Brick Veneer Insulation Retrofit Assembly Check

Hi all, I was hoping that someone could double-check my details on a proposed insulation retrofit of a brick veneer wall on my 1955 ranch-style house. I think I’m understanding the complexities of the assembly and responding appropriately, but vapor drive is one of the fuzziest of all the BS concepts to me.
A few climate considerations: I’m in Boise (CZ5), but only 5800 HDD, so on the warmer side of CZ5. Also, it is relatively dry here with only 13.8 inches of rain per year, with most of that coming in the cold months. April through early June are the only real crossover wet/warm months where we get about 1.3 inches of rain and have any temperatures above 65 degrees. Additionally, the wall faces East, and our temps in those few months don’t really peak until the afternoon, so the sun rarely beats on that side of the house when it is wet.
There are attached detailed drawings of the current situation, along with the proposed solution, but one thing that I sticks out to me is the double-layer of 6-mil poly behind the roofing paper and how that complicates a solution. My thinking is that the poly will stop vapor drive from the exterior, but also largely limit/completely stop any sort of drying potential to the exterior as well. In order to accommodate that lack of drying to the exterior, I need to respond by preventing interior moisture from making it to the exterior wall in the cold months as well as accommodate as much drying to the interior as possible. Am I thinking about this correctly?
I’m sure there are many solutions (assuming I’m understanding the concepts correctly), but my proposed is to remove the interior drywall and replace the R13 fiberglass with either Rockwool Comfortbatts or dense-packed cellulose, and then follow that with Siga Majrex as the air barrier/smart vapor retarder. While I have the wall open, it seems to make sense to use a Bonfig assembly to give the cavities more depth and a thermal break. Does that make sense as an approach to this situation? Or, is the Majrex SVR overkill so long as I properly detail the interior drywall as my air barrier?
I’ve read several articles on masonry retrofits, but most are relative to mass walls and not veneers. The closest I could find to my particular situation was an article written by Kohta Ueno (link below), but it only briefly touches on something related in Figure 5. Perhaps I’m overthinking things relative to the exterior poly, but would love to know if I’m off in my assumptions about my particular assembly.
Thanks in advance for taking a look.
https://www.buildingscience.com/documents/insights/bsi086-vitruvius-does-veeners
GBA Detail Library
A collection of one thousand construction details organized by climate and house part
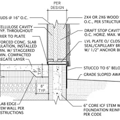
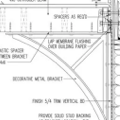
Replies
For whatever reason it doesn't associate the post with my account, and it didn't attach the detailed drawings. I'll clean that up if I can, but for now, here they are attached as a comment.
>" I’m in Boise (CZ5)"
------
>"There are attached detailed drawings of the current situation, along with the proposed solution, but one thing that I sticks out to me is the double-layer of 6-mil poly behind the roofing paper and how that complicates a solution. My thinking is that the poly will stop vapor drive from the exterior, but also largely limit/completely stop any sort of drying potential to the exterior as well."
That is correct- polyethylene sheeting on the exterior of the sheathing prevents the sheathing from drying into the cavity, forcing it to dry only toward the interior (a LOUSY thing to do to a brick veneer in climate Zone 5B.) Can it be removed?
If yes, simply venting the brick cavity top & bottom with weeps every 3rd verical mortar line near the bottom, with corresponding vents near the top course will convection-dry the brick & sheathing to the exterior adequately even without smart vapor retarders on the interior (standard latex paint on wallboard would be fine.)
If (as is likely) there is no practical way to remove the polyethylene sheeting and still retain some sort of weather resistant barrier, any smart vapor retarder on the interior would be sufficient (even comparatively inexpensive MemBrain), so long as you aren't actively humidifying the air to much more than 35% RH @ 70F during the winter. While 50%+ RH may feel great to the human occupants, it's potentially high enough to increase the vapor permeance of MemBrain enough to increase the peak moisture content of the sheathing to riskier levels. The dew point of the entrained air in the insulation will still track the temperature of the sheathing in winter, lowering the permeance of the vapor retarder, so it's not SUPER risky even at 50% RH indoors, but 35% RH would have a large safety margin.
