Better NOT to vent the top of a rainscreen assembly?

My clients have a 1960s house, 30′ from the coastal bluff in Mendocino CA. We are currently re-siding the house by using the old T-1-11 as our sheathing, new housewrap, new rainscreen battens (1/2″ pressure treated ply 16″ o.c.) with Coravent SV3 at the bottom, then 4×8′ hardipanel and finish battens and trim.
I have noticed that the existing crawlspace vents suck in a huge amount of moist air on the ocean side of the building, and that the paint on the siding over the crawlspace appears to be poorly adhered and damp under the paint. This makes me wonder if there is ever a case NOT to vent the top of a rainscreen assembly. The logic being that venting at the bottom allows moisture to escape, but venting at the top and the bottom creates enough pressure to actually suck moisture into the rainscrren gap. Or is this totally nuts?
Any help is appreciated.
GBA Detail Library
A collection of one thousand construction details organized by climate and house part
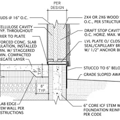
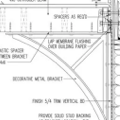
Replies
Cynthia,
I wouldn't overthink this issue. If you prefer to seal the top of the rainscreen, you can.
That said, research has shown that rainscreen gaps that have ventilation inlets at the bottom and ventilation outlets at the top allow damp siding and sheathing to dry more quickly than rainscreen gaps without ventilation openings.
For more information, see this article: All About Rainscreens.
Are there copious amounts of salt spray hanging in the air?
Allowing that convection is what allows rainscreen to provide rapid drying. If the exterior moisture drives are high enough to insert damaging amounts of moisture into the rainscreen, it means that the exterior side of the siding is being actively wetted at the same time. When it's calm enough that the active wetting has stopped, having the ability to dry to both the interior and exterior would reduce the drying time of the siding.
Siding that overlaps the walls of a damp crawlspace foundation is being subjected to groundwater moisture as well as exterior moisture. A rainscreen gap between siding the foundation helps, rather than hinders that issue.
A vented crawlspace can be OK in most coastal CA locations due to the low average dew points of the outdoor air (it usually tracks the cool ocean temperature), but it usually increases energy use. A sealed unvented crawlspace can work in any climate, and if prevailing winds are injecting salt spray through the vents making the crawlspace more damp than it would be from ground moisture alone. A ground vapor barrier and insulating the exterior walls works. See:
https://www.greenbuildingadvisor.com/blogs/dept/musings/building-unvented-crawl-space
That's a location that is way outside the norm as far as fog exposure. I think you are right to question whether the conventional wisdom and studies done in conventional locations apply. If you have fog flowing through the rainscreen gap, you could get wetting a lot faster than the subsequent drying. So I think your argument for closing the top makes sense.
Momentarily setting aside Martin's advice against overthinking, my engineering brain wants to put electric dampers at the top of the rainscreen with optical fog sensors to open and close them. But that is of course ridiculous. It would be much more practical to build it one way or the other and realize that it might need new paint more often than a building a mile inland.
Cynthia,
Rain-screens do perform better with their top vented, but they work perfectly well with just the bottom open.
They may not get as much air movement to aid drying, but you still get the full benefit of their other functions: a capillary break, and drainage plane for any bulk water intrusion.
Charlie: The part of the world where rainscreens are now required by code (western British Columbia) is also has "extreme fog" zones. Rainscreens have be proven to be the solution, not the problem.
Cynthia, I've seen a lot of upside-down rain and water intrusion into vented roofs on coastal projects, but I doubt you would have the same "sucking" effect with a rain screen vented at both the top and the bottom. The wind would have to blow strongly across the top of the rain screen cavity to create enough negative pressure to bring liquid water into the assembly. Even with the unique conditions that occur at the top of a coastal bluff, as long as you have at least a little overhang at the eaves, I don't think you'll have any problems.