Basement insulation for a 1930 house retrofit (wall and slab)
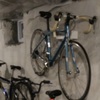
Greetings:
The northern Massachusetts house where I am now living had some very bad energy efficiency characteristics when we moved in last summer. These included:
* a poorly insulated attic with an HVAC system in the cold zone
* an uninsulated basement with 18 inch thick fieldstone walls
Last December we took care of the problem with the attic by installing closed cell spray foam insulation. I got some great advice in this forum — see https://www.greenbuildingadvisor.com/search/node/1930 . Now the attic is toasty and the house is less drafty.
However we have yet to tackle the basement . We now need to address it, because we now have VERY cold floors in the downstairs. In fact, due to the thermal mass of the basement walls we expect to have cold floors well into May, even when temps outside are in the low 70s. Certainly some insulation under the floor may be needed. One contractor also recommended a second heating system dedicated to the first floor. I don’t really want to do this, it seems like a waste to have two heating systems in a house that is 1800 sq. ft.
I would also like to get more use out of the basement for a workshop and for storage. Currently it is a damp space with 60% humidity in the winter (temperatures in the low 40s) and 100% humidity in the summer (keeping a fan going lowers the humidity, but it is almost too damp to dehumidify). If we don’t do something to warm up the basement floor and/or walls the humidity alone will eventually rot the house.
My first question is on replacing the basement slab, which is only 3″ thick and crumbling. I have a quote to dig the whole basement down a foot, and then pour a more proper floating 6 inch slab with drainage underneath. This would have the effect of lowering the basement a bit. My contractor said nothing about under slab insulation or thermal bridging to separate the slab from the cold wall. Has anyone ever tried to add an insulated slab — or a heated slab — as a retrofit in such an old house?
My second question is on insulating the fieldstone wall. I am reluctant to insulate from the inside as I don’t want to trap the water from the spring thaw in the wall. The downslope portion of the house has the fieldstone wall 60% exposed so I would potentially like to do cover that from the outside — it makes this part of the house very cold almost froze our sewer line. But digging below grade to insulate (we have a 3′ frost depth) all around the house would be expensive.
I think it makes sense for us to try things with the greatest chance of success, so I am wondering if anyone has an idea what we should try first — tackle the slab or tackle the wall? And should we insulate underslab or not, and should we insulate the fieldstone wall or not?
Thanks in advance for all your suggestions,
Rich
GBA Detail Library
A collection of one thousand construction details organized by climate and house part
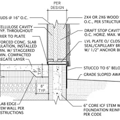
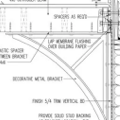
Replies
Rich,
The first thing you should do is neither slab replacement nor wall insulation. The first thing you should do is to try to reduce the amount of moisture in the basement.
The work might include changing the grade around the house so that the soil slopes away from the foundation; installing a swale on the uphill side of your house, with the swale draining away from the foundation; and installing roof gutters connected to a conductor pipe that conveys the water away from the foundation.
Then you can tackle the walls next. In an old house like yours, you might have to install a French drain at the perimeter of the inside of your basement walls, draining to a sump. Then you may have to install a dimple mat against your walls, with the bottom of the dimple mat leading to the French drain. Once you've done that, you can install closed-cell spray polyurethane foam on your walls.
The slab comes last. And yes, you need continuous horizontal foam insulation under your new slab.
Martin --
We already changed the grade around the house, in May of last year. Removed 160 yards of earth from the back yard! Then we installed a well drained stone patio in the backyard which gently slopes away from the house to an area that is 30" above the driveway. There is a walkway of crushed stone leading the water down towards the driveway. Finally, on the wet side of the house, we installed roof gutters and downspout extensions.
The difference between last year and this year is huge. We had efflorescence (white crystals) on the back wall last year. Three of the four walls were very wet (15 inches of rain in 1 week helped). This year the back wall is totally dry as are the other walls, so far. We are coming to the peak of the frost melt and it has not rained very much at all during this period.
