Cathedral Ceiling With Inadequate Exterior Foam Insulation

Dear GBA,
I have been driving myself crazy trying to understand and complete a cathedral ceiling assembly in an old, Southern Ontario farmhouse we recently purchased. I learned what I could from the GBA articles about such ceilings but am still unsure how to proceed. Are you able to please offer any help?
The problem is that we have a new roof with too-thin exterior insulation for our climate zone. We have 1.5″, R-7.5 GPS Silverboard over our 2×8 and 2×4 rafter cavities (different parts of the house), which following the 50:50 formula for fibrous insulation to exterior foam would allow only R-15 in our roof assembly.
The good news is, the SB is micro-perforated and air-permeable, according to the manufacturer. There is a board over the insulation over each rafter, creating a ~3/4″ air channel above the insulation and below the sheathing to the soffit. So, maybe we can fill the 2×8 cavities with 7″ of rockwool and 2-4″ of foil-faced foam under the rafter cavities (air barrier), since the cavities will be able to dry to the outside, to the extent the microperfortions are trustworthy in this respect(?) It would yield R-40 to R-50, depending on how much headroom we were willing to give up.
When I asked the Silverboard manufacturer about this, they kindly ran a model to advise me my dewpoint would fall inside the rafter cavity somewhere, which would have 80% RH. But they didn’t spec the vent cavity, and I haven’t heard back from them about whether this would matter. Is an interior dew point still a problem where cavities can breathe?
The bad news is, there are are a pair of hips on our roof creating a few cavities where there is no venting. Also, our 2×4 rafter section has boards over the rafters and under the 1,5″ silverboard, undermining their breathability. For both sections I gather my only good option is filling them with ccSPF, is that right? Perhaps with 2″ of the foil-faced insulation under the 2×4 filled cavities (for R-40 total and to help protect us from off-gassing). Would it matter in this case that the dew point was still interior – presumably not if the dew point fell inside the foam? Finally, the house does have A/C, so we have to manage the possibility of summer condensation, as well.
Thanks in advance for any help you may be able to offer.
GBA Detail Library
A collection of one thousand construction details organized by climate and house part
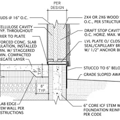
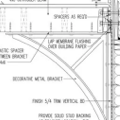
Replies
> exterior insulation ... R-7.5 GPS ... micro-perforated and air-permeable
> 3/4″ air channel
This is a hybrid assembly, combining a little ventilation and a little exterior foam. The only way I know of to determine if it might work is WUFI. Very well air sealed on the inside will help significantly. A smart-retarder is also beneficial (sometimes allows inward drying). The clearer solution is ccspf everywhere.
> is interior dew point still a problem where cavities can breathe?
With the right interior/exterior perm ratio or tight on the inside and leaky on the outside, it can be fine. Lots of walls and roofs prove this.
Venting bellow a rigid layer completely negates the benefit of the insulation. Might as well have built a vented roof with no rigid above it.
R 7.5 is not that much but it does help a bit, depending on your local HDD, that is good for R15 to R18.5 in the cavities.
In the case of the 2x4 rafters, R14 is all you can fit, so that is fine.
For the 2x8, you can go with 2x6 batts pushed up against the roof deck and help in place with insulation wires. A gap bellow the insulation on the warm side is fine. If you want more R value, spray the underside of the roof with 2" of closed cell spray foam followed by the 2x6 batts. This brings your assembly R value up from about R25 to around R35, might not be worth it as SPF is expensive.
If you can make sure your ceiling is air tight, you can push the exterior rigid to fluffy ratio a bit if you include a smart vapor retarder under your drywall. The smart vapor retarder would limit moisture movement into the rafter cavity but would also allow for drying outside of the heating season. This would let you install 2x8 batts and skip the SPF. Air tight is the key to make this assembly work, ie. no pot lights.
In either case, cut and cobble rigid to the underside of the roof deck is a bad idea. It is a lot of work and impossible to do air tight. With the inevitable small air leaks, moisture can make it into the space between the rigid and the roof deck and would have a very hard time drying through the foam+shingles.
Thanks Jon and Axos for your insights and comments. I am going to have to see if I can figure out "WUFI Light" to reveal the extent to which a smart retarder can save the day here. We do have a rule that there won't be any pot lights in these ceilings!
Akos, I'm confused about the negation of the rigid insulation. It is the thermal barrier for the house: there is venting above it, and warm air below it. Why wouldn't the rigid insulation do its job trapping warmth below, while reducing wind-washing? And wouldn't the venting above help keep the sheathing, which sits above the vent, cold (reducing ice dams)?
I should have added that we went in with a goal of hitting R-40 everywhere in our retrofit. With two layers (7") of Rockwool, I would hit only 7.5+28 = R35.5. Maybe 1.5" of comfortboard (fully breathable) below that, plus smart membrane. This is my preferred approach, but this does feel like I'm putting a lot of faith in the membrane functioning as advertised - is that a safe bet? Another option would be 3" of SPF plus a batt of Rockwool in the cavities, yielding 7.5 + 3*6.5 + 14 = R-41, albeit with more thermal bridging. At any rate, I will share back here what I learn from WUFI.
For the 2x4's, if I completely filled those cavities with ccSPF I would get 7.5 + 3.5*6.5 = R30.25, and by adding a 2" continuous foam layer directly below that, I would hit R40. I gather there would be no risk of moisture issues there because it is all foam of one kind or another with no air in the assembly, right? Any issues with layering rigid under SPF?
I missed the fact the vent space is above the rigid. In that case, it doesn't effect R value and does help with moisture. How much it helps with drying is hard to say without modeling.
Generally high R value roofs with a lot of SPF tend to have no ROI and large carbon footprint. Sometimes SPF is the only solution for a robust roof though.
In southern Ontario an R25+ assembly would get you most of your energy savings even for a roof, going much above that especially if it adds a lot of cost might not be worth it. Best is to limit closed cell SPF to the minimum needed for condensation control and fill the rest of the rafter space with batts or open cell SPF.
Thermal bridging from rafters also reduces the high R value of the spray, in most cases the center of cavity R value looks impressive but assembly R vale barely budges.
You can check out the calculator here and work out some of assembly options:
https://www.ekotrope.com/r-value-calculator
A bit less work than WUFI, there is also this that does condensation calculations:
https://www.ubakus.com/en/r-value-calculator/index.php?
Just a quick comment for anyone else following this, that I used both the ubakus and free version of WUFI to come to an understanding of my planned roof assembly. The difficult aspect was obtaining norms -- "what's acceptable"? There are often not clear answers to whether what you've found in your simulation will be sustainable long term. Also, the quality of the simulation relies on the quality of your many assumptions. But in the end, it allowed me to feel confident in our plans, as I obtained reasonable outcomes even if some of my assumptions were violated. I encourage others to give it a try.