Cathedral ceiling rafter cavity and insulation

I am trying to figure out how best to use Rock Wool in my cathedral ceiling with the space that I have. I am using 2 x 12 rafters. I am not using spray foam. I was going to build my vent baffle from xps sheets for a 1″ air space sub roof sheathing…I was even willing to shrink that space down if needed. I live in zone 3 and would like at least R-35. So with my rafter space I start out with 11 1/2″ inches. No matter how I figure it with rock wool batting, I either end up with 2″ of dead air space that should be filled with something or 1/4″ too much for the space. My main question is, can you slightly compress (1/4″) the rock wool insulation to fit the cavity,or does it have too much density, and would you compromise the insulation value too much?
I know there are a million and one ways to fill that space, but I was looking for the best method with rock wool, with the least amount of steps.
GBA Detail Library
A collection of one thousand construction details organized by climate and house part
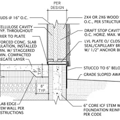
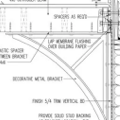
Replies
Scott,
Your air space needs to be at least 1 inch deep to meet code (although 1.5 inch or 2 inches is better).
Your baffle can be quite thin if you use cardboard, luaun plywood, or an AccuVent plastic baffle.
As long as you are using ordinary mineral wool batts, and not one of the denser board-like products, mineral wool is quite compressible.
For more information on these issues, see these articles:
How to Build an Insulated Cathedral Ceiling
Site-Built Ventilation Baffles for Roofs
A 2" vent space is fine- better than the 1" code minimum, especially on lower sloped roofs.
An R30 rock wool batt is 7.25" thick, adding 3" of polyiso would still leave you over an inch, and would bring the center cavity R to R48- better than the R38 code min for zone 3. If you used 3" foil faced EPS for the baffle you'd still be over R40. Low density Type-I foil faced EPS is pretty cheap stuff, and even at 2" you would come close to R38 when paired with an R30 batt.
Don't build the baffles with XPS, which is climate damaging due to the blowing agents used in it's manufacture, and would need to be at least an inch thick (R5) to meet code prescriptives for dew point control when placed on the exterior side of the fiber layer: http://publicecodes.cyberregs.com/icod/irc/2012/icod_irc_2012_8_sec006.htm
With 2-3" foil faced polyiso or foil faced EPS and foil-clad roof decking you would get a decent performance benefit out of the foil facers, and have a bit of margin on the Chapter 8 prescriptive.
Not that you'll need to, but compressing batts is fine- the rock wool would gain a bit in R/inch terms, but lose slightly on total R for that layer.