Best insulation updates for above grade bonus room?

Hi All,
Can’t say enough good things about the information and community here at GBA. After purchasing a home just over a year ago, I’ve been absorbing as many blogs, websites, and podcasts as I can to learn how to work on, and improve my home. This site has proven to be the best source of information on the newest science and best practices.
The home is a 70’s split level. I’m currently working to refinish the last of the remaining space with faux-wood paneling. The space is 100% above grade, in the back corner of the house. Two of the walls are block w/ exterior brick veneer, one is an interior partition wall, and the last wall is shared with garage space.
The garage wall has been gutted, and air sealed by caulking the framing to the slab and the drywall to the studs. Receptacles facing the garage side were sealed with spray foam, and i’ve replaced the R-7.5 batts with R-15 Rockwool.
The two exterior walls are currently clad with 1″ of EPS and furred out with 3/4″ strips nailed into the block onto which the paneling was fastened. The electrical panel for the house is mounted on one of these block walls, which has caused me to take a step back and consider my options.
If i leave the 1-3/4″ of EPS/Furring in place, it leaves me with 3 inches before i’m flush with the panel. Less 1/2″ for drywall, and i’ve got 2.5 inches to play with. I’m hesitant to remove the existing furring because it seems i may destroy the existing EPS in the process of prying out the cut nails.
My options, as i see them are:
1. Leave the current assembly, and add a continuous layer of 1″ EPS, followed by a criss-cross grid of 3/4″ furring for running some additional electrical, then finish with 1/2″ drywall.
2. Pull the furring/EPS, and go with a full 2″ of Polyiso against the block, followed by a 2×3 stud wall, then drywall.
Would adding rigid insulation over the furring be of any benefit? or would it be problematic?
I also have some concerns with the way the current furring is butted against the slab, and will likely cut it back up the wall a couple inches to allow for some foam between the slab and furring/framing — especially if i’m going to use Polyiso.
Lastly — if I do employ a 2×3 wall, is it possible to install the Safe n Sound 3″ batts into a 2×3 wall cavity? If i understand correctly, part of the sound attenuation is derived from the 1/2 air gap created between the 3.5″ stud depth, and the 3″ roxul batt; however, i’m not concerned with the acoustic properties. Just curious if i could compress it 1/2″ further down to 3″ for a 2×3 wall. I believe they make a commercial 2.5″ product for steel studs, but it may be more difficult for me to get my hands on.
Lots of questions, but any help or advice is greatly appreciated.
regards, alex
GBA Detail Library
A collection of one thousand construction details organized by climate and house part
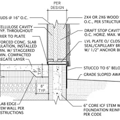
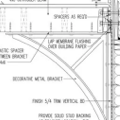
Replies
edit: Location is South Central PA, Zone 5
Alex,
In your Zone 5 location, you're aiming to achieve R-20 in your walls if you want to achieve minimum code requirements. You now have R-4. Adding another layer of 1-inch EPS gets you another R-4, for a total of R-8, plus a little bit for the air space.
Your other option (2 inches of polyiso) would give your about R-10 to R-12 for the polyiso, plus another R-9 if you insulate the proposed 2x3 wall. Call it R-19 to R-21 total.
Of the two options, the second option will perform much better from a thermal perspective, and will get you close to a code-minimum wall.
It's not hard to compress fiberglass or mineral wool batts. Even 3.5-inch-thick batts will go in a 2.5-inch stud space.
If it's continuous foam on the interior of a CMU wall, R17 would meet code minimum on a prescriptive-R basis in zone 5A as a mass wall with the the thermal mass exterior to the insulation. Using reclaimed roofing polyiso that would take 3" of foam, using Dow Thermax you can get there with 2.5" of foam. If leaving the R4 EPS in place, adding 2" of most 1lb foil faced polyiso gets you there, or 2.5" of reclaimed roofing polyiso.
https://up.codes/viewer/utah/irc-2015/chapter/11/re-energy-efficiency#N1102.1.2
Unless they glued the furring to the EPS most of it will stay intact when pulling the furring. Larger dings can be filled in with can-foam. Simply filling-in between the furring doesn't really cut it, since the furring is less than R1, and probably a double-digit percentage of the wall area. A single square foot of R1 passes as much heat as 5 square feet of 3/4" polyiso- it's not trivial.
If you're contemplated 2" polyiso + 2x3 studwall you have 4.5" to work with. Going with 3" of reclaimed roofing polyiso and 2x2 furring would also be 4.5", and substantially cheaper than 2" of virgin stock foil faced polyiso. Splitting and compressing R15 rock wool batts for the space between the furring would then bring it comfortably well ahead of code, with more than R21 at center cavity, more than a continuous R17 on the interior of the thermal mass an a U-factor well under U0.082 (code max for mass walls) , or U0.060 (code max for framed walls.), and higher performance than the proposed 2" of foil-faced polyiso + 2x3 rock wool studwall.
Martin/Dana,
Thanks for the quick response. I'll go ahead with pulling down the existing furring/EPS and start fresh with the continuous foam + studwall route. I also need to look locally for reclaimed polyiso. I was able to find 1" thickness sheets of JM polyiso for a reasonable price, but like the idea of reusing these materials.
Dana -- how easy is it to achieve a good split on the standard R15 rock wool batts? From working with it recently, i wouldn't think it would hold up that well once split open.
ab