Cathedral Ceilings Retrofit – Zone 5

Hi All,
I have house just north of Boston, in Zone 5. It is a contemporary home built in 1983 with nearly 100% cathedral ceilings. I have an active leak on one of the roof sections, and as such will be replacing the roof very shortly. The roof section is 6/12 pitch 22 feet wide and 28 feet high with two layers of asphalt shingles.
I would like to address some of the shortcomings of the existing roof system which are:
Currently inadequate ventilation, with eave vent but no ridge vent. The rafters on this section are 2 x 10, and I suspect the fiberglass insulation is nearly 10 inch thick allowing very little if any ventilation gap. Consequently, I experience awful ice dams and icycles. This is a post and beam house, and there is poor air sealing between the beams and the various ceiling sections (blueboard with plaster skim coat).
I would like to rectify the ice dam situation and would appreciate some input as to the most cost effective way to do so. At the moment, these are some options based on my limited research:
(1) Remove existing asphalt shingles. Cut portions of plywood sheathing out. Remove fiberglass batts. Apply Icynene foam. Paint ceiling with Vapor retarder and caulk gaps between beams and ceiling.
Pros: Seems to solve my ice dam issue, improves insulation. Does not mess up rakes or fascia.
Cons: I am very nervous about any residual smell after foam application. We have a very smell sensitive family, and I have two kids with immune disorders. It just seems like Murphys law that things can go wrong here even though all the marketing hype tells you foam is safe and doesn’t smell.
(2) Remove existing asphalt shingles. Use Hunter Cool vent panels attached directly over existing sheathing (what thickness)? Fill existing eaves vent with foam to seal. Apply new shingles over hunter panels.
Pros: No foam application so no risk of smell.
Cons: My rakes and fascia would have to be adjusted / added for six inches, which would not match the rest of the house and may look poorly. Not sure about the cost.
(3) Stay with standard roof and simply apply ice and water shield to deal with ice dams when they occur and hope that it works. Live with icycles.
Pros: Cheapest solution. Does not alter rakes and fascia.
Cons: Hope that it works (for twenty years).
(4) Remove shingles over existing sheathing. Roofer is proposing to build cold roof directly over existing sheathing with 3/4 inch strapping and new plywood on top.
Pros: Less expensive than foam and Hunter panels. Results in only an inch and a half of rake and fascia adjustment which can be handled by a drip edge.
Cons: Does nothing to improve insulation. Also I have a concern that I am getting some condensation on the underside the existing sheathing which causes mold. This would not improve this and may make it worse.
What are your thoughts as to the best solution for my situation (I don’t have an unlimited budget)? Do you know of contractors in the Boston area who are experienced in solving this situation effectively?
GBA Detail Library
A collection of one thousand construction details organized by climate and house part
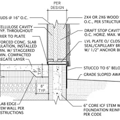
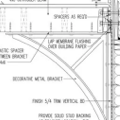
Replies
Bernie,
I think it would be irresponsible not to improve the insulation on your roof at this time. Since you are replacing your roofing, now is the time to improve your roof's R-value.
The Icynene plan would work if your rafters were deep enough, but they're not. (Your existing rafters are probably 9.25 inches deep). In your climate zone, the code calls for a minimum ceiling R-value of R-38. If your Icynene contractor could fill the rafter bays completely -- and I doubt that he or she can, because your plan is to work from above, and it will be difficult to shave off any excess foam -- that would provide only R-34. You could, of course, settle for that amount of insulation if you want; it will still perform significantly better than fiberglass batts. The vast majority of spray foam jobs are completed successfully, without any odor problems. If this approach seems risky to you, however, it's perfectly understandable if you choose to avoid spray foam.
You could also add rigid foam on top of the roof sheathing, using either the Hunter panels as you propose, or another type of nailbase or rigid foam. This approach will perform better than the other options your propose. According to most building codes, this approach requires at least R-20 of rigid foam. (For more information on all the various approaches to your problem, see How to Build an Insulated Cathedral Ceiling.)
If you are worried about the cost, you could get estimates for both approaches -- installing Icynene and installing R-20 of rigid foam -- and decide which way to proceed based on cost.
Good luck!
Thanks Martin.
I reviewed the link provided and the comments and it was helpful.
One question - if r-20 rigid foam is added on top of the existing sheathing, is it necessary to have a ventilation channel as included in a Hunter Panel Cool Vent product? Or, would R-20 rigid foam directly applied over the sheathing with OSB directly fastened over the rigid foam, and then shingles be sufficient to improve my ice dam situation. In this case I would then have my original fiberglass batts (nominally R-30), original plywood sheathing, R-20 rigid foam, new sheathing and shingles.The omission of the ventilation channel above the rigid foam improves the situation with my existing roof aesthetic.
