Calling on the pros – still searching for an answer to a vapor transmission question

Please see Oct 1st thread:
” Are there more cost effective ways to dry an old basement”
I have updated the question from March of this year and it begins at post #5.
I am trying to find out if my assembly when fully complete will have any problems with the wall drying inwards due to the elements I propose. Sorry to have started a new thread but my “bump” did not elicit any replies so I thought I would try a work around.
Any feedback and observations are appreciated.
GBA Detail Library
A collection of one thousand construction details organized by climate and house part
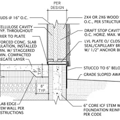
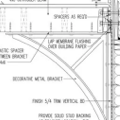
Replies
GBA readers:
Here is the link to the old Q&A thread that John Scanlan is talking about:
"Are there more cost-effective ways to dry an old basement?"
GBA readers:
The information is buried, but it seems as if John Scanlan's house is in Climate Zone 5.
To All,
Reposting the pertinent details of previous post Martin mentions, I hope it makes it somewhat clear and easier follow:
Revisiting a design to drain, air seal, insulate the first floor and basement of a 1901 two story house in Rochester Ny, climate zone 5. Since the last posting I installed an interior drain tile instead of my proposed drainage plane on the basement floor. Attached is a drawing of proposed design. I also have a few questions if possible:
1.) The final design will have an a future exterior foam installed with thickness TBD ( 1.5"-2"?) but at this time there is no exterior foam insulation other than 3/8" foil faced foam under vinyl siding.
2.) Can fiberglass or cellulose insulation be used in the first floor service wall cavity. In the basement interior wall also?? If the insulation is able to be used in the service cavity of the first floor, what thickness should the exterior foam insulation be?
3.) The purpose of the 3/4" OSB adjacent to drywall interior drywall is for wall mounting heavy artwork. Will it adversely affect the drying properties of the wall.
If anyone could review and comment on the design I would appreciate it.
User avatar GBA Editor
Martin Holladay | Sep 28, 2018 04:47am | #6
John,
There are several oddities about your wall assembly. For example, the wall has sheathing in three places -- exterior board sheathing, and OSB between the two rows of 2x4s, and then interior OSB as well.
The wall also has three layers of rigid foam -- EPS on the exterior, and then EPS as a cut-and-cobble layer, and then EPS in the middle of the wall. Phew! That's confusing.
Any chance you could simplify things?
John Scanlan | Sep 28, 2018 10:45pm | #7
Martin,
Thank you for the reply. All layers that I propose I think will provide benefits but would like your professional opinion on the proposed stack up especially in regards correct vapor transmission qualities once you know my reasoning. If I need to alter the design in order for it to perform better I am more than willing to do so. Answer to your questions are as follows.:
My house was built in 1901 and the air coming through the walls was quite a high volume even after newly installed windows that were flashed/ air sealed correctly. The 1" EPS cut and cobble insulation layer was to stop this outside air from entering the stud cavity at the outermost point. A 1" furring strip was added to the stud face to keep from compressing the R-15 batt from the additional 1" pf cut and cobble EPS withinin the stud cavity.
The taped layer of 7/16" OSB on the inside of the exterior wall framing is to act as continuous primary air barrier as well stiffening the creaky house walls of the old loosely nailed T and G 1" x 6" exterior sheathing. The 1" EPS layer on top of the 7/16" OSB air barrier/ wall framing stiffener is to act as a thermal break until I get the external foam installed in the future. I used eps in all rigid foam on the interior because of its vapor permiability. The interior most layer of 3/4" OSB on the service cavity is inside of gypsum is only for structural backing inside the wall to hold heavy wall art. The interior 2 X 4 service cavity wall is to allow for all services as well as deep splayed window jambs as well as giving me a flat plane in front of a very wavy and out of plumb existing exterior walls.
I am really trying to make sure that my proposed stack up does not alter/ degrade the vapor transmission qualities of the "vapor smart" layer of 7/16" OSB that acts as an air barrier/ wall framing stiffener. I understand that due to the existing 3/8" foil faced insulation below the vinyl on the exterior makes this wall an inward drying wall. I would like to keep the 3/4" OSB layer in the wall for the utility purposes stated but want to make sure it does not harm the stack up.
