Budget concern: Better to buy the R-10 windows with less-great walls?

A budget crunch forces some tough decisions. Most of the bidders prefer using 2x6s instead of the double stud wall, and using American R-2.5 to 3 windows over the European R-10 ones. My general knowledge is that heat always moves to warm up what is cold, therefore keeping our R-10 windows in the design seems like the place to spend our money. This would mean backing down to an overall R-22 wall (2x6s 24″ oc, exterior 1.5″ Zip System and another 1″ of rigid insulation, well sealed batt or rock wool in the cavity). Alternatively, we could shift the money to get spray foam everywhere if we went with the less insulated windows. I can not find research on the matter. I suppose another insight that I would enjoy would be the value of the R-40 double stud wall when combined with the R-2.5 windows. This is for RI, low Zone 5, and windows make up about 25 – 30% of the exterior wall. Thanks, Will
GBA Detail Library
A collection of one thousand construction details organized by climate and house part
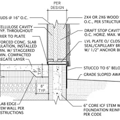
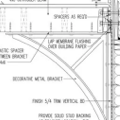
Replies
Will,
Does your project have an architect? A designer? An energy consultant?
This question would be easy to answer if your designer or consultant were using energy modeling software to optimize the envelope design.
An "American R-2.5 window" would be a window with a U-factor of 0.40. That's not very impressive. I'm not sure that you have researched all of the window alternatives. There are good windows available with better specs than U-0.40, but that are significantly less expensive than European windows with a U-factor of 0.10 -- let's call them "pretty good" windows.
A simple spreadsheet heat load calc would tell you the performance of each change. The basic calculation is:
U-factor x area x temperature difference= BTU per hour
The relationship between U-factor relative to R-value is:
U-factor= 1/(whole-assembly R)
The U-factors of window assemblies are published. The U-factors of framed wall assemblies have to be calculated or estimated, since cavity insulation is only a fraction of the cross sectional area, and has a different R-value than the framing fraction of the area, and the continuous layers of wallboard, sheathing, siding, and insulating sheathing all have their own R-values that add into the total. A typical wood-sheathed 2x6 wall with R20 cavity fill comes in at about R13-R15 whole-wall depending on the actual framing fraction and the siding & sheathing types, etc. The R-value of any continuous exterior insulation gets added directly to the stackup. The 1" ZIP-R adds about R6 over a conventional OSB wall, so that brings the whole-wall up to about R20, but mid-winter performance will be less than that in an RI location due to the low-temperature characteristics of it's polyisocyanurate insulation layer- call it R18-R19, unless you put at least 2" of exterior rock wool or EPS on the exterior of the ZIP-R to keep the polyiso warm enough to keep it in it's higher-performance range.
Upgrading the cavity insulation to a high R/inch insulation has remarkably little boost to the whole-wall performance due to the thermal bridging of the framing. (R-1,000,000 cavity fill only brings a 2x6 wall up to about R17 or so average performance after thermal bridging.) Using less expensive cavity fill and spending it on thicker insulating sheathing (that isn't thermally bridged by framing) is a far better value.
Windows usually comprise much less total area than walls, and gaining wall-performance is generally cheaper than window performance, but it depends on where you're starting from, and what your goals are.
Martin,
Perhaps you have some makers to suggest. As you know, many builders are in the Marvin/Pella/Andersen camp; so OK, let's call their products R-3 but I have heard that gases they use have already left the window before they leave the shop, so I certainly don't want to count on gases. I have researched a few American and Canadian window outfits that are in the R-5 to R-7 range but find them very uncommunicative, even with our window package of 50 windows! With the Euro decline, the premium for the R-10 versus the R-5 is only about 15%. An average operable is costing us $550 and fixed is down at $340 (and for the bigger sizes of doors and windows there is no premium at all even with the American standard bearers!). Of course, the interior and exterior casing adds a fair bit of labor to the equation.
I am an architect, but old school, and would appreciate the skinny on energy modeling software. The client may be forced into funding an energy consultant but is loathe to spend. Again, my sense is that the weak points in the envelope are the concern, and I don't see any other than the windows. So, perhaps my question is more conceptual in nature: Why build an R-40 wall if your windows are only R-3 and at ~30% of the wall will suck out all the heat; Why isn't more R-equality between wall and window a better way to reduce heat loss? Thanks, Will
Dorsett,
Thanks for your observations about the exterior versus cavity insulation - well said. Again, my understanding of physics is that heat always moves to warm up the coldest object it can find - this would be the 2 or 3 windows in each room rather than the wall, or, proportionately, some heat will seek out the wall, but eventually the wall becomes relatively warm enough that the heat will migrate instead to the windows. There, loss is at a maximum and windows are where they will never reach a steady state compared to the much better insulated wall, so there is a continual movement of heat to these locations. So, your last remark is indeed the question: If our windows are generally 25% of the exterior wall in any room, (this is not a tiny amount) and our exterior insulation is probably capped at 3", maybe 4", don't we conceptually want to allocate money to the better window? Thanks, Will
Will,
The triple-glazed windows sold by Paradigm Windows are said to be relatively affordable. I've never priced them, however.
