Best exterior foam 2×4 wall and 1/2-inch sheathing system

Looking for some comments on the best way to insulate my addition with the highest R-value possible for my situation and climate area (in New England).
GBA Detail Library
A collection of one thousand construction details organized by climate and house part
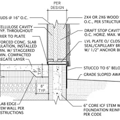
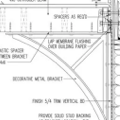
Replies
William,
The highest R-value possible? That would be unaffordable. In any case, most experts agree that it isn't worth exceeding R-40 for walls in New England.
One good way to create an R-40 wall is with double-stud walls with a total thickness of 11 or 12 inches. This type of wall is usually insulated with dense-packed cellulose.
If you insist on having a 2x4 wall with 1/2-inch exterior sheathing, the best method would be the PERSIST approach with 6 inches of exterior polyisocyanurate foam. This type of wall would have an R-value of R-39 if you left the 2x4 walls uninuslated, or about R-50 if you insulated the stud bays.
For more information on the PERSIST system, see Getting Insulation Out of Your Walls and Ceilings.
Perhaps taking too fine a spin on it, in a New England climate 1.5lb iso can't be counted on for anything better than R6/inch for average seasonal performance, and when it's 0F outside, 68F inside that 6" layer wouldn't do better than ~R34, best case, even if it's closer to R6 when it's 50F outside, and even if it's ASTM C518 rated R-value is more like R6.5/inch. For thinner layers where the foam is less than half the total center cavity-R, derate to R5.5/inch @ 0F
In a New England climate, if it's half the R value or more the derating isn't very relevant from a dew-point control point of view, but when it's less than 1/3 of center-cavity R it can be, particularly in the colder parts of the region.
Alternatively...
A wall framed with 2x6 @ 24" o.c. would have about the same board-feet of lumber and structural capacity as a 2x4 studwall 16" o.c. (and fewer boards to cut- by rights it should cost less ;-) ) and with a damp-sprayed cellulose cavity fill (or open cell foam) delivers about ~R13-R14 "whole-wall" after all the thermal bridging is accounted for. After that it only takes ~4.5" of exterior iso to hit a whole-wall R of R40, usually at somewhat lower cost than a 2x4 + 6" iso approach.
With either, using reclaimed fiber-faced roofing iso (typically 2lb density, somewhat more rugged than foil-faced goods) from commercial demolition & re-roofing is both cheaper and greener than going with virgin-stock goods. (There are several outlets for reclaimed goods in New England) Going with a layer of reclaimed goods next to the structural sheathing, then using a layer of foil-faced goods on the side facing the rainscreen, (staggering the seams between layers and sealing the seams of each layer separately for better air tightness) gives a small but measurable performance boost from the low-E aluminum facer. ( Aluminum facers are also easier to air-seal reliably with FSK tape.)
My planned wall system from in to out,
1/2 Sheetrock
Caulk and seal all joints and cracks with air seal foam and or silicone
2x4 wall cavity with R-15 batt, un-faced insulation
All windows and doors wrapped with grace window/door material
Tyvek house wrap, tapped and sealed to windows and doors
1 1/2 foam board xp R-7.5
Vinyl siding installed over foam
Floor and ceiling will be an R-40 or better
My other question is would my wall system I spelled out above, be Sufficient enough to stop condensation, to have air flow for condensation if it happens.
Just a word of caution (maybe) on reclaimed foam; I have not verified this from any other source, btw. A building science individual told me to avoid reclaimed foam from roofers up here, as it often has been exposed to leaks. Leaks result in, perhaps several, freeze/thaw cycles that eventually denigrate the integrity of the foam. Although the foam is still "water proof", the freeze-thaw cycles create a multitude of voids in the foam and it will be very susceptible to water down the road, killing its R value, if nothing else. FWIW....