Cathedral ceiling – polyiso and cellulose combined

Hi, all.
I have a question about insulating a cathedral ceiling. After getting feedback from Martin on the comments chain of his cathedral ceiling article, I’ve changed my plans to the following, from top to bottom:
– standing seam metal roof
– roof underlayment
– 1×12 rough sawn pine boards (as roof sheathing)
– 2×12 rafters and ridgeboard
– ventilation vents with 1.5 inch space made from OSB board and caulked at all seams
– 4 inches of polyiso foam
– 5 inches of dense-packed blown cellulose
– NO vapor barrier
– drywall (as ceiling and air barrier)
I live in Southwest Wisconsin, Zone 6. My main question: Could the combination of polyiso on top and dense-packed cellulose on bottom create any moisture or air movement issues? I don’t see any, but as an owner-builder, I find myself constantly working against blindspots, and just wanted to check in with the forum here before pursuing this plan.
I’m not doing all foam because I’m not a fan of the material. But I want to use some to get my R value close to 49.
Thanks for any suggestions.
Peace,
Joe O.
GBA Detail Library
A collection of one thousand construction details organized by climate and house part
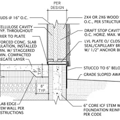
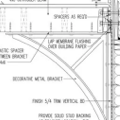
Replies
>"I’m not doing all foam because I’m not a fan of the material. But I want to use some to get my R value close to 49."
Putting high R/inch foam between framing is a waste, since the thermally bridging R1.2/inch wood robs it of a large fraction of potential performance. With just 6" of continuous polyiso (not thermally broken) would get you to code-min performance (on a U-factor basis) with no cellulose.
A code-max U-factor would be U0.026 , which is R38.5 "whole assembly", fully accounting for the R-values of all the materials and air films in the stackup.
Dropping back to 2x8 rafters and installing 5.5" of cellulose (leaving 1.25" gap above a 1/2 " fiberboard or MDF vent chute, OSB only if you must) and just 3" of continuous foil faced polyiso (R18) on the interior side, strapped to the rafters with 1x4 furring on which to hang the gypsum board hits code-min performance on a U-factor basis. Asphalted one-side fiberboard supported at the mid point between rafters with a spacer to the roof deck as well as at the edges next to the rafters would be stiff enough to handle dense-packing, even with 24" o.c. rafters.
The foil facer on the polyiso next to the air gap to the gypsum adds about R1 to the whole-assembly stackup.
Half-inch MDF or fiberboard is another R1 ( compared to only ~R0.5 for half-inch OSB), and it offers more drying capacity.
The air films in the vent channel add another ~R1.
Full dimension 1" rough-sawn pine is good for at least R1.4.
The sloped exterior & interior air films above the roofing/below the ceiling add up to about R0.8.
Half inch gypsum is good for ~R0.5.
So the continuous layers add up to:
R18 polyiso
+R1 facer + air gap
+R1 vent gap
+R0.5 gypsum
+R1.4 pine decking
+R0.8 interior & exterior air films
= R22.7
At a 7% framing fraction (typical for 24" o.c. rafters) the 5.5" cellulose thermally bridged by framing comes in at about R19, even at a 12% framing fraction (16" o.c. rafters + other framing) it runs R18.5.
R18.5 + R22.7= R41.2 "whole assembly", or (1/R=) U 0.024, meeting/beating the U0.026 max, using less foam and fewer board feet of lumber.
If you are using fully dimensional, rough-sawn 1x12s then I would add the polyiso above it. You don't have to worry about your screws hitting a rafter with such thick sheathing.
>"If you are using fully dimensional, rough-sawn 1x12s then I would add the polyiso above it. You don't have to worry about your screws hitting a rafter with such thick sheathing."
Then you'd have to go with 4" of polyiso (for dew point control on the R20-ish cellulose) rather than 3" if done on the interior, letting the cellulose dry into the vent channel. The thermal performance of the polyiso would (in most cases) take a hit if on the exterior side of the assembly compared to putting it on the interior side. With a vented assembly is fine to put the polyiso on the interior side.
With an interior side approach the furring strapping it in place should be perpendicular to the rafters, and no more than 16" o.c. if the cavity is being dense packed.
Wouldn't this defeat the purpose of the vent channel? Shouldn't the vent channel be as close to the underside of the roof as possible, to keep the underside as cool as possible, and shouldn't all insulation be between the vent channel and the conditioned space?
Wow, thanks for the thorough replies, Dana. I should have clarified, though, that most of my roof assembly is already built. I've got everything done from the standing seam metal down to the OSB vents. So with this less than optimal set-up, I'm just trying to finalize the best plan for filling those cavities. I'd rather not extend the rafters, as a high window in the gable peak and other complexities make it difficult.
Joe,
Going with your proposed stackup, assuming 16 OC rafters, you end with an overall R33 roof. If you just use cellulose you end up with an R30 roof.
My guess is the payback period in energy cost saved with the cut and cobble insulation is many many decades.
An R30 roof is pretty decent in your climate, the incremental increase in R value from there saves very little energy overall. Even going up to an R40 assembly would barely change your losses.
For example, assuming 1500sqft of roof and 5F outdoor 65F balance point. With an R30 assembly you loose 3500btu through the roof. With an R40 that goes down to 2600 btu. There are many places in your envelope that you reduce your heat load by 1000btu for much lower cost.