Building cost premium estimate for best practices

I am building just north the St. Louis MO area. I’m certain, in absolute terms, labor and material costs vary significantly. What I expect though, is that there is a relationship between traditional building costs [I’ll define that in a minute in my area] and best practices [which I’ll try and define as best I understand]. So, how much of a premium, broken down between labor and material, as a % of cost is there to building best practices.
In this area, currently. traditional practices is a poured foundation, no insulation under the slab nor around the walls, with some form of water-proofing on the walls. Main structure is 2 x 4 construction with a vapor barrier on the interior and a WRB between siding and the sheathing. Fiberglass insulation in the exterior walls, R-13. Vented roof with soffits and peak vents. Insulation in the attic is a ‘crap shoot’ but consensus is probably R-20 or so.
Minimum Best Practices for Zone 5 [building a bit north of St Louis] would be poured foundation and slab. Either staggered double 2 x walls or 2 x walls with no vapor barrier and with some form of air barrier [spray closed cell, taped exterior foam sheet insulation, well crafted wrap of some type], same for the roof with the rule of thumb of 5-10-20-40-60 insulation. All things being equal, I’d like to use foam insulation on the exterior walls and roof.
I’ll be building where there are no required codes or inspections but also where I believe best practices will be unknown and unpracticed. I’m hoping to convince a builder to build to best practices and want to be able to anticipate what that premium might cost.
I’m sure there are a myriad of variables so I’m just seeking opinions and some general guesses of % cost differences, perhaps in your geographic region or particular expertise.
Thanks
John
GBA Detail Library
A collection of one thousand construction details organized by climate and house part
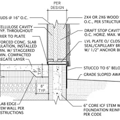
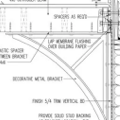
Replies
John,
I understand what it means to live in an area without code enforcement. But R-13 insulation for walls in Climate Zone 5? Really? It's one thing to ignore code requirements, but if builders in your area are really doing that, some future home buyer will take one of those builders to court.
Just because the code isn't enforced, doesn't mean a builder can be that sloppy.
Thanks Martin.
Any insights as to the cost differential between minimum building practices and best building practices, as a %?
All the Best,
John
Minimum best practices would be IRC 2019 code min, which would be a 2x6/R20 wall or 2x4/R13 + R5 continuous insulation, R49 fluff in the attic, and R15 continuous insulation on basement walls.
https://codes.iccsafe.org/content/IRC2018/chapter-11-re-energy-efficiency
Maximum financially rational for zone 5 is still pretty close to Table 2 p10 of this document:
https://buildingscience.com/sites/default/files/migrate/pdf/BA-1005_High%20R-Value_Walls_Case_Study.pdf
Note, those are "whole assembly R" numbers accounting for the thermal bridging of the framing, and the R value of the wallboard/sheathing/siding/ air films, etc. A typical 2x4/R13 wall comes in at about R10 whole-wall, a typical 2x6/R20 comes in at about R15 whole wall. To hit the R30 whole wall takes 2.5-3" of exterior polyiso sheathing, or a ~9.5-10" deep cellulose insulated double-studwall.
If you're on the zone 4/5 boundary shooting for the zone 4 row on that table is a good start. Going much beyond the row 5 table might be more expensive on a lifecycle basis than rooftop solar leveraged by air source heat pumps. At the falling price of solar (only about 1/3 the un-subsidized cost now than it was in 2009 when that was drafted) even going for the zone 5 row values might not be fully rational on an energy cost basis.
A lot of the foam-money sting can be alleviated by going with reclaimed roofing polyiso, which often shows up for cheap on sites like this:
https://stlouis.craigslist.org/search/sss?query=rigid+insulation
The $10 /sheet for somewhat rough 2" from the outfit in Springfield IL is fair unless it's really REALLY tired. Derate to R5/inch for used roofing polyiso from a design point of view. So for a 2x6/R20 wall clad in 2" roofing foam would typically run ~R25 whole-wall or a bit better, depending on the actual framing fraction & the other layers.
