Best practices ideas for retrofitting existing PWF built in muskeg and best practices for foundations for new builds in muskeg (i.e. very wet !) and a severe cold climate

The existing PWFoundations are wet (many moldy) and have dirt floors. the crawlspace is heated with a baseboard to keep plumbing from freezing. House shifts with freeze thaw action on the spongy ground. Looking for ideas for retrofit – can remove non-draining back fill, install a skirt of frost protection, backfill with free draining materials and can cover the dirt floor with sealed poly. need to make the crawlspaces a cleaner and warmer conditioned space. Any other ideas to achieve this? In particular, how to circulate the air – will passive floor vents connecting the crawlspace to the home work? Will be difficult to install an exhaust fan in the conditioned crawl space -are there other options? For new builds, would ICF be the best option for a crawlspace in this wet soil? Slab on grade the best option? Anyone have any experience in other locations ?
GBA Detail Library
A collection of one thousand construction details organized by climate and house part
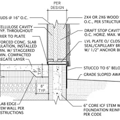
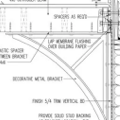
Replies
It seems that no affordable water barrier is 100% bullet proof. Some ceramics and metals can be virtually 100% impermeable. For my PWF I use 20 mil foundation grade poly backed up by a layer of Tu-Tuf. They are fussy to fit and easy to puncture, requiring careful installing to ensure what they are on top of and underneath will not make a hole now or in the future. Hard to retrofit. You will have to do it in stages and use top grade tapes for the seams. I guess you could make a liner inside an existing foundation and reframe the basement.
If anyone's' PT lumber or ply is moulding; it's not the right grade. Someone needs to be sued. Mould indicates the wrong material was used.
In-ground contact grade PT lumber and ply does not mould and if the site is permanently in water or ice, as with permafrost and muskeg, it might require marine grade. Sit down before you ask the price per sheet. But its still much cheaper and easier than concrete..
No grade of PT plywood is impermeable, it soaks up and passes moisture. It is used for structure not waterproofing. That mistake is why PWF's lost credibility. Folks were under the impression PT plywood was supposed to be waterproof and neglected adequate waterproofing outside the foundation.
By the way, I wrap my wooden poles and in-ground timbers with Cu-bor post wraps. If its legal where you are, there are several forms of copper and borate treatments that stop mold, insects and the rotting of wet wood due to fungi and bacteria.
http://www.coppercare.com/products/CuBor.aspx
In my view,the best foundation in wet ground is no foundation. Levitate the building with concrete piers or PT posts, with an open air breezeway, topped with a raised superinsulated foor/platform (use wood I's), build house on top. Raised high enough to work underneath and install your mechanicals on the platform, piping and wiring through interior walls and designed-in floor and ceiling chaseways/bulkheads.