Can I build an old-fashioned vented crawl space with modern Lstiburek reccomendations?

Joe Lstiburek, the respected building scientist with Building Science Corporation, provides an approach to building vented crawlspaces in energy efficient houses. http://www.buildingscience.com/documents/insights/bsi-009-new-light-in-crawlspaces/?searchterm=crawlspace
Basically he is saying that the crawlspace needs to be isolated from the house (thermally and hygroscopically). He recommends insulating the floor framing thermally, and also isolating it from the outside air with a vapor barrier on the outside of the insulation..(facing down into the crawlspace. This addresses problems like condensation of humid summer air on cold floor framing. My question is : how does this address condensation of indoor air on the warm side of this vapor barrier in winter?
GBA Detail Library
A collection of one thousand construction details organized by climate and house part
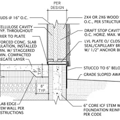
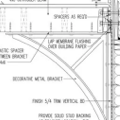
Replies
Michael,
Condensation occurs on cold surfaces. If you install polyisocyanurate foam of adequate thickness on the bottom of the floor joists, the foam surface facing the joist bays will be warm, not cold — so no condensation will occur. The polyiso performs just like foam sheathing on a wall.
Remember, plywood subflooring is a pretty good vapor retarder and air barrier, so you won't get much moisture traveling downward.
Martin,
Thanks for the quick answer! In this case we do not want to use any foam....so the thought is to use Knauf board insulation, with a plastic film on the bottom (crawl space side) so the upper surface would be porous ...and might allow humidity to travel to the cold film, where it could conceivably condense.
The floor sheathing is planned to be OSB, , less permeable than plywood..... This is a near passive house building, the floor will be airtight, and the air quite dry...unless someone decides to use a humidifier in winter....I could put a vapor barrier above the insulation board....: (
Michael,
Polyiso is a much better product for this application than porous fiber insulation. I'm sure you have your own reasons to avoid foam, but in my own home I wouldn't compromise performance just to conform to a rigid rule.
To be clear, Lstiburek doesn't advocate vented crawlspaces, he just states that with the right thermal and hygric isolation of the floor framing a vented crawlspace might not be problematic.
I avoid petrochemical foams everywhere I can, but just as in subgrade applications foam board is the only insulation that works, also in this application high-R and vapor impermeable foam board or closed-cell spray foam are the only workable options. Otherwise, seal and condition the crawl space.
Martin and Robert,
You have confirmed the nagging concern that i had about using fiberglass insulation board for this application.
By going back and looking at my cold Climate book, I understand now that impermeable board insulation means impermeable as a unit, not just on one face. The project involves modular boxes on a crawl space with 12" Dense pack cellulose walls , 18" deep atic cellulose .triple glazing...HRV... It's based on Passive house principles so I want to avoid including the crawl space in the heat load.
Humour me for a moment and Imagine that petrochemical foam is not an option....What about using a fiberglass board with integral vapor barrier on one face (the lower face) and some kind of vapor barrier above it....(below the floor framing and fiberglass insulation) how would this perform differently from an impermeable rigid foam board in the same position?
Can you explain what would be different ? thanks for your patient input..
Why do you feel that high-embodied energy fiberglass that is a known carcinogen and often uses formaldehyde binders (which are a primary trigger for multiple chemical sensitivity) is a better option than petrochemical foam? Neither are green products and both have significant ecological and human health impacts.
Radiantly decoupling the floor framing from the ground is as important as thermally decoupling it. The best option is foil-faced polyisocyanurate rigid board.
When you're faced with a devil's choice, you may as well use the most effective devil.
Robert, I hear you. It is clear that a foil faced impermeable foam board is the practical and time proven approach, even if "it requires tiny people with good workmanship to tape the seams...",
This building is for a client who has an extremely strong preference for non foam materials, and that's why I am looking for an alternative. Foil faced fiberglass board without formaldehyde is made by Knauf and JM, which makes it a possible candidate, but theoretically it is clear that its porosity on the upper face could be a problem in winter...
It seems that I could try one of two things: reduce the permeability of the floor OSB with a low perm paint, or somehow create a vapor barrier just above the fiberglass board. This latter seems to be the better solution because that way there is still a path out for any water vapor that might find its way into the floor.. Is that sound thinking , in your opinion?
Michael,
You still haven't explained why this client rejects foam and prefers fiberglass. You might start by educating him/her on the significant liabilities of both products.
I am a strong advocate of avoidance of synthetic materials but I seen no environmental or health advantage of fiberglass over foam board.
Michael, why the vented crawlspace?
The client would prefer to use a more natural material.(the roof and four walls are insulated with cellulose) but I haven't found a way to insulate a floor cavity over a crawl space with more natural materials. (and also restrict heat loss per passivhaus standards)
The building is part of a Meditation Retreat Center and is designed according to two disciplines: Maharishi Sthapatya Ved and Passivhaus . MSV is the revival of the ancient science of building in accord with Nature from the Vedic Civilisation of India. It deals primarily with orientation, placement and proportion, but also includes recommendations for materials. In general these are natural materials and non toxic materials. Foam materials are felt to have an effect that is the opposite of life supporting, and avoided except in very limited quantities. Having the main floor insulated from the earth with foam is not a possibility in this approach. Fiberglass without formaldehyde is an acceptable , though not ideal material. Cotton insulation is OK.
Isolating the crawl space this way makes it a vented crawl space vs a conditioned crawl space.
oops something didnt come through...
James:
The building is designed to be very efficient , following Passive house standards as much as possible.
