Building envelope for small winery/cidery in southern Quebec

ShaunQC
| Posted in General Questions on
Hi there,
I’ve found a lot of help and wisdom through the sites’ articles and discussions, so here’s my first question.
I’m building a small winery/cidery in southern Quebec (south of Magog, zone 6), about 900 sq ft. I’m in the design phase right now with an architect and we’re discussing the building envelope. At the moment, the structure is wood framed 2×6 with a shed roof. It’ll be on a slab.
Now, the ideal interior environment for wine barrels in the cellar is 10C-15C and 55%-65% Relative Humidity. So we’re trying to design the envelope so the building is not at risk of any moisture issues with this higher humidity environment. The interior cellar has to have washable plastic panelling—no manufacturers have done perm testing on this product but they say to install a vapour barrier behind it so I’m treating it as pretty vapour permeable. We’ll use a heat pump to heat and cool when necessary, but we want to do as much passively as possible. There will be building exhaust.
I’ve taken inspiration from many of the discussions here as well as this Building Science article on wine cellars that argues for slight vapour drying in both directions.
Our first thought was:
Exterior to Interior
Cedar siding
3/4” rainscreen vent
3” ISOCLAD EPS (R12.1)
plywood/OSB
2×6 mineral wool insulation (R-23)
Intello Plus barrier
Washable plastic wall cladding
However, someone ran a WUFI analysis on this and the EPS caused moisture issues. Switching to rigid exterior mineral wool solved those issues. I’ve attached the analysis.
I imagine it could be similar for the roof, which will probably be unvented (R23 Rockwool on the interior and R24 EPS/Rockwool on the exterior).
So, using the upper limit of the interior environment of 15C and 65% RH, what would the best building envelope be? What else would make this building efficient and resilient?
Please feel free to ask any questions if you need more details.
Many thanks to the community.
Shaun
GBA Detail Library
A collection of one thousand construction details organized by climate and house part
Search and download construction details
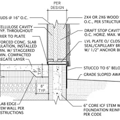
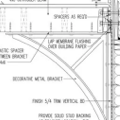
Replies
Hello ShaunQc,
I would go to the most reliable source possible and that is the Building Science Corp. The founder has worked in Canada and from another article he has lived in climates with snowy winter. BSC is located in Westford, MA.
This article provides a specific recommendation for wine cellar walls and compares that assembly to the walls recommended for saunas. You just need to be patient and read through the lengthy piece of context provided.
https://www.buildingscience.com/documents/insights/bsi-010-wine-cellars
There are lots of other suggestions online but you will see BSC and it’s founder/expert staff being quoted over and over on the GBA site.
Hope this helps.
Sean,
I agree with using the demands of a wine cellar are a good starting point - with one caveat. The reasoning behind the ability to dry to both sides is that while (much like your winery) there will be a constant low temperature which may cause moisture concerns on alternating sides of the building assemblies depending on the seasons, the assumption is you will have permeable interior finishes, which you will not.
My suggestion would be to move the continuous foam to the interior, and make the exterior much more permeable. That way you have sufficient interior R value to keep the exterior face of the foam above the dew point when the outside temperatures are high, and the assembly can readily dry to the outside during the heating season.
I would treat the interior plastic surface as being a vapour-barrier, and not assume any drying to the inside. Given that I don't see any advantage to using Intello-plus over poly.
Have a lot of good memories of Lake Magog and the surrounding area. Good luck with your project.
Appreciate the replies.
Malcolm, thanks for your thoughts. Interesting idea to flip the wall assembly around. Doing this, would you still need to abide by the R11.25 minimum that you would for exterior application? Or could you drop down to 2" of EPS? Or maybe 1.5" of polyiso?
So the wall assembly would be:
Exterior to Interior:
Cedar siding
3/4” rainscreen vent
plywood/OSB
2×6 mineral wool insulation (R-23)
Poly
3” ISOCLAD EPS (R12.1)
Washable plastic wall cladding
And how would it work for the roof? Would you put 6" of EPS on the interior and then 6" of rockwool in the rafter bays?
Would a vented roof be less risky in this situation?
It's a nice spot in the world out here.
Shaun
Sean,
The idea is to make sure the rigid insulation is thick enough so that there are no dew point concerns no matter whether the interior is warmer or colder than the outside. I'm sorry, I don't know what amount of foam is necessary to do that.
I suspect the roof should be much like the walls, where you want that same layer of interior foam, and after that can have fluffy insulation and a vent channel above, but I'm not overly confident that's the best solution. Hopefully other posters will chime in on those two issues.
If you look at the wall/roof sections in the link I provide, you will see that BSC does in fact recommended to have the same assembly on the ceiling. Since your ceiling is a roof you would add more rigid insulation.
BSC recommends leaving the exterior walls empty, which makes the wall assembly the exact opposite/flip of their “perfect wall”. You can read about their perfect wall online.
Adding insulation in the cavity is not necessary according to BSC but they don’t usually have an issue with the additional insulation with the perfect wall.
