Can I use spray foam with a vapor permeance of 1.3 at 3 inches for an unvented roof?

As part of a remodel, we are considering creating an unvented roof situation, in Seattle, without the option of adding insulation to the exterior of the roof deck. My understanding is that along with making the finish surface (drywall) as airtight as possible, what you really want is a spray foam with a vapor permeance between .1 and 1 to act as a vapor retarder. Is 1.3 close enough? How much difference do the .3 perms make? Would adding a coat of PVA primer directly to the foam take care of the issue? The roof joists are 2X4; we want to minimize loss of ceiling height.
GBA Detail Library
A collection of one thousand construction details organized by climate and house part
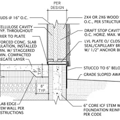
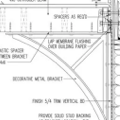
Replies
What you really want is a spray foam with no permeance, which means closed-cell rather than open-cell. A 1.3 perm material is sufficiently vapor-open to allow the potential for condensation under the roof deck. Of course completely air-sealing the ceiling and applying a vapor retarder primer to the drywall will minimize the potential for moisture in the roof assembly, but not eliminate it.
You will also be far better off by also installing a thermal break/vapor barrier, such as foil-faced polyiso rigid board insulation under the rafters. Surely you can afford to lose 1" or 2" of headroom. Tape the seams and foam the edges for a good air barrier.
Also, you're in climate zone 4, which requires R-38 ceilings. You're a long way from that target with 3" of open-cell foam and thermal bridging through the undersized rafters.
Robert, would your answer have been different for a mixed-humid climate? Or do you think closed cell is the best foam choice in any case?
Patsy, your specs will work just fine. And do spray on the vapor barrier primer.
That is what an Icynene contractor would do.
I am not for using board foam with any air space to another foam. Too much can go wrong.
If higher r value is desired, you must radically redo roof which you most likely are not going to do.
Interior moisture must be very controlled when building tight double air barrier construction.
Hunter,
Open cell foam in an unvented roof, without perfect moisture control below (both air/vapor barrier and spot and whole-house ventilation) can be problematic because it is vapor open and will hold water like a sponge against cold sheathing (it is a non-hygrosocopic material that forms a hygroscopic matrix).
Closed cell foam has the advantage - with perfect installation and no separation from substrates - of blocking vapor diffusion, but the significant disadvantage of also preventing drying of the unvented sheathing if there is a vapor-impermeable layer above it (particularly self-adhering membranes).
So I don't normally advocate any spray foam in an unvented roof assembly - there are just too many variables that are impossible to control in the field. But, since in this case the OP wants some insulation in an unvented 2x4 roof assembly, the least worst option would be closed-cell foam and foil-faced polyiso, well taped and sealed, beneath the rafters.
And I never advocate an unvented roof. Venting mitigates at least four common problems, including allowing a roof to dry. A Florida Solar Energy Center study showed that a roof sealed both above and below simply did not dry out after a weather-related leak, in either hot/humid Miami or cold Boston.
My recommendation would be the same in any climate for the same minimal roof section.
Patsy,
Be very wary of anonymous "advice" since it's almost always wrong.
"your specs will work just fine."
Your specs will not give you either an adequately insulated roof or a moisture-durable roof.
"That is what an Icynene contractor would do."
Unfortunately, this is all too true. Icynene contractors are in business to sell a product and often abuse building science in order to do that (for instance, by selling too little insulation in order to keep down cost and make the sale).
"I am not for using board foam with any air space to another foam. Too much can go wrong."
There is nothing at all wrong with an air space between two layers of impermeable foam. In fact, a foil-faced air space will offer as much as R-3.5 for free in a slanted ceiling.
"If higher r value is desired, you must radically redo roof"
Not at all. Just follow my advice and add an inch of two of foil-faced polyiso beneath the rafters for vastly improved performance, summer and winter.
"Interior moisture must be very controlled when building tight double air barrier construction."
Interior moisture must be controlled in any new construction. That's required by code.
Robert, if I may (and sorry to the OP for deviating from the original question), isn't the closed cell contradictory to the discussions we've had recently about the need for vapor-open assemblies and drying to both sides (climate specific)? Also, it seems that venting a roof in a cathedral ceiling or conditioned attic could also be difficult in the field to get right, while keeping air barriers on all sides.
Hunter,
In my book, vapor-open assemblies are always preferable, as long as they aren't likely to cause more problems than they are intended to solve.
In new construction, I never recommend (or use) spray foams, never recommend or use unvented roofs, and never recommend or design cathedral ceilings (they create a plethora of problems and are almost always unnecessary from a functional perspective).