The XPS blue board rigid foam acting as a drain plane against the basement stone foundation is 2.5" thick. Is it advisable or of value to insulate with fiberglass the 2 x 4 wall in front this XPS in the basement prior to covering it with gypsum?
I plan on living in the house for the next 20 years and had the time, inclination to perform a deep energy retrofit while I am still physically able. Hopefully I have addressed your questions and I appreciate any and all feedback from anyone interested in any aspect of the design.
Thanks,
John
Martin Holladay | Sep 29, 2018 04:38am | #8
John,
It's hard to tell from your description how much of this plan has already been implemented, and how much is simply a plan drawn on paper.
In general, the most robust wall system will have a very thick layer of exterior rigid foam, with an optional layer of fluffy insulation between the studs. I don't know if you can follow such a conventional approach with your building. For more information, see "How to Design a Wall."
John Scanlan | Sep 29, 2018 10:27pm | #9
Martin,
The first floor wall is complete except for the installation of the 1.)service wall insulation, be it fiberglass or cellulose, 2.) the 3/4" OSB below the gypsum and 3.) the gypsum.
The exterior layer of thick rigid foam you speak of is NOT yet installed but hopefully will be in the forseeable future.
The basement foundation section is complete except for the addition of fluffy stuff ( fiberglass or cellulose) in the stud cavity and drywall to fire protect the XPS. The 2 1/2" rigid floor insulation is a future addition and has NOT yet been installed.
Do you see a problem in the first floor wall stack up in regards to drying inward correctly if I add the either fiberglass or cellulose insulation to the service cavity followed by the 3/4" OSB layer for wall hangings and gyp? I do not want compromise the wall drying inwardly with the 3/4" OSB layer. If it is felt that it might hinder the assembly drying correctly I could install wood blocking though it is much more work.
Do you see a problem in foundation wall stack up. I used 2 1/2 " blue XPS instead of sprayed closed cell foam due to the cost. It is foam sealed at all edges with foam taped seams. Can I safely install R- 15 fiberglass in the cavity against the XPS prior to gypsum insulation?
I have previously read the " how to build a wall" and just rescanned it tonight and think I have it correct but am looking to have someone check to see, if in their opinion, the wall is going to perform correctly especially in terms of vapor transmission and wall health, and function as I described in my intro and clarification posts as to why I added the elements that I have within the wall. Hopefully this info helps but If you need anymore clarifications I am at your service. I appreciate all of your input.
Thanks,
John
John,
I'm looking for a question, and I think I found one.
Q. "Do you see a problem in the first floor wall stack up in regards to drying inward correctly if I add the either fiberglass or cellulose insulation to the service cavity followed by the 3/4 inch OSB layer for wall hangings and gyp?"
A. The fact that you have two layers of OSB in this wall -- one in the center, and one on the interior -- certainly slows down inward drying. However, since you have foil-faced exterior foam, I don't think you have to worry much about inward solar vapor drive and inward drying during the summer.
The biggest problem with this stack-up is that you have installed an exterior (cold-in-winter) vapor barrier, without providing enough R-value in the exterior rigid foam layer for your climate zone. To learn the rules for walls with exterior rigid foam, see "Calculating the Minimum Thickness of Rigid Foam Sheathing."
Fan-fold 3/8" EPS & XPS with perforations is available (and recommended), which raises the average vapor permeance to the Class-III vapor retardency level. (The paint on the old siding is probably more vapor retardent than perforated fan-fold.) Since the fan-fold is not going onto a uniform smooth surface on either side the perforations would be even more effective than when applied to smooth sheathing.
The half-inch OSB in the middle is a "smart" vapor retarder- it'll still be able to dry toward the interior if it needs to (even if using UN-perforated double foil faced EPS fan-fold.) With beveled siding on the interior side of the fan fold it's unlikely to be very air tight even with some effort applied toward that end. As long as the middle OSB is detailed as an air barrier it should be fairly robust, even with <1.0 perm fan fold, but more vapor open is still preferred.