The advice revived here is the same basically as offered by BSC, except BSC also adds a furring strip between the interior finish and the rigid insulation. That again is the same idea as an exterior rain screen. That would seem to me to be appropriate given that you intend to hose down your interior walls.
Not sure how you could ultimately get away without a vapour barrier in QC but I have not read their code on vapour retarder requirements.
If it were me i would consult with manufacturers to see if could simply be built either
- like a walk-in cooler.
Or
- cold storages warehouse
https://www.coolmaster.ca/cold-storage-warehouse/
These manufacturers offer full service consulting, not just the product.
Not sure why their product could not deal with higher humidity but the manufacturers could tell you.
Thanks for the responses Malcolm and Hugh(?),
Seems the cold storage warehouses use steel structures and commercial panels (foam sandwiched between metal siding). We discussed this but ultimately decided not to do it based on costs and aesthetics (as long as we can build a resilient wood structure).
Starting to get a clearer idea of how the interior environment can be sealed from the rest of the structure using foam and a vapour barrier (poly) and using mechanicals to manage the temperature and humidity. (I've been reading BSC and elsewhere on indoor pools.)
Do you think 6-mil poly is enough? Some people recommended getting the heaviest poly you can find and not stapling it--rather using "hand-applied roofing nails" according to one source.
And would you put the poly interior or exterior to the foam?
From interior to exterior:
Plastic panels
EPS foam
Poly
OR
Plastic Panels
Poly
EPS foam
I'll have to talk to our architect about venting the roof as our original idea was to have an unvented assembly.
Now just to figure out how much foam on the interior to control the dew point, as you suggest, Malcolm. Maybe others will chime in.
Cheers.
With any reasonable thickness of rigid on the interior, you won't need a poly layer. In case your building department insists on it, most foam data sheets will show permeability which will bellow the 60 ng/ (Pa∙s∙m 2 ) required by code.
The more foam you install the lower the chance that the condensing plane will be inside the stud cavity. Even if you do get some condensation in the cavity, as long as you build the exterior as vapor permeable (ie use gypsum / fiberboard / CDX sheathing) you can get a lot of drying through the siding.
For your roof, I would use similar idea (interior rigid under rafters, batts in rafters), so this does mean a vented assembly. The only way I can see a safe unvented assembly in this case is if you go with all closed cell spray foam for your roof.
This is a good tool if you want to play with your wall/roof stack up. Use the coldest 3 month average outdoor temperature as the design outdoor temperature.
https://www.ubakus.com/en/r-value-calculator/?
There is a device called a CoolBot that allows you to use a regular window air conditioner to make your own walk-in cooler. I'm not sure that the CoolBot is the right device for your application, but I think looking at what other people have done with them will give you an idea of what kind of construction you need to build a climate-controlled room inside of a climate-controlled building, with the two climates different. They've sold tens of thousands of them and if you do a google search you can see blogs and videos where people show what they've made.
DC makes a good point that also begs the question: Is your barrel storage facility treated differently than your production floor? And, is the production space allowed to vary in temperature and humidity seasonally? If so, then the demising wall also needs to be properly designed, though the design is not too difficult.
If we look at a psychrometric chart for your conditions, the dewpoint of the interior air at 10-15C and 55-60% RH is in the same range as more common interior conditions of 18-20C and 35% RH. So, in fact, you could use a similar wall system to the typical wood-framed wall systems in your climate and you would be safe in winter. However, we typically focus on the cold range of your climate and neglect to look at the warm range in summer. With constant 10C inside the barrel cellar, we need to be concerned about condensation inside the wall in summer. With summer outside dewpoint temperatures well above 10C, we need to either stop that humidity from reaching any interior condensing surfaces (with a vapor barrier), or eliminate condensing surfaces entirely by making the wall vapor-open until the backside of your washable plastic, then allowing the condensed moisture to drip to the floor for collection. You could do this by using untreated plywood/OSB for your sheathing, as both are somewhat of a "smart" vapor retarder (plywood is a bit better), fluffy insulation in the wall cavities and then Intello on the studs behind EPS (vapor-open) insulation, then strapping and your washable plastic. The Intello should be detailed as your air barrier, though detailing the outside surface of your sheathing as an air barrier would also work. Doing both is always safer.
But you might get similar performance and save a bit of space and installation costs by replacing all of the layers inside of the studs with Dow's Thermax Ag Board. This is polyiso insulation with rugged aluminum facers on both sides. It is intended for use inside ag buildings (think milking parlors), with powerwashing of the surface on a regular basis. It would certainly be tough enough for your needs. The aluminum facers make the entire panel a self-contained air/water/vapor/thermal control layer. 2" of this would prevent condensation on any of your wall surfaces in any conditions. It is a bit pricey, but it works. I would bump up your stud size to 2x6 to get a bit more overall insulation value at relatively low cost. Have your WUFI guy take a look at this approach, it might work for you.
