Best method for insulating

Doing foundation work for a new house in Jackson, Wyoming it is in Climate zone 7B. The architect has specd. 2″ closed cell foam then r13 and 1/2 rigid foam over sheathing (exterior).
Based on current Building science knowledge, I don’t this is a good idea.
any thoughts on the best method of insulation for this project would be greatly appreciated.
Thanks
Donny
GBA Detail Library
A collection of one thousand construction details organized by climate and house part
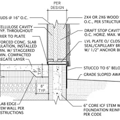
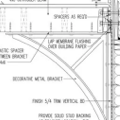
Replies
Donny,
Your question is confusing. You mentioned foundation work. Then you posted an image. Is this a basement wall? A roof assembly? Hard to tell.
I finally figured out that it is probably an above-grade wall. I'm guessing that the studs are 2x6s. (Correct me if I'm wrong.)
It sounds like the architect is proposing a type of flash-and-batt approach. For more on this method, see Flash-and-Batt Insulation.
Building codes call for a minimum of 2.5 inches of closed-cell spray foam for a flash-and-batt job in Climate Zone 7. That would be better than 2 inches of spray foam (and a code official might object to the job as spec'd).
The 1/2 inch thick continuous layer of exterior rigid foam is also somewhat problematic, because it sandwiches the sheathing (unidentified -- what is it? OSB? Plywood?) between two layers of foam.
A better wall would put all of the foam layer on the exterior side of the wall sheathing. In your climate zone, this approach would require rigid foam with a minimum R-value of R-15. If you follow this approach, you won't need any spray foam between the studs.
For more information on these issues, see How to Design a Wall.
Martin,
First, thanks for your quick reply! Your answer is exactly what I was thinking, all foam (r15) on the exterior with batts in the cavity, but wanted to run it by those more knowledgeable than myself.
Sorry I should have been more clear, these are exterior walls above grade 2x6 16 o.c, sheathing specd is 1/2 OSB.
What rigid foam? It makes a difference- anything with facers would be a problem.
But half inch unfaced EPS or XPS doesn't present a drying problem to the exterior since it's over 2 perms, (almost as vapor open as interior latex paint) and the 2" spray foam will be under 1-perm, but over 0.5 perms. It's sufficient protection for the sheathing from interior moisture drives, but still retains some drying capacity toward the interior.
The 2.5" total foam in the stackup plus the R0.5 for the sheathing itself provides PLENTY of dew point control the foam/fiber interface for the R13-R15 fiber.
But I'd object to it on cost, performance, and verditude grounds. The closed cell foam barely moves the needle on whole wall performance since the R13 foam is thermally bridged by the ~25% framing fraction, has a high polymer per R factor, and (usually) a high global warming impact blowing agent. Assuming 1x nominal board & batten you're looking at a whole wall performance of about R19-R20 depending on the rigid foam type and the density of the fiberglass, a U-factor not lower than U0.05.
It would not quite meet IRC 2015 code-minimum sfor zone 7, which would be R20 cavity + R5 continuous insulation, or R13 cavity + R10 continuous insulation, or a U-factor no greater than U0.045. It's over U0.050 unless that half-inch rigid is something truly exotic, such as aerogel.
If you did the cavity with R20 fiber, and installed R15 continuous 3.5" of Type-II EPS (would exceed the R15 required for dew point control during the winter months) you'd be at about R30 whole-wall, with only 1% of the climate damage and a comparable or lower cost. (3.5" of EPS runs about $1.50/square foot, to 2" of closed cell polyurethane at about $2/square foot. The 50 cents per square foot difference more than covers the longer timber screws for the furring.)
With dense-packed 2.2lb fiberglass you'd be at about R31 whole-wall, but that would be more expensive than R20 damp sprayed cellulose or R20 batts (or even R20 open cell foam)
If you dropped back to 2x4 /R15 with only 2.5" of EPS for dew point control you'd be ~R22 whole-wall, about 10% ahead of the described stackup on performance, at much lower price point and higher moisture resilience. That's a much cheaper and somewhat higher performance build than what's in the drawing, at the same wall thickness. Better yet, this actually meets/beats the code minimum performance. If you want foamed cavity for air sealing, a full 3.5" of half-pound open cell foam (R13) seals as well or better than 2" of closed cell, and it still meets code-minimum. Half pound open cell foam uses about half the polymer per R compared to 2lb closed cell, and uses water (instead of HFC245fa) as the blowing agent- that's as green as it gets in the foam insulation world.