John,
Q. "Any insights as to the cost differential between minimum building practices and best building practices, as a %?"
A. That's tough to say. If builders in your area are framing with 2x4s insulated with R-13 batts, with no other wall insulation, the reference bar is extraordinarily low. It's a little like asking, "How much does a nice dinner in a good restaurant cost compared to a cheeseburger and a Coke at McDonalds?" The answer is, "More."
Quality construction isn't just about specs. It's about paying attention -- and caring. In some areas of the country, finding builders who pay attention and care isn't too hard. Elsewhere, it's quite difficult.
Thanks for the replies.
What I'm seeking, and perhaps I'm not making my question clear, is:
Best practices costs something incrementally over 'traditional/cheapest' practice.
What is that?
What is the cost differential, in any region, between R-13 2x4 wall and R-20 or so attic vs. R-30 wall and R-49 roof?
I'm no expert and maybe that isn't something that can be guesstimated but in my ignorance, it seems to be doable?
Thanks
John
I suspect that the incremental cost is primarily a function of the builder's experience. If they've built several/many houses that are well air-sealed (<1.5 ACH, say), and if they've worked with external insulation before, the incremental costs will be relatively low. If it's the first time a builder and his/her subs have tried to build a tight home, they're probably going to spend a lot of extra time figuring things out. Especially if the drawings are "usual and customary".
Would it be possible to give a cost differential between a minimum code built house and a best practices build house in zone 5?
No, it's not possible to give that number.
It's possible to put together materials lists and compare them, but the contractor experience & overhead and labor costs vary quite widely.
An IRC 2018 code-min house for zone 5 that actually meets code in all respects (including foundation insulation) with a design optimized for efficiency by shape, window area & orientation, roof overhangs, etc. can easily be twice as efficient as a code min house with a gazillion corners & bump outs, excess window area, and has ducted mechanical systems in an attic, above the insulation etc, and come in at a lower cost too.
Michael Maines has it right: Run a BeOpt simulation on the design as it evolves. Sometimes more efficient is cheaper. eg: Smaller windows, windows that don't open, no windows on the west side, simpler foundation footprint with no more than 6 corners.
Dana,
Thanks for your response. I didn't have a chance to study it and read the paper you referenced until this morning.
Your observations and suggestions are very helpful.
John
John Paul, as others have noted, your question is impossible to answer accurately, because there are way too many variables. Particularly when builders don't understand high performance building techniques, the ramp-up (and hand-wringing) can be time consuming. In addition, many people who build (or who hire others to build) high-performance homes make tradeoffs that affect the cost, such as using an exposed concrete slab as a finished floor, or less-expensive kitchen cabinets, or eliminating window trim.
All that said, if you want a range to think about, I'd expect at least 5-10% more, and possibly 20-30% more, to make the jump you're talking about. Builders who have been building high performance homes for a while understand what needs to happen, and would be on the lower end of the scale.
Because a lot of it involves the building size, shape and details, you might find it helpful to use BeOpt, a free download from the Department of Energy, which is an energy modeling tool that includes national averages for many different assemblies and equipment selections. Of course the prices will not be perfectly accurate, but might be a little better than my ranges above. While you're using the program you can get a sense of how much these energy improvements will save you.
The most accurate approach would be to design a house with low-performance details and another with high-performance details, and have that builder price it out both ways.
Michael and Dana,
Thank you both very much. I'll download BeOpt and try to learn and use it.
I've attached some preliminary drawings of what I want to build. Very simple: 40 x 44, no dormers, no valleys, walk out lower level [south side]. Only 2 windows on the east side. 4 windows on the north side [ran out of attachment space]. The side with all the windows and deck, faces south. Primary HVAC will be ground loop heat pump. Not on the drawing is a wood burning stove on the main level in the great room, south side.
I have to accept I must pay for labor inefficiency since I doubt I'll find anyone with experience. I'll try and mitigate that by using sub components [like Zip Systems-R] that may not spook them too much.
I'm also going to try and strive for a super zone 4/sub zone 5 efficiency: balancing what can be done with what is best. Some areas, like insulation under the slab shouldn't be a problem at all.
You both have been very helpful and I feel like I can learn enough during this design phase [hope to build in the spring] to be able to get something close to energy efficient at a somewhat cost effective amount.
Thanks again,
John