The demising wall inside (if you have one) should also be insulated, but as I mentioned above, this is easier. With the inside conditions described above, you never have condensing conditions on either side of the demising wall, so vapor control is much less important. Here I would probably just use a layer of OSB on the warmer side, fill the stud cavity with fiberglass and call it a day. If your production space is allowed to go to outside conditions in summer (no A/C or humidity control), then you need to do something like the exterior wall described above. Here, a 1" layer of Ag Board on the interior, no VR on the production side of the wall and no FG in the cavities would work fine. You could either make the ag board thicker or add FG in the wall cavities to safely decrease heat transfer through the wall if you want.
Hi All,
Thanks for the suggestions. Ubakus is an addictive program. Having spent far too many hours playing around with different wall assemblies I have more questions.
So, no matter what there will be a vapour barrier on the interior. As others have noted and further research has revealed, the PVC plastic cladding will be pretty impermeable.
I was playing with two options: Moving the rigid EPS to the interior as many have suggested or simply using poly 6 mil. From a building point of view--and correct me if I'm wrong--having the the EPS on the interior will mean a larger foundation to get the same floor space and will also mean putting up gyprock between the PVC cladding and the foam for fire barrier purposes. On the other hand, I could tape the EPS and not bother with poly.
The second option is to keep the rigid insulation on the exterior but use mineral wool to keep things permeable and put up poly on the studs behind the PVC cladding. Smaller foundation, more work putting up poly but no drywall.
And my third scenario that I've been musing about is a double stud wall, say 10.5" of mineral wool batts with poly on the interior behind the PVC. I know there can be moisture issues on the sheathing with double studs so wondering if it would be too risky given my higher interior humidity. (And would dense packed cellulose be asking for too much moisture in this situation or would it dry fine?) This would also require a larger foundation.
I've included the three Ubakus wall assemblies. They all seem to work find--the risky spot is the interior surface temp/RH which gets above 70% RH sometimes. This can be mitigated by bringing the interior RH down to 60% for the winter--and I'm not worried about mould growing on the PVC.
(As you'll see, in the interior rigid foam assembly I have a layer of Poly--I couldn't figure out the German for foil faced EPS so put this in to more accurately reflect the perms rating of ISOFOIL EPS.)
Any thoughts are most welcome.
Cheers.
Shaun
Shawn,
All your wall assemblies look like they would perform well during the heating season. My worry is that in the summer, when the interior might be a lot colder than outside, you end up with a wrong-side vapour-barrier where moisture may condense. Coping with that possibility is why the interior foam was suggested. It keeps the outside face of the foam above the dew point.
Peter, sorry, I didn't see your response for some reason before I posted. Thanks very much for the detailed thoughts.
We aren't separating the barrel room/production space/warehouse. We'll keep all at the same temperature and humidity (using a air-source heat pump and whatever humidity controls we need).
Yes, being in Quebec I was focussing on the winter but as you and Malcolm pointed out, summer is also an issue.
Dow's Thermax Ag Board sounds interesting, though the only Ag Board I found was XPS. Do you have reference to the polyiso? And I'm not sure if it would meet food-safe criteria and therefore I'd still need the PVC cladding (though if they use it in milking parlours maybe).
I was playing around in Ubakus and putting a 1/2" air vent behind the PVC cladding seemed to help bring down the condensate and drying time in all scenarios--to what seems like very little moisture and a quick drying time, which might be enough, and I could use that 1/2" to run wiring as well.
But with 3" of interior EPS it eliminated both entirely using a three month summer average of 20C and 80%RH. Maybe 2" of foil-faced Polyiso would also work (I just can't find the option in Ubakus).
I know no moisture is better than none--better to be safer than walking the edge--but would the 2" of interior or exterior foam with a vent work? Or am I asking for trouble?
And am I making any mistakes or assumptions in these calculations/thinking? (I'm just leaping in to this building science rabbit hole.)
Many thanks to all.
Shaun,
The product I was thinking about is the Thermax White Board. It has a polyiso core and embossed white aluminum facers. Joints are covered with a plastic molding. The product can be pressure washed up to 1000 psi. I don't know whether this will meet local health requirements or not, but it's worth a try. If you are going to need the PVC cladding regardless, then use standard Thermax with thinner facers to save a bit of $$.
I'm not sure what you mean about venting. If you are venting the space between the insulation and the PVC interior cladding, that's fine. You should not have any venting inside the wall system itself.
I think Peter's original suggestion of ag panels are the right way to go. There are many version of this with different facers, you would have to do some digging to figure out what facing works in terms of health and safety and local building code. There are ones made with stainless facer commonly used in food processing facilities. Search for polyurethane sandwich panels. Some do come with an EPS core which works just as well.
I would avoid standard drywall in the assembly especially between two impermeable layers. If you will do the PVC cladding, it should be adhered directly to the wall. With a surface that will see water you don't want a gap where moisture get in but has no way to get out. I think a gap here is asking for trouble, if you can detail it similar to a vented rain screen it could work but that is a lot of extra complexity.
Another option would be to go with standard rigid (polyiso/EPS/GPS) and cover it with a cement board that has a ULC-S124 rating, some roofing products do come with this, or gypsum sheathing which has no paper in it. The PVC could then be adhered to this surface.
Unfortunately Thermax left exposed does not meet OBC requirements, I would not expect the Quebec code to be that different.