Basement insulation questions
Preparing to finish a currently unfinished basement in Chicago (Zone 5). Ideally we would have used pre-extruded foam on the walls, however when the home was originally build the main plumbing drain lines were installed tight to the foundation walls and reworking these is too cost prohibitive.
With this said our installer is suggesting 3″ of closed-cell spray foam for an R21. Code is R15, is their suggestion worth the potential extra cost?
The other question is in several areas we our walls are several feet from the foundation due to water services, sump/ejector pits, or other plumbing obstructions. These areas can’t be sprayed, can’t spray in main copper supply and or village meter, nor can rigid foam insulation be added. What is the suggestion for insulation in these instances?
Thanks
GBA Detail Library
A collection of one thousand construction details organized by climate and house part
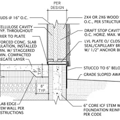
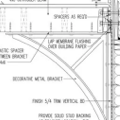
Replies
2.5" - 3" of reclaimed roofing polyiso, using FrothPak or can foam to insulate and fill in between the plumbing and foundation could be a lot cheaper if done as a DIY. Don't install any insulation between the plumbing and the basement space or it'll freeze, but DO insulate between the pipes and foundation to the extent possible. (Encapsulating the pipes in closed cell spray foam would all but guarantee freeze-up.)
Possible sources of used foam:
https://chicago.craigslist.org/sox/mad/d/brighton-used-poly-iso-insulation-sold/6942970738.html
https://chicago.craigslist.org/search/sss?query=rigid+insulation
If you're building a studwall in front of it, you could get away with 1" polyiso and R13s in the stud bays.
I did my basement (in a comparable climate) with 3" of reclaimed roofing foam strapped in place with 1x4 furring through screwed to the foundation with masonry screws. Due to the history of minor basement flooding I stopped the polyiso a few inches above the slab, above the high tide mark. Even in a dry basement, keep the cut edge of the polyiso from contacting the slab, to prevent ground moisture and any wall seepage finding it's way down the wall from wicking into the foam. If the high-tide mark is fairly high, use only EPS or XPS from the slab up to a few inches above that mark.
If it's literally impossible to insulate around some sections without re-plumbing, leave those sections alone. It's fine to install uninsulated partition walls around them, but don't insulate between those areas an the interior, since that would raise the freeze up risk.
Insulating above grade walls to R15 or higher makes good sense. On a $/r-value basis there is a diminishing return in that each additional inch buys less benefit, so R15 might be satisfactory depending on how many square feet etc. There may be some air sealing benefit to choosing spray foam over board foam, especially if you have stone or block rather than cement.
On below grade walls and floor, insulation is about preventing condensation in summer rather than avoiding heat loss in the winter, since ambient ground temps are already close to room temp. If you need below grade air sealing that's a different story, but in any case you'd only need an inch of spray foam below grade anyway.
Building Science Corp has some helpful reports on how to fix basements. https://www.buildingscience.com/
>"On below grade walls and floor, insulation is about preventing condensation in summer rather than avoiding heat loss in the winter, since ambient ground temps are already close to room temp."
Not really. It's more about energy use.
Deep subsoil temps in user-7371062's Chicago area are about 50- 52F:
https://www.builditsolar.com/Projects/Cooling/US-ground-temps.gif
A 52F room temperature in a semi-conditioned basis would represent a significant heat load for the first floor.
Shallower soil temps have seasonal swings around the deep subsoil temperature, with winter season averages reaching temperatures significantly lower than the deep subsoil temps even as deep as 5' below grade:
https://www.builditsolar.com/Projects/Cooling/US-ground-temps.gif
In Chicago the 32F frost depths often extend to more than 3 feet below grade. Room temperature isn't anywhere near 32F unless you live in an igloo, ( which is hard to do in Chicago, given how warm it is the rest of the year. :-) )
For US climate zone 5 (Chicago included) or cooler, the current IRC code minimum is R15 continuous insulation for the entire basement wall (including below grade). Code minimum is the crummiest house that's legal to build.
If using cheaper materials & methods such as reclaimed roofing foam there can be a lifecycle rationale for something higher than that even on a net present value of future energy savings basis, but most people balance that against the loss of interior space too. At 3" the labeled R-value of roofing polyiso is about R17, foil faced polyiso would be about R18.