Can Larsen trusses be used for roofs?

My goal is to build a net zero home in a cold climate using the most cost efficient designs, methods and materials as possible. I’m in the design and planning stage at the moment and, to lower my costs, I plan to do as much of the work myself as reasonably possible and I’m hoping to use commonly available building materials whenever it makes sense. I’m currently in favour of using the Larsen truss system for a thick wall of dense packed cellulose but I’m wondering if that can be used for the roof as well. Has anyone seen this done before?
GBA Detail Library
A collection of one thousand construction details organized by climate and house part
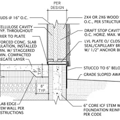
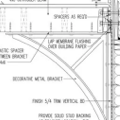
Replies
Yes. In fact one company, Ecocor, offers it as a standard panelized product: https://www.ecocor.us/panelized-roofs, using I-joists instead of site-built Larson trusses. (I used to work there and helped develop the product and get it through Passive House certification.) It's not the least expensive way to get a good roof, but if you're doing the work yourself it may be the best roof you can build. It's important to understand where your air barriers and vapor retarders are in the assembly, though.
Thank you Michael! This is a great example. I can see that they've used solid panel I-joists instead of the typical method of smaller, interspersed panels and webbing. Is that for the added strength or because I-joists are more readily available? I'm wondering, are the solid panels required for snow loads or will the standard site-built Larsen truss be enough?
Least expensive does not necessary equate to 'cost effective'. ;-)
I'm planning on putting all insulation on the exterior of an air and vapour barrier such as a 40 mil peel and stick membrane. (such as Grace Ice and Water Shield) This will leave the rafter bays empty for electrical and/or aesthetic purposes. The Larsen trusses will be covered with OSB, roofing paper, and metal roofing (with or without furring strips as specified by the roofing manufacturer).
They use I-joists for both reasons; labor is expensive, I-joists install quickly, and they provide a reliable level of strength. I know of several builders using I-joists and none who are currently using traditional Larson trusses, now that I-joists are readily available from any lumberyard. I'm frugal enough that I might build Larson trusses for my own home, but for clients it would probably not be cost-effective. It should be possible to build Larson trusses to withstand snow loads but proper design depends on several factors and would best be done by an engineer.
I didn't see you mention a ventilation space, required by code for dense-packed roofs--do you have a plan for that?
I was not aware of a requirement for a ventilation space in dense packed roofs.
Please correct me if I'm wrong, but my understanding is that ventilation of a roof assembly is not required if both control and insulation layers are adequate. An air barrier prevents moisture from entering the assembly from the conditioned space and the insulation keeps the exterior roofing sheathing and cladding (shingles, metal, etc) cold so no ice dams will form.
Any exterior moisture that reaches the top deck of OSB (under the metal and paper) will dry to the outside.
If I get an inspector that doesn't 'get it', I'll add diagonal 1x furring strips under the metal.
The IRC building code, used in most of the US where code is enforced, requires air-permeable insulation in roofs to be vented. Cellulose is air-permeable. There are examples of roofs with unvented dense-pack, some cellulose companies have promoted it, and I've had it done on my projects in the past, but it's at risk of moisture accumulation. One cellulose installer I know does it regularly on retrofits, but only if the home has a dry basement and bathrooms fans that are used. He has had problems with the cellulose becoming saturated when he didn't follow those rules. For new construction there is no reason to build a risky assembly when there are so many safe assemblies to choose from.
An air barrier does not prevent moisture from reaching the insulation, it prevents air from reaching the insulation. A vapor retarder slows water vapor movement, which diffuses from high vapor pressure to low vapor pressure--in cold climates, usually from indoors to outdoors. Vapor diffusion moves much less water than air leaks, but it still moves water--enough to create uncomfortably high moisture levels in the spring.
It's true that ice dams won't form due to heat leaking from indoors in most cases, if the total R-value is adequate, but a very thick layer of snow and/or insolation (radiative energy from the sun) can still create ice dams in some cases. But it's probably not worth worrying about, as long as you have code-required ice and water shield at eaves and valleys.
Most roofing materials are not vapor-permeable so there is little or no drying to the exterior without a vent space. Diagonal strapping under metal roofing can work, but it should be at least 1" thick to meet code, and more is better. Running it diagonally means you have to put soffit vents (or another form of intake) along the rakes, so although I've done it on one project, I prefer cross-strapping so only the eaves and ridge need to be vented.
