Batt and Flash (inside out)

After meeting with insulation contractors the last few days, I received the Feb/Mar 2011 FHB with the “Flash and Batt” article. Timely!! But the dew point concerns are sobering… So how about reversing the assembly, where the project details permit?
I am gutting a 1930 balloon framed house, 1400 SF in Rhode Island (zone 5A I think, though there seem to be a number of climate zone mapping schemes…)
Considering spray foam insulation in the walls, 2×4 plus 1″ furring, for a tight seal, full thermal break inside the studs, about R-15. Thicker on the north side.
The attic will be unheated for now, with plans to expand, insulate, and finish it as a 3-season room in “phase II”. Basement is unheated shop space. So I am thinking, how about “Batt and Flash” for basement ceiling and attic floor? 1″ foam against the warm surface, to seal the assembly, with thick fiberglass batt insulation in the cavity. Would this address the vapor issue? Any downside, or detailing to consider?
Also, spraying the wide-open 2×4 bays full of foam, is firestop required between floors? Or does the foam serve that purpose?
Thanks
GBA Detail Library
A collection of one thousand construction details organized by climate and house part
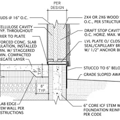
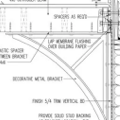
Replies
Curtis, the current EPA climate zone map is at the start of the Q+A section here at GBA. It is different from older EPA climate zone maps, and different from climate zone map for agriculture, from the USDA.
If you are doing a gut rehab, inside and out, there are several good alternatives to flash and batt. There are advantages to installing the foam on the outside of the wall assembly, where it will keep the framing warm and dry. There are advantages to putting the foam on the inside of the wall assembly, where you don't have to worry about water vapor as much.
Your "batt and flash" approach is an excellent way to insulate attic floors. The only downside is air washing reducing the insulating ability of the batts, so you might do blown cellulose instead, over an air barrier of sprayed foam.
In your basement, if at all possible it's usually better to insulate the walls rather than the ceiling.
2 1/2" of fiberglass over foam is considered an ignition barrier, as long as the fiberglass is unfaced. It's always a good idea to install solid fireblocking between floor levels.
Thank you, Michael
Flood zone issues make a finished basement impractical, hence the plan to insulate the ceiling.
As noted, the attic will be finished in the future, with insulation in the roof (approx R-26) as well as floor (approx R-26) for "3-season" use, as well as occasional guests for the winter holidays. A weatherstripped door or hatch will separate 2nd floor from attic. Are there issues with this approach?
Thanks again
Sorry, missed the plan to finish the attic in the future. I have no idea how to finish an attic as a 3-season room; it's hard enough getting the details right on a fully conditioned attic or a vented attic.
I would suggest doing it right and making the shell of the building your thermal barrier; in other words, insulate the roof properly. Filling the attic floor with fiberglass (or even better, dense-packed cellulose) will help you in the short term and won't hurt anything in the long term.
If you want to insulate your first floor, you can spray foam against the floor sheating and fill the remainder of the cavity with another insulation product. Sealing up any air leaks is important. Alternatively, if you have the headroom, you might do a layer of rigid foam below the joists and fill the cavity with cellulose (after air-sealing, of course).
Michael,
Intriguing. You say the 1” spray foam and batt insulation is “an excellent way to insulate attic floors. The only downside is air washing reducing the insulating ability of the batts, so you might do blown cellulose instead, over an air barrier of sprayed foam.”
Would this work in a ventilated attic with roof trusses? I’m aiming for R-50 if possible. How many inches of spray foam (and what type?) should be sprayed onto the exposed top side of the GWB ceiling, followed by R-38 batts laid on top? Or if blown cellulose is used to combat air-washing, what’s the best ratio of each material? Is this cost effective? House is in climate zone 5A (Albany, NY).
Thanks.
Laura, as long as you're in a heating climate (such as zone 5A), and the foam is on the warm side of the assembly, there is no minimum thickness of foam or an ideal ratio of foam to fill. 1" of closed cell foam provides an air and vapor barrier, and is about the minimum that foam guys can spray. The more foam you use, the better your insulation will be. It's only when the vapor barrier is on the cold side of the assembly that you have to pay close attention to thicknesses and ratios.
Batts really don't work very well as attic floor insulation. There are too many gaps around each batt, no matter how well they are installed, and they don't block air movement. Air movement means that the warmth trapped by the insulation is being sucked out by wind or drafts. Blown fiberglass or cellulose are better because there are no gaps, and cellulose blocks air movement to some degree.
Whether or not it's cost effective depends entirely on who is doing the insulating, and what the exact conditions are of your project. It's quite possible that your best value will be in hiring an installer with good attention to detail to seal problem areas with canned foam and caulking, then blowing in piles of cellulose. Or you might find that an installer can do your project entirely with closed cell foam for less than you might think.
Closed cell foam averages about R-6 per inch (depending on mgfr claims); loose-blown cellulose and fiberglass average about R-3.2/in.
"as long as you're in a heating climate (such as zone 5A), and the foam is on the warm side of the assembly, there is no minimum thickness of foam or an ideal ratio of foam to fill."
That is not true. Although I don't know why you explain foam in a flash and batt system as "on the warm side of the assembly" a condensing surface is a condensing surface. The thickness of the spray foam layer should absolutely be considered. Martin has covered this in a couple of his blogs-- I can't find them but I do know the colder the climate the thicker the foam. Knowing that its impossible to get a consistent 1" layer of foam throughout the assembly, most experts would specify 1.5 inches of closed cell foam at the very minimum in climate zone 5 (I actually would specify 2" if I was building the home).
Brett, you're absolutely correct, in a "conventional" flash and batt installation, except that in a roof or attic floor you should have more than 2" of foam. What Laura is talking about is a bit different.
Imagine you're standing in a conventional attic, with sheetrock already installed on the ceiling of the living space below. You're on the cold side of the assembly. Looking down you see floor joists and the back side of the sheetrock. (if you're in the northeast, you also see strapping.)
Spray one inch, three inches, or ten inches of foam between the joists, against the drywall. Then blow as much loose insulation over the foam as you want. The foam is on the warm side of the assembly, and it doesn't matter how thick it is, you won't have condensation problems. It's not considered an air barrier until it's an inch thick.
Here's an article some guy wrote, explaining the basics of flash and batt: http://www.finehomebuilding.com/tool-guide/articles/why-flash-and-batt-makes-sense.aspx?ac=ts&ra=fp.