Bernie,
Q. "If R-20 rigid foam is added on top of the existing sheathing, is it necessary to have a ventilation channel as included in a Hunter Panel Cool Vent product?"
A. No, although some builders prefer the ventilation channel for added belt-and-suspenders insurance.
Unlike A.J., I've never heard of moisture problems in roof sheathing in an R-38 or better roof that includes R-20 foam on top of the roof sheathing. Failed roofs have much worse specs than these -- and most failures involve air leakage. Pay close attention to air tightness, and you should be fine.
Martin, a home on Brant lake with what sounds like the exact air leaky beamed cathedral with fitted between air leaky joints..... Exists.... Moisture rot city..... Both successful contractors near here that exclusively build with ridgid foam always vent above the foam. They have decades of experience. I'll leave it at that.
Martin's related blog.....
https://www.greenbuildingadvisor.com/blogs/dept/musings/how-build-insulated-cathedral-ceiling
Personally, I would take the belt and suspenders approach and vent it. If you choose to go with rigid foam, try to find Polyiso roof sheating. Per Martin, to get R20 with polyiso foam, 3 1/2" is sufficent, and is easily covered with an additional 1x6 fascia piece. You will ever have a better opportunity to do it than now.
Bernie,
If you use spray foam with higher r-value than Icynene, you can achieve a vented, code compliant roof without adding exterior foam. We have worked on a number of similar projects and use either semi-closed cell foam at r-5 per inch or closed cell at r-6.5/" depending on the rafter depth. All work happens from the outside and there is no need to air seal the ceiling from the inside. It is necessary to remove the sheathing completely so coordination with your roofing company is crucial. In your case, closed cell foam will give you a generous ventilation area. It is not cheap but works very well and the exterior details remain unchanged.
Torsten,
That is a solution that is of particular interest and that had not come up before. Am I correct in understanding that 6 or so inches of closed cell foam could be applied from the roof (sheathing removed). Provided the foam applicator is diligent in keeping the existing vents open, and also a ridge vent is retrofitted, this would leave around 3 1/4" of ventilation space under the sheathing. This would seem to provide the best of both worlds:
- Ventilation under the roof deck
- In excess of 38 R-value
- No modification to my existing rake and fascia system (the house has significant ridge and rake lines)
Again the downside is the risk of "lingering smell" from the foam application.
I appreciate all of your input.
Venting over ridgid foam sheathed roofs is less risky than no vent. There have been roofs destroyed near me by trapped moisture.
Ice and water layer is least expensive by thousands and thousands. If you have natural gas your payback for superinsulating the roof does not exist. Also use Grace's best product and reroof during warmer weather only.
Caulk with geocell or any top quality caulk the best you can to make your ceiling airtight. Add ridge vent though I would cut opening smaller than called for. Lstiburek says upper vent area should be smaller.
If you do go with ridgid foam there is quite a market of used foam that sells for half price or less coming from commercial flat roofs and roofers.
I agree that spray foaming would seal well and does not need venting in most applications unlike ridgid foam. Expensive. Let us know the costs of your options when you get your estimates.
Water blown Icynene is to me one of the least risky spray foam choices.
Torsten, in applications such as you suggest, do you generally apply any sort of "slip sheet" to prevent the foam from bonding directly to the drywall?
AJ,
I sometimes find it hard to understand you. You warn of roof failures (I think) when someone installs R-20 rigid foam on top of roof sheathing and fluffy insulation below. If such failures exist -- and I've never seen any -- there must be some serious air leakage problem. I always advise people to pay attention to air sealing.
You wrote, "a home on Brant lake with with what sounds like the exact air leaky beamed cathedral with fitted between air leaky joints." I'm not sure what this means. Is this a house with a failed roof? If so, it sounds like you are telling us it is "leaky" and "air leaky." If that's what you're telling us, then there's your problem. Rotten roof sheathing in a cathedral ceiling is almost always due to air leaks.
Martin, am just today working on another moisture destroyed project. A flashing problem exacerbated by ridgid foam used under drywall 20 years ago.
Yes, I am seeing terrible rot problems more often then not in framing that has ridgid sheet foam applied to either the inside or the outside. And in walls and roofs.
It is easy to make mistakes with ridgid foam, superinsulating, and or various air barrier builds.