But the OP wants to insulate an undersized roof assembly (2x4), apparently does not want to do anything above the roof deck, and doesn't want to build downward. That leaves no option except a high-R closed-cell spray foam. Open cell is OK for a vented roof, since any moisture that diffuses outward and condenses on the sheathing can dry through convection. For an unvented roof, closed-cell is preferable to mitigate against condensation. But, both to block thermal bridging and to create a more reliable air barrier than foam sprayed against non-stable wood members, I recommended well-sealed foil-faced polyiso. That would offer an air-tight assembly with maximum R-value in a minimum of space, without losing much head room. Assuming the is roof covered with asphalt shingles with felt underlayment , it can breathe and dry to the outside. And that puts the air/vapor barrier where it belongs in the north country - on the inside.
Diffusion is not going to make a wet sponge of open cell. Show me a case of this.
Foamboard is very tricky to install. Why? Because of air leaking past it.
Open cell spray foam glues itself to sheathing.
Any moisture that gets into Robert's assembly will likely stay and be a problem.
Robert is going against his own good advice to plan for future leaks as eventually all roofs leak.
Open cell with no boardfoam is indeed the best long-term assembly given the needs of the questioner.
I question those that attack "the anonymous" . Debate is good. Debate Robert instead of the cry baby act.
Anonymous,
You wrote: "Diffusion is not going to make a wet sponge of open cell. Show me a case of this."
Here's the case. It's an article I wrote for the July 2005 issue of Energy Design Update:
Every Failure Holds a Lesson
Thanks for all the thoughtful input! I realized that I didn't specify that the foam I was thinking of was a medium density icynene, but, you all figured it out. I was also intending to include a thermal break. My reading, mostly from the people at Building Science Corp., indicates that a class II vapor retarder is preferable to a class I (vapor barrier) because it will provide some opportunity for drying. The roofing is asphalt shingle, but we don't know what the underlayment is.
The only "baby" on this site is the one who does not have the honesty, courage and maturity to stand by his words but needs to hide like either a coward or a scoundrel (likely both) behind the dark curtain of anonymity.
And it is no wonder that Anony Mouse feels a need to hide when making wild, unsupportable and highly biased statements.
I've thoroughly explained this to any who are not blinded by either ignorance or bias. The assembly I suggest, though hardly optimum, can dry to the exterior if it does not have an impermeable roofing or underlayment (not likely).
I don't think Seattle considered a 'cold' climate.(?)
(oops, my post was cut off)
...I imagine they have a pretty large summer vapor drive. I know the closed cell will still be beneficial to this...I'm just becoming confused as to why this differs from the vapor-open walls we've discussed. Perhaps it's the intense heat from the roof shingles.
Hunter, I'm pretty close to Seattle and can tell you that I've seen problems here in attic caused by cold roof sheathing and warm moist air in the attic.
What about installing 3" foil-faced polyiso between the rafters, held flush with the bottom of the rafters--that gives you a 1/2" airspace above--and another layer of 1" foil-faced polyiso continuous across the bottom of the rafters, taped and edge-foamed?
I've done too much remodeling to be comfortable with SPF against the roof deck. I've done many, many repairs where it was necessary to remove and replace roof sheathing, and would hate to find it glued in place with foam. You'd hate my bill for dealing with that, too. So much better to lift a piece of sheathing and find a nice clean foil-faced install just below.
Hey Martin, how about a "edit my stupid spelling mistake" button to go with my posts?!
that's not a bad idea David. would you install nailers on the sides of the raters, at the sheathing to attach the polyiso to, or just fit is snug to hold in place until the bottom layer was attached? or leave a small gap to caulk or foam airseal it to the rafters?
David,
Apologies if this is a dingbat question, but, is your 3" polyiso suggestion still assuming an unvented situation? And then that if that air gap does see vapor/condensation, drying to the outside can occur?
I have to say I'm loathe to use a full on vapor barrier. Contrary to what Robert has said, my understanding is that closed cell spray foam is a class II vapor retarder, not a vapor barrier, and that if applied 2" or thicker, it will have the effect of dissipating the vapor to the extent that there is virtually nothing left to condense. It's not impermeable, it has some drying potential, which I think would make it a good choice in this case. The problem is we don't like the global warming potential of closed cell foam. That's why I was asking about the perms; there's a medium density icynene product that is sort of in between open and closed cell that has a perm of 1.3, which I was hoping could be made to function like a class II vapor retarder (perms .1 - 1) in combination with a vapor retarding primer.
Patsy,
Closed-cell SPF @ 2 pcf has a perm of 1.1-1.4 per inch. That means that 3" would have approximately 0.4 perm, which makes it a tight class II vapor retarder. Remember that these classes and names are arbitrary. What' s important is not the name but the dynamics.
Without a perfect ceiling air/vapor barrier, a low-perm material like SPF can allow vapor diffusion sufficient to cause condensation on a cold roof sheathing. Once condensed into liquid water, it cannot return through the SPF, which IS impermeable to liquids. There may be some outward drying potential, but that can be negated by alternating rain and sunshine, which can drive moisture inward (which is why vented roofs are always more durable than unvented roofs, except perhaps in wildfire zones).