You can specify roof trusses in almost any geometry when you order them from company that designs and fabricates them. A "parallel chord" truss would probably be what you would want. You can simply specify it to have plenty of depth for insulation.
There should be a ventilation channel above the insulation.
Do you need the attic space? If not, raised heel trusses and insulation at the ceiling will likely be cheaper and easier.
Hi Reid... It's not a need for attic space... although I do love the idea of open vaulted ceilings... it's more about being able to easily implement a perfect air barrier on the exterior of the frame rather than doing the business as usual routine of poly and drywall on the interior... something that is rarely done correctly.
The goal is to slam the front door and hear the toilet flush as a result. ;-)
User 7037573,
First of all, can you tell us your name? (I'm Martin.)
Q. "I was not aware of a requirement for a ventilation space in dense-packed roofs. Please correct me if I'm wrong."
A. You're wrong. For the full story, read this article: "Smart Vapor Retarders for Walls and Roofs."
Hi Martin... sorry about the name... I had tried to edit my profile before but it wouldn't seem to let me update the screen name. I just tried again so I'm hoping that my proper name is displayed now.
I've been reading up on dense-packed roofs since reply #8 was posted above. (I have to have my facts straight if I'm going to contribute around here.) I had to re-read your excellent article on cathedral ceilings and your replies to the comments at the bottom. I've read Joe Lstiburek's "Don't be dense" article, as well as Bill Hulstrunk's rebuttal and you're own comments on this subject.
BSC's Guidelines for Dense Pack Roof Assemblies talks about 3 possible sources of moisture in a roof assembly:
"Dense-packed roof assemblies are subject to the same moisture sources as all roof assemblies:
bulk water (introduced by leakage), built-in moisture, and water vapor (introduced by vapor
diffusion or air leakage). "
Of these three, it would seem to me that the big concern is water vapour entering the assembly from the conditioned space and with standard practises, I can understand why since air control is rarely perfect.
However, I'm talking about a perfect control layer applied to the exterior side of OSB sheathing nailed to standard framing. Harold Orr once told me that he would just use poly but in my description above, I advocate using a peel-and-stick membrane, from grade to ridge, such as the one used on Matt Resigner's "Perfect House". (In fact, my plan is directly inspired by Matt's video in which he shows open stud bays with 1x6 sheathing that is visible from the interior.) With such a perfect control layer, how could water vapour, introduced by diffusion or air leakage, ever be a problem?
My idea for a perfect wall/roof assembly consists of open rafters/studs sheathed in OSB (structural layer) and wrapped in poly or peel-and-stick (control layer) that creates a perfect air-tight building envelope. On top of this, I propose to put webbed Larsen trusses covered by webbing that allowed cellulose to be blown in and dense packed (insulate layer). On top of this, OSB, felt paper, and then metal sheet roofing (cladding).
I'm not a contractor and I've never built anything larger than a garden shed before but I've been trying my best to learn about building science and my goal is to build a cost effective, energy efficient home using readily available building materials and smart design. If my idea is crazy, I'm ok with crazy... If my idea will fail, I need to know. If I have to lay 2x4's flat on top of the webbing that stretches across the Larsen trusses before I install the top layer of OSB, then I'll open up the soffits and ridge to vent the roof... but I'd rather not if the only reason is to appease the building inspector.
While it does seem that code will not allow my roof assembly to not be vented, it would seem that it is based on the fear of incompetent contractors rather than science.
Kristin,
I would think that by putting your insulation ABOVE your decking, as you described, you would keep it far above dew point and eliminate any concern about moisture accumulation. I wonder if Michael Maines and Martin (two of the smartest people on GBA) simply overlooked your assembly or confused it with dense packing between the rafters.
If not, I going to make a bag of popcorn and enjoy the physics lesson as to why your assembly won't work. (I've learned so much from these guys so I mean this seriously.)
I posted my reply above at 2am on a Saturday night. That tells you a little about what I like to do for fun. Pass the popcorn. ;-)
To paraphrase Joe Lstiburek: There are two kinds of roofs. Those that leak, and those that will leak. I suppose the same can be said of control layers.
Douglas Higden
> On top of this, OSB
So you are going to have a layer of cold, highly moisture susceptible sheathing - sounds closer to an unvented, cellulose filled double stud wall than a "perfect wall".