Martin,
Understood about the lack of exterior rigid insulation but that should be corrected in the future with the installation of foam board.
Q. How about using dense pack cellulose in the first floor service cavity wall, no difference than fiberglass in terms of correct drying.
Q. How about the use of fiberglass in the basement wall prior to drywall?
Q. Do you see any other problems in any of the wall or basement details.
Thanks again for the help, your blog is invaluable!!
John
In the basement the bottom plate of the studwall being below the level of the floor foam will make the wood colder/wetter, almost equivalent to burying it, especially if you then intstall fiberglass batts in the stud bays.
Since the studwall isn't structural, it doesn't have to rest on concrete. Both the floor foam and the subfloor should extend all the way to the wall foam, in which case it would be fine to use fiberglass in the stud bays. That way you can skip the vertical nailer board too, since the gypsum can be fastened to the bottom plate directly.
There's no need to go with environmentally UN-friendly XPS here- EPS would be fine for both the floor & wall. Polyiso would be fine for the wall, as long as the bottom edge doesn't rest on the slab. Running the floor EPS all the way the foundation so that the cut edge of the wall foam rests on EPS, not concrete would be the way to go.
Dense pack cellulose is OK to use it the service cavity. If cellulose it's better to use sulfate free goods rather than cellulose with ammonium sulfate fire retarder, since the latter can corrode copper (wiring & pipe) pretty quickly if it ever gets wet. (Borate fire retarders are fine.) Damp sprayed fiberglass such as JM Spider would be fine too, and wouldn't have the fire retarder issue.
Dana,
Thanks for your feedback.
Concerning the bottom plate detail of the basement staying wet as drawn, I understand your concern. I have lowered the first floor framing members 8” within the stone foundation to increase first floor ceiling heights so the new wood framed basement walls are load bearing.
Q. Could you offer a detail appropriate to allow a bearing wall on blue XPS 2.5" ( 30 psi??) and 3/4"OSB to achieve your the wall foam to floor foam detail. I am trying not to pour another layer of concrete on top of foam for cost as well as maximizing the shrinking headroom in the basement due to the lowered floor. I have purchased reclaimed 2.5” XPS material at a reasonable price so I have been utilizing it for the basement walls and floors while all other rigid foam is new EPS. Sulfate free cellulose purchase advice noted.
Thanks again for your valuable input,
John
There is no generic detail for foam under a load-bearing wall- the load matters. A certified professional engineer needs to run the numbers to make the specification and sign off on it.
John,
Q. "How about using dense-packed cellulose in the first floor service cavity wall? No difference compared to fiberglass in terms of correct drying?"
A. There are at least two types of fiberglass insulation: fiberglass batts and blown-in fiberglass. In order of preference, from the best to the worst, I would list your options this way:
1. Dense-packed cellulose.
2. Dense-packed blown-in fiberglass.
3. Blown-in fiberglass that isn't dense-packed.
4. Perfectly installed fiberglass batts.
5. Fiberglass batts installed the way most builders install them.
For more information, see "Installing Fiberglass Right."
When choosing between these options, the drying rate isn't the most important issue. All of these types of insulation allow drying at a rate that is fast enough to avoid problems (assuming that your wall is otherwise properly designed). The main advantages of dense-packed cellulose are (a) it fills every nook and cranny of your stud bays, and (b) it reduces air leakage compared to the other options.
Dense packed fiberglass is at least as air-retardent as dense packed cellulose. (Low density fiberglass isn't as air retardent as low-density cellulose though.) Dense packed fiberglass has a somewhat higher R-value than cellulose, but when thermally bridged by framing the actual whole-wall performance difference is negligible.
Fiberglass will dry much faster than cellulose, but cellulose will share the moisture burden with the structural wood, wicking & storing far more moisture (without damage or loss of insulating function) than fiberglass can, which is protective of the structural wood.
Thank you Martin and Dana for your observations, all are sound and I will follow your guidance. GBA's Q & A section is the best thing around.
Thanks Again.
John