Interior Insulation for Basement Walls

Hello to all!
I look at internal insulation options for an energy retrofit.
Assuming the R-value meets code, I would like to combine unfaced XPS/EPS and a stud frame with cavity fill (Rockwool) in a compact assembly (just 4″). The seams of the foam boards will be taped to provide a tight layer.
– 2″ of foam
– 2×4″, cavity filled
– 1/2″ gypsum board
Based a bit on Info 511 by BSC
https://www.buildingscience.com/documents/information-sheets/basement-insulation
– Unfaced foam to allow inward drying.
– some condensation can take place on the concrete, the inner face of the foam should stay dry.
I seal the foam towards the slab and it will trap the moisture (condensate). Will that water run down the wall and how to deal with it?
I mean – this is as stated in BSC 511, what I did not find is whether to use some adhesive to fully adhere the foam to the wall to immobilize any condensate there or put it loose against the wall?
If the condensate can’t flow down, the transition to an uninsulated slab would become simpler – less risk of rot to the wooden studs..
Thanks for the advice!
GBA Detail Library
A collection of one thousand construction details organized by climate and house part
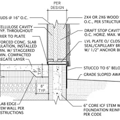
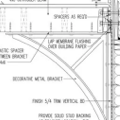
Replies
Their note says "Depending on the component, 0.5 kg / m2 to 1 kg / m2 are permitted.". I take this to mean that .19 kg/m2 is so low that it doesn't run down the face of the concrete.
In new construction, I think it's wise to lap the under-slab poly inside of the foam.
The BSC article you link to is from 2009, Joe has emended his thinking several times since then. His latest thinking is here:
https://www.buildingscience.com/documents/building-science-insights-newsletters/bsi-125-concrete-basement-foundations
Skip to the section "Concrete Basement Foundation With Interior Rigid Insulation."
At one point Joe said he no longer believed basement insulation should be permeable although he's back to recommending it now. His current recommendation is that the foam layer should be 1 perm.
For the life of me I don't understand that recommendation. It's not at all clear where the moisture that is drying through the insulation is coming from. It shouldn't be coming out of the concrete, that should be handled with damp-proofing, a capillary break and a vapor barrier. There's just no way that exterior moisture making its way into the interior is a best practice. If the moisture is there because it came from the interior, it got there in the first place because of the permeability of the assembly, if the foam were impermeable it wouldn't need to be permeable!
I'll add that in a properly constructed wall there is no vapor drive toward the interior. Moisture tends to move from warm to cold and from humid to dry. If the wall is sealed against exterior moisture it should be less humid than the interior. In all seasons the interior of a basement is warmer than the ground below grade. The vapor drive is always to the exterior.
I think Joe's concern is that moisture always seems to find a way in, especially with underground things. The drying recommendation is probably a "just in case" precaution. I personally don't worry about interior drying of the concrete, and have no problem put a crawlspace liner, which is a vapor barrier, up the wall all the way to the top of the masonry. I do check for a capillary break though. I don't think there is any issue using foil faced polyiso, an excellent vapor barrier, or thicker XPS, which is very close to a vapor barrier, on a basement wall, either.
I think Joe goes back and forth between thinking "concrete can be wet, and shouldn't need to dry, so interior impermeable insulation is OK" and "well, moisture is pretty good at finding a way to get in over time, so a little insurance is probably a good idea, so we should allow for a bit of interior side drying ability". It would be interesting to hear from him as to what his reasoning is.
Bill
What I don't have a problem with is saying that if you have fluffy insulation it should be absolutely vapor open to the interior, so that yeah, if moisture does get in there it has a route out and an easy one at that. At the same time there should be a vapor barrier and enough impermeable insulation between the fluffy stuff and the concrete so that condensation is never a problem.
Here is another recent article in GBA regarding basement insulation.
https://www.greenbuildingadvisor.com/article/183793
Poly is used under the slab and the rigid iso insulation is foil faced. I was planning to use this technique for my basement and I agree with Malcom's comment in the article that drainage pipe outside the footing is a must and inside as shown in the drawing is optional.
I don't really get the drying in requirement either if the wall is properly waterproofed on the outside?
Here in summer we cannot ventilate the basement too much because the humidity will condensate on the cold interior suface of the concrete wall. Note this is a house without AC, no de-humidifier- only hydronic heat. To get the humidity out of the basement you use dry days in the shoulder seaons or the winter. (if it is not raining...)
I would like to ventilate in summer without having to worry about condensation. Assuming that no vapor barrier is 100% effective, a bit of drying potential would help.
XPS is rather superior compared to EPS (or ISO) - the condensation rate goes up by a factor using the thickness discussed here with the later ones. 3 or 4" of XPS + glued on drywall would also do the trick - would need a full face glue in all interfaces and a stable XPS..
What climate zone are you in? Unfaced GPS has a much higher perm rating than XPS if you want it to dry through the insulation.
Hi Allan,
CZ is 4, mind - cologne area/Germany..
The GPS will allow more humidity to contact the concrete. Yes, drying will also improve, but spec. in spring the wall will be more wet till the concrete wall has heated up enough.