I encourage you to not focus on "net zero" - while typically beneficial, it's a numbers game that doesn't lead to the most efficient ways to reduce costs and environmental damage.
I agree... The term 'net zero' really is a numbers game. I should simply use the term, 'energy efficient' but it's so abused by production builders that I felt I needed a stronger term. The 'zero' part is just a goal... I'm not going to get hung up about the numbers.
I also agree that OSB is highly moisture susceptible but my question to you is, "Where is this moisture that you speak of coming from?"
I quoted BSC above... there are 3 sources of moisture that we must address:
1) Bulk Water - A leaky roof is a problem whether it is vented or not but a properly installed roof cladding and WRB should prevent this. I would lump exterior water vapour into this point as well since this would dry to the outside.
2) Built-in moisture - Can be completely negated since dense pack cellulose is installed dry;
3) Water Vapour - introduced from the conditioned space via air leakage or diffusion which simply can not happen if the control layer is perfect... which is made possible when applied continuously on the exterior of the structural layer instead of the typical patch work of poly on the interior side.
It would seem to me that the only reason we vent roofs is to make up for poorly performing internal air barriers. The fact that venting can be omitted if ccSPF is used seems to back this up.
You can see below for tests where unvented with cellulose performed poorly and vented performed well (even at a very high 50% RH).
https://buildingscience.com/documents/building-america-reports/ba-1409-field-testing-unvented-roofs-asphalt-shingles-cold-and#f04
Even if perfect external air barriers existed (they don't), air could come from the interior, deposit moisture and return to the interior.
Interesting note: barometric cycling can cause the wetting of cavities about 10 times faster than by vapor diffusion.
Jon R,
Good point! I didn't realize it initally but Kristin would be creating a "vapor closed sandwich" with his assembly. (Peel and stick on bottom, osb/roofing up top).
Better off with really vapor open material for top layer (wood fiber board, gypsum, or wrb with strapping) along with an air space...
According to BSC...
"OSB sheathing and plywood sheathing covered with a building paper or housewrap and vinyl siding are classed as vapor semi-permeable."
https://buildingscience.com/documents/information-sheets/info-312-vapor-permeance-some-materials
And, it would seem that not all OSB is created equal when it comes to it's performance as an air barrier either...
https://www.greenbuildingadvisor.com/article/is-osb-airtight
So, it's not entirely 'vapour closed'. However, the application of a second layer of peel and stick instead of felt paper would certainly qualify.
Kristen, I did not fully understand your plan to cover the rafter bays with an impermeable membrane. That does change things, as in theory you would have no vapor diffusion (or air leaks) toward the exterior. What is your climate zone?
As mentioned previously, roofing offers essentially no drying to the exterior, so you would be creating a "vapor sandwich." There is a chance it could work ok for you, but it's far from a safe, resilient assembly. If you're building a new house I don't understand why you would take such a risk. Vented roofs are safe, easy and forgiving. Covering the Larson trusses with a high-quality, vapor-permeable WRB, creating a vent channel with 2xs run above the Larson trusses, and covering the assembly with osb, underlayment and roofing is more labor and materials, but not a lot more.
Kristin,
Roofs insulated with dense-packed cellulose need a ventilation channel between the top of the insulation layer and the underside of the sheathing above the cellulose. That's what the code reads. If you think you can get an engineer to agree with your insulation approach, and if your local code authority can be convinced by the engineer's argument, you may be able to proceed with an unvented cellulose-insulated roof.
Is it a good idea? Is it worth jumping through all the necessary hoops to get the idea approved? No and no, in my opinion. But it's your house.
The key to your assumptions is this piece of logic: "The big concern is water vapor entering the assembly from the conditioned space and with standard practices [actually, the big concern is air leakage, not vapor diffusion]. I can understand why since air control is rarely perfect. However, I'm talking about a perfect control layer applied to the exterior side of OSB sheathing."
In the real world, control layers are almost never perfect. If you go ahead with your plan, I wish you good luck.
Thanks Martin
I haven't purchased the land yet and the option exists to purchase in an area that does not require building permits or inspections beyond septic. While I understand what the code says, I was more concerned with what the science says.
Still... there is something to be said for 'playing it safe' and if it only costs me some extra 2x4s to lift the OSB 1.5" above the webbing that holds the dense pack, then maybe that is a good plan.
