Moisture in Vented Low-Sloped Shed Roof

Hello
I’m having an issues with a roof assembly that we constructed last year (Newfoundland, Zone 6). It was part of a home that the client was renovating. I’d like to run it by the good folks on here to see if I have it correct.
It’s a low-slope shed roof constructed with TJIs. The top side of the roof is butted into the wall above. The lower side is on an exterior wall with vented soffits. It was constructed as a vented assembly with the following:
Drywall
6 mil poly
strapping
Fiberglass insulation
Ventilation baffles/air space
Roof sheathing
Torch On Roofing
The client noticed some water staining on the ceiling and I’ve been by to check it out. The roofing was very well done and flashed well so I’ve ruled that out. I also popped off the siding above the roof/wall intersection and no signs of anything going on there. I believe this is a condensation/air leakage issue from inside. I popped down a couple of the wafer style pot lights and there is definitely moisture in the assembly (frost on the underside of the roof deck).
The RH was very high in the home when I visited. The clients enjoy to cook (a lot) and there’s plants, pets, etc. I’ve left them with a hygrometer and a dehumidifier and have asked them to try and keep the RH down around the 40% range so we can monitor this under normal circumstances going forward.
Because this “vented” assembly is only really vented on the bottom, then there’s not much drying potential or forgiveness for having any issues.
My plan, and this is what I’m hoping for advice on, is to follow these steps:
Get the RH down in the home and see if that helps over the next few weeks
If it doesn’t, pop off the dozen or so pot lights and seal those to the drywall with caulking
If these don’t help, take the ceiling down, spray it with closed cell foam and re-drywall, turning it into an unvented assembly with a hot roof.
I’d appreciate any advice on this or if i’m missing anything obvious here.
GBA Detail Library
A collection of one thousand construction details organized by climate and house part
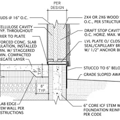
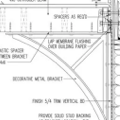
Replies
Dan,
Unfortunately I suspect better air-sealing won't be enough, and you will need to vent the top of the roof where it meets the wall. Be careful how you do that as vents in that situation often get wind driven rain entering them.
Thanks for the reply Malcolm. The top vent was debated when we constructed this but I decided it would create more issues than it would solve. With the torch on and then windows above, the best I could see was to vent it into the wall above. It would have been a non-typical detail and to tell you the truth may not have worked very well anyway
A common way here is to install mushroom vents on the flat roof. One or two is typically all that is needed for a kitchen size addition if it has an attic space.
In your case with cathedral ceiling, if you can locate your rafters and set the vent above it so it can vent two bays, you can get most of the roof vented. I-joist webs are thin osb, even if one bay is unvented it can dry through the web to the next bay over.
The other option is to install gable vents on the sides near the top of the shed roof. You would have to do some drilling to connect each rafter space, most could be done with a long 3/4" flex auger bit, the rest through a couple of holes in the drywall.
Venting your way out of leaks is usually a loosing battle. Most disk LED lights do seal pretty well so if the holes are the correct size and the lights seem to sit tight, you are probably OK. You might want to check the roof to wall connection on the house side. These tend to be a hard area to air seal well, 20' or so with a small gap adds up to a very big hole.
Closed SPF is a guaranteed fix but a messy install.
I think your correct about the pot lights. The electrician did a good job installing those. Holes are nice and tight and the spring clips seem to pull it tight. I've looked into a bunch of way to seal those in riskier assemblies but usually just leave it and those foam gaskets do the trick.
I appreciate those other suggestions as well.
The front of the home is very exposed so that much direct roof venting is out of the questions. Sorry for not explaining the location of the home better than I did. I think wind driven rain would cause trouble there. The only way I could figure to vent it was to create some sort of a channel in the wall above that would let it vent higher than the wall/roof intersection. It is currently connected to that wall but doesn't have a clear air space as such that air can flow freely through.
I've reviewed this with my very understanding client and we've come to the conclusion that the best way to proceed is to take down the gyprock, remove the fiberglass insulation, let the structure dry out and install the closed cell foam.
I'd like to tackle this job asap. Is there any issues with closed cell foam being applied in the winter time. The home will be heated but the roof deck will most likely be cold with snow/ice sitting on it?
I'm also leaning toward only installing closed cell foam and not taking the flash and batt approach to bring the R-value up. This is an older home where humidity is an issue and I think the risks of having problems again are too high to have to take all this apart again.