Best budget wall assembly?

Building in Zone 4C marine and looking for a budget efficient wall assembly.
Climate here is not extreme, so I do not plan on having a 4 inch foam wrap or anything the colder zone people will do. But stopping thermal bridging in some fashion seems like a no-brainer.
SIPS are off the table, and i’d like to avoid spray foam if possible.
Any ideas? thanks
GBA Detail Library
A collection of one thousand construction details organized by climate and house part
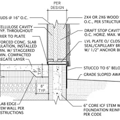
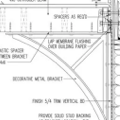
Replies
2x6 framing 24"o.c. is about as cheap as 2x4 framing 16"o.c. (the minimum required to support one floor above). It provides a deeper space for insulation, a big plus. You might need 16" o.c. to support your chosen siding material.
R-19 fiberglass batt insulation for 2x6 framing isn't the highest performing insulation, but is very cheap. It may be code minimum for your town or county. Be careful to install the batts as tightly as you can. Empty spaces are a worse thermal bridge than framing (and may allow some convective heat loss as well).
I'd suggest plywood sheathing, despite being somewhat more expensive than OSB, since it has better drying potential and is more resistant to damage from water and water vapor.
House wrap is a cheap but effective air barrier. Typar seems rated better than Tyvek but the latter is cheaper.
Especially in a rainy, humid marine climate during winter like the Pacific Northwest, a rain screen assembly is a must to minimize water intrusion and enable better drying potential in your wall. I'd suggest adding a layer of polyiso or EPS foam, then the rainscreen. Used foam is very cheap, and recommended over and over in these Q&A's. It would provide more insulation and reduce thermal bridging through the wall framing. The rain screen itself can be 1x4 or plywood cuts. Only a quarter of an inch does okay, though most people use 3/4" 1x lumber. It doesn't need to be pressure treated lumber, as it will typically stay dry. Some may suggest a crinkled house wrap product, thereby skipping the rain screen, but those products cost more than Tyvek/Typar, and may not be as effective a rain screen.
Joe, in your climate zone, the IRC requires either R-20 cavity insulation or R-13 cavity + R-5 continuous insulation. Assuming fibrous insulation and 16" o.c. construction:
Standard 2x6 construction meets code but yields about R-18.6 if you include studs ("center-of-wall" value), not considering posts, headers, plates, etc., which further lowers the wall's average R-value.
Cross-strapping a 2x6 wall with 2x2s on the interior increases the center-of-wall value to about R-23.7.
Framing with 2x8s yields an R-24.5 for center-of-wall. That's more than 30% better than standard 2x6 construction, similar labor costs (though the wall will be heavier to lift) and almost certainly less than a 30% upcharge for materials. If I were you, I would lean toward this option.
The easiest place to locate the primary air barrier is usually at the sheathing. Commodity OSB is not always airtight, but Huber's ZIP system makes a good sheathing, air barrier and WRB all in one shot. Or CDX with taped seams and any WRB also works well. Just be sure to use a rainscreen gap, the thicker the better, to allow drying. For extra insurance you could add a variable permeance membrane at the interior, but if it strains your budget, painted drywall is enough, as long as the sheathing is airtight and there is a robust rainscreen gap.
As for foam, you could wrap the exterior with it, as Robert suggests, but even if you get used material, it makes other aspects of construction difficult, and I don't like any aspect of working with it, or introducing foam dust into the environment (or my lungs).
Rock Wool Comfortboard and Budget don't go together, do they?
Nope.
But the upcharge for R23 ComfortBATT in your 2x6/ 24" o.c. advanced framing/optimum value package isn't huge.
Doing it with 2x4 16" o.c. and putting 1" polysio + 1x strapping "Bonfiglioli" strips and intstalling R23 rock wool (performing at R22 at the 5.25" cavity depth) is comparable to 2x6 R23 + R4 continuous insulation type performance.
https://www.finehomebuilding.com/membership/pdf/9750/021250059.pdf
Cutting the 1" foil faced polyiso into 1.5" wide strips is quick , clean and easy using this method:
https://www.finehomebuilding.com/2009/01/29/theres-a-better-way-cutting-rigid-insulation
Unfortunately I don't think this one will be advanced framed. 2x6 @ 16"OC most likely. Interesting idea with the Bonfiglioli strips. I Imagine this+ dense pack cellulose would perform similarly.
Dense packed cellulose would have a lower center-cavity R value than rock wool, and would be more expensive too. But the thermal mass of the cellulose gives it a modest performance boost too, so yes, the overall performance would be similar.
Thanks Dana,
A couple things to clear up.
Is the 2x6 standard only to achieve the R value? Can I replace any 2x6 for a 2x4 if I then add thickness with the strips to the interior. I would of course talk to my engineer about this but is this generally true?
Do you not factor in that dense packed cellulose, if applied properly fils gaps better than the rock wool batt? Therefore leading to better performance?
It is possible to use 24" OC stud spacing without utilizing other Advanced Framing techniques. If you use a double top plate, you do not have to worry about lining up the studs between floors, which is what most bothers people. You can even use 16" OC floor joists with it if you want.
I'd get a quote on damp sprayed cellulose.