I'm sure I've probably harped on about this in other threads, but it's worth considering the other possible consequences of not building to code when it isn't required in your region. It can leave you open to liability issues, problems getting mortgages , and having insurance claims denied.
For Canadians it's worth remembering that codes are enacted for the entire province, even if there are no permits or enforcement in certain remote areas.
Hey Malcolm... I totally agree. For the most part the codes are there for good reasons... but sometimes we need to rethink those reasons and challenge them when new methods or evidence is presented. However, your comment about the insurance claims gave me pause.
What do you mean when you say that codes are enacted but not enforced? What good is one without the other?
Putting the control layer on the exterior seems like the best approach but I hate the idea of using such an environmentally un-friendly product as rigid foam (especially XPS) as the insulate layer. Dense packed cellulose seemed like such a great idea but it's going to be very difficult to install on a slope without a second deck on top.
In Canada, many rural areas and small towns, especially in the north, do not require building permits or inspections, but are still subject to our building codes. That is a different situation to some areas in the States where codes have not been enacted at all. The preamble to our code here in BC says that it covers the whole province, and that it is incumbent on owners to make sure their projects meet code.
Very interesting! I've been trying to learn more about the Ontario Building Code but it seems shrouded in secrecy and getting a straight answer on anything seems to require paying someone or buying a $200 book and reading it myself.
Our code costs almost double that. I've never understood why you should have to pay to see the laws you have to abide by.
http://www.buildingcode.online/
Section 9, for the most part, is the section of interest for residential construction.
Google "2012 Building Code ontario pdf" and the first couple of hits usually result in what you'd like (the links come and go).
Though, personally, $200 put towards what will likely be the average person's largest life purchase is worth the cost.
Though, I also agree that all relevant laws/codes/etc. we pay taxes on to draft should be made publicly available for free. If ignorance of the law isn't an excuse, it makes no sense to hide the knowledge or to force me to pay for it twice. Unfortunately, we are not alone in that.
https://arstechnica.com/tech-policy/2017/03/public-records-activist-violated-copyright-by-publishing-georgia-legal-code-online/
Kristin,
Q. "What do you mean when you say that codes are enacted but not enforced?"
A. Malcolm has explained the situation in Canada. The situation in the U.S. is similar, especially with respect to energy requirements. Even when building inspectors show up on a job site, few are qualified to understand or enforce energy codes. Many researchers have looked into the issue, and have convincingly shown that in the U.S., energy codes have been enacted without being enforced.
"Cost effective."
Traditional gable truss roof with raised heels, flash coat penetrations and wall plates, cover with cellulose. KISS.
If only it were that simple. If air sealing this type of wall assembly was so easy then why do we have so many leaky houses? I can appreciate this simple method but getting the details right seems to be a challenge. Part of my challenge was to design a wall and roof assembly that could support super insulation and simplify the air sealing by employing a continuous air barrier on the exterior.
... and I like vaulted ceilings.
We have leaky houses because very few people air seal the ceilIng plane. It is that simple.
If you insist on a vault, I dont know why you wouldnt go parallel chord truss to eliminate thermal bridging, sheet the bottom chord to air seal. Strap the ceiling if you wanted a service cavity but I digress, Im talking to myself.
OK... thanks to all who commented. The consensus seems to be that Larsen trusses would be strong enough to be used on a roof but that using I-joists might be less labour intensive for production builders.
As for my assembly, I did some more research and re-watched a video with Joe Lstiburek called, "To Vent or Not to Vent" and he makes the case for a vented over-roof on top of a vaulted roof with an exterior air barrier and insulation. His reasoning has nothing to do with rot due to moisture entering the insulation layer and condensing on the under-side of the roof deck... it actually has to do with ice damming due to the thermal properties of snow accumulation.
I've modified my roof assembly idea accordingly. (see attachment) The layers, from inside to outside, are as follows:
- Load Bearing Structural Wall/Roof (Dimensional Lumber or timber frame)
- Wall Sheathing (OSB, plywood or 1x6 with diagonal bracing)
- Continuous Air Barrier applied to the exterior of sheathing (pictured in blue... peel and stick membrane or poly)
- Larsen truss (with Isoweb, not shown)
- 2nd layer of sheathing (OSB or Plywood)
- Cavities between trusses dense packed with cellulose
- Roofing paper
- 2x 'sleepers' running vertically to create a channel for airflow from facia vents to ridge vents
- 1x furring strips running horizontally to provide surface for attaching sheet metal roofing
- Sheet metal roofing (Galvalume shown)
This checks all the boxes, right?
