Cathedral roof options

I have looked over many posts and can’t seem to find the answer for this roof issue. Contractor removed a tile roof and wants to install a new roof this week. The roof construction consists of exposed 1-1/2″ T&G decking, 5/8″ plywood, two layers of 1/2″ fiberboard, felt, and ceramic tile. Roof is approx. 5/12 pitch in a 4A climate zone (suburban Philadelphia area).
Owners moved in this summer, so have no history, but had some recent leaks. When the contractor removed the tile he found that much patching had been done in the past and some felt, fiberboard, and plywood were deteriorated, mostly near the bottom 1/4 of the roof. I think the leaks were partially due to tile issues and probably significant ice damming.
This is a single slope roof with a clerestory window at the top. Because of the window sill height, cost factors, and architectural factors, installing an ideal roof is not practical. I am thinking about the following, but have concerns:
Covering the T&G decking with plywood (preferred) or OSB. Either taping the seams or placing an air barrier above this (recommendations?). The two layers of 2″ polyiso. Then OSB roof sheathing, ice and water shield (entire roof) , and asphalt shingles.
My concerns include the lack of ability for the roof sheathing to dry outward or inward, roof sheathing attachment (beams are spaced approx. 8 feet o.c. oriented side to side), the potential for ice damming with an unvented roof and less than ideal level of insulation, and picture framing at panel joints. Giving up the ice an water shield may allow some drying, but maybe with a greater chance of water penetration, and then the ice and water shield at the eaves would trap the moisture. The roof is about 30 feet from eave to top and with the height limitation adding ventilation is out of the question without significantly reducing the amount of insulation. Changing the clerestory windows has been rejected.
Any advise or guidance would be greatly appreciated.
GBA Detail Library
A collection of one thousand construction details organized by climate and house part
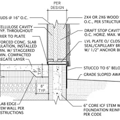
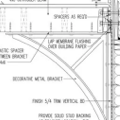
Replies
Mark - 4" of polyiso ( 2" of polyiso covered with 2" of EPS may give you a more optimal R-value since polyiso loses R-value when it's cold) will certainly be a drastic improvement over what you have now. Ice and water shield on the deck,as an air barrier and vapor retarder, covered with 4" of foam and then plywood screwed through to the decking should work o.k. The plywood with underlayment and asphalt shingles won't dry to the outside at all anyway, or minimally, but this is the same situation for many roofs with foam under the sheathing, or SIP panel roofing.Keep the plywood dry and you won't have to worry about the plywood drying. No moisture will diffuse through the I&W shield from the inside. The deck T&G will dry to the interior. I would not recommend osb. Good luck with the project.
Mark,
The biggest problem with the plan has nothing to do with drying to the exterior. (Roofs with asphalt shingles can't dry to the exterior in any case.) The biggest problem is insufficient R-value.
The foam layers need to be thicker.
For more information, see How to Install Rigid Foam On Top of Roof Sheathing.
Mark- is there any insulation in the rafter bays? If so, how much?
Kevin- in a zone 4 location 4" of polyiso will outperform 2" polyiso + 2" EPS on a total energy use basis, even if there were R30 under the roof deck (so that it met IRC code min.) The mean January temp is above freezing, and the mean 12 coldest weeks is north of 40F. The performance of polyiso peaks when the mean temp through the foam layer is in the 50sF, outperforming it's labeled R-value, and doesn't drop to the performance of EPS until it's mean temp is below 45F. So the outer 2" of polyiso might underperform EPS for a few weeks in January, but unless there is LOT of cavity insulation the mean temp through the outer 2" of polyiso will average above 45 most of the winter, and thorughout the shoulder seasons, outperforming EPS by quite a bit.
Thanks for the replies. The only insulation will be what is above the roof sheathing. Cost is a big factor here. I believe that the 5/8" plywood presently installed above the exposed T&G ceiling is in good condition, so keeping it would be a big cost savings. I'm thinking that taped plywood seams wood work as an air barrier? I know that the amount of insulation is less than ideal, but it is a huge improvement of what is there, and ice damming in this area is not generally a big concern. However, I think I am more worried about the potential for water penetration due to ice damming that trapped moisture. Hence the desire to use ice and water shield on top.
It does not appear that internal moisture has been a problem is the past. The house has large single pane windows (that's another story). If internal moisture is not controlled the windows should reveal that condition long before it is an issue with the roof.
Bottom line is how much risk of an ice damming problem with this R valve. I believe that I figured that with an outside temperature of 20 degrees F and assuming an R value of snow between .5 and 1, the roof surface would be 30 degrees with 6-1/2" to 13" of snow. That is more snow that we commonly see on roofs, and 20 degrees is below average. I guess I know the answer-ice damming will happen, but probably not often. So, what is the best compromise?
