Cathedralizing attic spaces in a Cape

Context:
I have modified cape style house in zone 5. Originally built in the early 70’s, extensively renovated and added onto in the early 2000’s by the prior owners. About 1/2 or 2/3’s of the roof / attic spaces are accessible without demolition, though these spaces (e.g. the “top attic”) are mostly pretty tight. The remaining 1/3-1/2 of the roof is above sloped ceilings which appear to have baffles and fiberglass insulation. All of the roof pitches have a direct path from soffit to ridge vent. HVAC serving second story is in the “top attic”. Shingles are around 15 years old and seem in good condition, so don’t want to tear them up for exterior roof insulation.
Objective:
Main goal is simply to increase energy efficiency, as well as reduce variability (“cold areas” vs. “hot areas”).
Plan:
In the attic over the addition, there is currently about 6 or 8 inches of fiberglass insulation, and judging from the cold air coming down from the can lights below, its pretty leaky (its also one of the coldest areas of the house). There are 2×10 rafters 16″OC and a vent at the top of the ridge. To improve the insulation and air sealing for this area, I was planning to “cathedralize” the attic, but because I can’t access 100% of the roof, I was planning to maintain a pathway from the soffit to ridge vent. Specifically I was planning to make a 1.5″ baffle using 1.5″ rigid foam with some thin strips of the same foam as spacers beneath. I was planning to also add 2″ rigid foam strips under the rafters. I would spray in ~2.5″ of ccSPF, leaving ~5.5″ in the cavity for R-23 rockwool batts. I calculate the cavity R at about 45. For the gable end walls (2x4s 16 OC), I was planning to repeat the 2″ foam on the studs, spray on ~2″ of ccSPF, and finish with R-15 rockwool batts. That should be R-27 in the cavities so again above code.
Questions:
1) Overall does this seem like a reasonable plan? Any major issues I’m missing or opportunities to make it cheaper / less labor / better performance?
2) For the homemade foam baffles, since there is ccSFP on top, can I skip the air sealing and just kind of “rough fit” these and then let the ccSPF do the rest?
3) Would I really need to pull up the existing insulation from the floor / ceiling below once complete? And some rigid foam previously installed on a vertical wall leading to conditioned space from this attic?
4) Any tricks to connecting the new baffles and insulation to where the existing baffles and sloped ceiling fiberglass insulation emerge from below? I think the basic idea is to keep an open connection baffle to baffle, and then seal out any other spaces (e.g. cover the fiberglass from below with a piece of foam board to force any air that is coming up from the soffit through the fiberglass into the new baffle)?
This has gotten pretty long as it is — I’ll post separately with a similar set of questions but some different specifics for the “top attic” and a large knee wall area in the original 1970’s part of the house.
GBA Detail Library
A collection of one thousand construction details organized by climate and house part
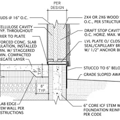
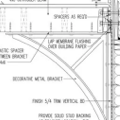
Replies
Hi CapeCape27.
I think your plan is reasonable and maybe your best bet for increasing R-value, air sealing, comfort and efficiency. As you probably know, closed cell spray foam is not an environmentally responsible choice, but sometime is a problem solver. Perhaps it's worth taking the time to look for a product with a less-harmful blowing agent than the one used in most closed-cell foam. This article will offer more info on that issue: Is Using Closed-Cell Spray Foam Worth the Trade-Offs?.
You can use the closed cell foam to air seal the baffles, most builders would, I think, though there are reports of the foam pulling away from framing when not installed perfectly.
I don't believe there is any reason that you need to pull up the existing insulation from the floor, but you may want to if you are not planning to bring heating and cooling to this space and want it to be comfortable. Hopefully someone with experience in this situation will offer more thoughts on this question.
I don't have any tricks for connecting your baffles, but it looks like your new site made baffles may be able to slip over the existing baffles. You will need to block the eaves with a backing for the spray foam and should probably have the spray foam lapped onto the top plates. This can all be part of the same solution, I bet.
Thanks Brian! Glad to hear I wasn’t totally off. It seems this topic of insulating capes has been discussed many times, but somehow each situation seems a bit different and I couldn’t find any examples with exactly my issue.
