Cathedral Ceiling Insulation Confusion and Idea

I am trying to understand the best methods for insulating cathedral ceilings and have read many articles but am still confused about a few things.
1) For a vented approach, if you use only cellulose in the rafter bays and put a ventilation baffle against the sheathing, won’ t the condensation then just occur on the cold baffle and still get the cellulose wet?
2) I will be using scissor trusses for a livable attic and will have a huge amount of space within the trusses to fill with cellulose. If I use an unvented flash-and-batt method with 4 inches of closed cell foam on the sheathing, can I just fill the remainder of the cavity (maybe 20 inches) with cellulose? I am in climate zone 6 which dictates R25 of foam but with so much cellulose (R75+) I worry the foam will still be cold enough to collect condensation. Is it okay if I only fill half of the truss cavity with cellulose beneath the foam and have an air gap between the cellulose and drywall?
3) I see that a lot of failures are due to not being able to dry out, usually because of foam. Can I just make everything super vapor open and then try to be meticulous with my drywall air sealing knowing that if tiny amounts of vapor diffuse through the drywall or tiny amounts of air leaking through fixtures and causing condensation could easily dry out? Example layers from inside: Drywall, truss cavity full of cellulose, zip sheathing, 4 inches of Rockwool Comfortboard 80, airgap with 1.5″ battens, zip sheathing, metal roofing shingles. I attached a photo of this idea.
Thanks!
GBA Detail Library
A collection of one thousand construction details organized by climate and house part
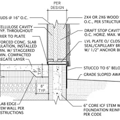
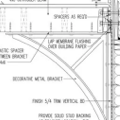
Replies
In order:
#1: If the baffle is highly vapor permeable (say MDF board or 1/4" foam board) it's not a problem, and if the thickness of the baffle is small, the drying path through the rafter (or truss chord) is short enough to highly vapor permeable, thus providing a drying path. If the baffle is something like say, 2" thick foil faced foam board, yes, there is a potential problem.
#2: In zone 6 with an unvented insulated roof deck at least HALF of the total R has to be closed cell foam to avoid moisture accumulation at the foam/fiber boundary. Using the 4" foam example that's R24 (if HFC blown) to R28 (HFO blown). Assuming R3.7/inch for the cellulose you're then limited to no more than R24/R3.7= 6.5" of cellulose for the HFC blown case, or R28/R3.7= 7.5" of cellulose for the HFO blown case. Clearly with a scissors truss a vented approach will be cheaper & easier.
#3: If it's all vapor open and unvented the moisture will all end up in the cold roof deck and any truss elements that extend above the insulation layer, which is NOT good. If the roof deck is fully vented soffit to ridge, latex paint on air tight drywall would be a sufficient vapor retarder in zone 6, but in zone 7 a polyethylene vapor barrier would be safer, even with the venting. The bigger the vent path, the less of an issue that is. With scissors trusses the vent space could start at 1-2" at the soffits and end up increasing to 1-2 FEET at the ridge, which would be fine.
There is no point to using rigid rock wool for the cellulose baffle. If the truss chord is a 2x4 use it to create a 3.5" vent gap with MDF, plywood, OSB, just about anything as the baffle, but don't run it full length, just high enough that you can hit your target depth above the ceiling layer easily, and design in enough of an energy heel at the soffit end to hit your target R value with just blown cellulose. Using a "stablized formula" damp spray with water activated adhesive the cellulose won't slide down the sloped ceiling, and won't be blown around and redistributed by wind currents coming in from the venting.
The drawing shows an open web truss, and NOT a scissor truss. Scissor trusses look like this, with the slope of the ceiling somewhat lower than the slope of the roof deck:
https://s3.amazonaws.com/greenbuildingadvisor.s3.tauntoncloud.com/app/uploads/2018/07/10114758/Scissors-truss-4-700x382.jpg
With open web fully parallel trusses the top chord is usually 1.5" thick 2x lumber, which is fine to use as a depth stop for your baffles. If the trusses are 24" o.c. (probably are) use strips of 1.5" thick foam board glued/tacked to the underside of the roof deck mid-way between the trusses as support to keep a thinner baffle from buckling under dense packing pressures.
In an open web truss the baffle itself could be almost anything- half inch exterior grade gypsum board is strong enough and highly vapor permeable. Half inch asphalted fiberboard is also good, with the asphalt side facing the vent channel if only asphalted on one side. Half inch foam board is NOT strong enough to dense-pack against though.)
