Cathedral Ceiling Unvented with Fluffy Insulation

Hello,
I have a friend who has a challenging roof situation. Its zone 6 Maine and he is remodeling an old barn into a living space. He wants to avoid spray foam and messing with the exterior roof–old metal roof over 2 layers of old shingles. Its a 12/12 on a second story barn–its way up there and a cherry picker ($) would be necessary.
He’s going to build a roof within his roof for extra insulation and to add structural support. He can’t add interior venting spaces under the roof sheathing because of existing purlins. Cut and cobble would be a PIA and tough to get right on the log purlins.
His plan is to stuff the whole assembly with the lightest insulation possible (wood fiber or fiberglass?) to get his r-60. Then, he wants to rely on a European vapor barrier impeccably detailed, drywall detailed for vapor, a vapor retardant paint, and a oversized ERV to make the assembly work. He argues that if there is no way for vapor to get to the sheathing, the sheathing cant get wet. I think this dries to the inside, but not the outside due to the old layers of asphalt roofing under metal. The vapor barrier would continue down on the interior of the knee walls and double as the air barrier.
Thanks for a risk assessment on this assembly.
Stephen
GBA Detail Library
A collection of one thousand construction details organized by climate and house part
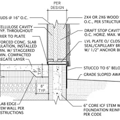
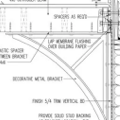
Replies
Stephen,
" He argues that if there is no way for vapor to get to the sheathing, the sheathing cant get wet."
If we could completely stop the movement of air and vapour though walls and roofs, GBA could probably close up shop and we could spend our time talking about sports or food instead. The ACH 50 we use as a metric for air-sealing equates to the pressure on a house's enclosure a fairly windy day. In those conditions a well air-sealed house has the entire air inside it move through the envelope every hour.
It's a bad idea to decide that known risky (and non code compliant) assemblies will be fine based solely on the difficulties of using proven safe ones. My advice would be to pick one from this list: https://www.greenbuildingadvisor.com/article/five-cathedral-ceilings-that-work
Thanks Malcolm, as always.
Interesting, you state, "The ACH 50 we use as a metric for air-sealing equates to the pressure on a house's enclosure a fairly windy day. In those conditions a well air-sealed house has the entire air inside it move through the envelope every hour."
I would benefit from learning more about what you state above. So, even very well air sealed houses, and those with redundant interior vapor control, have large amounts of air and vapor moving through the assemblies. I think my knowledge gap is in the area of understanding ACH and what it means, in relation to this. I appreciate the nudge in that direction and no doubt, my friend will appreciate this input.
Stephen,
We measure air tightness by pressuring the enclosure to 50 pascals - which is roughly equivalent to the pressure difference you get in a 20 mph wind. We consider a 1 ACH50 house - that is one where the entire volume of air is replaced once an hour - to be fairly tight. In calm conditions that 1 ACH50 equates to something like one complete air change every five hours. So yes, even in well air-sealed houses you can get a lot of air moving through the building enclosure.
Code compliant assemblies are all premised on that occurring, even with good air and vapour control layers. In general the two strategies that are used are:
- To give the assemblies good drying paths so that moisture is removed faster than it accumulates - usually though ventilation cavities.
- Keeping the vulnerable parts of the assembly (like the sheathing) warm enough that moisture doesn't not condense or accumulate in it by adsorbtion.
In a perfect world, we could forgo ventilation and not worry about the permeability of the exterior of the assemblies, but in the absence of those conditions relying on good air-sealing and vapour control aren't enough to guarantee a roof is safe - and this is especially true in colder northern climates.
Well explained and clear. Thanks again!
Stephen, if he does a good enough job with his installation, and he has a fair amount of luck, there is a chance his assembly would work. Moisture WILL get into the insulation cavities but the "ping-pong effect" (https://buildingscience.com/documents/building-science-insights-newsletters/bsi-016-ping-pong-water-and-chemical-engineer) might be effective in driving moisture toward the peak.
I would only consider this approach if there was nothing casting shade on the roof and if there was a way for moisture to escape at the top of the building, either ridge vents or gable end vents. And if I was not subject to building codes; everyone in Maine is legally required to follow MUBEC, even if small towns aren't required to provide enforcement.
If I followed that approach, I would not be surprised to find moisture damage or even dripping water within 10-20 years, and the undesired microbial growth that comes with it. It's not a risk I would take on, except perhaps for short runs of sloped ceiling in an old house.
Making a barn into a home is a very romantic idea but the realities of making a barn into a tight well insulated home are daunting.
When I walk into an old barn, I see light streaming thru the gaps between ever siding board the siding has no overlap the rain easily gets thru the gap and on the inside of the siding. The water getting inside is not a problem because the gaps are large and the water quickly evaporates and is carrier away by the wind blowing thru the barn.
If you fill the walls with insulation and add an air barrier without somehow stopping the water from getting into the walls mold and rot are likely to set in quickly.
Note 3 layers of roofing would be a code violation and generally a bad idea.
If you don’t have the time of budget to strip the place back to the frame and install a modern water barrier/rain screen covered with the original siding maybe just let this barn, be a daydream.
Walta