For the ccSPF, thanks for the reference to your blog noting some “greener” options than the standard blowing agent. I’ll have to see if I can access one of these.
I haven’t decided whether I’m going to try to do the spray foam myself or hire a company to do it. I am not sure if a company would be as careful with uniform thickness and ensuring a good air barrier, but I guess they might be able to get materials more cheaply when buying in bulk, and might have access to a broader array of options. Any advice on that question?
For the rigid foam, any recommendation what kind to use? It sounds like polyiso is better in both performance and environmental impact, but I think I would want to avoid the foil backer which seems to be what is most available as I don’t want to accidentally create any moisture trapping issues.
Hi CapeCape27.
I believe you would be fine with foil faced polyiso. You could also use EPS. You should avoid XPS for environmental reasons and because there is no compelling reason to use it in this situation.
As far as the spray foam instal, price both options. If hiring the work out is affordable, vet the contractor well. It can seem like we get a lot of horror stories about spray foam installs on GBA and other online forums, but that's because people don't post their success stories. If they did, you wouldn't have concerns about the contractor.
Thanks Brian for the advice. Its a good point, if all goes well you don't tend to go post about it online, whereas when things go wrong, its a different story.
Now that we've sorted out that area, the next challenge is the top attic and a large knee wall space that actually directly communicates with the top attic (from the knee wall area, you can look up over the ceiling of the adjacent room into the top attic).
The top attic has a peak ceiling height of probably 3.5-4 feet with a central ridge beam (maybe 4x12) with a vent above and 3x6 rafters spaced 30" or 32" OC. The sheathing is actually boards ~5 inches wide running perpendicular to the rafters. The rafters and sheathing have been painted white (I assume this plays some sort of role in vapor management?). From what I can see in the attic, the rafters rest on a pair of ~4x10 beams toward the front and back of the house. Beyond these beams the space gets very narrow but I can see fiberglass and at least in some cases baffles coming up from the pitched ceilings on the second floor. The HVAC unit for the upstairs is located in this space, so there are ducts running everywhere.
The floor of this space is covered with ~5.5" of pink fiberglass between the 2x6 ceiling joists, with an additional ~4" of yellow insulation on top, in parts. Oddly, there is fiberglass batt insulation on the gable end walls (kraft paper facing inward) despite the fact that the other side of these is outside (just like the uninsulated rafter bays). There is also interestingly a ceiling fan, like you might find in a bedroom, in the top attic as well.
Given the tight spacing, I am a little hesitant to tackle this area, but on the other hand, its seems very inefficient, even after probably some attempts by prior owners to make improvements (e.g. the gable end insulation in the vented attic).
The basic plan I had in mind was similar to the other space. I'd track as far back as I can go between the rafters, create a soffit dam and connect the existing baffles where available to a site built 1.5" baffle made of rigid foam. I'd also add 2" rigid foam to the rafters, and fill the cavity (~4.5") with a "green" ccSPF. I could alternatively put continuous rigid foam 2" under the rafters, but I think that would be more difficult in the cramped space. I think the roof R-value comes to about R35 which is below code, but with reduced thermal bridging, might perform at or above. I'd probably also leave the existing fiberglass unless that was an issue. For the gable end walls, I'd do the same as in the attic of the addition -- add rigid foam strips to the studs, flash 2" ccSPF to air seal, and then add rockwool batts to fill the cavity.
Questions:
1) Again, overall does this seem reasonable? Anything I could do to reduce cost or labor, or improve performance and environmental impact? Its a lot of ccSPF but hopefully I can find some with low impact blowing agent and it seems the only practical way.
2) Am I crazy to tackle this at all in this space? Detailed air sealing below the existing deck and insulation seems even worse, but its a lot to accomplish in a tight space
3) There are lots of somewhat mysterious cavities created by the original structure plus renovation. I assume the strategy is just to seal these off from the now conditioned attic, assuming they may directly communicate with vent spaces, or have major leaks to soffit vent spaces. Is there any risk to a "when in doubt, seal it out" approach?
4) As before, any issues if I leave the existing insulation? Especially with (probably leaky) HVAC equipment in this relatively small space, I think it will be pretty well conditioned.
Thanks for the help!!