Can I put fluffy insulation over rigid board which is on the interior of my walls?
I have a pole barn building with living space upstairs and a garage downstairs. The building is sided with bat and boards. The garage is insulated with rigid foam boards. Can I fill in the leaky spots with some spray foam and then add a layer of fluffy stuff over the rigid boards after framing the walls? I live in Delaware County, NY. It gets down to -20s and worse with highs in the single digits for periods of time (too long this winter). I would eventually like to make the garage living space. Thanks.
GBA Detail Library
A collection of one thousand construction details organized by climate and house part
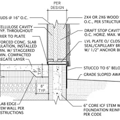
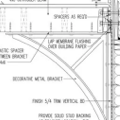
Replies
Retrofitting pole barns for insulation seems to be one of the more popular posts on GBA. I will give this one a bump to see what the professionals think.
GBA has an article on combining air permeable and rigid insulation (https://www.greenbuildingadvisor.com/articles/dept/musings/combining-exterior-rigid-foam-fluffy-insulation), but it presupposes that the rigid insulation will be on the outside of the foam. I'm not sure you can assemble the other way around, which is what I think you are suggesting.
User-7xx, can you give us your name? The software isn't showing it for some reason.
There are many ways to build pole barns so it's hard to give specific advice. In general, yes, you can fill any gaps with canned foam. If you have a lot of gaps, you might want to invest in a froth pack. It may or may not be safe to combine rigid and fluffy insulation--we would need more information (preferably a drawing) to better understand your situation.
Yes, thanks. I saw the article but wasn't sure it was applicable to me. I just want to use the foam to fill in the irregular corners and spaces that the boards don't fit nicely into. Then frame inside to add the fiberglass. The outside wall is just bat and board. I am under the impression that the rigid boards act as a vapor barrier. Is that correct or would I need something else between the boards and the fiberglass? Or even some other "sheathing between the boards and fiberglass to make it more like outside insulation? Thanks.
Sorry, my name is Michelle. I don't know how to put a drawing on here. Basically, right now it's wood pole post with some large boards going from pole to pole and bat and board on the outside.
The other option might be to take down the bats, using the boards for sheathing and putting the rigid on the outside, but that would require adding siding.
Michelle, I think you probably mean "board and batten" siding, which are vertical boards with narrow boards covering the gaps between wider boards. Or sometimes the battens go on first, called reverse board and batten. Or do you mean you have board siding with batt insulation? Edit to add: based on your response above it sounds like you have standard board and batten siding.
One typical way to build pole barns is with horizontal members screwed to the outside of round or square posts. The horizontal members are often 2x6s. Then siding is installed directly over that, with no plywood or osb in the assembly. Or sometimes full, conventional 2x4 or 2x6 walls with sheathing are installed between posts, called infill framing. Or the horizontal members, called girts or nailers, may be larger dimension poles framed between posts.
The reason it matters is because there are several things you need to protect against, and every situation is different. In order, you need to:
1. Keep rain out of the building. Siding helps but is never perfect, so there needs to be a secondary layer, called a WRB (weather resistive barrier)
2. Keep wind out of the building, with an airtight (or at least air resistant) layer somewhere in the assembly. The WRB can do an ok job with this, though it takes some effort with installation for it to do a good job.
3. Keep heat in (or out) of the building.
4. Control what happens to water vapor--in your climate, warm, moist indoor air wants to get outside when it's cold out, and deposits the water it holds on its way through. If you use air conditioning in the summer the opposite happens. In either case, that deposited water can lead to mold and rot.
Spray foam will help you with #3, but it may compromise one of the other layers. Wood siding needs to be able to dry out, insulation doesn't do well against water leaks, etc..
By "rigid boards" I assume you mean rigid foam? Rigid foam retards moisture movement; some types and thicknesses are a full vapor barrier, but many are more technically vapor retarders. The difference matters, because your wall and floor need to be able to dry in at least one direction, either toward the interior or exterior, and preferably in both directions.