Joe,
Personally on my own house, I'd prefer to do a self-install of rock wool batts vs. fiberglass batts, but you were asking about "best budget" wall assembly. Dana notes rock wool is a small upcharge, which in the greater scheme of things is true. However, the actually cost difference for this is pretty large (perhaps triple the cost, fiberglass batts are dirt cheap). Rock wool yields a higher R-value so some of that cost difference pays off in reducing the cost of exterior insulation, cross-strapping or 2x8's. Tighter fit and better sound-suppression too. Rock wool will compress into tight spots better than more flimsy fiberglass batts.
Dense packed cellulose would certainly do a better job filling every spot in walls with plumbing pipes or in odd-shaped cavities. Cutting batts to fit is a chore and won't fit that great around pipes unless you are a perfectionist. But how would mixing dense packed into walls with foam "Bonfiglioli" strips work during installation?? Installing highly packed cellulose in one cavity may blow out those strips into an adjoining empty cavity, not to mention problems fastening the cellulose netting (or drywall) to and through those foam strips. Doesn't seem like a combination that works easily. You could follow Michael Maines suggestion of interior cross-strapping or 2x8's, then use cellulose, but again not cheap. You also have to pay for an installer with better equipment for dense pack cellulose, but can self-install batts if you are an owner-builder on a tight budget.
Ultimately you have to decide how much you are willing to pay for these upgrades, as well as your personal construction preferences. Lots of ways to build a code-compliant or high performance wall.
Budget means very different things different people depending on goals and time frame and sweat equity.
If you are flipping a house and the plan is to own the house for a few weeks, budget is the lowest cost item code enforcement will allow.
If you plan to own this house for the next 60 years and believe the new green deal is a done deal in 4 years funded totally by fuel taxes, 10X your current heating fuel costs. R60 wall begins to sound budget friendly.
Question 1: How long do you plan on owning this house?
Question 2: Is this a new build project?
Question 3: Are you paying someone else to install the insulation or is this DIY?
For my new build 2x6 16 on center filled with wet spray cellulose and 1 inch of foam sheet over the zip board was my choice.
I found BEopt very use full in selecting between options.
https://beopt.nrel.gov/
Walta
Thanks Walta,
Owning the house could be anywhere from 5 to 30 years, not a spec house.
Yes this is a new build.
I always figured I would hire out the insulation but that's because I basically ruled out batts. But if I can do them way cheaper myself then I am open to it. I am a details type of guy so I could do a tight job with batts I am sure. If I did choose batts I would like to use rock wool, but at triple the cost it makes me wonder where the cellulose contractor comes in
Insulating beyond code R20 is a long term bet as potential buyers are very unlikely to see it as added value and any return from energy saving on that investment is way out there in years.
I decided to pay and have most things done by the contractors. My thinking was it would likely take 10 times as long for me to do the work and I saw greater value in keep the project on schedule.
The quality of the wet spray cellulose was great. I had some fiberglass bats that looked ok before drywall but they look terrible in the inferred photos.
Walt
>"Is the 2x6 standard only to achieve the R value? Can I replace any 2x6 for a 2x4 if I then add thickness with the strips to the interior. I would of course talk to my engineer about this but is this generally true?"
It's generally true. Standard 2x4 16" o.c. framing with plywood or OSB sheathing meets all the structural requirements. Adding the edge strips for a thermal break and greater cavity depth for insulation improves the thermal performance. A 2x6/R20 meets the IRC code minimums, but an R6 Bonfiglioli solution with R22 cavity beats those minimums at modest uptick in construction costs.
>"Do you not factor in that dense packed cellulose, if applied properly fils gaps better than the rock wool batt? Therefore leading to better performance?"
A truly bad batt installation will underform cellulose, but it's possible to do batts carefully enough to get the full performance out of them. Either batts or cellulose would have to be inspected for the quality of work before closing it in with wallboard.
I like the idea of the Bonfiglioli framing. . It hasn't been taken up by builders because it is so labour intensive. It will probably remain one of several viable upgrades for owner-builders as a niche technique for those whose time doesn't have a market value - unless someone manufactures a ready-made product. There were several manufacturers making thermally broken studs a few years ago, but they seen to have disappeared.
So with the Bonfiglioli technique, would it be advantageous to start with 2x4 framing as opposed to 2x6 so you don't start creeping into your interior square footage?
on the other hand, If left as 2x6 it leaves the owner/builder all the options if you decide not to go that route, and just gives you a deeper wall in the end for a higher r-value
Joe,
These folks went trough the cost of a bunch of walls:
https://www.homeinnovation.com/~/media/Files/Reports/Extended%20Plate%20and%20Beam%20Wall%20System%20-%20Summary%20of%20Initial%20Assessment.pdf
Lot of options there, pretty much comes down to what your builder will build. For DIY build, all wall assemblies are pretty easy, so just go with the one you prefer (except for exterior rigid mineral wool, that is a PIA).
My only recommendation is it is best to stick to standard thickness so you can use off the shelf doors and windows (ie 6 9/16" or if getting brickmolds you can go up to 7 1/2").
Denspacking thin walls is expensive, better off to stick to batts.