BTW: Is the sheathing shiplap plank, as suggested by your drawing?
If yes, it's probably not very air tight unless the exterior polyethylene was detailed as an air barrier (not likely), with those details still in good shape (even less likely). If using fiber insulation (especially batts) it's important to put an air barrier on the exterior side to have any shot of it's meeting it's rated R-value in this assembly. If using dense packed cellulose (3lbs per cubic foot or higher) or fiberglass (1.8lbs density or higher) that's less of an issue. The air barrier solutions that work can be tedious &/or expensive. While a 2" (R6- R7) HFO blown "flash & batt" solution might look good on paper for it's air tightness and vapor retardency, it's hard to make BATTS fit well in real-world foam installations (though blown fiber still fits fine.) It would be cheaper & easier overall to go with a full cavity fill (including the furred out Bonfiglioli strips) with half pound spray polyurethane foam (R20-ish @ 5.5").
Thanks so much for your response, Dana. It seems unlikely that I'll be able to remove the poly without compromising the WRB. However, we do keep it pretty dry in the house; it's currently at 32% RH, and the average has been 41% for the last 3 months.
And yes, it is shiplap plank, and very leaky based on how cold that wall is relative to the others (which is saying a lot). I can't imagine that they detailed the poly at all.
The wall in question is under 250 sq feet, so I'd be more willing to entertain a tedious solution. Would a detailed air barrier—perhaps a SVR fully taped to the inside of the stud-bay against the sheathing, or, a rigid foam insulation taped to the inside of the stud-bay—followed by fluffy insulation followed by MemBrain work as well in your opinion?
I'm not morally opposed to spray foam, but the nearest/most qualified HFO spray foam contractor is actually 100-miles away, and he charges accordingly as you can imagine. Every other contractor I've contacted only supplies HFC blown foam.
Strange to see poly on the cold side of a wall, it is pretty bad idea in zone 5. I would say the safest approach is to flash the walls with closed cell spary foam before any fluffy insulation is installed. Since the SPF now becomes your vapor and air barrier, there is no way for moisture to make it to the exterior poly and no chance of condensation.
A batt only with a warm side smart vapor barrier might work but there will definitely be a bit of condensation on the sheathing. The good thing is lumber sheathing can handle a lot more moisture than OSB or CDX, so it might work as long as you air seal your walls. Instead of mineral wool batts, might be better to dense pack with cellulose as this will help with buffering moisture and also helps with air sealing.
Thanks, Akos. I was definitely surprised—and disappointed—to find it in there. I only discovered it upon a deeper look as it was obscured by the tar paper, and did a double-take when it appeared as I’ve never heard of it being used on the exterior behind a reservoir cladding. Apparently I’m just that lucky.
So if I’m understanding it correctly, from a durability perspective my biggest concern should be warm, interior moisture hitting the cold, condensing surface of the sheathing. Normally, this could be solved by an SRV (MemBrain, Intello, Majrex) on the interior side with fluffy insulation in the cavity so long as I keep the interior humidity around 35% ideally as Dana pointed out.
However, the shiplap board sheathing complicates things in that it allows enough air to flow into the wall cavity that the insulation’s performance will be greatly compromised, which rules out the above solution from a performance (and therefore durability) standpoint.
From a conceptual standpoint, an air-barrier is needed between the sheathing and any insulation in the cavity. As both Dana and Akos pointed out, spray foam would be ideal for air-sealing and vapor-permeance reasons. Half-pound spray foam at a thickness of 5.5” would have an R-value of about 20, and a perm rating of between 3–5, which would be sufficient in keeping the sheathing dry when paired with our relatively low interior humidity. Flash-and-batt could work for all these reasons, but as Dana pointed out, it’s difficult to ‘batt’ over the unevenness of the ‘batt’ from a practical standpoint.