As long as it's supported every foot or so half inch gypsum, fiberboard or MDF will handle dense-packing to 3.5lbs per cubic foot. In a sloped roof it doesn't have to be that dense- 3lbs is more than enough to prevent settling in a sloped roof, whereas 3.5lbs is pretty standard for 2x6 vertical walls with a lot more cellulose weight bearing down on the bottom of the stud bay.
Thank you for your detailed response!
1) So it seems like condensation will DEFINITELY occur but it doesn't matter because it can dry easily. I was thinking it would be great to design in a way that condensation NEVER occurs, but that only seems possible with interior spray foam and lots of exterior insulation.
2) It makes sense that the spray foam should be at least 50% of the R value. If I have flash and batt in the rafter bays, then add mineral wool on exterior, is the mineral wool part of the foam R value? For example: 4 inches exterior mineral wool (R16) + 4 inches spray foam under sheathing (R26) = R42. Does that allow 11 inches of cellulose (R41) under the spray foam?
3) I am sorry about naming the truss incorrectly and I think my drawing wasn't clear. I tried drawing up an unvented roof. The mineral wool is actually external continuous insulation which will continue down the walls and gables. The entire truss cavity is totally full of cellulose with no air gaps. I was trying to take advantage of all the space inside the trusses. I am understanding though that moisture will definitely gather in the cellulose if unvented and with continuous air barrier sheathing around it there is not enough drying potential for it to work.
Thanks for your help!
Per #2, the important part of the assembly that one is concerned about is the vapor control layer. This is the least permeable portion of the assembly. In this case it would be the interior side of the ccsf. One wants to make sure that this stays warm enough that it will prevent condensation (technically, keep condensation low enough and rare enough that the assembly will have more opportunities to dry than to get wet- this is what the code is trying to define in each climate zone). Any type and amount of insulation above this layer will only help keep the vapor control layer warmer, but if you are going with a vapor open insulation such as rockwool, you would want a vent chamber above this as you wouldn't want to have an issue with the sheathing above it. I've attached a pic of a project we did years ago that had this detail except that instead of ccsf below the sheathing we had cellulose (I am in CZ 4c).
One issue you could run up against is the local planning department. We had an issue with a planner in the city of Portland, OR who took quite a bit of convincing with WUFI models and made us create hand calculated thermal gradients and use a psychrometric chart to define the dewpoint. Long story, but we endured and got it passed. This is just to say you could find some pushback with a non traditional assembly.
Thanks for the explanation and example. It makes sense how keeping the first condensation plane warm will avoid problems. It looks like the example you provided with the photo is almost exactly what I drew up in my drawing: cellulose beneath sheathing and rockwool above sheathing with air gap above rockwool. In your example it also looks more risky because of the rather thin layer of rockwool and thermal bridging of the overframing. Why in your case can you prove it works but everyone else (including Dana above in post #1) says that construction will cause moisture buildup and failure? I would really like to avoid using any foam at all but it seems extremely difficult without a physics degree and getting dangerously close to the brink of failure.
We are in CZ 4C and currently we would need R-20 above the sheathing if the planning department interprets this as a 'hot roof' assembly. In this particular photo the planning department interpreted this as a vented assembly so it was a moot point. This was also built in 2013 (under the 2009 IRC code, I believe). The reason I mentioned the planning department is that on a current project this same assembly was interpreted as a 'hot roof' and we needed R-20 above the sheathing, so we upped the overframing to 2x8 rafters with 5.5" of rockwool bats (we didn't use the comfoboard in either case as it isn't necessary).
We offset the overframing from the rafters below by having the structural engineer spec it as such which resulted in 2x4 blocking on the flat under the sheathing every 4'. I've attached a detail showing how it was done. We didn't want to have the thermal bridging issue, and we didn't want to have the overframing perpendicular to the slope of the roof so that any incidental water that got in the overframing assembly could drain down and out.
In addition to this, on our recent project we incorporated a variable permeance membrane (Siga Majrex) at the bottom of the rafters to help control vapor into and out of the assembly and act as a redundant air barrier (the zip system was the primary AB and VCL on this project). Avoiding air leakage and the associated vapor that it contains is the highest priority. The diffusion is orders of magnatude less of a worry.