[√] Uses relatively inexpensive, readily available building materials
[√] More environmentally friendly than rigid foam (and possibly less expensive?)
[√] Perfect air sealing within reach of the mortal man
[√] Allows for variable width for super insulation
[√] Works everywhere!
... and the vaulted ceiling makes the wife happy. :-)
I didn't finish the drawing. It needs exterior cladding on the walls... but what works for the roof also works for the walls... roofing paper, vertical 1x furring strips to create a rain screen and horizontal cladding such as ship lapped cedar would work.
Kristin,
There are a few areas where things look a bit unresolved .
- Presumably the sequence of construction is to erect the structural frame, sheath the walls and roof, then install the air barrier. That needs a bit of thought if you go with a timber-frame roof structure, as there will be nothing to attach the sheathing to until the Larson trusses are installed. To make it work you will need a conventionally framed roof structure, which gives you a deep cavity you don't seem to be planning to use for anything, and another deep truss space above. That's a lot of roof.
- Similarly, the air-barrier and insulation don't need to extend down to the fascia, and there is no way to extend the sheathing out to the overhang until the trusses are installed.
- Using the trusses to frame the overhangs mean they will end up being very deep. Something that will have a big effect on the look of the house and what materials can be used for the fascias.
Malcolm,
"... a bit unresolved" is a very kind understatement. ;-)
A timber framed roof would be no different than a conventionally framed roof. The idea is to start with a fully sheathed frame. It could be a barn with 1x12 pine for a roof deck. As long as we can apply our continuous air barrier on top of it... you could walk all over this and take your time laying down your trusses. The trusses only act as air-permeable baffles for cellulose and to hold up the roofing and any snow load that occurs. The rafters beneath the sheathing (not the trusses) support the entire roof (just like a normal roof) and need to be engineered for this.
It is a lot of roof. I like the idea of exposed rafters and roof decking (especially if it consists of planking instead of OSB) but this is also a place to run electrical without worrying about complicated air-sealing. Lights and fans could easily be installed with or without exposing the rafters. Many folks like T&G ceilings despite the issues they cause due to their 'leaky-ness'... but in this case, that would be a good thing.
In Joe's video about venting, he recommends extending the air barrier (and the insulation) down to the eaves and venting the facia and not the soffits. This is to prevent radiant heat from the sun hitting the cladding and rising up into the soffits.
"Using the trusses to frame the overhangs mean they will end up being very deep. Something that will have a big effect on the look of the house and what materials can be used for the fascias."
You are absolutely correct. This is a detail that I had not completely figured out. With no rafter tails, how do we support the overhangs? Temporarily supporting them until we lay down the trusses on top and then tack them up from beneath doesn't sound like a great idea. Pre-building sections on the ground might work.
Another idea would be to hang rafter tails and soffits from ledger boards on the outside of the wall truss assembly.
Another idea is to extend the roof out 6' or more and create a covered porch along the entire length of the building on both sides (something that appeals to me regardless) with posts and beams holding up the eaves.
Kristen,
I brought up the timber framing because unlike conventional stick-framing, it typically has a much larger spacing between the structural elements, which would leave nothing to attach the roof sheathing to.
I guess what I'm wondering is whether there is any advantage to paying for and installing a complete structural roof, then having to build deep Larson-trusses on top, when you could achieve the same goals by using a variety of load-bearing options (I-joists, parallel-chord or scissor-trusses) and then building a shallow service cavity below.
This would solve the overhang problem, and avoid the difficulties of site-building something that needs engineering. I can see the appeal of the Larson trusses on the walls, but I can't quite get there with the roof.
I agree... and apparently most of the industry does as well... placing your insulation between structural members seems to be a much easier way to do things... however, it makes getting air tightness difficult.
My goal is to have a continuous (and thus superior) air barrier that connects to the air barrier of the walls... which connect to the air barrier beneath the slab... etc... The only way to do this is to put it on the outside.
If my ideas seem needlessly complicated and expensive, look at how folks are doing things now... fancy (read: expensive) new materials and products that all claim to help in one way or another (zip this and tyvek that)... a reliance on foam (rigid and ccspf) for just about anything and everything... special factory-made solutions for air-sealing, venting, insulating...