When it comes to European windows, Intus is known for low prices.
GBA readers with more window-buying experience than me will probably chime in here with recommendations.
Correcting my typo- with R-million cavity fill you'd be at about R27, not R17... (With 5.5" of R6/inch closed cell foam you'd be at about R17.)
Take a simple example- say you have a 200 square foot room with 30 square feet of U0.30 window, and 100 square feet of R20 (whole wall= U0.05) wall. For every degree of temperature difference the window loses:
U0.30 x 30 square feet= 9 BTU/hr
For every degree of temperature difference the wall loses:
U0.05 x 100ssquare feet = 5 BTU/hr
Combined losses are then 14 BTU/hr per degree-F.
If you spend a lot of money on U0.10 windows you reduce that 9 BTU/hr to 3 BTU/hr per degree F, a reduction of 6 BTU/hr-f per degree, bringing the total down to 8 BTU/hr per degree-F.
Clearly you could not reduce the 5 BTU/hr-F heat losses of the walls by 6 BTU/hr-F, but there are cheaper ways to achieve the same heat load reduction than going straight to U-0.10 windows. For instance:
Reducing the size of the window by 1/3 would take 3 BTU/hr off the window losses, making the window losses 6 BTU/hr-F, but adds 0.5 BTU/hr to wall losses since it's now 110' of wall, not 100'. That's a net reduction of 2.5 BTU/hr-F.
Using U0.20 windows instead of U0.30 is still a lot cheaper than U0.10 windows, and would cut the 6 BTU/hr-F window losses to 4 BTU/hr-F, a net reduction of 2 BTU/hr-F for the windows.
So now we're at a 4.5 BTU/hr-F reduction without changing the wall stackup at all and have a combined load of 10 BTU/hr-F.
To get the remaining 2 BTU/hr-F reduction to equal the same improvement as going for the U0.10 windows with wall improvements is do-able. U-factor of the 110' of wall started out at U0.05, resulting in 5.5 BTU/hr-F losses. To get it to 3.5 BTU/hr-F takes a U-factor of 3.5 BTU/hr-F/100' = 0.032, which is a whole wall-R of 1/U0.032 = R31
That's achievable by adding R11 of additional exterior sheathing.
So the financial trade off becomes the cost of 30' of U-0.10 window vs. the additional 110' of R11 insulation (and the additional 10' of ZIP-R, which may be zero, since it comes out of the window-cut scrappage) + the cost of 20' of U0.20 windows over 30' of U0.30 window.
For making these calculations easier a free download (courtesy of the US taxpayer) of the BeOpt tool is worth it, since you can then and play "what if" games based on real or estimated costs of different configurations, and get a much better handle on the where the $/performance trade-offs lie at any chosen performance level. See:
https://beopt.nrel.gov/
Intus windows are indeed a good deal. Their base model uPVC are competitive with wood Marvins.
And I agree w/ Martin that an energy modeler seems like a critical partner here. You're making huge and expensive decisions with very little data. And Dana's points about other ways to skin the cat are excellent. you can also think about using fixed units (both for price and performance) in some areas.
Rather than going all out on either, you are likely to do best with "pretty good" on both windows and walls. That might mean a triple-pane low-e argon window, but almost surely not a krypton fill gas which is where the U 0.1 values come from.
For North American windows I recommend checking out Loewen (canadian) for great aesthetics and quality as well as performance at reasonable up to outrageous prices (if you go for their fanciest finishes), or Comfortline from FiberFrame for great performance at lower prices. I speak from experience with Loewen but only quotes from Fiberframe.
As Dana illustrates, calculating the performance difference is not hard. What's harder is calculating the cost difference, particularly for wall construction.
As a general rule, super-performance windows aren't needed for most energy use or peak load goals unless you need/want a lot of window area, and cutting less window area into the wall adds effectively zero to the wall costs, since the cut out is usually scrap.
While 15% window/floor area is typical, it's not a code requirement, and not always desirable. You don't need anything like that much window for daylighting purposes, and that much window area leads to uncomfortably high solar gains in some rooms.
Huber recommends AGAINST installing exterior foam over ZIP-R, since there is then a moisture-trap potential at the OSB layer. Using rigid rock wool rather than foam eliminates that as an issue, but if you DO go with foam, use a crinkle type housewrap (eg. Tyvek DrainWrap) between the foam & ZIP-R for faster drainage and a partial capillary break.