I know the assembly is clear to you, but there are many other variables that make it hard to give you a specific answer. If you can supply a drawing or photo it would help a lot. When you post a response, below the box where you write it says "File attachments" in large green print. Before you hit "Post," just click on that word and you can link to an image you have stored on your computer or phone.
Yes, sorry. Board and batten. Horizontal 2x6s screwed to square poles. On a slab, which I was also hoping to insulate using rigid foam boards. Basically I want to make a livable space out of garage, without breaking the bank but keeping longer term heating costs down. (Don't we all.)
Maybe this is a post and beam structure. Not a pole barn.
It looks like what I would call a post frame building, but pole barn or post and beam also work. The term "post and beam" is a bit tricky because it can also mean a building with traditional timber frame joinery. But the photos tell enough of the story.
Michelle, the short answer is that with this type of assembly, the only approach I can safely recommend is to remove the battens from the exterior, wrap with a self-adhered WRB such as Henry Blueskin VP100, and install new siding. Your structural bracing against horizontal loads looks a bit weak, so you could add exterior CDX or Zip sheathing for added strength.
For insulation, you can either add exterior insulation of some sort--rigid foam or nailbase, which is rigid foam with osb adhered to one side, are the usual options, but semi-rigid mineral wool can also work well. And/or you can frame walls on the interior side and insulate with any of the usual options.
The approach you first suggested, spray-foaming the areas where you can see daylight and adding fluffy insulation directly to the interior of the boards, is not a good long-term solution, as it will be susceptible to moisture accumulation, leading to mold and rot, and is also may be at risk of pest damage.
Pole buildings are good for barns, but not so good for creating conditioned space in a safe, energy efficient manner. Not as bad as log homes, but close.
I should probably mention that this space is under the rest of my house and my intention is to upgrade the insulation upstairs next. So maybe the rigid foam boards (zip system maybe?)should go outside to keep everything even? New siding is on the list, it could be moved up. Thanks again.
Michelle, that could be a good approach. You're in climate zone 6A, so your walls should have at least R-22 total insulating value, including the value of lumber in the wall. In other words, meeting the 2015 IRC requirement of U ≤ 0.045 for walls.
All things considered, the simplest approach for your situation would be to wrap the building with nailbase or structural insulated panels. (OSB with foam adhered to one or both sides, respectively.) Then you can leave everything on the interior exposed, and the framing will be warm and dry. 6" EPS panels or 4" poyiso panels would cover your insulation needs, though additional insulation is often worth the cost.
If you want to use a mix of interior and exterior insulation, at least 34% of your R-value needs to be on the exterior for condensation control in your climate zone. Zip-R12 insulation (totaling 2 1/2" thick) on the exterior with 2x4 framing at the interior, with R-13 cavity insulation, would meet all requirements.
Your unconventional framing system means that you won't be able to meet Huber's installation requirements, though, so you should add vertical studs at the interior, to have something to nail to, and to have bays to insulate, install electrical boxes, hang drywall, etc.
One other idea; instead of Zip-R sheathing, you could add diagonal metal bracing to the exterior, wrap it in Blueskin (or similar), install rigid foam (min. 2" polyiso would be my first choice if you're on a budget, or Rockwool Comfortboard if you want to be more environmentally conscious), strap vertically to create a rainscreen, and install horizontal siding. With 2x6 framing cavities on the interior filled with cellulose or other fibrous insulation.
Ok, I was kind of thinking that direction initially, then wondered if there was a shorter route. I will go the wayof you have suggested, thanks a bunch. I think I can stop obsessing now and get a decent night's sleep. Thanks again.
Ok, I was kind of thinking that direction initially, then wondered if there was a shorter route. I will go the wayof you have suggested, thanks a bunch. I think I can stop obsessing now and get a decent night's sleep. Thanks again.