Best way to separate SmartSide panels from concrete stem wall?

I will be installing SmartSide panels directly to my wall studs, rim board, and sill plate, which rests on a concrete stem wall. The SmartSide instructions show the panel extending a little below the sill plate, but they require that it not be in contact with the concrete, and they show a piece of flashing that has a 1-1/2″ vertical leg then a short angle that juts out below the bottom of the panel. It’s not a z-flashing; it’s more like a droopy L.
If I had thought about this back when I built the stem wall, I would have given the sill plate a small overhang so that the SmartSide would be separated from the concrete by air, but given what I have, I’m hoping there’s some better way to separate the SmartSide from the concrete than with metal flashing, as I don’t like the idea of a metal edge sticking out, z-flashing would look weird with nothing below it, and the droopy L doesn’t seem to be available pre-formed. The separator would have to be waterproof, as its purpose is to keep moisture from wicking from the concrete into the SmartSide. I’m thinking that vinyl roll flashing might be a good choice; I could get a 10″ x 50′ roll and cut it into narrower strips fairly easily, unlike a galvanized roll that would seem much more difficult to cut. (I gather aluminum and concrete don’t get along.) If I use roll flashing, I could have just a bit poking out below the SmartSide. Is there a better solution?
GBA Detail Library
A collection of one thousand construction details organized by climate and house part
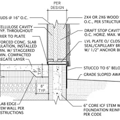
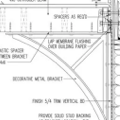
Replies
Well, I have some 50 year old aluminum flashing on concrete that would argue that...
IF you are considering making something, old flashing brakes are pretty cheap on CL and could be sold the same way when done.
You could also buy Z flashing and fold the bottom lip back to become a hem, I think done easily on a tapco[siding] brake
Thank you, Keith. I'm hoping to avoid metal if I can. The consensus among engineers is that aluminum and concrete damage each other, https://www.eng-tips.com/viewthread.cfm?qid=407349, but I imagine in certain conditions, perhaps when both are quite dry, it's minimal.
Jeff,
Why not kill two birds with one stone and use a flashing-tape to both seal the intersection of the plywood and concrete, and provide a break between the siding and foundation wall before putting up your WRB? If you extend the tape down an inch or so and do the same with the siding you should be good.
Watch the very beginning of this video (disregard the base-flashing):
https://www.youtube.com/watch?v=SqP4liutJFs
Your link is to an engineering discussion board, not a construction one. While there are many weaknesses to aluminum flashing, it is widely used . If you are concerned, and I am not saying there is zero cause for concern, use painted flashing or put something in between the concrete, as Malcolm suggests
Some of the flashing I referenced is at grade, always wet.
No problems, 50 years
The linked discussion spoke of embedding aluminum in concrete, I can see where this might be a problem, total electrical connection to the concrete, maybe.
I see this kind of thing on Car forums, don't use stainless hardware, it will galvanically corrode. Which it will, about 50 years after the regular steel hardware would have ceased to exist....
Great idea, Malcolm; thank you! It could cover the joint between the rim board and the sill plate and then extend below the sill plate 1" onto the concrete. I'm in the desert, which allowed me to have a vented crawlspace, so I'm thinking I don't need the tape to stick to the concrete, which would require primer, and form a seal there, unless having the bottom inch not adhered would lead to a loss of adhesion higher up.
Living in the desert sounds fairly appealing today. High winds and rain. No power since this morning. Hope it's on by supper time!
I'll push some warm, dry air northwest, Malcolm.
Cheers Jeff!