Best/first crawlspace energy efficiency upgrade?

We recently purchased a home in climate 6B (zip code 83864). The spec of the house are as follows:
mid-2000s construction, single-story, ~2900 sq ft.
hydronic subfloor heating (electric tankless water heater and no heat transfer plates)
R-19 fiberglass faced batting in 12″ deep I-joists with ~4″ dead space between PEX tubes and batting.
vented crawlspace with minor moisture issues
About half of the flooring is thick-padded carpeting.
We are using significant amounts of electricity for heating and I am trying to determine what the first and or best step is for improving efficiency (also not spending a ton of money would be a plus). Projects I have considered include:
air-sealing the attic and subfloor penetrations and foam board/spray foam the rim joists
adding ~R12 batting to fill in the joist/PEX air gap to 1″
installing heat transfer plates and adding even more insulation
installing and taping rigid foam board underneath the I-joists
insulating and air sealing the crawlspace (unvented)
I have read a few books and countless articles (green building advisor being the best source of info thus far). If I missed any details or other possible projects, please let me know. Thanks for your help!
GBA Detail Library
A collection of one thousand construction details organized by climate and house part
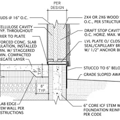
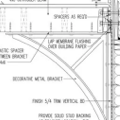
Replies
Jcer32,
Your home's heating system is unusually bad. The five biggest problems are the expensive fuel (electric resistance); the lack of heat transfer plates; the fact that outdoor air is being invited into the crawl space; the sloppy insulation job under the PEX tubing; and the carpeting above your subfloor. Except for those five problems, everything is hunky-dory.
Step number one is to convert your vented crawl space into a sealed crawl space. Here is a link to an article with advice: Building an Unvented Crawl Space.
I'm not sure what the next step is. If this were my house, I would be tempted to abandon the existing heating system, and to install a few ductless minisplits. The ductless minisplits would provide air conditioning as well as heating.
The heat transfer plates or stripping the carpet for a lower-R finish floor won't change the efficiency of the electric boiler based system much. It would allow the system to operate at a lower operating temperature which will lower distribution losses, but even in the vented unconditioned crawl space if the distribution plumbing is insulated the distribution losses are usually pretty small. If all of the heating system distribution plumbing were inside of conditioned space with heat transfer plates and lower R flooring the difference in the power bill would be measurable with some analysis of power use against heating degree day data, but most likely still only a single-digit percentage.
R19 under the floor is woefully below IRC 2015 code minimum, even WITHOUT the radiant heat. After air sealing, bumping the joist to as much insulation that will fill the space under the 4" air gap would be in order, unless you'ver already committed to converting the crawlspace into conditioned space (which is worth it in the long term, but not the biggest most immediate return on investment.)
To start:
If the boiler has an outdoor reset features- use it, run the system at the lowest temperature that still covers the heat load.
The place to start spending MONEY is insulating any uninsulated distribution plumbing, which is pretty cheap.
Finned convective heat exchangers (eg: Ultra-Fin) may be retrofitted to further lower the operating temperature for much less money than heat transfer plates. Consult the installation guides to see if the way the tubing is currently suspended is going to work. ( http://www.ultra-fin.com/wp-content/uploads/2015/06/Ultra-Fin2013manual-WebHi.pdf ) It's not worth ripping the tubing out and re-configuring it for this upgrade, but if they can be clipped on prior to beefing up the insulation the system will be more responsive, and distribution losses will be lower.
Spending the bigger money on turning the crawlspace is still worth it, but you'll still get more immediate (and bigger) bang/buck out of high efficiency mini-split heat pumps, which would use less than half the power than the radiant system even if the radiant system was perfect, and already fully inside of conditioned space. Running the radiant system with a floor thermostat and letting the heat pumps set the room temperature is usually an excellent compromise, still cushy warm barefoot comfort, with the bulk of the heat being delivered by the heat pumps.
Thank you both for the quick responses. A few clarification details that may help: Our first step upon moving in was to install a wood-burning stove (we live in an area prone to power outages and electricity was the only heating source). In the first month of running the fireplace daily, we noticed a $130 decrease in the electric bill with an average daily temp 6F colder than the previous month. Normally, only one of the three zones turns on (furthest from the stove) as most of the house consistently stays above the thermostat setting (67F).
The tankless water heater is an Ecosmart ECO36, so no outdoor reset feature. The distribution piping and water heater is in an unheated garage, about three feet from where it enters into the insulated joist bays. The joist bays only have 3" of fillable free space before you get into the "must maintain at least 1" air space between insulation and radiant tubing" region. This is why I mentioned installing and taping rigid foam board underneath the I-joists; thinking maybe get more R value and additional air sealing.
