Can I spray closed-cell insulation on inside of brick wall ?

I live in South Louisiana and am remodeling a Ranch Style Brick Home. I have removed the drywall and have 2 x 4 studs, 1/2 ” impregnated sheathing, 2 1/4 ” dead space then brick and mortar.
If I remove the 1/2″ sheathing from the inside (easy to cut out) , this would give me 6 1/4 ” space to insulate. Could I spray the closed cell spray foam directly aganist the inside brick wall filling the wall cavity up to edge of 2 x 4 , then finish with new drywall? Would this create any future problems for walls?
GBA Detail Library
A collection of one thousand construction details organized by climate and house part
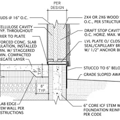
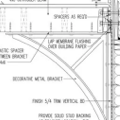
Replies
First, the sheathing is likely structural, and you'd have to cut in steel to keep the place from racking if you cut it all out. Closed cell foam is sort-of structural at 2", but nothing like half-inch plywood or timber.
If that's taken care of the short answer is "it's probably OK", but a lot of details would have to be looked at, particularly the flashing around doors & windows. The cavity by-design allows the brick & mortar to dry in both directions and keeps rain-moisture penetrating the brick from affecting the wood. With 2" of closed cell foam between brick and wood the wood is protected, but all of the moisture is exiting toward the exterior, which may erode the mortar more quickly than it would otherwise. In cold/very-cold climates filling the space could even lead to freeze/thaw spalling of the brick, but that's not very likely in S.LA, eh?
Leaving the studwall wall cavities empty isn't recommended, since that allows fire to spread rapidly and may create a thermal-bypass channel undercutting the performance of your foam. It may be cheaper & better to give the brick a nominal inch of closed cell for air sealing & vapor retardency, then filling the rest with open cell foam or cellulose. But the flashings all should be looked at to guarantee that no water can end up in the studwall, since the masonry cavity had been a drying path for the framing and it won't be when you're done.
All said & done I probably wouldn't take that route were it my house, even if it sort-of works on paper. YMMV. In the UK they've taken to blowing EPS beads into masonry cavities with some success, but I'm not sure how well that works out in the long term. Bead insulation is very air-permeable and the drying path still works, whereas closed cell polyurethane pretty much blocks it.
Please reply, taking into consideration that the sheathing is not at all structural, it is a soft fiber board and can be ripped apart with bare hands. Also the exterior of the brick will be painted with Rhino Shield , a ceramic coating that is waterproof .
Theresa,
First of all, all wood-framed homes need wall bracing. Just because the fiberboard sheathing on your home is in bad shape, doesn't mean that the fiberboard wasn't intended to provide wall bracing.
There are two possibilities: either the fiberboard sheathing used to be in better shape, and provided adequate wall bracing but no longer does, or else the fiberboard sheathing is still providing useful wall bracing in spite of the fact that it appears flimsy to you. In either case, however, your wall needs adequate bracing. Removing the fiberboard sheathing without considering the effect of the removal on your wall's racking resistance is potentially dangerous.
Second, your brick veneer has an air space behind it for a reason. The air space allows any water that gets past the brick veneer to drain, and the air space helps the damp bricks dry safely. You should not fill the air space with insulation.
Third, the manufacturers and distributors of Rhino Shield exaggerate its miracle qualities. Rhino Shield is paint. It is not a "ceramic coating." Nor is it waterproof. As time passes, in fact, a layer of paint becomes less and less waterproof.
Don't paint your bricks.
Spraying 3" of closed cell foam directly on to the punky fiberboard would add significant structure to the assembly, but that's not the right solution either. If any of the fiberboard has frayed/sloughed off and fallen to the bottom of the cavity the foundation sill might be suffering moisture damage that may need attending to before closing it all up.
If you can cut in T-bracing and really clean it all out for a good look, if there's a way to snake in 3/4" or 1" t&g XPS and get it to hang on the studs, leaving a 1.5" gap to the brick, and the flashing & brick ties all looked good etc, you could then put damp sprayed cellulose or open cell foam between the studs and have a pretty good rebuilt wall, but the details of how to get it all done reliably & cheaply aren't obvious in the abstract.
To figure out the right solution would probably require a site visit and even some disassembly for inspection to see what's really going on there. ( I'm not offering, just saying...) The short answer is that there is really no short answer, and what you've proposed is both expensive and potentially risky.
The ceramic paints and ceramic paint additives claims by vendors are all over the place, and some have been bitten-back by the FTC for excessive or fraudulent claims. Any time a building materials vendor claims it was invented/used by NASA, verify that your wallet is still there an keep on walking. (Unless of course you're house is in a high-vacuum high-radiation environment- say the surface of the moon, or something. :-) )
I wouldn't spray-foam the brick, and I wouldn't guess as to the function or necessity of the of the fiberboard, whatever it is--I'd ask a structural engineer to look at it and then decide what to do. You can usually install metal X bracing on the interior side of the wall.
The most effective insulation, assuming there's no competent backing in your wall cavities to blow insulation against, is probably going to be 3-1/2" rigid foam cut and fit into the stud bays, with aerosol foam around the edges to make everything airtight. If you want to go further, you can add more to the inside face of the wall, but it creates some hassles for electrical, drywall, trim, etc.
If you just fill the stud bays, you preserve that all-important air space behind the brick. It's important to recognize that these walls are currently able to dry to the inside, and any tightening you do is going to change that. It would be worth learning about what brick needs to perform well in your climate. Maybe Building Science Corporation has something on this on their site. It's also likely a good local mason could tell you.
In S.LA you could still get substantial drying toward the interior using open cell foam (rather than closed cell) in the stud bays. The long term air-tightness of a cut'n'cobble approach to rigid foam is always suspect. Open cell foam wouldn't add structure the way closed cell would, but it has an order of magnitude higher vapor permeance- enhancing the capacity to dry toward the interior, but putting the paper facer on the gypsum at a slightly higher risk of moisture issues if you insist on air-conditioning down to 70F all summer. Putting an inch of closed cell on the sheathing then filling the remainder with cellulose or open cell would be something of a balance- nore vapor tigth than all open-cell, but still allowing some drying toward the interior. (An alternate would be to use 3" of Icynene's MD-R-200 2lb foam, which is ~3x as vapor open as most closed cell foam, but nothing like open cell foam.)
But again, all the flashing & venting details, as well as how much crud has accumulated in the bottom of the cavity, and the condition of the brick ties should be assessed before following through on the insulating and refinishing.