As for the interior french drain -- we did have our mason contractor put one in under the rear wall in the basement. FYI, he found standing water 20 inches below the top of the slab. The drain slopes toward an area under the driveway and it will not be fully functional until we excavate the driveway and add pipe. The stone in the drain is exposed, so as soon as there is water in there it will be easy to see as the rocks will get wet. As of now, the stone is still dry, so it leads me to believe that the drain will only be needed in extremely wet situations, as we had last March.
So the idea of a dimple mat against the rear wall is interesting. This would direct water downward if it was really wet, but I question whether that wall is wet enough to "catch" any liquid now.
Can we assume for now that the walls are going to be dry in the winter and early spring? Only in the summer (when outside air with dew points above 55 degrees causes condensation) will the walls be a problem.
Also, I tend to regard spray foam in the basement as a last resort. Once the spray foam is applied, we no longer have access to the walls to assess their condition or do any touchup masonry work. Is there any data on the durability of fieldstone when insulation is applied to the inside vs leaving them alone (or insulating on the outside)?
I think we are at the stage where the slab deserves attention (I didn't give all the detail before because the post would have been too long). A new slab will not let in as much moisture in the winter and spring. What is recommended for insulation thickness? 2 inches? Do we need thermal breaks on the edges? Even if we insulate, there is a 4 x 4 area we poured last spring to support the center column which rests directly on the earth, does this matter? Thanks.
You may have seen this, but this is an interesting paper concerning insulating rubble foundations, freeze thaw and drainage issues.
http://www.buildingscience.com/documents/insights/bsi-045-double-rubble-toil-trouble/
Thanks for this link, it is very useful and helps to dispel some of my fears about insulating the walls from the inside.
I now think we will ultimately go with a combination of aproaches, including:
1) opening up the outlet to the drain (It looks like it is getting water now, so I might dig down tomorrow to see if there is standing water at the bottom and siphon it out as a temporary fix).
2) improving the drainage on the wet side of the building and perhaps adding an "insulation skirt" on the other side to keep more heat in the ground where the foundation is half above-ground
3) we may do an addition (garage) next to the lowest corner of the house, which could protect and warm the wall that is most exposed now
If we do all this, plus the new slab, I wonder what kind of temperature gain we could expect in the basement?
And in the places where we have 5 or 6 feet of exposed fieldstone (held together with mortar mix and concrete), is there anything we can do to the outside of the structure to protect it from the extreme cold or is that a waste of money?
Rich,
Q. "In the places where we have 5 or 6 feet of exposed fieldstone (held together with mortar mix and concrete), is there anything we can do to the outside of the structure to protect it from the extreme cold?"
A. Sure. It's certainly possible to insulate the exterior of your foundation wall with closed-cell spray polyurethane foam, provided you don't mind the change in appearance. The foam would need to be protected by stucco, and I'm not sure exactly how the lath would be attached -- but it can be done.
Your most beneficial and cheapest
move, is to insulate under the ground
floor. While little heat is lost
downwards via conduction, radiation
and convection insulating between the
joists will eliminate the losses by
convection. Filling the spaces
between the joists with polystyrene
will make the room above feel warmer.
You will still have the losses by
radiation, not much. If you have the
head room, fitting a two or three inch
thick layer of tightly butted
polystyrene across the basement
ceiling, will stop the heat loss by
conduction.
You write that the basement has a
relative humidity during the winter of
60% at 40 degrees fahrenheit.
This level of humidity at this
temperature is in fact low, almost dry.
This does not require and attention.
You write that you have 100% humidity
during the summer - but do not provide
the relevant temperature.... that makes
this comment pointless.
The thing is, that at temperatures
below 40f there is hardly any water
vapor in the air, it is to all intents dry.
There is no possibility of the water
vapor in the basement rotting the
house. Water vapor always moves
from warm wet air to the nearest cold
surface, you have already mentioned
that the walls are cold....presumably in
comparison to the ceiling, therefore
all the water vapor in the air will
condense onto or into these walls in
preference to anywhere else.
Did you raise the possibility of using
the basement as a work shop?
Did you mention that you would
perhaps like to add heating to the
basement?
Breaking up the existing floor and
replacing it with a new concrete slab
is quite common as people seek to
expand their living space.
