage range like you’d need for a house. The only very small chillers I’ve ever seen are for special purposes and tend to be much more expensive than a similar capacity (in terms of tons) air conditioner.
Bill
Points taken about the risk.
I'm not thinking of using a dedicated dehumidifier. What I'm thinking is having an abbreviated forced-air cooling system for handling latent loads and some of the sensible load, then using the coils in each room to fine-tune the temperature.
I'm thinking of a single duct that runs from basement to top floor. In the basement there would be an air handler, with a hydronic cooling coil receiving cold water from the same chiller that serves the radiant loops. I would tune this to dehumidify more than normal.
Just tossing around some numbers, assume that my whole cooling load is 2.5 tons. I might put 1 ton in the forced air system. That would need 400 cfm. At 600 fpm I'd need 2/3 of a square foot of duct, or 8x12. I think I could sneak that into a chase that went from basement to top floor.
Each zone would have a combo thermostat/humidistat. If the humidistat is calling it activates the trunk blower. It also blocks the thermostat from calling from cooling. If the thermostat is calling for cooling and without the humidistat then cold water would be fed to the radiant loop.
I would probably have to keep the dew point lower than usual and I have to study the energy impact of that.
To “tune” the unit for more dehumidification, you can either lower the airflow across the coil, or reduce the coil temperature. Usually you need to reduce the coil temperature, and in your case, with higher than normally used chiller water temperatures, you’d have difficulty running the dehumidification coil on the same chiller as the radiant system. You could maybe make it work with a variant of a tempering valve, but I think you’d have a lot of hassle keeping it tuned.
I think trying to make all this work correctly is going to cost more than just putting in conventional radiant heating and forced air cooling systems. If you want to use some ground source “chilled” water in a sort of passive cooling system, I’d put a hydronic coil in your air handler ahead of the A coil for the regular refrigerant-based system. Use a modulating blower so that most of your cooling is handled by the hydronic coil, with the A coil kicking in for any extra cooling and all of your dehumidification needs. The hydronic coil probably won’t be enough to handle all of your dehumidification needs, but it will help with sensible cooling. You’ll want to cut off the hydronic coil when running the A coil for dehumidification to get mad efficiency for dehumidification purposes.
Bill
Just to clarify, when I talk about "ground source" I mean a closed loop water-to-water heat pump. Groundwater here is too warm to be effective as a cooling medium. I'm not that crazy!
The control is described in the article I linked to earlier. The chiller runs at the temperature needed for the dehumidification coil, and the water is mixed before going to the ceiling loops to keep it above the dew point, just as warm water in radiant loops is often tempered by mixing.
Excerpt:
This is the same piping one could use to control the temperature of warm water supplied to the radiant panel circuits for heating. The only difference is the control logic used to regulate the mixing valve. For cooling, it would be the previously discussed dew-point control. For heating, it would be outdoor reset control, where the water temperature supplied to the panel increases as the outdoor temperature decreases.
So wouldn’t it make sense to have a single electronic controller that includes both control algorithms? This would allow the same panel that provides excellent thermal comfort in winter to provide sensible cooling in summer. The concept is shown in Figure 4.
Because condensation must be avoided, radiant panels only can provide sensible cooling (e.g., lowering the air’s dry-bulb temperature). Proper system design also must address latent cooling (e.g., lowering the moisture content of the air). The latent cooling load can only be handled by a device that allows condensation to form within it and properly dispose of that condensate. Most systems use one or more air handlers equipped with chilled-water coils and drip pans for this purpose. The volume of air passing through the air handler often is determined by the ventilation load of the space.
Figure 5 shows the concept for such an air handler. It includes a heat-recovery unit that scavenges some of the cooling effect of the exhaust air stream and uses it to precondition the incoming ventilation air. This assembly also includes a multiple tube-row chilled-water coil that is very effective in dehumidifying the air passing through it. The goal is to dry the air supplied to the space to a condition that allows it to absorb sufficient moisture from the space to maintain a comfortable relative humidity.
The cooling capacity (and rate of moisture removal) of the air handler in Figure 5 is controlled by the flow rate of chilled water through the coil. In this case, that flow is regulated by a variable-speed circulator that responds to a controller that measures the relative humidity of the supply air stream and compares it to a setpoint value such as 50%. The controller outputs a signal which is compatible with the speed controller driving the circulator. When the relative humidity starts to rise above setpoint, the circulator speeds up to increase the capacity of the coil and vice versa.
The air handler system also could be used for ventilation in winter. In cold climates, the circuit through the cooling cool, which could be used to warm incoming ventilation air in winter, would need to be protected by antifreeze.
Apparently you could use a supply temperature of about 60F. If you can ensure 55% RH surrounding all of the cold elements , you won't get condensation (but you might get mold).
The cost to dehumidify depends greatly on air sealing and other moisture sources. It can be so minimal that waste heat from it isn't much of an issue. And you need it even with a ducted mini-split.
If you don't want to use fan coils in each room, you can use some combination of a central, ducted fan coil for dehumidification plus radiant for sensible (each with their own supply temperature). Look into commercial DOAS systems.
So here's the calculus I'm struggling with: to prevent condensation, the water temperature has to be above the dew point of the house. The warmer the water, the easier that is to achieve. However, the warmer the water the less cooling it provides.
Cooling capacity is given by the difference between the water temperature and the room temperature. If the room is at 75 and the water is at 60 the delta is 15 degrees. If the water is at 45 the delta is 30 degrees --twice as much-- and your radiant loop has twice the cooling capacity at at 60. Which means your coil has to be twice as big. My calculation is that with water at 50 the coil needs 40% of the ceiling area. Pushing the temperature up to 60 means it needs 67% of the area. At a certain point you're going to run into a practical limit because you can't really use 100% of the ceiling. And certain rooms might have a high cooling load relative to their ceiling area.
On the other hand, keeping the dew point below 60 is a lot easier than keeping it below 45, I'd say a house with a DP of 60 would be marginal to be considered air-conditioned.
The question is whether there is a sweet spot where the competing forces can be balanced.
There have been a couple of questions about how I would heat and chill the water, so here's what I'm thinking.
I'm undecided among ground-source geothermal and air-source heat pump for cooling, and those two plus additionally natural gas boiler for heating.
I want to have separate devices for heating and cooling. I'd like to have domestic hot water come off of an indirect coil on the heating system, and that would happen during the cooling season. Second, it's possible that there would be call for dehumidification during heating and I'd like to allow for that.
There are a couple small-tonnage water-water heat pumps available for ground source applications. I think Chilltrix is it for air-source. Gas boilers are easily available.
If I go with ground-source heat pumps, I'd look into feeding the output of one into the input of the other so that when producing hot water while cooling the energy would be recovered.