Catskills PGH House : An Update + Questions

Hi all!
It’s been awhile and I’m posting with some updates and questions on my PGH build in the Catskills.
It has been almost two years now, slow but steady, and we’re finally closing in in on rough-in for plumbing, electrical and minisplit linesets, and am working on FFE now (Fixtures, Furniture, Equipment) I have a few questions to run by the community, see below, along with notes on latest house. Attached: Building envelope PDF, photos of latest house exterior, interior design layout from Sketchup (doing my best architect impression).
HOUSE INFO
* 1600 sq feet. Climate zone 6. Shooting for PGH. Floor: R30, Walls R38, Roof R-60, Anderson 400 Casement Windows, Dual pane Low E4 glass, and one Anderson sliding door. Two new Thermatru doors for two entrances.
* House is 2X6 walls, with added 2X4 interior wall for service cavity and added R value. Siga Majrex directional, variable, vapor control layer for air seal and vapor movement if needed (didn’t fully calculate condensation point).
* Rockwool insulation in walls, blown cellulose in ceiling, closed cell spray foam in floor joists. Lunos ventilation system from 475. New minisplits for heat / cool, replacing removed oil furnace baseboard. New stuv wood stove with makeup air.
* Pier and beam with dirt crawl space for about 75% of house. Newer addition has a mini foundation about 6’ down, also has mini foundation that is now clear (used to hold oil furnace and compression tank)
QUESTIONS
* There was great advice earlier from community on alternative to spray foam in floor joists, but but in practice pricing these options were too costly, as nobody wanted to crawl under there that long, making netted or plywood holding zones between floor joists to get cellulose or rock wool in there, also deal with the two poured mini basements. Same with trying to insulate the crawls space to include it as conditioned space, with two bilco doors.
* I have a quote for $9,600.00 to use Huntsman High Lift HFO Closed Cell Spray Foam at 4” for R30. It’s plastic, but here’s the eco pitch, “this product uses recycled plastic materials, rapidly renewable soy oils, and the blowing agent has zero ozone depleting potential.” No idea where they get this recycled plastic yet, need to ask. Question: Thoughts / experience with the product itself, in terms of VOCs, carbon footprint, etc? I know it’s not great, but would like to put best foot forward considering the situation.
* There will be some thermal bridging via exposed remainder of floor joists into cold crawl space. So I know the R value will be reduced, but am hesitant to also cover exposed remainder of joist with foam, as I’d like to see how things go with water condensation, etc. Builder and insulator agreed, also said it’s cheaper initial spend. There was suggestion for dehumidifier in crawl space, venting the PVC skirting, no need for vapor retarder along floor for now. They said any water coming up from soil or moving under house should evaporate, get grabbed by dehumidifier, should not condensate. Does this seem like enough, along with crawling under there after a few months or year to see if there’s any mold or rot going on, take it from there? Can do without a moisture barrier for now on top of soil in crawlspace?
* Floors and water damage concern. Leaning towards hardwood floors of some kind, wide plank panel style, light color, ie oak or something. Remote chance of cork but may not have time to figure that option. I’m paranoid about potential water damage to wood floor or floor joists underneath kitchen, bathrooms and stacked washer / dryer in . A junior architect from NYC who is helping with elevations for plumbing suggested waterproofing above subfloor, below wood flooring in these areas, ie some kind of membrane she’ll tell me about soon. I guess they’ve done it for renovations in city. It seems doable, except kitchen is tough, because it’s open format, where it would need to terminate in middle of wood floor, ie no wall. Also, it seems a bit iffy, like maybe all this does is make a shower pan for the water collecting under the wood floor and increase warp / rot / mold potentail. The spray foam insulator said closed cell spray foam is air tight but water still goes through it eventually, so accumulated water from a leak, etc, should drip down and into crawl space (in worst case, ie am not home and leak is occurring). Perhaps it’s better to just do the flooring and spray foam, hope for the best, and go with insulator’s input? Reason for paranoia: previous owner had pipes burst in winter, caused mold, and I had to pay to remediate as part of remodel cost.
