Cathedral ceiling condensation ‘chicken or egg’ question

I’ve read a number of old threads here to do with cathedral-ceiling insulation and condensation issues. My primary takeaway, for my setting, was that my unventilated cathedral ceilings needed to be completely and anal-retentively sealed against vapor intrusion from below, before I’m done. My question boils down to this: how can ‘sealing the ceiling’ ever really be achieved without trapping whatever moisture happens to exist at that point within the roof/ceiling assembly? And if that’s not too purist of a concern, is there some means to allow trapped moisture to escape, to prevent a ‘water cycle’ to proceed within the assembly?
Background:
I’m in Honolulu. Lots of seasonal rain, very seldom below 60F, and dew forms on the roof during cooler months well into the AM; it persists until the sun’s been on it for an hour or two. (This makes it easy to believe that there would be a hidden-condensation problem, especially if I were not very detail-oriented in sealing up the under-surfaces.)
On a part-time basis, taking forever as a solo project, I’ve been re-framing/sheathing/insulating all my roof faces. After demo of a section of roof, it’s open to the sky – that is, everything goes. There have been times during this process when rain has leaked through temp roof covering (blue tarp), and then of course through roof-ply-sheathing joints and thence the iso-board end-joints, finally getting into the OSB ceiling to the point where at times there was a rapid drip from the low-point at the eave-line, where the OSB ceiling material terminates and the stud-wall framing begins. It swelled a bit in some places as a result, but never to the point where it seemed structurally compromised, and my finish wouldn’t be impacted by that, so I let it be.
Insulation is all closed-cell (Sika) though one layer has a paper/glass face… that I was dismayed to realize could be soaked with water. During those days, I hadn’t yet made any attempt to seal the ceiling, and assumed (wrongly) that months of being left to dry out from below would be enough.
But even without rain-related leakage like this, there’s going to be a certain level of ongoing daily-cyclic humid-air condensation within the assembly, as recounted in a lot of cathedral-ceiling condensation threads, at least until the last surfaces are sealed and joints covered.
This all came to a head just a few days ago when I found that the complete fluid-applied membrane I’d created on the underside of the south-facing roof was prone to peeling off the OSB as a thick layer while I was installing (repositioning) some self-adhesive ceiling tiles. Ceiling is aluminum-faced OSB, which I’d taped with weatherproofing flashing tape and then coated with primer and elastomeric, and this membrane peels off without much effort, including the foil, leaving a slightly-damp-feeling raw OSB substrate, over much of the south face, where I encountered and then explored the problem. This south face was markedly more exposed to rain-leaks during construction vs the west face – which showed none of this tendency to detach at the membrane-OSB interface.
I tend to think that the OSB on the south face retained enough moisture to cause this problem, and perhaps some was still trapped when I applied the membrane components, but I’m not sure whether any amount of waiting for it to dry out could have helped (it was a matter of months as things were.)
Thus my question about allowing the trapped water or vapor to escape somehow. Is there some mechanical means I can retrofit?
It’s also not clear to me WHERE it would escape, if it could at all. My observation is that the trapped moisture may simply not be able to migrate upwards because there’s no airspace for it to do so. Since the temps are low on the interior, it never vaporizes, and instead it leaches down towards the low end of the OSB ceiling (another reason I didn’t use gyp, since I knew I couldn’t expect to keep things dry all the time during construction).
The picture that emerges in my mind is that an assembly like this is inherently fragile. Once breached with some kind of leak (whether it be rain from above, or the more subtle problem of humid air from below) it might never be restored to adequate interior dryness to ensure that mold won’t take over at the interfaces within the assembly. Is that overly pessimistic?
Ideas, treatments?
BTW are SIPS immune to most of this due to the air-tight bonding between the foam and the panel interior faces? They’re not in my budget, but I’d like to know…
GBA Detail Library
A collection of one thousand construction details organized by climate and house part
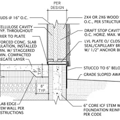
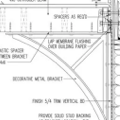
Replies
Moisture typically leaves through diffusion and/or air movement. Smart retarders are a practical way to let things dry while reducing wetting. Air movement can be controlled with pressure, but where it occurs isn't very predictable.
