Basement wall insulation dilemma

So our “Final Home” is moving right along here in Asheville, NC, and we’ve incorporated numerous ideas and tips from GBA into the design.
The good news is that the framers moved much faster than anticipated. The bad news is that they framed out the inside perimeter basement walls, which they weren’t supposed to do.
Our plan – and the way the house was quoted – was for the inside perimeter basement walls to be left as bare poured concrete. Then, we were going to install foil faced foam panels against the poured concrete wall, thoroughly air seal those sheets to each other and to the concrete wall, and THEN stud out the inside perimeter walls, add rock wool insulation, and cover everything with paperless drywall.
We cannot add insulation to the outside of the poured walls, as they will be covered with a rain screen and 3 part stucco in the same plane as the upper floor. So, we need input on the best way to insulate/moisture seal the already studded basement walls – from the inside.
The “cut and cobble” approach doesn’t sound viable based on everyone’s experiences. Closed cell foam is a possibility, but is expensive and environmentally unfriendly. We met with the insulation contractor today, and he recommended fiberglass batts??? I even suggested tearing out the stud walls and doing the job the way we originally planned. Are we making too big a deal out of this?
Any and all advice is appreciated. Thanks in advance!
GBA Detail Library
A collection of one thousand construction details organized by climate and house part
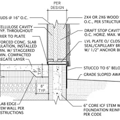
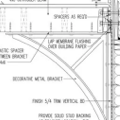
Replies
Fiber insulation in contact with the foundation will wick moisture. It's better to have at least some vapor retardency and a capillary break between the concrete and fiber insulation to be better able to control the humidity range inside the wall cavities.
Cut'n'cobble will probably work here. Concrete isn't damaged by moisture, unlike a wood sheathed wall or roof which are potentially damaged wherever the cut'n'cobble leaks a bit of air. But it's a lot of work.
A flash inch of HFO blown closed cell foam would run $1.25-1.50 per square foot, and would be sufficient to skip any interior side vapor retarders. Filling the remaining 2.5" of cavity depth with compressed R11-R15 (or 3.0" thick soundproofing/fireproofing rock wool batts) would bring the performance up to above code min, but it would still be lower performance than a half-inch of foil faced polyiso or EPS and a 2x4/R15 wall despite having a somewhat higher center-cavity R.
Stud edges in contact with the concrete could still wick moisture from the concrete, but as long as there's nothing more vapor retardent than latex paint between the fiber insulation and interior it' will have substantial drying capacity, and risk is low. If it's possible to slip some foil tape or polyethylene between the framing & concrete before spraying the closed cell (or cut'n'cobble) it would mitigate the wicking risk.
Or, you could hold the line and make them follow the plan.
Thanks for the reply Dana. The framers did leave 1/4" to 1/2" of space between the studs and the concrete walls. Would we be better off slipping a polyethylene sheet behind the studs before having the closed cell foam blown in - even though there is no contact between the studs and the cement? Or should we just insist that the insulation company pay great attention to spraying behind those studs as much as possible?
Skip the polyethylene sheeting. If the installers "picture frame" the cavity, spraying the perimeter of the framing to ensure foam gets into that 1/4-1/2" gap before spraying the center it will be fine. Even if it misses in a few spots 1/4" of air is a pretty good capillary break- moisture can't wick directly from the concrete to the wood through an air gap.
Nancy,
Dana gave you good advice. Remember: Whatever you decide to do, it sounds like you are negotiating for a way to fix a contractor error. When a contractor makes an error, the costs associated with the resolution of the error should be borne by the contractor.
To add to what Martin said, the general rule with design and construction is if the builders build to the drawing and the drawing is wrong, the costs to correct the error are borne by the designer (Architect, engineer, etc.). If the drawing is correct, and the contractor doesn’t build what is drawn, the costs to correct the error are borne by the contractor.
Assuming you have a written quote that included the set of drawings that were quoted, you should have an easy time arguing that the contractors made the mistake and they need to fix it. If you are using a general contractor, have them deal with the framing subcontractor for you. If you are using an architect, they can probably help you too.
Don’t just “let it slide”, make sure what is built is correct and what you need. Its a huge deal trying to get anything fixed after the project is completed.
Bill