* Blower door test. Not going for certified anything, but want to do blower door test to get air sealing best it can be. When is best time to do this? I’m guessing it’s after we do this rough in and do closed cell in floor joists, so everything is still exposed and can be tweaked / improved with air seal? Any advice, input, things to consider for this stage?
* Kitchen. I cannot find anyone to do plywood boxes with nice wood fronts for less than $15K, it’s crazy. Meanwhile, I can get an Ikea kitchen for about $6K that is not great environmentally, but a big saver, and would allow budget for a quartz waterfall on island, also counter and backsplash, to make for a decent end design + cost. If anyone has thoughts on alternatives before putting in Ikea order, please let me know. Am meanwhile going doing custom millwork bathroom vanities, wood shelves and desk using oak and maple from the property to try and make up for it. Also using kiln dried wood from site to make dining and coffee table, simple cuts off slab cut with prefab legs.
SIDE NOTE
If anyone wants to learn about DIY yakisugi (shou sugi ban, but fyi, that’s not the correct term), happy to share info / tips, just let me know. I did it with propane and flame thrower. Yes, it’s not the traditional way, also there is a carbon toll, but total fuel used was low and I often had to truly do it myself, in middle of nowhere, aka I can’t tie three long ass heavy boards together with twine, burn center like a chimney, then put it out safely. Also, a tip: I used Osmo one coat black stain on soffits, because they were already mounted on house…this stain is plant-based, expensive, but great, truly one coat (on hemlock at least). And very close colorwise, almost matches the charred wood cladding.
THANKS!
For those who responded to my earlier posts, THANK YOU!! It helped so much. Shout out especially to Michael Maines, PGH posse, the book, BS and Beer podcast for lots of learning early on. For anyone new who didn’t see earlier posts, here are links fyi:
https://www.greenbuildingadvisor.com/question/pgh-building-envelope-design-help-round-2
https://www.greenbuildingadvisor.com/question/plywood-baffles-wind-dams
GBA Detail Library
A collection of one thousand construction details organized by climate and house part
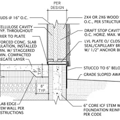
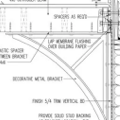
Replies
"Blower door test. Not going for certified anything, but want to do blower door test to get air sealing best it can be. When is best time to do this? I’m guessing it’s after we do this rough in and do closed cell in floor joists, so everything is still exposed and can be tweaked / improved with air seal? Any advice, input, things to consider for this stage?"
You do this after your air barrier is in place. Is drywall your air barrier? Then you do it after the drywall is in. Is the exterior sheathing the air barrier? Then you can do it after insulation but before drywall. In any case you want to do it as early in the process as you can so that you can do sealing before your finished surfaces are in and not worry about messing them up.
What you always have to think about is new penetrations. There's a lot of making of holes in the building envelope that happens in the finishing of a house, you need to make sure those holes all get sealed.
For the crawl space, I recommend this article:
https://buildingscience.com/documents/insights/bsi-009-new-light-in-crawlspaces
The biggest mistake you can make with a crawls space is having a poorly defined building envelope. And this is the way houses were built for the most part until very recently, crawl spaces were kinda sorta inside and kinda sorta outside. If you're insulating the floor, that is the boundary of the building envelope. It needs to be completely air sealed, all your mechanicals need to be inside the building envelope, and there needs to be a vapor barrier on the wet -- the bottom -- side of the envelope. Closed cell foam acts as an air barrier, vapor barrier and insulation layer, but you have to cover all of the framing. You also have to make sure there is a path for the floor assembly to dry upward -- your finish flooring has to be vapor open.
A dehumidifier in that space is terrible advice. It's outside the building envelope, it would be like running a dehumidifier on your front porch and trying to dehumidify the outdoors. Whoever suggested that simply doesn't get it, they're stuck in the old mindset of kinda-sorta inside, kinda-sorta outside.