Mark,
Q. "I'm thinking that taped plywood seams wood work as an air barrier?"
A. That's right.
Q. "How much risk of an ice damming problem with this R value?"
A. You might get an ice dam, but you won't get leaks if you include Ice & Water Shield. Not the best approach, of course, but that's what a lot of roofers do.
At only 4" of continuous polyiso it's a pretty crummy performance point relative to IRC code minimums. If there's room for 6-7" of fiber insulation under the t & g it would bring it up to something like code min. performance, and cut the ice damming risk to near-zero in that climate.
But dealing with the large single pane windows is probably a higher priority from an energy use point of view. Low-E exterior storm windows over old single panes improves performance to near code-min levels at a fraction of the cost of replacing them with code-min dual-panes. They're available for non-operable picture-window type windows, as well as operable single & double hungs. The Larson low E storms sold through box stores aren't bad. It's worth the up-charge for the "Silver" or "Gold" series if it's going over a double-hung rather than an inoperable window, rather than the "Bronze" which leaks a lot more air. Low-E storms cut the condensation potential dramatically.
Thanks again for the replies.
Martin, given the limitations they probably can live with that. It has to be a big improvement over existing conditions, but I do not want to create any new problems.
Dana, adding insulation and a new ceiling is not an option due to cost, etc. Numerous walls have floor to ceiling windows. Most are very large panes. Windows are a big energy problem, but for now closing up the roof before winter is top priority.
Floor to ceiling ~R1 windows... (yikes!)
...definitely the larger energy problem!
DANA - Thanks for that clarification. Martin and Dana - Sometime on already built houses we have to compromise energy efficiency, cost and aesthetics. In this case, Mark has a roof that can only handle 4" of foam. Any more blocks his clerestory windows, any insulation added inside takes away his nice wood ceiling. 4" of polyiso will be a dramatic improvement over 1" of fiberboard. Down the road, maybe he could add insulation under the deck and put up an air barrier and some nice new wood, and really take care his roof heat loss and ice dams. And then those darn windows….
Kevin: They're out there! I have some in-laws who bought an architecturally interesting ~1960-vintage house in Massachusetts earlier this year that came with large amounts of single pane glass. They upgraded the windows to U0.28-ish prior to moving in last spring. They THOUGHT they had dealt with the worst of it, but it turns out they were just getting started.
During they summer they discovered just how badly insulated the low-slope roof was, when the pair of noisy roof mounted AC units could not keep up with the load(!). Furthermore, the house began to reek from outgassing of the 50+ year old ceiling & roof deck materials, driving them crazy. One of the AC condensers was 5 tons, the other 4, on a house with 2000' above grade, and another 2000' of finished walk out basement facing east, with fairly modest amounts of west or south facing window area. The AC ducts were insulated, but like the AC units, completely above the roof deck (!). The membrane roof had recently been replaced, maybe year prior to the purchase, with 1-1.5" of rigid polyiso installed under the membrane. Further inspection determined that some sections of the roof only had 3/4" fiberboard between the new polyiso & plywood, with nothing in the rafter bays, other sections had some R11 batts between the rafters, still others had a couple inches of vermculite. Great...
When they called me in to assess the situation it was maybe 70F out and sunny, but the membrane roof had already hit ~160F by mid-morning. Given that most of the ceilings were cathedralized,limiting the ducting options, and that the rafters were 2x10 making it impossible to even hit code-min, my first and only recommendation was that they sell off the fairly new AC units as salvage, get rid of the duct-sculpture, and build a new roof superstructure over the original to accommodate newer much smaller air handlers & ducts, and ground mount the much-downsized single condenser unit on the windowless north side of the house.
The did all of the above in only 6 calendar weeks that began half-past October (without involving me further) scrapping the 25 year old hydronic boiler and the 50+ year old hydronic radiant ceiling heating system, installing a right-sized condensing gas furnace in the micro-height attic that housed the much smaller ducts, and installed a Venmar HRV to boot, and added an office addition over the garage (partly to provide a duct & utilities chase to heat/cool the lower level with the same equipment without destroying the architectural integrity of the place.) They haven't given me the nickel tour of the new-improved mechanical systems yet, but I was over there just last night for a family celebration, and the difference in comfort level (and indoor air quality) was dead-obvious.
Is / was that house ever destined to be a paradigm of energy efficiency? Not even close! But I'm sure they've cut the annual energy use by more than half, and gotten a lot more comfortable in the process. Not everybody has the depth-of-wallet to pull it off in one fell swoop like that, but it's definitely "worth it", turning an nice looking but uncomfortable energy glutton into something far more reasonable.