Thanks Jon - I've just now read a little about smart retarders, but not clear on whether they'd have had (or still could have) a place in my roof-reframing/ceiling-replacement project. LMK if so...
David,
There's a lot going on in your post in narrative form, and it makes it difficult to assess what exactly your roof stack-up is.
Your fundamental concern about trapping moisture is a good concern to have. I don't believe it has ever been recommended to create assemblies with vapor impermeable materials on both sides, as you seem to imply.
What HAS been recommended is to AIR SEAL the ceiling plane to keep humid air out of the roof assembly, thereby reducing condensation concerns. Air movement and vapor diffusion are two separate things and need to be treated separately.
The specific vapor profile and moisture tolerance of the materials in the stack-up matters here. You mentioned foam, but it's unclear (to me) where exactly it is in the assembly.
Most any roof assembly won't handle massive bulk water well. Perhaps it is more critical with an unvented assembly, but either way, fixing large leaks would be step 1. You likely won't build an insulated roof that is 'designed' to handle significant leakage.
If you're concern is specific to the in-construction phase, there may be added steps you need to take to dry out the extra wetting (like fans, dehumidifiers, pulling out soaked insulation, opening up the interior to increase airflow, etc).
Thanks, Tyler, for your considered response. (If you think my description was verbose, you should have seen what I edited out...)
To clarify, the 'stack-up' is as follows:
- aluminum standing-seam (that's the next step)
- (roofing metal direct to) waterproofing underlayment (self-adhesive 36" roll - Owens-Corning, https://www.homedepot.com/p/Owens-Corning-200-sq-ft-WeatherLock-Specialty-Tile-and-Metal-Self-Sealing-Waterproofing-Underlayment-WLSP/205664212)
- 5/8" CDX
- 1.7" closed-cell iso-board (glass faced)
- 1.5" closed-cell iso-board (paper/glass faced)
- OSB ceiling (Techshield, ~1/2")
- primer/flashing-tape/elastomerics as appropriate to completely coat and seal all under-surfaces
(There is no air-gap in the above layering.)
Let's assume I've finished my reframing/sheathing and any in-construction leaks have been handled (as I'm writing this we're having the heaviest rain we've had in months, so it's a bit of a stretch for me) but yes, handling active water-leaks is clearly prerequisite. It's a less clear at that point what an acceptable level of dryness is within all layers, and how it can be assessed/corrected. (You'd probably be right to point out that my assembly isn't compatible with any leaks during construction, I suppose, and this is a bit of painful hindsight for me, but still leaves me wondering how the same concerns would be handled within a SIP envelope, since surely they get wet during construction and are subject to some degree of humid-air intrusion before any undersurface-sealing could be completed.)
Anyway, assuming water-leaks have been plugged, I'm unclear as to how there can be any meaningful vapor OR air-movement provision - could you please explain a bit more? Seems you're drawing a distinction there, but I'm not clear on what exactly it is in the case of this assembly. The iso-board is virtually impermeable, right? I guess there's permeability to both CDX and OSB before they're put together in the above layering, but the roof underlayment is designed to be impermeable, no? And per most of these cathedral-ceiling-condensation threads, it seems like the inevitable conclusion is always to air-seal the under-surfaces to the nth degree. That would include the edges at the un-insulated eaves, too, yes? So unless there's to be some opening around the ridge -- and a path/means of transport for the low-lying moisture I'm seeing near the bottom of the ceiling plane -- I can't think how I can hope for even a long-term dissipation of trapped moisture.
I can't say I'm all that familiar with the sounds of your ceiling situation (metal clad osb, elastomeric / primer and all that). If the ceiling is relatively vapor impermeable, it seems your stack-up would indeed have poor drying potential.
Many common building materials will stop air flow. Drywall, plywood, osb (mostly), and a variety of sheet membrane products, for example. Yet all these materials also retard moisture diffusion to varying degrees. You typically don't want to create a stack-up with very low vapor diffusion potential on both sides.