Your plumber is going to want to run pipes in the crawl space. This space is not conditioned, and in zone 6 will be subject to freezing. Don't let him run the supply lines, there's no reason they can't be run in the conditioned part of the house. Drains are going to be a problem, particularly traps which will hold water and then freeze. The fixtures that usually have traps below the floor are tubs, showers and floor drains. Ideally you want those as close to the floor as possible, which the plumber isn't going to like because it's easier for him to run the drain pipe below the joists.
The plumber will probably be in kinda-sorta world too and will insist the crawlspace is protected from freezing. If it's properly done, it won't be.
Having written all this, I would recommend getting a quote for spraying the same 4" of spray foam on the walls of the crawl space rather than the ceiling. In most houses the walls have less area than the ceiling so insulating the walls is cheaper. Then if you roll out a vapor barrier on the floor, presto, the crawl space is inside the building envelope and a lot of things become easier.
Hi, this is solid advice, and the article you shared is amazing, thanks so much!
The suggestion to do 4" along walls of crawl space, add vapor barrier would be great. However, a problem is this house has two mini basements, with two bilco doors leading down to them. In discussions with people, it would require adding airtight doors at bottom of bilco stairs, then there is the transition between poured concrete basement walls and the crawlspace underneath to figure. So far, everyone has said it's too much headache and cost, don't do it, also who's going to crawl under there all those hours, not me kind of thing. This said, it is a more ideal setup...just too difficult to pull off.
From the article, it seems like a workable alternative for climate zone 6 is use closed cell spray foam, but also encase the exposed sections of floor joist to warm the wood and stop condensation, like attached "Figure 5: Warming the Wood"? And do a floor assembly that's vapor open to dry upward like attached Figure 8b?
The subfloor is plywood btw, but it’s coated with white mold remediation paint in most of the sections. This was done for good measure during that phase. I don't know if this will block some of the upward vapor movement?
Fyi, all plumbing supply lines will be inside the envelope, within a 2X4 service cavity on walls, except to the kitchen, where it unfortunately needs to run across ceiling that small service cavity, to avoid going along exterior wall, with freezing danger. So it’s just plumbing out to septic tank that will go under house. Good point about the traps, how do plumbers keep traps and run drain lines close to floor, not below floor joists? Is it drilling holes through joists? That seems structurally bad.
It seems like traps are the main issue though with too much water that could freeze? It seems the drain lines would not accumulate enough to freeze and clog, but also an issue?
I can ask plumber to take a look at this post, share what he thinks.
Btw, I think I was wrong about where dehumidifier advice landed. I think it was advice just for vents and fans on insulating floor joist option, dehumidifier for option where crawl space was within the envelope / conditioned space.
Thanks again!
So how are the mini-basements insulated?
They are not insulated now, just some cut rigid foam insulation stuffed into rim joist area and betwen floor joist gaps where they are resting on top of the mini basements. I don't think as well that previous owner insulated outside of the poured concrete wall...there is definitely no insulation on interior part of poured concrete wall.
With plan to insulate floor joist, the idea is just to continue same closed cell spray foam 4" layer below floor joists, and with this adjusted version from article you shared, also bottom of exposed floor joists, also into the rim joists. So this would form the continuous insulation and air seal along bottom of floor.
Thoughts? I know...not ideal...and I don't like idea to encase wood with foam. But so far, it seems the middle ground way to handle.
It would be legit to treat the basements the same as the crawl spaces, the ceiling is the building envelope dividing line. Do you have plumbing, HVAC, water heater etc in the basement? That would be a reason not to do it that way.
Oh, good question! So the well currently feeds directly 4' underground for about 10 feet, through to bottom part of the larger mini basement. There is electrical wire as well, ready to get it hooked up to switch, compression tank, water heater, etc. That's not done yet, waiting for upcoming rough in.
