Cathedral ceiling insulation for a summer cabin

Need help with weekend summer cabin roof insulation, and best way to avoid moisture problems – zone 4, non vented roof.
Metal roof over plywood over 2×4 rafters, then plan to install exterior siding on interior for finished walls.
I currently have extra 2″ rigid insulation sheets that are R10.
Option 1: Cut and cobble rigid insulation against bottom side of roof sheathing, rigid held in place with spray foam. (1A add radiant barrier paint to interior wall panels which will be exterior siding)
Option 2 : Install rigid foam flush with interior rafters leaving 1.5″ airspace between roof sheathing and insulation. Roof is not vented, there are no soffit or ridge vents. (2A would be paint radiant barrier on interior side of roof sheeting)
Option 3: Install batt fiberglass insulation 3.5″ thick with VB on interior side.
Option 4: Install spray foam – lost of $.
Option 5: ?
Summer cabin primary use with AC.
GBA Detail Library
A collection of one thousand construction details organized by climate and house part
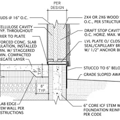
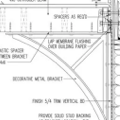
Replies
Eric,
Of course it's always better to plan your insulation details before the roofing is on -- because now your options are limited.
If you can't vent the roof, and you can't install continuous rigid insulation above the roof sheathing, your only choice is closed-cell spray foam on the underside of the roof sheathing.
If you can retrofit soffit vents and a ridge vent, you'll have more options.
The cut-and-cobble approach is unsafe for unvented roof assemblies -- it is associated with failures and rot.
More information in these two articles:
"How to Build an Insulated Cathedral Ceiling"
"Cut-and-Cobble Insulation"
With your limited use, I expect that you would get away with option 1. Three continuous air barriers (the sheathing, the sealed edge foam and something under the rafters) would help (air movement is by far the primary mover of moisture).
In the unlikely event the air sealing isn't enough, you can control air movement with building pressure (not very expensive for a well sealed building with limited use).
Eric and Jon,
There are two problems with Jon's suggestion.
The first problem is that in most parts of the country, you have to follow the building code -- and according to the usual interpretation of most building inspectors, cut-and-cobble insulation isn't allowed for unvented roof assemblies.
Of course, Eric may be building in an area that isn't subject to building codes.
The second problem is than any insulation strategy that depends on "limited use" of the building to avoid moisture problems is risky. Buildings last a long time, and a building that is used occasionally in 2019 might become a full-time home in 2030. That's why our insulation strategies need to be robust.
similar situation, struggling to find correct solution(s).
off grid 400 sq ft cabin, low slope shed roof 12’ high front, slope to 10’ high at back, 16’ span.
2x10 rafters. plywood sheathing, ice and water, Ondura asphalt corrugated panel covering. ( no external side ridgid foam)
with no code requirements and realizing limits to rvalue, goal is air quality (bush/ lake smells/ lots of bugs and critters)) and cabin comfy winter use.
no air conditioning in summer ( or very limited if bring up portable unit with window vent in july heat/ humidity)
4 season use in zone 6, central ontario , with weekend only use including winter heated by wood stove and other supplemental heat source (blue flame propane).
Budget conscious so wont be full spray foam.
Considering 2 options from reading your articles.
1) unvented: cut and cobble. have available inexpensive 3 1/2 inch unfaced eps. place between 2x10s 7” deep and seal with 1” spray foam.
2) cut and coble similar or same as above but create 1-2” air space between sheathing and eps and cut holes/vents in wall/rafter blocking between each joist on both front and back for air flow?
3) other?..
any help appreciated. struggling with all the various articles
many thanks