Ceiling construction in tropical fish wholesale facility

I have recently hired on as a maintenance man in a Tropical Fish Wholesale facility. Probably 1000 fish tanks and 100% humidity. After looking at the Hodge Podge of insulation boards fastened to the sheetrock Ceiling for 3 months now, (This is to keep sheetrock from falling down, and using this same method to repair 2-3 spots) I’ve decided to investigate the attic situation. Worst fears have been realized. It is Literally raining in the attic. Plywood covered with ice and water. Cellulose Insulation totally soaked. Flexible air ducts full of water. Galvanized truss plates peeling away from the wood. I walked 10 feet into the attic and found 2 truss’s where the top truss plates completely separated from the top rafter, meaning collapse of ceiling in that area immanent.
Here’s what I’ve found out and the facts. approximately 40×200 building.11′ ceiling height. Several Horizontal forced air furnaces mounted at ceiling level. 1 Medium sized heat exchanger which is currently not working. Block construction with a shingled 4/12 roof pitch. Flat roofed parking garage, no problems here, and an office area, no problems here. Roof replaced in 2000. They replaced all the plywood with pressure treated, and installed a commercial ridge vent. This is a cold weather region, with moderate snow fall. I have a background in roofing so was able to tell and show the owner what was happening. He knew about the problems but didn’t understand the “ticking time bomb” that it is. I’m pretty sure a heavy snowfall now, may collapse the whole roof, and that something needs to be done immediately. Don’t think putting off any longer is an option.
Here’s what I’m thinking for a solution:
1. Have all the insulation removed from the attic by an abatement company. It is Cellulose, soaking wet. I’m thinking there is a company that could suck it out in some manner. Might have to cross lines meaning for instance a company that can handle the wet insulation. Wet Grain? Make immediate repairs to all truss’s with plywood gussets over existing galvanized truss plates. Replace flexible air ducts with galvanized. Super insulate and seal all ducts from moisture air.
2. Find a company, probably a drywall contractor that would do the following. Be able to break the job up into 4-5 weekends, we are shut down Thursday – Sunday. Big enough company with the man power, scaffolding, tools, etc. Take down the Hodge Podge of insulation board. Leave existing Sheetrock ceiling in place. (No way we can deal with that kind of demolition) Add 1×4 purlins perpendicular to roof truss’s. 16 – 24″ O.C. This will stabilize sheetrock, and provide a level base for the new ceiling. I would be available to deal with moving the lights, extending electrical box’s, dropping gas furnace’s, garage doors, etc. Next add 2 layers of hard board insulation. Thinking R-30 minimum. (The amount of heat loss now must be substantial) 2 layers because when cut 2′ off second layer length and width, there will be No heat loss. Joints would be staggered. Use a fastener for EIFS, or roofing insulation with a Galvanized screw. Don’t know if should go with a typical foam product, or something like urethane. I have noticed that when the foil backed urethane has been used it condensates terribly. Because of 100% humidity, tapes, caulks, and coatings won’t work. Don’t know if urethane foam would work to fill gaps either because of the humidity. The exposed layer of insulation? Should it be painted, coating, or some kind of moisture barrier. Would a foam product absorb the moisture? Can you paint Styrofoam? It Can be painted off site. Don’t see any benefit of an exterior galvanized product if not needed.
3. My next thought would be to keep all the humidity in the building, and deal with it through heat exchangers and ventilation fans. There are huge fans mounted to the walls, and more could be added for circulation. Would it be enough to rely on the 2 layers of staggered insulation to provide a moisture barrier, or should a moisture barrier be used like a Tyvek product. Finally a seal needs to be made between the foam board and the interior block wall. Maybe just stuffing a 1/4 – 1/2″ urethane rod would do here.
4. Finally I think I would eliminate all Roof vents, Currently there is a commercial “Barn Style” Ridge vent. Remove this and install either Powered Roof vents, or Powered Gable Vents. Controlled by a thermostat, and humidistat. Once attic is dried out, fans would run minimally if we could contain all moisture from the attic.
In closing I think the building is on course to self destruct, and it is a very harsh environment. Grant
GBA Detail Library
A collection of one thousand construction details organized by climate and house part
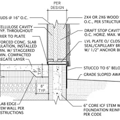
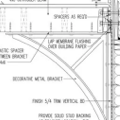
Replies
Grant,
As you apparently realize, your ceiling may collapse at any point. That means that for the safety of the employees, you need to get a structural engineer on the premises immediately. If the ceiling is in danger of collapse, it may not be safe for any employees to enter this area.
This type of facility is comparable to an indoor swimming pool. If the indoor humidity is this high, there is only one way to safely detail the air barrier and insulation, and that is to follow the PERSIST approach. The roofing needs to be removed, and contractor needs to cover the roof with a peel-and-stick membrane like Ice & Water Shield. Then the contractor needs to install several layers of rigid foam insulation above the peel-and-and stick. The last layer can be nailbase (rigid foam with OSB adhered to one side) -- perhaps one of the vented nailbase products. And then you need to install new roofing.
Of course, if the high humidity has damaged your roof trusses, you may also need new roof trusses.
If the building is worth repairing, you also need to detail the wall insulation carefully, and pay attention to air barrier continuity and thermal barrier continuity where the walls meet the roof.