Dense-pack cellulose (3+ lbs) or even blown fiberglass, along with an SVR could work as well. This is due the way these dense-pack materials largely inhibit air movement even though they aren’t true air barriers. Cellulose also benefits from its ability to act as a hygric buffer and redistribute moisture should any make it to that cold sheathing.
I’m sure I’ll go with one of the above solutions that you all suggested, but in a bit of ‘teach a man to fish’ moment and with labor aside, would a solution of 1.5” (or more) thick foil-faced polyiso cut to fit the 16” stud bays and then taped to studs to form an air barrier, followed by batt insulation work? My thinking is that the polyiso would be of a necessary thickness to keep the foil-faced surface warm enough to stay above the interior air dew point, and it’s low perm-rating would mean that no moisture could reach the cold sheathing. An air-tight drywall approach (or, MemBrain if a vapor retarder is required by code) would be helpful in lessening the amount of moisture heading in that direction, although it’s really just insurance. Attached is a detailed drawing of that scenario for clarity. Does that sound like something that would work? Or, am I off in my understanding of the goals/materials?
>"I’m sure I’ll go with one of the above solutions that you all suggested, but in a bit of ‘teach a man to fish’ moment and with labor aside, would a solution of 1.5” (or more) thick foil-faced polyiso cut to fit the 16” stud bays and then taped to studs to form an air barrier, followed by batt insulation work?"
Foil faced foam would be a disaster. Foil facers (like polyethylene sheeting, and UN-like 1-2" of closed cell spray foam) is a true vapor barrier. Installing vapor barriers on both sides of the sheathing creates a moisture trap- any bulk moisture that found it's way in would take years to dry, creating a serious rot potential.
And that's before considering that cut'n'cobbled foam board always leaks air somewhere, eventually. It's not flexible enough to handle seasonal dimensional changes of the wood, and foam board usually shrinks a bit over a few decades, making stress cracks in or breaking the bond of the can-foam sealer. For a reliable seal the air barrier needs to be flexible, and at least somewhat permeable to water vapor in order to provide a drying path.
If there are no nail-points sticking into the stud bays to rip it, using flexible but vapor permeable materials for the air barrier works. Cutting 18" wide strips of housewrap to tuck in and side-staple to the studs can work, using housewrap tape to seal over the staples and edge of the sheets to the studs. If the studs are too grungy for the tape to stick, apply a thin bead of polyurethane caulk under the edges of the housewrap and smooth it out with putty knife or wallboard mud knife or similar to ensure the seal. Super-skinny stud bays that are too narrow for this treatment can filled with can-foam or Froth Pak (a 2 part closed cell foam sold in small volume kits) or similar.
Cut and cobble is not the same as spray foam. There is no way to make it reliably air tight, the foam is not bonded to the sheathing. Once any moisture makes it behind the rigid insulation, there is no way for it to escape, can create a lot of problems down the road.
You want about 1.5" to 2" of closed cell SPF. This is enough for condensation control and it is thick enough to act as a vapor barrier.
Open cell SPF has the same issues as fluffy, the condensing surface is still the exterior poly, but it does do a better job of air sealing. I would still be more comfortable with the cc SFP+batts approach. Most batts can be squished a bit to make up for a lumpy SPF install. If it is very lumpy, go for standard fiberglass batts, I've had no issue with squishing 2x4 batts into a 2.5" cavity.
>"You want about 1.5" to 2" of closed cell SPF. This is enough for condensation control and it is thick enough to act as a vapor barrier."
At that thickness closed cell foam is about 0.5-o.8 perms. While that is sufficiently low permeance to qualify as a "vapour barrier" under Canadian codes, it's still a 10x or more vapor open than 6 mil polyethylene vapor barriers.
