Basement vapour barrier
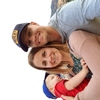
Hi,
Brand new to the site and first want to say “ what a goldmine of building knowledge”! My question is about a recent article I read regarding insulating basement walls. On a current build of mine, I’m trying to adopt some of the teachings here by installing 2” eps rigid foam to the foundation walls sealed at every joint and seam. 2 pound closed cell will fill my joists spaces and tie into the rigid foam. Then 2×4 frost walls in front of the eps with R15 batts. Next, we are expected to apply a 6mil polyethylene vb fully taped and sealed with acoustical sealant as per code. With that said, an article I read by Martin Holladay simply says the poly is a bad idea. He explains it well and I understand but the City inspectors will not pass inspection without it. I’m thinking of using Certainteed Membrain? Any suggestions would be greatly appreciated.
Thanks!
Paul (Freezing in Climate Zone 8 – Northwest Canada)
GBA Detail Library
A collection of one thousand construction details organized by climate and house part
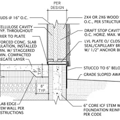
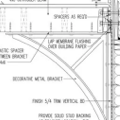
Replies
If you are forced by the inspector to use a vapor barrier, see if a vapor barrier paint is acceptable. If not, an adaptive vapor barrier like Membrain or Intello would be my next choice.
Paul,
You should be able to explain to a building inspector -- even a Canadian one -- that a below-grade wall is not the same as an above-grade wall. Even a Canadian building inspector might be made to understand the fact 2 inches of EPS is already a vapor retarder (or, if you prefer, a vapour retarder).
But if logic fails, a so-called "smart" retarder is better than polyethylene.
At 2" most common densities of EPS would not meet the NBC code definition of "vapour barrier" (which is 60 ng/Pa-s-m2 , just over 1 US perm = 57 ng/Pa-s-m2 ) without a facer of some type. Unfaced Type-II (1.5lbs per cubic foot nominal density) would run about 75-85 ng/Pa-s-m2 at 2" thickness.
But any density EPS with a plastic or foil facer would comply unless specifically designed for higher permeance.
But for climate zone 8, the ~R8-R8.5-ish 2" of EPS is inadequate for dew point control on R15 fiber insulation. R10 would meet the letter of code minimum prescriptive in the US, but R12+ would be better, and even WITH 2-mil nylon (MemBrain) going with 3" of EPS would be advisable in that stackup.
For the record, what is location/postcode (for climate data purposes only)?
Hi Dana,
Sorry for not responding! I honestly did not see the email until I was just cleaing out my inbox today. Anyway, after meeting with a local energy consultant regarding a new job, I found out I'm actually in Zone 7A according to her. Edmonton, AB, Canada. I was planning on using "Durofoam" from Plastifab (2") adhered and sealed to foundation wall with R14 batt insulation in front. This will give me R21.5 according to the manufacturer with a perm rating of 0.5.
Here is the link for the product;
https://www.plastifab.com/pdf/technical-library/pibs/plastifab/PIB%20232%20-%20DuroFoam%20Insulation%20-
%20NBC%202005%20Insulating%20Sheathing%20Installation%20Requirements.pdf
Thanks again for your responses.
The link doesn't work without some cutting & pasting, but the data sheet indicates R3.75/inch, so you'd have R7.5 @ 2" (more at colder temps). That's a bit marginal for dew point control on R14 batts in zone 7A, but maybe enough. Bumping up to their~50% higher density Type-II "DuroFoam Plus would give you R8.1, and a little bit better margin. (And R22+ at center-cavity.)
The facers on this product line reduce the vapor permeance to ~0.5 perms, which is fine, but you don't want to go a LOT lower than that.
[edited to insert: The following discussion was about above grade framed walls much of which is less pertinent. I neglected to review the thread prior to posting. Mea culpa! But the principle is still valid- there won't be significant moisture accumulation at the foam/fiber boundary in either above-grade or below grade portion of the wall. ]
See figured 24 through 27 in this document, in particular the plots labeled ' International Falls- 2" ' and ' International Falls- 1" '
https://buildingscience.com/sites/default/files/migrate/pdf/BA-1313_Moisture%20Durablity%20with%20Vapor%20Permeable%20Insulating%20Sheathing.pdf
In that set of simulations they used highly permeable R4/inch rock wool, but adjusted the drying rate to the exterior by the vapor permeance of the housewrap (WRB). The cavity insulation was R13, and standard interior latex paint on gyprock as the interior vapor retarder. In Figure 26 you can see that the peak moisture content of the interior side of the sheathing will still be under 15% independent of vapor retardency, which is fine, but at only 1" it would be 18%, which would be high enough to allow dry rot to get started. That's the peak seasonal moisture content, on the interior side of the sheathing. Looking a Figure 24 at the half-perm mark (where your chosen foam will be) you'll see that the exterior side peak moisture content stays under 10%, which is good.
The annual average moisture content at half perm, 2" would be under 10% for both interior and exterior sides of the sheathing, as seen in Figures 25 & 27.
Print out that PDF for yourself- you may need it to get the inspectors on board with skipping the interior side polyethylene, but worst-case, install 2 mil nylon (MemBrain), not polyethylene.
Thanks Dana. This info is very helpful!
Paul