Original plan had compression tank in basement but water heater in the mechanical closet within building envelope. Plumber thinks water heater and compression tank should go down in this mini basement, below insulated ceiling, and add a heater and thermostat down there in case to keep things warm enough if needed.
It seems either way, there is some freezing risk for the portion of piping that goes from 4' depth up and into building envelope, or does that also become freeze risk for the entire basement with this insulation plan?
We could maybe create an insulated enclosure within basement for these items, with a door I guess, if needed...I'd like to find easiest, affordable way to handle.
> So far, everyone has said it's too much headache and cost, don't do it, also who's going to crawl under there all those hours, not me kind of thing.
Yep, this is very typical. Nobody wants to do it right when it's easier to do it wrong.
Ha, yes, this seems like a default approach sometimes...hats off to those wanting to get these things right, with good building science and all.
From the article, it seems like a workable alternative for climate zone 6 is use closed cell spray foam, but also encase the exposed sections of floor joist to warm the wood and stop condensation, like attached "Figure 5: Warming the Wood"? And do a floor assembly that's vapor open to dry upward like attached Figure 8b?
Yep. Exactly like that.
The subfloor is plywood btw, but it’s coated with white mold remediation paint in most of the sections. This was done for good measure during that phase. I don't know if this will block some of the upward vapor movement?
Most paint is actually quite vapor-open even if it is waterproof. You may have to contact the manufacturer to find out for sure. If it is a vapor barrier it's going to cause problems, there won't be any way for moisture to get out of your floor.
Ok, great, thanks.
One question with regard to those diagrams and way to handle it. The article says following: "Any foam will work for the wood warming—low density, high density, whatever. Recall, just by warming the wood you lower it’s equilibrium moisture content. Where things get difficult are with the vapor drive across the floor sheathing and the floor finish. Unless you stick to carpet, and ventilated furniture and ventilated cabinetry you are going to have to use high-density foam—at least 2 lb/ft3—due to its lower perm value. And at least 3 inches thick or thicker (gives you less than 1 perm at this thickness). "
Would you mind helping translate this? I think it means the planned 4" of Huntsman High Lift HFO Closed Cell Spray Foam will be sufficient?
And thank you re: input on the paint! I just emailed the mold remediator to ask if he knows, also to get brand / name of the paint used to contact manufacturer if needed. Is there a name of the specific measurement for paint used to show how vapor permeable it is?
The measure of permeability is the "perm" and the higher the perm rating the more permeable something is.
Generally with insulated assemblies you want the wetter side to have a vapor barrier and the dryer side to be vapor open, so that to the extent moisture gets into it, it can dry toward the dryer side. With a floor over a crawl space the wet side is the crawl space and the inside of the house is the dry side. What Joe is saying is that you need to have a really good vapor barrier over a crawl space -- 1 perm or less, which is at least three inches of closed cell foam.
If you can't swing a 1 perm or better vapor barrier, then you have to be extra careful to let the top side be able to dry. What he is recommending in that situation is only carpet, no furniture or cabinets with closed bases.
Regarding the use of HFO foam: the soy component makes a tiny, tiny difference. All foam insulation has had zero ozone-depleting potential for over 10 years now; they only advertise that to confuse people. If they use "recycled plastic materials," why don't they go into more detail?
I've been spec'ing HFO-blown foam for 5+ years now and if you have to use closed-cell foam, it's the best option. I have used it in situations similar to yours but I prefer to use lower-carbon materials when they will work; HFO-blown foam still has one of the highest climate impacts of any insulation, though it's much better than legacy HFC-blown foam.
On my most recent project on piers, the one in the lead image here: https://www.greenbuildingadvisor.com/article/all-about-helical-piles, I added 2x4s below the joists, filled the cavities with R-40 dense-packed cellulose and covered the underside with Zip sheathing. It's a more resilient and higher-performing assembly than yours on every level.
