Bathroom remodel – mold on exterior OSB
Hi all,
We have recently begun remodeling our master bath.
We have recouped space from a not-so-walk-in closet next to ththe bathroom and installed a tile shower and tile flooring.
We redid the ceiling drywall with 5/8 mold resistant drywall as well.
We would like to put nickel-gap shiplap up on the walls in the bathroom.
I want to use 1/2 PVC boards to make my own and attach it directly to the exposed studs (no drywall). My thought being that I would have no issue with wood absorbing any moisture.
The bathroom has 3 walls interior to the house and 1 that is an exterior wall.
The exterior wall consists of vinyl siding, house wrap, 1/2 OSB, 2×6 studs, R19 unfaced batts, and 6 mil poly. It had drywall on it, but we removed it during the remodeling.
When I was inspecting the batts, I found mold on the interior side of the OSB.
We live in north central WI, right on the 6B/7A line.
I’ve read through these posts on the mold subject:
https://www.greenbuildingadvisor.com/blogs/dept/qa-spotlight/why-sheathing-moldy
https://www.greenbuildingadvisor.com/community/forum/general-questions/30654/cold-sheathing-condensation-mold
I was planning to use Sporicidin to deal with the mold.
I am contemplating doing a flash and batt method to insulate the exterior wall, but I’m unsure if I should then reinstall poly on the interior of the studs.
I still have a couple of questions:
1) Thoughts about using Sporicidin to deal with the mold? Alternatives? Another consideration on this point is the time of year, we are currently in the 40s up here.
2) Most appropriate method to insulate and create the air barrier on this exterior wall once the mold is dealt with?
3) Other thoughts?
Thank you for your time,
Brian
GBA Detail Library
A collection of one thousand construction details organized by climate and house part
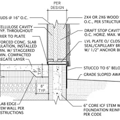
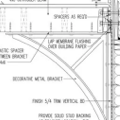
Replies
Brian, I would either skip the flash-and-batt and stick with well-installed batts, with a variable-permeance interior membrane (Pro Clima Intello, Siga Majrex or Certainteed Membrain) or skip the vapor retarder and make sure you are generous with the foam in a flash-and-batt approach. I can't advise on the Sporicidin.
Thanks, Michael.
I appreciated your time. I was reading about barrier options since I posted and had gotten confused about which to use, poly or a variable product. You must’ve read my mind.
As far as the R value of the batts goes, would it be best to use some R-30 up here in the north woods?
Michael has a Fine Homebuilding article on this topic: https://www.greenbuildingadvisor.com/sites/default/files/Why%20Flash%20and%20Batt%20Makes%20Sense.pdf
But maybe he has some additional thoughts on the topic since it was published in 2010.
You can do the spray foam yourself and add interior side mineral wool to reduce thermal bridging. Or even 1" unfaced EPS on the interior side.
No poly or anything else that is fixed low perms (PVC?) on the interior side.
Steve, thanks for linking to that article. Nothing has changed science-wise, but there are now closed cell spray foams with more environmentally friendly blowing agents, and the cost of spray foam has come down quite a bit (or more accurately it has held steady while everything else has gotten more expensive). The 2015 IRC code has a handy table for determining the required ratio of impermeable to permeable insulation, table 702.7.1: https://codes.iccsafe.org/public/document/IRC2015/chapter-7-wall-covering. It requires a bit of reading between the lines; basically, in zone 7 you need at least 42% of the R-value to be on the exterior side, whether in a flash-and-batt or a continuous exterior insulation arrangement. With the high vapor pressures of a bathroom I would err on the side of caution.
I had missed the detail about the PVC cladding on the interior. Where you're in a cold zone, with an impermeable interior surface, the safest approach would be to either fill the framing cavities with closed cell foam, or use permeable insulation only, allowing drying to the exterior.
As for total R-value, I would use at least the code-minimum amount, roughly R-25 for cavity-only insulation (using the U-factor alternative approach). The Pretty Good House approach in cold climates calls for R-40 walls, although using energy modeling I'm finding that the benefits drop off significantly after R-30.
Thanks to all for the replies, I’ve found it very informative.
One last question regarding cleaning the mold.
It is currently 30F here. Obviously not ideal conditions for removing insulation and spraying liquid on the OSB, but I need to get this project completed.
If I’m using waterborne borax solution, am I safe(ish) with spraying and cleaning the mold in these conditions? Should I wait a period of time before putting up the insulation and Membrain once finished?
Thanks,
Brian
This should be useful for dealing with mold:
https://www.greenbuildingadvisor.com/community/forum/general-questions/26895/dealing-mold-inside-osb-sheathing
Also this one (includes "Borates alone are only marginally effective
at controlling mold fungi"):
https://www.fpl.fs.fed.us/documnts/pdf2004/fpl_2004_clausen004.pdf
I would only use a no-foam wall with cellulose and monitoring of indoor humidity (eg, < 40% all Winter). Spraying foam on the OSB will be more robust.
I really appreciate all the input. Information overload for my brain.
So here is what I think I've gleened and a couple final questions:
1) I will clean the mold
2) reinsulate with R30 batts
Question:
1) Is it ok to clean this mold with a waterbound method in this cold weather? How should I go about drying it out?
2) Should I prep the OSB surface with something before reinsulating?
Thanks,
Brian
Brian, mold remediation requires specific training. If you're concerned, you could contact a local mold remediation company. (ServePro, ServiceMaster or similar.)
If it was my own house I would probably just spray it with some diluted bleach and keep the heat cranked while it dried out, but I don't have training in this area.
Thanks Michael. That was my initial thought as well.