Basement – XPS insulation without drywall

I am in the planning phases of my finishing a basement in a home built in 2014 with poured concrete walls. Located in Indiana, near Chicago, climate zone 5. I plan to do most of this with 2″ XPS on the walls, 2×4 framing, then covered in drywall. There are a few places where this won’t always work, such as building closets around the sump pit, water meter, etc. Should the XPS insulation be continuous (this would make sense to prevent condensation on the wall), or should it be excluded in these closets (this makes sense because its not covered in drywall for fire protection)?
Also, this is an L shaped basement, and the long part of the L will be finished, and the short leg will be not finished and just for storage and furnace/water softener/etc. Can I avoid insulating this area?
GBA Detail Library
A collection of one thousand construction details organized by climate and house part
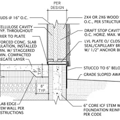
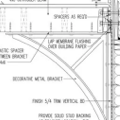
Replies
A few comments:
At 2" of XPS doesn't even meet IRC code min for US climate zone 5 where you're located (R15 continuous insulation does). The warranteed R-value is only R9 (90% 0f labeled performance), but as it's extremely high global warming potential HFC blowing agents diffuse out over time it's performance drops toward R8.4 at full depletion, the same performance as EPS of similar density. EPS is blown with comparatively benign pentane, most of which leaves the foam and recaptured while still at the factory, and has a stable R-value over time.
To hit code min performance would require either installing fiber insulation in the studwall, or installing 3.5" of EPS/XPS.
At 3" roofing polyiso (also blown with pentane) would run R16.5- R17, beating code minimum. Using reclaimed roofing polyiso is even better- it's dirt-cheap, and unlike polystyrene (EPS/XPS) it doesn't melt into a flaming puddle of liquid if there were ever a fire, but would char in place. There are several foam reclaimers in the Chicago & N- Indiana area, some of whom advertise here:
https://chicago.craigslist.org/search/sss?query=rigid+insulation
https://southbend.craigslist.org/search/sss?query=rigid+insulation
https://fortwayne.craigslist.org/search/sss?query=rigid+insulation
If instead of a studwall 3" foam were strapped to the wall with 1x4 furring through-screwed to the foundation with 4.5"- 5" masonry screws the wallboard could hang on the furring, taking up less interior space than 2" foam + studwall.
When using polyiso it's prudent to leave a gap between the cut bottom edge of the foam and the slab, since it can wick moisture if the slab is damp, or in the event of a minor flood. If going with a studwall, installing 1-2" of EPS under both the bottom plate of the studwall and the foam, leaving a half-inch gap between the EPS and foundation as a channel for bulk water is a sufficient capillary & thermal break. If there is a history of flooding, stop the polyiso at the high tide mark and continue down with EPS of the same thickness.
Even unfinished unheated parts of the basement represent a substantial heat loss. Even when it's 50F in the uninsulated portion of the basement and 0F outside every square foot of uninsulated above-grade foundation is losing more than 30 BTU/hr, and the below-grade wall is also losing heat (but at a steadier rate that varies more slowly with season). So a 40' of wall with 2' of exposed foundation has 80 square feet and a heat loss of more than 2400 BTU/hr just on the above ground section, and a comparable amount on the below grade 3/4- call it 5000 BTU/hr. Just that 40' section of uninsulated wall is more than 10% of the whole house heat load of a typical 2500' house, even though it's not being directly heated. Insulating that section of wall to IRC code min would reduce that load by more than 90% to about 500 BTU/hr- the amount of heat an adult human emits during an exercise workout.
During the summer the outdoor infiltration air has a dew point higher than foundation, which leads to mold growth and "musty basement smell." With an insulated basement wall the wall's surface will average a much higher temperature and would be less susceptible to those moisture accumulation issues.
So while you could avoid insulating the unfinished area (it's not required by code in a retrofit, only new construction), it's still in your best interest to insulate it and put up some drywall, even if you never paint it.
Dana,
While he does not mention it in his post, Garret includes a diagram showing 2" EPS on the exterior of the foundation. Combined with the 2" of foam on the interior, I believe it will be sufficient to meet code.
I have 2" EPS on the outside of the wall and also plan to add fiberglass insulation, so I think my total R value will be more than sufficient. I have read XPS is preferred internally to EPS or polyiso, due to it's permeability?
> have read XPS is preferred internally to EPS or polyiso, due to it's permeability?
The vapor permeance of XPS is lower than EPS, and at 2" would be less than 1 perm, comparable to paper or fiberglass faced roofing polyiso (any thickness). At 2" Type-II EPS (1.5lbs per cubic foot nominal density) is less than 1.5 perms, tighter than latex paint on wallboard, and not a problem. At 2" Type-VIII (1.25 lbs nominal density) is less than 1.8 perms, still at least twice as tight as latex paint on wallboard. From a moisture point of view at 2" it simply doesn't matter what foam you use in your stackup.
With 2" of EPS on the exterior 1.5" of roofing polyiso or 2" of EPS on the interior would meet code without the fiberglass, and no interior side vapor retarder tighter than standard interior latex would be needed for R11-R15 batts.
I do not see the advantage if having half the insulation on the outside and half on the inside. If you are going thru the trouble of put any insulation on the outside and covering it up there is no more labor to make it thick enough to do the job alone.
Walta
Insulation on the outside was put in by the builder of the house, I had no input on this. If I did I probably would have used XPS and made it thicker. I purchased the house after it was built.
Using EPS on the interior would be great, much lower cost compared to XPS.
Does the exterior XPS extend all the way up to the top of the foundation, or is this one of those where the foam ends at-grade?
If it stops at grade the fiberglass will be necessary to hit code min performance.
Most insulated concrete forms are made of Type-II EPS. Several vendors' product lines start at 2.25" + 2.25" (R19-ish) or 2.5" + 2.5" (R21-ish), though it's still possible to get 2" + 2" (~R17)
This is 2" EPS that was put against the walls after they were cast. It extends only up to grade.
I have already put 2" XPS + fiberglass insulation in the rim joists.
So assuming I use XPS or EPS on the inside of my walls, can I use it inside of my sump pump closet (see diagram)? It's not covered directly by drywall, but there is a drywalled closet in front of it.
Bump
You can use Thermax or mineral wool wherever you can't cover the foam with drywall. Or skip the interior foam and live with the increased heat loss.
Question about polyiso. I've seen many mentions of polyiso performing worse than XPS and EPS as temperatures get colder (EPS and XPS R value increases as temps go lower). For a US climate zone 5 like this install (and my situation), is polyiso a worthy alternative to XPS and EPS given how its R value drops with temps (and time)?
XPS R value also drops with time, so don't consider XPS to be superior to polyiso in this particular respect. EPS is the only one of the three that holds it's R value over time.
Polyiso provides quite a bit better R value compared to XPS, R13 in 2" instead of R10. Polyiso is sometimes derated to R5/inch for cold weather, so even after derating, polyiso is still considered to be the same R value as XPS! I'm hoping to have a test rig working sometime this summer and will post some actual numbers for everyone here about this.
In a basement or crawlspace, your average temperatures are going to be better (higher) than for exterior sheathing, so the cold weather performance of polyiso in this application is less of a concern. I would recommend polyiso in these locations and I've used polyiso in my own basement and crawlspace.
Bill