We ran a WUFI model on this assembly that showed drying over the seasons and didn't show any moisture build up on the vapor control layer (zip sheathing). In addition to this we ran some long hand math (per an especially difficult planner who "Didn't trust computers" (!) using the calculation that Joe Lstiburek outlined in Martin Holladay's great article 'Are Dew Point Calculations Really Necessary?' Where on can (per the article): 'Take the average temperature for December, the average temperature for January, and the average temperature for February — and you average those, and use that average as your design temperature for outside. You set your interior design condition as 70°F and 35% relative humidity. Then you do a simple calculation to make sure that the condensing surface doesn’t drop below the dew point."
When we did the above calculation it showed that we were significantly outside of the dewpoint on this particular assembly. See the attached screenshot.
What one learns through all of this work is that a simple dewpoint calculation set with the local design degree day and high interior RH doesn't capture the whole story and shows that these assemblies can be quite resilient in real life. Again, I stress the importance of an air tight building assembly, ideally coupled with balanced heat recovery ventilation and a smart vapor retarder at the bottom of the rafters.
I would also acknowledge that in your CZ of 6 that the amount of insulation required above the roof deck may not make physical or financial sense. I would suggest running the simplified dew point calc above and see if it works with your local inputs. I can also point you to another foam free vaulted roof assembly we have done which I have written about in Fine Homebuilding issue #299 'A New Take on Insulating A Roof' This could also be an option for you to explore.
If you fix the R ratio, your 3) stack is an excellent roof with adequately warmed sheathing and venting. It's allowed by IRC 806.5.1.2 and 5.1.4. IMO, in Z6 with low perm Zip, it should have a smart retarder like Intello or MemBrain on the interior. This reduces the amount of moisture accumulation when the lower sheathing is below condensing temp while still allowing good inward drying. Do not use a Class III or I.
As you said, air seal the interior side - with both sides being even better. Always test to verify.
Use less above the sheathing R value and it's not IRC approved and needs analysis. Plywood (vs low perm Zip) helps - because moisture is more likely to flow-though and so less likely to accumulate.
Non continuous exterior insulation is probably not IRC approved - see 2018 Table R806.5 b) where it says "continuous".
With a lumber overroof type of setup, you want the 2x lumber to run at 90 degrees to the rafters bellow to reduce thermal briding. Since you have trusses, less of an issue unless the top chord is above a 2x6.
The way to make the overoof more robust in heating dominated climate is to put a vapor barrier across the first deck. This can be one of the inexpensive non-granular ice and water protectors. Besides sealing up the roof deck, this lets you skip the ZIP there and gets the place rain tight even before the overoof goes on. You can than skip the interior vapor retader as painted drywall is sufficient.
Provided you get the insulation ratio correct (50% exterior, 50% interior), there is no issues with condensaion on the roof deck, the insulation on the interior can dry to the inside, the insulaion on the exterior can dry to the roof.
Our code allows for this type of assembly (vapor barrier on the outside but behind sufficient insulation for condensation control) which will make it easier to approve.
You also don't need comfort board for the over roof. This can be regular mineral wool batts which are way cheaper. If you have the purlins horizontal, you can even skip the upper roof deck if you go with a metal roof. A number of metal roofs can be installed directly over purlins.
I've done roofs with pee&stick on the sheathing midway in the insulation stack and it works well.
You can do plywood with peel&stick VB for the sheathing, but taped ZIP will work too. It has low enough permeability that it will work just like the peel&stick to throttle moisture, but it will retain a little bit of permeability just in case. I'd go with whichever one your builder is more comfortable with, and which is more cost effective. One of my roofs survived a partial loss of the roof covering during Sandy. Thanks to the inner layer of Peel&Stick, there was no water entry into the house. Yay!
If you have interior side air sealing and an interior side vapor retarder and an assembly that will allow moisture to flow-though, adding a vapor barrier in the middle of it will make it worse. Yes, it can still work - but why rely on just sheathing warming when you can have sheathing warming and flow-through? Like 3) above does.
Hard lesson learned on vapor barriers.
When your code calls for a vapor barrier, you might need to show the inspector a data sheet showing the material of choice being less than 1PERM.
5/8 Zip should technically qualify but since Huber doesn't publish the permeability of the panel, the inspector might not accept it.