It is designed with modular factory built boxes, stacked two high. such boxes are normally placed over a basement or a crawl space (not a slab). If the basement or crawl space is conditioned , it will add a lot of wall space to the heat load calculation and require extra Ventilation equipment. . It seems simpler and more efficient to isolate the bottom box from the crawl space with a insulated floor cavity, (9 1/4" Knauf formaldehyde free batt insulation, below which is added a 2" Knauf insulation board with integral vapor barrier facing down) That was the plan until I realized that this might be a problem in Winter , if vapor from the building condensed on the upper surface of the said integral vapor barrier. I want to avoid a foam board....
Michael,
Thanks for the explanation. I built a superinsulated floor deck for a timber frame straw bale building at the Center for Whole Communities, as part of the Yestermorrow Natural Building Intensive.
The floor framing was rough-sawn full-dimension 2x12 raised 8" above grade on a concrete grade beam over a rubble-trench foundation. The floor was cantilevered 18" beyond the foundation and timber frame to support the exterior straw bales. Dry-laid stone was filled in under the cantilever.
RS 1x4 ledgers were attached under the joists, upon which were laid short lengths of RS pine perpendicular to the joists to support the blown cellulose insulation. Filter fabric was laid in strips between the joists over the board shelf to contain the cellulose as the boards shrink and to keep insects out (though the boric acid fire retardant is a natural insecticide). I also wrapped filter fabric around the outer edge of the floor deck and then installed the upper half of the band joist (RS 2x6) so that the RS decking could be put down and the straw bale walls built.
The cellulose was blown in through slits in the filter fabric below the half band joist, with the hose inserted to the center blocking and withdrawn as the cellulose reached density, and then the lower half of the band was installed.
Because the floor decking was to be RS boards, I installed a layer of Typer housewrap over the joists to prevent water from penetrating through the decking. If you're using T&G plywood subfloor, this wouldn't be necessary (perhaps they Vedics don't use plastic).
The 8" crawl space was vented and the ground was well drained by the perimeter drains in the bottom of the 5' deep rubble trench.
Perhaps some variation of this approach might work for your project.
Sorry Robert, the idea of an 8" deep inaccessible vented cavity below an inhabited space makes my head hurt. I just hope that if Michael follows through with this plan he at least makes the crawl space tall enough for maintenance access.
Michael, insulating the floor deck may 'seem' simpler but if you have any plumbing, electrical or mechanical penetrations through that floor deck simplicity goes out the window, in addition to the potential for interstitial condensation problems which you have already identified. Also a floor deck of say 40 x 28 would have 1120 sf of area to insulate versus 408 sf for a perimeter foundation wall 3' high. I understand it is probably difficult to reconcile the uninsulated base grade of a sealed crawlspace with Passivhaus theory and practice but a vented crawlspace is probably not the answer either.
You also may ultimately need to consider that in seeking to fully integrate Vedic and PH practices in this single project you may end up with deeply compromised results on both counts. Just a thought.
That's why we wear helmets when we go caving. We crawl through 8" spaces routinely. Sometimes vertically downward head first.
Robert, I like it! Just regard that 8" crawl space as a recreational resource, a kind of horizontal climbing wall, and it's not a bug, it's feature! We're kind of short of enthusiastic spelunkers among our maintenance crews down our way, but perhaps we should promote the tiny, muddy, moldy subfloor spaces of our old local mill houses as a tourist thing...
Michael, you don't mention the specific purpose of the structure you're working on. You say it's part of a meditation center, if that means it's not in full-time residential use with showers, cooking etc. going on all the time your vapor condensation issues may not be so significant. Robert has posted persuasively elsewhere on this site about the value of vapor capacitance in cellulose insulation, which could even out your vapor loads in a lightly-loaded building. I'm not sure in that scenario if the vapor barrier is still desirable? Again, Robert has posted thoughtfully about air-sealed, vapor open wall construction, and what you're proposing here is rather like a horizontal wall.
You also don't mention the location of your project. Vented crawl spaces have been such a general disaster here in the South that I find it hard to think of them in a high performance building, but your climate may be more forgiving. Further thought: if you're determined to have air flow below the building what about doing it properly, with open pier construction? Lighter impact on the land and on adjacent vegetation root systems, lower cost to boot.
Robert Riversong said:
Coming soon to North America - foam glass gravel. I think it's going to make below grade foam obsolete. Low thermal conductivity, relatively good compressive strength, and material cost will be less than the equivalent foam board and traditional gravel aggregate it displaces. Oh, and it's usually made of recycled glass at local/regional factories.
A kind of eco-tourism? Visit the local rain forest environment? Save on jet fuel?
Exactly. Even with health benefits: develop resistance to mold-born ailments by controlled exposure.
Thanks for all you input. I will provide more responses soon.
It occurred to me that no discussion of summer condensation in a crawl space is serious
without climate data. The site is located in Northern West Virginia, in climatic Zone 5 (cold). it has about 5800 HDD, and please see summer Dry bulb and wet bulb hourly/daily/weekly graphs at the following link.
here's the link...
http://picasaweb.google.com/chelnovm/TemperatureDryBulbAndWetBulb?authkey=Gv1sRgCJuqwODNqYrTzQE#5450345221267046482
This will be more legible....I'm not a pro at this...
http://picasaweb.google.com/chelnovm/TemperatureDryAndWetBulbDewPoint?authkey=Gv1sRgCOS1lejTgK3nTQ#
PS you can drag it to see the whole