Creating a stack-up with very low AIR exchange, however, is another story, and not fraught with the same pitfalls.
This may be a good primer on diffusion if that's the needed point of clarification: https://www.greenbuildingadvisor.com/article/vapor-retarders-and-vapor-barriers
I'm not all that familiar with your climate zone and its relevant building techniques, so I'm hesitant to give much advice on the specifics of your stack-up. I will ask for clarity, however:
Is your iso-board cut and fitted in between rafters? A 'cut n cobble' if you will.
Have you had a look at this article? (see mention of cut n cobble):
https://www.greenbuildingadvisor.com/article/how-to-build-an-insulated-cathedral-ceiling
*edit: I googled techshield and see it appears to be a radiant barrier. As a side note, if you don't have an air-gap by that barrier, it won't function as a radiant barrier.
Thanks again, Tyler. Somehow I didn't previously review that cut-n-cobble thread, but it's as close to being specific to my concern as I could expect, so I posted a similar question there after reading Martin's article (c. 2013) which has approaching 200 followup questions from people like myself.
I still need to delve into the link you offered regarding (I anticipate) selection of moisture-diffusing materials. I think my situation could be modeled simply as a 'tub' that's impervious below (I'm taking my air-barrier as continuous, and enveloping the ceiling material along with everything above), breached once it ties back to the CDX sheathing, and perhaps needing to breathe through a replacement roofing-underlayment material. (Waiting on Owens to get back to me regarding the permeability of the material I've been using, which doesn't have a published figure for some reason, but I think it's going to be near-zero by design.)
BTW the Techshield was my choice simply because it had a nice surface that would, I thought, simplify a ceiling finish, not for radiant-barrier properties. In hindsight, it's become a nightmare, because that foil layer is apparently trapping moisture in the strands above, and losing that battle, so that's where my air-barrier membrane is failing. My thermal-insulation needs were more than met by the is0-board thickness: there's absolutely no sense of heating from the sun, and this was my main goal in this long, fussy project, but of course now I'm dealing with the unexpected side-effects...
Dave
< .08 perms for WeatherLock Specialty Tile & Metal. I expect TechShield is even lower and so yes, you have a moisture trap.
Some upward moisture movement would occur if you had permeable underlayment - because metal roofing isn't airtight. More than most would think - but how much isn't clear.
> iso-board is virtually impermeable, right?
I'd expect some drying through it. How much depends on the perms.
Overall, agreed. If you are are going to assemble things wet, you need a mechanism for it to dry. I'd be concerned with wet SIPs.
Thanks, Jon. I'm probably about to do a bunch of product research on permeable underlayments. I'd agree (as would all manufacturers, I believe) that metal roofing just isn't considered airtight, or even watertight - hence the requirement that a waterproof underlayment be installed to handle the small percentage of leaks that will make their way below the metal.
Basically, it seems to me if nothing else, old-school asphalt-paper would provide the breathability I think I need (through the CDX and out the many air-holes found in standing-seam) though I'd rather use a newer, better-engineered underlayment. I started out with GAF Feltbuster (cheap, light, easy to install) but it has nowhere near the allowable exposure time that I need with my glacial speed, so I replaced it all with the Owens product (even that one is nearing the end of it's permissible exposure period).
--Dave
Jon,
From the name Techshield, you might think it was intended to be impermeable, but it's actually intended to breathe (not sure how much stock I take in that). The foil has tiny incisions in it, something I was actually dismayed to find, once I embarked on trying to create an air-barrier along the lowest surfaces, most of which are this Techshield foil face. I'm pretty sure I plugged all of those and other defects with multiple coats of primer and elastomeric, so if that was a mission worth undertaking, it's accomplished. Topside is another question (now my best guess is that I need to introduce permeability there). I have a call in to Owens about the Weatherlock permeability - but somehow you had that figure already, so thanks.
> it's actually intended to breathe (not sure how much stock I take in that)
Yes, let's see their measured perm value.