It seems the consensus is to seal and condition the crawl space, then install mini-splits? With those additional details, does that change your recommendations?
Thanks again for your help!
Jcer32,
Can you tell us your name?
Q. "It seems the consensus is to seal and condition the crawl space, then install mini-splits?"
A. Correct.
Q. "With those additional details, does that change your recommendations?"
A. My recommendations remain unchanged. Good luck.
In the dry winter air of Idaho you can expect a right-sized ductless mini-split to only use 1/3 the amount of electricity on average that the current system does, and only 1/2 as much even during the coldest weather, about 1/4 as much when it's in the 40s or higher outside. While insulating and sealing the vented crawlspace will STILL be worthwhile even at mini-split efficiency, there's no way lowering the radiant floor's operating temperature with heat exchanger plates and insulation/encapsulation upgrade strategies would come anywhere close to level of improvement.
Putting it another way, spending $5-10K on mini-splits will have a FAR greater impact on the power bill, cutting it by more than half,co compared to spending than $5-10K of crawlspace insulation and tweaks to the existing system, at most a ~25-30% savings, even if you did ALL of it including continuous R15 crawlspace walls, a better boiler with outdoor reset mounted inside of an insulated closet with heat spreaders on the tubing to lower the temperature requirements, etc.
Regarding those other improvements...
If you take the trouble to move the tubing up to the sub-floor with sheet metal heat spreaders (cheaping out is fine here), the insulation can be (and should be) snugged all the way to the top with no gap. Even dense-packing would be fine. IRC 2015 code min for floors over unconditioned space (even without heated floors) is R30, and 12" of dense packed cellulose would give you R45-ish.
If you're leaving it as suspended tube (with or without convecting fins) you'll have enough vertical space for R30 rock wool, which are nominally 7.25" thick, and are dense enough to be fairly air retardent.
Unfortunately batts are designed for 1.5" framing and nominally 15.25" designed to be a friction fit into a 14.5" nominal cavity width. They're not quite wide enough for a snug fit in to 16" o.c. I-joists. But it'll still work if they're cut carefully to 16" lengths. Rock wool designed for 24" o.c. framing are 23" wide, 47" long. If cut in to thirds each batt piece will be 23" x 15.67", which might make it depending on the web thickness on the joist, or not. adding an inch strip to every third chunk. It'll still need an air barrier on the bottom- housewrap would be good enough, and would allow drying into the vented crawlspace.
With the boiler and distribution plumbing inside an unheated garage you have the option of building a fully insulated cabinet or boiler-closet to bring the boiler (electric tankless) and plumbing fully inside of conditioned space. For less than $1500 you can get an electric boiler of comparable output to your ECO36 that has outdoor reset (eg: Electro EB-MX-10), but there's still much better bang/buck out of applying those funds toward heat pumps. In the mean time you can experiment with reducing the temperature setting on the tankless by 5F at a time until it no longer keeps up with the heat load at sub-zero temperatures, then bump it back up a couple degrees at a time until it does.
But seriously, in order of cost effectiveness (beyond the cheap stuff such as insulating the distribution plumbing or turning the temperture down):
1: Install ductless heat pump(s) right sized to cover the load of the primary heating zone(s)
2: Seal & insulate crawlspace to IRC 2015 code minimums or better (R15 continuous wall insulation. If you insulate the crawlspace there is no need to up-grade the R19s in the floor.) If #1 is executed first this will still be saving 15-25%, but 15-25% of an already much-reduced number, provided you use the radiant only as the backstop for the heat pumps, or operate it off a floor-thermostat at some reasonably low temperature (say 72F max at a 70F room temperature) rather than operating from a room air thermostat.
3: Replace the tankless (not really designed for heating system flow rates) with a more appropriate electric boiler that has an outdoor reset function.
4: Build insulated boiler room/closet to IRC 2015 code min (2x4/R13 + R10 continuous insulation)
5: Install better heat coupling on the radiant floor to lower the operating temp.
Getting a third-party (not HVAC company) engineer or RESNET rater to specify the room by room heating loads of the whole house with "before" and "after" insulation upgrade numbers, then getting quotes on #1 properly sized for the "after" picture would be the first order of business.
The rest is all frosting on the cupcake, and you might opt to just mothball it as the "Hail Mary" backup system in the event of an extreme cold snap or a heat pump failure. Installing the ductless heat pumps prior to insulating the crawlspace is fine, even if it means you have to run the radiant floor more to stay warm during cold snaps.