I'd love to come up with a wall and roof assembly that anyone could build with readily made and relatively inexpensive materials... using the best understanding of building science that we have.
Kristin,
That will work, as long as your so-called "Larsen trusses" -- presumably, site-built -- are designed by an engineer.
I agree. That's always a good idea. In this case, I would find the physics very interesting. Unlike I-joists which are meant to be used to provide support for a open span, these will be installed directly on top of the rafters beneath 24" OC. Thus span strength would not be an issue. The concern would likely be more about crushing forces due to snow load and the static load of the roofing above. This is actually the main reason for my original question. Like you, I questioned whether or not Larsen trusses would be strong enough for this purpose.
My limited understanding of installing dense pack cellulose: You need a closed-in cavity that is not large, to be able to pack cellulose at high density. By using Larsen trusses (instead of I-joists), that would open up spaces among adjoining joist bays in your insulated roof. In contrast, I-joists would provide confined spaces every 24"o.c. (or whatever roof joist spacing you plan). Even then, pretty big areas compared to wall cavities. Having the deeper space of a roof, getting the highest cellulose density and R-value per inch isn't as critical as a wall. Just make the cellulose cavity deeper to get the same total R-value with less R/inch cellulose density. And there's less concern about cellulose settling and leaving an air space at the top of joists than at the top of wall studs. (Unless you have a steeply pitched roof.)
Robert, I mention in post #31 that the Larsen trusses would employ Isoweb but that it is not shown. I should have made that more clear. I have not illustrated the assembly with Isoweb in order to provide more clarity... but also because my SketchUp skills aren't quite there yet. ;-)
Adding webbing to the trusses turns them into air-permeable baffles for installing the dense pack cellulose.
However, you still make a very valid point. Even with webbing on the trusses, I'm still creating cavities that are 24" wide and 12" deep... and how many inches long? Well, wall cavities would be at least 8' high but, as you point out, this would be a vertical cavity. Cavities on the roof could span from eave to ridge and that could be much longer... and on a slope.
One of the ideas that I had was to break this up with horizontal members every 48". This would create 2' x 4' x 1' cavities that I'm hoping would be easier to dense pack... and provide resistance to racking forces. We wouldn't want the entire assembly to flop sideways like dominoes... and when we extend the overhang on the gable ends, it will become necessary to switch to a more horizontal layout so that 2/3 of the trusses sit on the roof deck and only 1/3 cantilever over the edge.
Kristin: You wrote:
"As for my assembly, I did some more research and re-watched a video with Joe Lstiburek called, "To Vent or Not to Vent" and he makes the case for a vented over-roof on top of a vaulted roof with an exterior air barrier and insulation. His reasoning has nothing to do with rot due to moisture entering the insulation layer and condensing on the under-side of the roof deck... it actually has to do with ice damming due to the thermal properties of snow accumulation."
Its been a while since I've watched that [excellent] video- but I suspect he is referring to an unvented roof that uses rigid foam and not air-permeable insulation like cellulose or FG? Without the air gap, where would your assembly dry if a little moisture found its way in? Remember that roofing is generally vapor closed.
Also- I would research rather or not OSB is a good choice for your outer sheathing layer both on the roof and on the walls. Yes, OSB is vapor open at 2-3 perms (and 10 when wet) but this may not be enough in your cold climate/ thick insulation layers- especially on the roof- even with an air gap. With really thick walls- very little energy (heat) is making its way to the outer layer of OSB so the OSB remains really, really cold. With radiation, it can even become colder than the air around it. This is bad as it becomes a condensation risk. There is a reason that many high performance builders use vapor open fiberboard sheathing or a WRB as the outer sheathing layer. (Google: Scranton Passivhaus, Pumpkin Ridge Passivhaus, Ecocor wall)
Please watch this this vide0: https://youtu.be/sBcNFeiWjrg?t=1310
(The relevant part starts at 21:50): Joe is talking about double stud walls here but the design points are identical to the Larsen Truss wall/roof assembly that you are thinking about. (He says this himself.) Given the stack-effect- I would take this even more seriously for a roof assembly.
Takeaways from video: At a minimum, use CDX plywood as your outer sheathing layer. I noticed that there is no rain screen gap on your wall detail. Was this going to be added later? I think that this would be essential to allow a place for the vapor to diffuse. The video speaks to this too.
