Capillary break between bottom plate and basement slab

Hey Guys,
I guess I should preface this with an apology for possibly being stupid, as ive now been booted from another forum for asking this…but im having trouble understanding the “why” this wouldn’t be acceptable.
Im wondering if I can safely use non-treated lumber as a bottom plate on interior basement walls if I put something in-between the plate and floor. So far the answer ive received are basically “no, because that’s how you do it” and “the bottom plate has nowhere to dry to and therefore you need PT to prevent it from rotting”. My understanding has always been that PT is used when in contact with concrete due to: a) the alkalinity rotting wood and b) concrete aborbs moisture which the wood will wick which will result in rot when it repeats itself over and over.
My basement is in extremely well draining rocky soil and I also added (from outside in) dimple mat, peel and stick barrier wrapped down over footer, caulked all cold joints and footer/wall joint. I also have a french drain on the side of the footer. On the interior I have 2″ of rigid foam that will be beteween the framed wall and concrete wall. Sub slab I have 2″ foam and a vapor barrier and I will have in floor hydronic heat.
There is an article on this site “Pressure treated sill plates and the building code” that seems to indicate that a capillary break negates the need for PT and treats the cause rather than symptom of high moisture in sill plates.
Are sill plates and basement bottom plates totally different in a way that im not getting? Won’t my bottom plates be drying inward?
GBA Detail Library
A collection of one thousand construction details organized by climate and house part
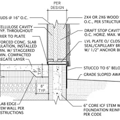
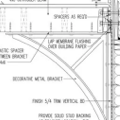
Replies
Jacob,
I don't know what your code says, but under ours we can do as you suggest and use a sill-seal without pt lumber as bottom plates. It's the accepted practice here. I seldom see pt plates.
I put aluminum between the bottom plate and concrete floors. We even retrofit aluminum under existing PT plates, when the basement is damp
( this dries the PT plates and the studs that are attached).
For whatever reason, when my house was built in 1967, they didn't use PT on any of the sills, but put aluminum underneath the sills. To date zero rot or damp sills.
What form does the aluminum come in? Flat roll?
Aluminum should never be in contact with concrete. Both materials corrode.
I think the real reason people question your question is because of the marginal expense of PT lumber as a percentage cost on the whole project. Such a small amount of lumber accounts for the PT sill plate that it adds ~$100 of marginal cost to a project, and no labor. For the protection that it does provide, I'd have to hear a very good reason not to use it. Use a sill gasket in either case, for even further isolation.
Your floor assembly isn't the norm in most of the US yet. I suspect that's another reason for the advice hesitancy. The first impression many people would have of the word 'basement' is a cool, somewhat damp space used for storage, with bare floors and walls. Your basement would probably be fine without a PT sill plate, but again for the small marginal cost, I'd still use it anyways. $100 is cheap compared to explaining your floor assembly to others every time a question is asked about it.
I can get behind this argument, though in my case I have salvaged a ton of lumber so the price difference would be more like $350 with current lumber prices since I would use lumber I have gotten for free. It's true that its not a huge percentage of the project, but I am also not building new (moved a house onto new foundation) and using a lot of reclaimed and salvaged materials i've been saving over many years. For me it represents a larger percentage of total cost, though i'm still not trying to risk rot over $350 bucks so point taken.
Like Malcolm wrote it's the standard way of doing it in Canada and it's actually smarter than using a PT plate. A PT plate won't rot but can still wick water to studs or anything touching it. Treat the cause not the symptom. Use a capillary break.
From the IRC, Section R317.1, requirements for PT or other rot-resistant wood:
Sills and sleepers on a concrete or masonry slab that is
in direct contact with the ground unless separated from
such slab by an impervious moisture barrier.
In your case, the slab is not in direct contact with the ground due to the foam and vapor barrier. Using a sill sealer also serves to separate the wood with an impervious moisture barrier. So code-wise, you're probably OK.
But there is another case to be made for PT sills. Basements flood. Every basement will experience a flood at some point. PT sills make the cleanup a little bit easier, since it is very hard to dry the moisture that collects between the sill and the slab. If you also hold the drywall up an inch or so and use plastic baseboards, the most frequent small (less than 1") floods are not even cleanup level events. Seems like cheap insurance.
Good point and thanks for the tips.