David's suggestion is a good alternative, using a lower-footprint foam: polyisocyanurate. But I would not only leave an air gap at the sheathing for drying potential (an air gap is second best after a vented roof), I would leave a secondary gap between the foam blocks and the under-rafter foam board. This will offer about R3.5 for "free" and also create a radiant barrier from summer solar gain. And the solar heat retained by the roof (i.e. not passed through to the ceiling) will aid in drying the roof deck.
Hunter, I think I'd rip up a bunch of 1/2 x 3/4 sticks and tack them to the sides of the rafters, up against the roof deck. Then, cut the insulation at rafter bay width minus 3/4. That would allow a 3/8 gap along each side of the foam, perfect for the nose on a Hilti foam gun. I would want to get the gun foam all the way back against the sticks and completely fill the gap, then trim the excess. I've seen guys put foam board in too tight and then try to force foam into a small gap.
Patsy, what I am suggesting would probably be questionable if your assembly now depends on drying to the inside, which it might. If you don't have a vent path then you'd have to decide whether solar vapor drive is a concern, and it might be. That said, if it is a concern, it might be a much bigger concern with SPF under the deck. In any situation where you are talking about "tightening" your house, I would run a blower door test and evaluate the ventilation situation. I would not be looking to create or continue a situation where interior moisture needs to leave via air leakage.
To clarify my comment about a gap being second best to a vented roof (all other things being equal), because this dynamic may not be commonly understood...
Water vapor in air will diffuse, under vapor pressure differential, through any vapor-permeable material, and will condense on any surface that is below the local dew point (which is determined by absolute humidity and temperature at that surface).
Once condensed into liquid form, water will diffuse (soak) into hygroscopic materials or a hygroscopic matrix in a non-hygroscopic material, like open-cell foam, where it will remain until driving forces - such as gravity, capillarity, surface tension, and temperature gradients - move it to a surface where it can find free air.
In order for liquid water to evaporate, it needs two things: enough energy to shift it to a gaseous state and enough additional energy to overcome local air pressure. It cannot evaporate unless it can expand into a gas, and this requires contact with air (or air pockets within a solid matrix).
So water vapor that reaches the underside of a cold roof deck and condenses into water will remain at that junction (or soak into porous materials) unless there is heat and air. Thus, an air gap underneath the roof deck - even without ventilation to the outside - will allow condensate to return to vapor, which can then diffuse back through either interior or exterior layers with the appropriate driving force.
So, after a fully-vented roof deck, second best is an air gap under the deck and some route for vapor migration, ideally in the dominant thermal drive direction.
Let me try that again:
Excellent idea. My thought in leaving the 1/2" air gap at the top is that the foil is more likely to perform as a reflective barrier if the gap is larger. The number that usually gets tossed out is 1" as a minimum, but I have no idea how much importance to give this. A gap between foam layers is definitely free R-value.
Robert,
The clarification is very helpful, I appreciate it. With respect to the gap between the polyiso, that's a new concept to me. The idea is that the two polyiso boards are trapping and insulating the air between them? Wouldn't that rely on a perfect air barrier?
It seems that having the polyiso at the top and bottom would stop the vapor from both directions, helping with the summer inward drive too. Connecting the 1" air space at the bottom to a continuous soffit vent and top to a ridge vent, now it's vented- this could be a great approach. As always, air sealing is critical. I agree with David that a blower door test would be a good idea before getting too tight.
Any low-emissivity air gap in a roof assembly will help reduce radiant transfer, but generally an upward-facing foil layer will collect dust and lose its reflectivity. Thats why attic radiant foil barriers should be stapled to the underside of rafters with shiny side down.
The thickness of a radiant gap is less important than the emissivity of the facing surfaces. In a 45° roof/ceiling with summer heat moving downwards and two facing foil surfaces, a 3/4" gap provides almost the same R-value (3.47) as a 1½" gap (3.50). With one foil surface, those numbers reduce to 3.27 and 3.30.
The lower the pitch (closer to horizontal, which means less internal convective looping), the higher the effective R-value of radiant spaces. In a flat roof/ceiling assembly, those numbers would be 3.80 and 6.41, with a 4" foil-faced gap offering 10.7 "free" R-value (which is why the best place for a radiant barrier in a cold climate is in the floor over unconditioned space).
Patsy, a radiant barrier has nothing to do with trapping air (though that helps reduce convective heat transfer). Radiant heat transfer occurs directly from surface to surface, whether air or the vacuum of space intervenes. Radiant transfer diminishes by the inverse square rule: as the distance doubles, the radiant intensity reduces by a factor of 2² or 4, which is why deeper gaps often provide greater effective R-value, unless they are vertical, such as in a wall, in which case anything wider than 3/4" will have less effective R-value because of convective loops (this is also true in double-pane windows, which is why they have to be thin).