>"Open cell SPF has the same issues as fluffy, the condensing surface is still the exterior poly, but it does do a better job of air sealing."
The vapor permeance of open cell foam is still an order of magnitude lower than fluffy stuff, but still way too vapor open to skip the interior side smart vapor retarder. But it's many orders of magnitude more AIR resistant than mid density batts- pretty much air tight at 3"+. With a smart vapor retarder and effectively zero convection potential inside the cavity, the sheathing is going to be pretty safe, even with the exterior side vapor barrier, so long as the interior RH isn't maintained at some unusually high level.
With a smart interior side vapor retarder even carefully fitted cellulose (or cotton/denim) batts would be pretty safe, as long as the interior and exterior air barriers are pretty tight. The organic fibers would share and redistribute the moisture loads, buffering and moving the moisture within the fibers without loss of function or damage, reducing the average moisture build up in the wood, and reducing any localized damp spots in the wood.
>"Most batts can be squished a bit to make up for a lumpy SPF install. If it is very lumpy, go for standard fiberglass batts, I've had no issue with squishing 2x4 batts into a 2.5" cavity."
Slumps of foam at the stud bay cavity ends and variations along the edge make it impossible to get a perfect fit. You can jam lower density batts in there, but there will inevitably be at least some voids, unless the foam installer is the Michelangelo of spray foam (an impossible talent level for an inexperienced DIYer with a 600 board foot foam kit).
With <250 square feet of wall most pros wouldn't touch it at anything approaching a "reasonable" price. That's true of 5.5" of open cell foam too, but that un-reasonable price would still be lower than 1.5 - 2 " of closed cell foam, and more guaranteed to be truly air tight. For a pro the travel time & set-up & break down time is the same whether installing 400-500 board-feet or foam or4000- 5000 board feet. The cost per board foot ends up being quite high for a flash & batt that size. With a DIY kit a 2" flash part would come in well under a grand, but in my book it would still call for blown fiber (not batts), adding more complexity. Even with DIY 2" of foam + DIY batts the cost would probably be in the same range a 5.5" open cell solution, with lower air leakage and fewer issues about fit and air leakage.
Sorry for the confusion; I wasn't suggesting cut-and-cobble with the rigid foam by using canned foam as the seal. Rather, I was talking about taping the faced-foam to the studs to allow for the movement inherent in the building materials.
I did some more reading/research after your kind explanations, and think I'm understanding the 'why' part a bit better. I made some false assumptions and had some critical misunderstandings:
"Dana>Foil facers (like polyethylene sheeting, and UN-like 1-2" of closed cell spray foam) is a true vapor barrier."
As you pointed out, I was treating the closed-cell spray foam as an equivalency to the >0.1 perm rating of the foil-faced polyiso. That is, I was thinking of the foams in a very binary way—basically, they're either a barrier or a retarder—when in fact it's far more of a gradient than I assumed. The BSC article linked to below is what seemed to make things click for me should anyone else find it helpful.
I also wasn't considering the possibility of bulk water intrusion into that 'barrier sandwich', which should have been a primary concern in terms of durability. I was only considering vapor, and had assumed that the same air flow that would make batt insulation unsuitable would also provide drying potential for vapor. But again, I hadn't considered if that would be substantial enough for bulk water as Dana pointed out, which it clearly would not be.
Akos, thanks for your perspective on the practical application of the flash-and-batt approach, and switching to fiberglass to accommodate a very lumpy application. That's good to know.
In regards to the application of the housewrap to the inside of the stud bays, would there be any benefit to providing a gap between the housewrap and the sheathing to promote drying should any bulk water find its way back there? Or is that overly complicated relative to the practical usefulness?
Thanks again so much for walking me through the reasoning. I feel like I have much better understanding of the elements in play due to your explanations.
https://www.buildingscience.com/documents/guides-and-manuals/gm-guide-insulating-sheathing/view