I know what has failed here. Ridgid foam jobs.... Several times have trapped moisture. Pictures possibly.... Someday.
AJ,
I'd still be interested to know if any of these failures occurred on a roof with R-20 rigid foam above the sheathing and more insulation below the sheathing -- assembled with attention to airtightness. I bet not.
Martin, Bernie's ceiling description "This is a post and beam house, and there is poor air sealing between the beams and the various ceiling sections (blueboard with plaster skim coat," to me sounds just like the Brant lake home (leaky.) Also all across the country thousands of kit log homes have been built similarly. I built some of them twenty years ago. Yes I am discussing TYPICALLY BUILT AIR LEAKY CEILING ASSEMBLIES. And I stated that in prior posts that somehow have you flummoxed.
I do believe any assembly if built perfectly can work. However experience has proved to me that much is far from perfect in home building. And I know you know that.
I think we agree Martin on most points always and on this topic too.
Bernie, Do you have can lights in your ceiling? Are you 100% positive you have a leak from the outside and not moisture buildup on the underside of your roof sheething? How old is that top layer of shingles?
If it's coming from the inside, I wonder if two inches of foil faced polyiso foamboard glued on the sheetrock ceiling, from the inside, taped and caulked with another layer of glued sheetrock would be a cheaper option.. Cut the power to the cans of course and go right over them.. I wonder if this would keep the dew point out of your assembly...
Do you have any mechanical interior ventilation? Passive air inlets? Basement moisture problems? Wall air sealing problems? Maybe a blower door test would help..
Can you see the beams from inside the home? Could always go right over them from the inside as well, to get rid of that thermal bridging.. Add roxul insulation to fill the void..
You'd still want to cut and create a ridge vent.
These are just random thoughts from someone without the experience of Martin or AJ.. So don't give them any weight without feedback from the gurus on this forum.
Thank you for all your comments. I am in the process of getting actual quotes re some of the options proposed and will report back.
One question: If I proceed with a medium density foam sprayed from above (sheathing removed), this will likely leave a small gap between the foam and the roof sheathing. As Martin has mentioned in other posts, the installers will likely no completely fill the cavity given the difficulty of shaving off the foam. Does this gap between the foam and the sheathing in an unvented assembly pose a problem?
Torsten proposed a solution which seemed ideal at first, which was to use closed cell foam but leave a generous ventilation space. This would involve making sure the ventilation openings do not get sprayed in. Then I remembered that several of my rafter bays are blocked by skylights, and also one terminates onto a chimney. Thus, for several bays, eave to ridge ventilation is not possible,
Thoughts?
How much life is left in the remaining roof shingles? (The non- cathedral portion)
Bernie, with sprayfoam, you are sealing up the air leaks so you don't need to vent. A small space left above foam is perfect. I would not vent the ridge to code, much less would be fine.
Sprayfoam's main advantage is that it stops airflow and air leaks and hence most normal amounts of moisture migration and hence the need for VENTING.
Aaron,
The house is 100% cathedral ceilings. Maybe I can get a few years at most on the two sections which aren't leaking.
Bernie,
Q. "Does this gap between the foam and the sheathing in an unvented assembly pose a problem?"
A. No.
Bernie, my reason for asking was to ask in a roundabout way if when you decide to re-roof the remaining sections, are you going to do this same treatment to more areas? Personally, I can't comment on open cell foam, all we have ever used is closed cell. I believe they use BASF components. It does smell, however, that smell is greatly reduced by having drywall on one side. Also, by having that airspace between the foam and sheathing, and ridgevent, it will act to vent the smell. The one time we have done something similar to this, the smell was not noticeable to me. However, the area was smallish (about 12x22) and I'm not sensitive to the smell. just my .02
An update:
Having met with spray foam installers, there are two options that have emerged as leading candidates:
Options:
(1) Icynene Open Cell foam sprayed from open roof with sheathing removed. It turns out the rafters in this section of the house are 12" depth (11.25"). One installer proposes to spray 9.5 or so inches of foam, keep the soffit vents open, and have the roofer install a ridge vent. With rafter notching under the skylight, there will be continuous ventilation over the open cell foam from soffit to ridge across the entire underside of the sheathing.
(2) Second installer proposes to fill cavity entirely (11.25 " rafter depth + 0.75" drywall strapping = 12") and close off all ventilation.
Does providing a ventilation channel over open cell foam pose an issue re moisture pickup from the outside air?
Which option is favorable? I do have leaky cathedral ceilings at ceiling to beam intersections which will be difficult to seal completely.