EDIT: Sorry Kristin: I re-read your post- you stated that you had not yet finished the drawing and would add the 1x furring strips later. You also said OSB OR plywood for sheathing layers... Sorry missed both. Use plywood for exterior! :-)
Rick, you wrote, "... I suspect he is referring to an unvented roof that uses rigid foam and not air-permeable insulation like cellulose or FG?"
You are correct. His example does show rigid foam but the entire point of my research here is to find a way to avoid rigid foam in a vaulted roof. The cost of any foam insulation, both monetary and environmentally, is too high if the goal is to super-insulate.
"Without the air gap, where would your assembly dry if a little moisture found its way in?"
The moisture would find it's way out the same way it found it's way in. The assembly is designed to dry to the outside so if moisture finds it's way through the metal sheeting, past the roofing paper, and through the OSB... then the it will find it's way out again through the same methods. Again, if you have a leaky roof, you have a bigger problem and you need to solve that problem first.
"Remember that roofing is generally vapor closed."
Not this roofing... above the insulation is OSB and roofing paper... both vapour open.
Although, one idea that I had was to not install OSB and roofing paper over the dense packed trusses... but instead just lay down more Isoweb... but that puts a lot of faith in the water tightness of the metal roofing and I would worry about not having a drainage plane for wind driven water.
Rick... I watched that video again... thanks for reminding me about this one. It's another great video and I had forgotten that he had provided an illustration of a truss wall assembly. You are correct... plywood would be a smarter choice and if I went any thicker than 12", something even more vapour open would be required. It makes me wonder if this layer of sheathing could be omitted entirely. It doesn't seem to be structurally necessary. The spacing and rigidity of the trusses could be achieved with horizontal furring placed on top of Isoweb before the cavities are filled.
Kristin,
First off: Sorry about mis-spelling your name.
"My goal is to have a continuous (and thus superior) air barrier that connects to the air barrier of the walls... The only way to do this is to put it on the outside."
Wouldn't having the sheathing (air-barrier) on the underside of whatever roof-structure you chose, and then building a service cavity, achieve the same result? That's done quite frequently.
I completely agree about the proliferation of needlessly complicated and esoteric building assemblies. I guess where we differ is that I see several well performing walls and roofs that have been used on high-performance projects featured here on GBA that are quite simple. For walls, either using exterior mineral wool, or double-studs. For roofs, ventilated truss-spaces using either conventional or scissor-trusses. None of those are difficult to build or yield risky assemblies.
No worries about the name.
"Wouldn't having the sheathing (air-barrier) on the underside of whatever roof-structure you chose, and then building a service cavity, achieve the same result? That's done quite frequently."
How do you attach the air barrier of the roof with the air barrier of the wall if one is on the inside and one is on the outside? If you put the air barrier for the wall on the inside, then how do you connect it to the air barrier under the slab? The best place for an air barrier is on the outside where there are no interior partition walls to work around and less holes for plumbing and electrical to worry about. And isn't it easier to lay a sheet of poly down then try to stick it up?
Maybe I'm getting a bit obsessive about this continuous air barrier thing but it seems like such a better idea than a patchwork of poly that looks like a toddler tried to wrap a xmas present with packing tape... from the inside.
I was inspired by Matt Resigner's '500 Year House', the REMOTE wall system, and Joe Lstiburek's 'Perfect Wall'... they all sound great but they all rely on rigid foam which is expensive and not particularly eco friendly. It just seemed like a good idea to investigate whether or not using cellulose would be possible. That's when I discovered Harold Orr's Prairie Wall... and eventually the Larsen Truss... but neither Mr. Orr or Mr. Larsen used cellulose on the roof.
I think a cross section would answer your air barrier continuity. Ceiling plane hits top plate, top plate transfers your "red line" to exterior wall sheathing. Lock the bottom plate to the slab, you dont need to connect to your underslab poly. You seem to be overthinking this, a standard house isnt too many steps away from being very sealed, it isnt difficult but chasing dollars leaves these basic steps out with standard building practices.
T, I agree.
> The best place for an air barrier is on the outside
Lstiburek:
"The significant disadvantage of exterior air barrier systems is their inability to control the entry of air-transported moisture into insulated cavities from the interior."