Be aware that wide-plank floors will have gaps in winter. I would not want a waterproof layer below the flooring. A few years ago I had a leak on a similar, existing assembly, with spray foam below one portion and a basement below another portion, and the wood flooring fared better over the basement.
Blower door test once your building envelope is airtight, which depends on what your air control strategy is. Then test again after equipment and vents are roughed in, and again after everything is complete. In your case, the last one be mainly for bragging rights so you could skip it if you want.
Environmentally, IKEA cabinets aren't too bad, other than the fact that they usually don't last as long as other types of cabinets. I used to build custom cabinets and $15K for a kitchen is not bad at all. The last time I saw a custom kitchen for that was in 2008. A lot of work goes into custom cabinets; I don't know why people think they should be cheap, then turn around and spend many thousands of dollars on a countertop. I would forgo quartz and I'm not a fan of waterfall counters anyway--why do people want their countertops to touch the floor?!--I would put that money into higher-quality, longer-lasting, locally-made cabinets, and/or the building envelope.
I didn't realize that about shou sugi ban, which is kind of funny because I recently helped a client order a houseful of it from Nakamoto: https://nakamotoforestry.com/yakisugi-or-shou-sugi-ban-learn-what-you-should-call-it-and-why/
Hi Michael,
Sorry for some delay responding. I'd like to do your design of 2x4s below the joists, cavities filled with R-40 dense-packed cellulose, then covered with Zip sheathing.
There are two challenge though which has made it seem impossible, or at least incredibly costly to achieve : 1) 3/4 of house is on piers, 1/4 is on two different mini basements, poured concreted foundations with bilco door entrances 2) Cost and not even sure I can get someone to crawl around that long and deal with unified approach that insulates and air seals
The builder meanwhile suggested an alternative to my plan above, which is to try and insulate the crawl space in all areas except these two basements, by doing 4" HFO spray foam in rim joists, down side of crawl space interior, then along the ground. And when arriving at the basement concrete, 4" up the side of the concrete to the floor joist / subfloor. And then on other side inside the mini basements, do the 4" of spray foam inside floor joists, and per the input here, also encapsulate the floor joists too, for preventing moisture accumulation.
In any case, it's going to be a ton of crawling around in limited space, while handling crawl space. But with the HFO foam approach, it seems 1) More possible to crawl around and get pretty close to airtight on first round 2) Get someone to actually do it.
An advantage to this approach is a lot more of the plumbing will be protected within the envelope, almost all of it it, except the entry point from well into one of the mini basements, water heater, compression tank, and the water line that goes up into the conditioned space for rest of water lines. This may require making a small insulated section of the mini basement that houses these lines. Or maybe there can just be a small electric heater in basement, go from there? The plumber does not seem concerned about freezing danger for these parts of water system in this basement. I'm curious to hear input.
I don't have a drawing of this insulation approach, but see attached, a basic mockup showing where the mini basements are located, while all the rest is crawl space on piers, with limited access, ie 24-36" max from dirt ground up to floor joists. This frankenstein setup on house comes from being two additions added to original that was on piers. The first addition added smaller mini basement, second additional the larger one. I have no idea what led previous owner to do it this way.
Hopefully text description and drawings are understandable enough to provide some feedback? Hope so, and can reply with any further detail or try to draw in piers if helpful! Thanks.
Soulincode, there is only so much help an internet forum can provide; it sounds like you have a good grasp of the important concepts and enough constraints that only you can decide what the best course forward is. Or a local expert who could help you, but I know that's not an option in your case.
"All foam insulation has had zero ozone-depleting potential for over 10 years now."
I feel like there's a qualifier missing between "all" and "foam."
All newly installed foam? All foam insulation used in the residential construction industry?
There may be nuance I don't understand; I can't find the straightforward information I've used in the past, but there is information here: https://www.epa.gov/ods-phaseout/phaseout-class-ii-ozone-depleting-substances
Never mind, I misread "ozone depletion" as GWP.
That's how they get ya! ;-)