Basement wall insulation

Hello
I’m planning to finish my basement, starting in a couple of weeks. I’ve been spending the last 6 months, at least, trying to figuring out what’s the best way to do it. I read everything possible but the more I read the more confused I get. And that’s why I decided to ask here.
my House was built in the 1940s. Basement walls are dry. Actually the basement in general looks very dry. Temperature without heating is always constant (64/66 degrees in winter time and 68/70 in summer). In summer time I need to run the dehumidifier other ways humidity will be around 75%. The previous owner painted some walls with an oil paint, I started scraping parts that became loose. Beyond the paint there was no moisture.
in some spots (the one not painted) there’s some efflorescence that I’m vacuuming once every 5/6 month.
I want to start with the best insulation for the wall and then I’m gonna concentrate on the rest.
I’m planning to use rigid foam for the walls and then metal studs and gypsum board at the end (leaving the cavity empty)
Do I need to paint the walls before using rigid foam? If yes, which paint?
Wich rigid foam insulation is the best way to go (this is where I’m really scared to make a mistake)? EPS or XPS?
I know that EPS will be vapor permeance while XPS will completale seal the wall.
for me would make more sense to let the wall to transpire but maybe I’m wrong.
Please help me make the right choice.
Thank you
angelo
GBA Detail Library
A collection of one thousand construction details organized by climate and house part
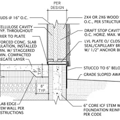
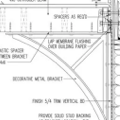
Replies
Hi Angelo.
Concrete walls do not need to be able to dry. If permeance matters here, it is because it might be beneficial to keep moist basement air from reaching the concrete wall where it could condense. However, your best defense against that problem is air sealing. EPS is a much more environmentally friendly choice. So, just make sure to air seal the panels well with sealants and tape and the perimeter and seams and continue to keep basement relative humidity in check.
Thank you Brian,
So if I understand correctly XPS would be the best choice in my case but less environmental friendly, correct?
I would like to go with the environmental one. Which EPS would you recommend? I saw one at Home Depot that has both sides with a plastic sheet in one and aluminum in the other. Those foils are easily pealing off in case the eps needs to be without any foil.
>"EPS or XPS? "
EPS for sure, but for environmental, not vapor permeance reasons:
https://materialspalette.org/wp-content/uploads/2018/08/CSMP-Insulation_090919-01.png
XPS eventually falls to the same performance of EPS as it's climate damaging blowing agents dissipate out over the decades.
>"I know that EPS will be vapor permeance while XPS will completale seal the wall."
What you "...know..." happens to be not so. EPS is only somewhat vapor permeable- even at a skinny 1" it's at the low end of Class-III vapor retardency, comparable to a couple coats of interior latex paint. At thicknesses of 2" or more it's considerably less permeable than interior latex paint. An XPS is nowhere near true vapor barrier status.
XPS of similar thickness & density is only about half or slightly less than the vapor permeance of EPS. At similar density and labeled R-value *rather than thickness) it's still more than half the vapor permeance. EG: 2" of 1.5lbs per cubic foot density XPS is labeled R10, and runs between 0.6-0.8 perms. 2.5" of 1.5lbs density EPS is less than 1.2 perms, typically ~ 1 perm, the boundary of Class-II and Class-III vapor retardnency. At 3" EPS at that density would qualify as a "vapour barrier" under Canadian building code definitions.
Thank you Dana for the explanation. I definitely will go with the EPS. I just have to figure out if I need the one with plastic foil on one side and reflective in the other like the one that I attached to my previous post.
Summarizing the results from Joe Lstiburek and also here: drying to the interior reduces mold risk, use unfaced EPS.
Thank you Jon!
What about this product:
https://www.homedepot.com/p/R-Tech-1-in-x-4-ft-x-8-ft-R-3-85-Insulating-Sheathing-320821/202532854
When you say your 1940's basement walls are generally dry, so are my 1970's poured walls Angelo Ds.. But its in the spring that occasionally water gets pushed right up the perimeter crack and floods the place after a hard rain. The jackleg contractor who built my addition screwed up.
Anyway, unless you have a walkout basement I think your wasting time and money on "finishing" it. Just a little advice from someone who thought their basement wouldn't flood.
You may also want to leave a inch or two of wall exposed so you can see if any bugs have used the foam as a tunnel to your home. And a 1/2" gap at the bottom so than any standing water wont wick into the new wall assembly.
Thank you Mike,
Yes I thought about leaving a couple of inches at the top to inspect for bugs.
I never found water in the basement. That’s the reason why I’m ready to finish it but I’m very confused on the first most important step: wall insulation
Should I seal the walls with a sealer like drylock before? Or do you suggest somenthing different?
I found this one:
https://www.homedepot.com/p/Zinsser-3-gal-WaterTite-Mold-and-Mildew-Proof-White-Oil-Based-Waterproofing-Paint-5003/205156866