Others:
https://foursevenfive.com/blog/an-interior-air-barrier-does-it-better/
Kristin, high performance builders connect wall sheathing/air barrier to ceiling air barriers regularly. There are several approaches, depending on the assembly. The simplest, in an assembly like yours, is to run an airtight membrane over the top plate before setting rafters or trusses, taped to the sheathing and to the ceiling air barrier. If you're using double stud walls, it's often easier to use a strip of plywood or osb over the top plates. On the projects I've been involved with there is no "patchwork of poly;" quite the opposite. One current project has Zip sheathing under the roof trusses as an air barrier/vapor retarder, but more often we use Intello.
Have you designed or built houses, or high-performance houses, before?
Jon, if that was a concern you could design the building to be able to be in a slight negative pressure.
That has been shown to help. But not in the case where you have an effective exterior air barrier and little to prevent interior air from reaching the cold exterior, depositing moisture and then returning to the interior.
If there is an effective air-barrier is on the exterior and there is a finished interior surface like drywall, what is the mechanism that drives the interior air into the cavities?
i guess a second question w0uld be: Has moving the air-barrier to the exterior been shown to cause problems in the real world, or is it a theoretical concern?
Hey Kristin, I'm in a similar situation as you but a little further along in the process. I'm building my own efficient house, and by building I do mean building as in I'm the one up there swinging a hammer and not just writing checks. It's been a great experience (even on the rain soaked days where tools are failing and your patience is tested) and you'll learn a lot as you go through the process.
A few comments...
There is no perfect air barrier. There really is no perfect anything once you're on site and the sooner you realize that, the better off the end product will be. An engineer had this sign taped to his cubicle that's always stuck with me: "In theory, practice and theory are the same. In practice, they are not." It's good to remember that one as you're penciling out ideas.
I've been lucky enough to work with a good designer and engineer who understand and appreciate energy efficiency, the reality of budgets and logistics, what it takes to build, and they were able to take my ideas and plans and bring them to the next level while also making the house better and easier/cheaper to build. I highly recommend getting good professionals involved at this stage.
I took on the challenge of building a vaulted ceiling for part of my home. We knew it would present challenges, but like you I thought it would be worth it for the impact it would have on the house. After looking at a few options we went with 14" I joists as the roof rafters. We're copying the Fine Homebuilding 2016 Pro Home model of using the top flange of the I joist to attach rigid foam creating the vent channel. It's a little labor intensive as is, but less of a concern since I'm personally doing that labor, but still has significant benefits like being code compliant and understandable to the building inspectors (don't underestimate the importance of this!), proven engineering calculations, easily sourced materials, and the ceiling is nice and planar!
Building your own Larson trusses is going to have challenges on those fronts for little benefit. The I joist can be furred out to get more R value if you like.
I'd strongly recommend going with proven assemblies wherever you can. Reinventing the wheel is time and money consuming and there are going to be enough surprises even with proven and known assemblies that it's hardly ever worth it to try to pioneer a new approach without having a lot of real world building experience.
Also, a note on peel and stick/ Ice and water membranes since I've been doing some of that this past week...THEY SUCK!! Well, to be fair they can suck to install. They don't adhere well if it's cold or wet and they really stick to themselves when it's dry and warm. The rolls often have little wrinkles when you roll it out and those can amplify as you peel the backer off. The list of toxic/carcinogenic components can be shocking, and the rolls are expensive to boot. They do have their place and are very necessary and should be used, but don't just think that they're some kind of magic wand that makes everything instantly impervious to any moisture problems. My hat is off to the guys out there who have enough experience and skill to apply those perfectly flat and smooth applications you see in photos, but realize that it ain't that easy in real life.
Good luck!
-Andy
Andy... your post is gold to me! Thanks so much for taking the time to contribute here. I really enjoyed reading it.
I've been working on a shed recently... 8x12 footprint... stick framing covered in pine barn boards... and a galvalume roof. Nothing fancy but I started with months of design when the weather was cold. I spent hours in Sketchup and really tried to put to use some of the armchair knowledge that I've gained from researching my house build. I have experienced, first hand, how all the best laid plans can quickly spiral out of control when you're actually building something. I've made mistakes... lots of them... some even cost me money... but I accept each one as a learning opportunity.
Your words about how there is 'no perfect anything' really struck a chord with me as I've experienced this time and time again.
Your comment about the importance of making things understandable to building inspectors was also not lost on me. I've yet to have the pleasure of meeting one but I've heard stories and it is something that keeps me up at night.
Thanks for the tips on the peel-n-stick. I wondered about that. I think I'll try it on something small (like a shed!) first. ;-)