Is % window/floor area a good measure? I would think that %window to exterior wall area is a better accounting of whether one is pushing too much glass. (Using this latter gauge, we could benchmark easily, as our institutional projects averaged 29% over about 40 projects).
Forgive my ignorance, but if you utilize Zip System are you still looking at OSB and housewrap?
Will,
Zip System sheathing is a type of OSB manufactured by Huber. If the OSB seams are properly taped with Zip System tape, Huber says that you don't need housewrap. Many builders who use the Zip System sheathing use housewrap anyway, because housewrap is easier to integrate with window and door flashing.
More details here: All About Water-Resistive Barriers.
Will,
I would go to the Intus website and find the nearest dealer rep and give them your window schedule. Price it out for the white PVC triple pane windows and you will be pleasantly surprised that the pricing will beat out or match most dual pane windows.
As an architect you know that house design is also about comfort. Triple pane windows provide superior comfort and one can sit next to a window without feeling a draft or convection. Plus they are quieter than dual pane.
Performance Building Supply - http://performancebuildingsupply.com
Talk to Alba or Jason.
Will- regarding post #10:
With ZIP-R the OSB is factory laminated to the polyiso, and has a WRB rated exterior surface coating, which works just fine if you're mounting your windows "innie" style, and adding rigid rock wool to the exterior, not foam. If you use exterior foam and innie windows you need to provide a capillary break between the ZIP-R and foam and some drain space, which is where the crinkled housewrap become important. Even though the exterior finish of the ZIP-R is a WRB, the surface tension of liquid water will trap it between the foam & ZIP, and some amount will eventually end up in the ZIP, taking forever to dry through the foam.
Drying rates through ~30 perm rock wool is an order of magnitude faster than an inch of unfaced Type-II EPS, and more than 25x faster than an inch of XPS. And rock wool would mildly wick moisture away from the ZIP, whereas EPS or XPS would not wick at all, leaving vapor diffusion as the only mechanism for getting the moisture off the ZIP after a bulk water incursion. Crinkled housewraps allow gravity to purge the majority of the inundation, as well as a tiny amount of air transport out. Gravity would also take care of a lot of liquid moisture in the rock wool case too, as much or more than crinkled housewrap.
If mounting the windows "outie" you'd need a housewrap on the exterior of the rock wool or foam, since the window flashing is directing the bulk water to the outside of the additional insulation.
ZIP-R does not need another layer of OSB.
Window / floor ratios are a commonly used metric in the residential housing biz, even though window/wall ratios are more relevant from a heating & cooling load calculation point of view. At 15% window/floor ratio is about average. Codes specify minimum window areas for daylighting & egress purposes, and those are usually enforced. Some codes specify maximum window / wall ratios before the room has to be engineered on a total thermal performance basis, but those are often ignored, especially when there's a nice view to be taken in. (Something like that happened on an addition to my home prior to my tenure- the newest rooms are the lossiest. It really needed higher performance windows or less window, but correcting that is an expensive proposition- there is still lower hanging fruit elsewhere.)
For those who mentioned INTUS,
Thank you, but EAS-USA is better, unless the flange offered by Intus is something really special. The least expensive Intus line (Arcade) is $26/SF for fixed and $40/SF for operable, and is R-6.7. The Schuco 182 window at EAS is R-10 and beats those prices. Plus, the prices I have from EAS include a Mahogany foil on the interior which is another premium on the Intus. Thanks, Will
Will,
I believe you have misrepresented the data. The Schuco 182 window you referenced is NOT an R-10 window. The REAL whole window value is around R 6.5 - R 7.0
Verify the NFRC #'s and you will see that you were incorrect in your conclusions. I went on the NFRC website and I could NOT locate European Architectural Supply, Schuco or Makrowin Windows as a participating member. Based on that, the windows were NOT tested and NOT certified by NFRC. Intus Windows are listed on the NFRC website and they are a participating member and have turned in windows to be tested and certified via NFRC. The European values that are usually posted are not apples to apples comparison to U.S. NFRC #'s.
As far as posting square footage prices of Intus. Those numbers are not accurate either. I've seen the prices and a lot of the cost depends on options. I've seen prices as low at $15 per square foot for Intus' triple pane uPVC fixed windows. So throwing out #'s is not fair because of the options that are available and one doesn't know if you are comparing apples with apples.
If you have the NFRC #'s of the EAS/Schuco Windows you are referencing that achieve a whole window R-10 NFRC rating, please provide the NFRC link showing the ratings. I could not locate any NFRC testing for the window manufacturer you quoted.