There is no reason why you should not
dig down and after taking care not to
go below the foundations, level the
ground and cover with four inches of
tightly butted polystyrene, covered in
turn with a plastic waterproof
membrane, topped by steel reinforcing
mesh with pex under floor heating tied
to the mesh covered with three or four
inches of concrete. Make sure you
add an upturn of polystyrene at least
two inches thick round the perimeter of
the slab to help stop the flow of heat
into the walls.
Under floor heating takes some time to
heat up, and then you will lose a lot of
your heat into the walls.
If you are only to use the basement
from time to time, a better and cheaper
way is to install a quartz radiant heater
that will be cheap to buy, cost nothing
to fit and be very cheap to run as long
as its pointing directly at you.
Why would you want to add drainage
under the slab? Water always finds the
easy way out, it will be easier and
cheaper to lower the front of the
basement to let any water flow out the
front and away downhill.
In response to Martin -- the idea of closed cell on the exterior is interesting... I don't know if the masons around here have experience putting stucco on top of closed cell but the building is overdue for stuccoing anyway. I like the idea! Would this eliminate the need for adding closed cell to seal the rim joists or would this be in addition to that?
Roger -- thanks for the long response.
On humidity levels, you are correct; it was dry but maybe I overstated how dry in my first post. Actually the measurement of 60% humidity was the minimum recorded in the fall... when basement temps were in the low 50s. I do recall it going up after that but I didn't record it as I was not concerned about mold with such low temps. As of today the spring moisture has saturated at least 10% of the basement floor and is starting to be moist -- humidity reads 75% at 50 degrees. Still far better than last spring, when any piece of cardboard left in the basement overnight would get saturated with water.
On the basement slab issue, our mason said he would normally put crushed stone under the slab as a drainage base. I guess that this is normal with the clay soil that we have; do you have any recommendation on how much crush stone to use? He was talking about adding 6" of concrete, so are you suggesting that using a foam base, you can use less concrete? I do like the under of under slab heating... it would be a bit extravagant for us to heat the basement to room temp, or 65 degrees, but it would be great to be able to warm the temps from 45 to 55 (or in the summer from 62 to 70 to fix our moisture issues). I have read that 5/8 inch tubing is recommended for a basement floor and we could always hook it up later.
As for the basement ceiling, the gas utility company in MA has a program to help insulate and they will cover most of the costs. I don't think that polystyrene would be a great choice though, because of the difficulty of installation (gaps are not standard and there is a lot in the way). I am hoping we can use some form of batt insulation, perhaps in combination with some kind liquid-applied sealant to reduce air movement, similar to the new Owens Corning Energycompete system.
I have heard some good things about roxul (rock wool) insulation, but before insulating I still need to figure out what to do about weak, aging floor joists. The joists are probably from the 1800s and were reclaimed in order to build the house in 1930. We have some dry rot, some powder post beetle damage, some surface mold,and even termite damage in the uphill corner. I am thinking that we should replace about 20% of the joists, the ones that are most problematic. If there is anything we could spray onto the other joists to increase their life (mildew resistant exterior latex paint?) I would also do that, as I don't want to have to come back in 10 years and redo the whole the ceiling.
Rich
Rich,
Rim joists can be insulated from the interior or the exterior; either way can work fine, as long as the insulation is properly chosen -- for example, interior insulation should not be air-permeable -- and, in the case of exterior insulation, as long as the flashing details are carefully worked out.
Here is my update as of late Sept. 2011:
The basement slab will soon get an overhall, followed by work on the ceiling to add heat (and improve the structure). This week, I am in the process of finishing my basement interior french drain, along with a drywell. Not just any drywell; an insulated drywell.
The french drain in the house, installed in May 2010, has never been connected to anything. To daylight it, I rented an excavator a few days ago and dug a 70 foot trench for 4 inch PVC pipe. Backfilled it today, and waiting for the rain to stop so I can clean up the yard! But the most important thing is that if we get water under our basement (which happens most often in the spring), the drain should bring the water to a new garden, just a few feet from the road in the front of the house.
FYI I incorporated a downspout connection in the pipe. Starting 10 feet away from the house, it is now bringing excess water from a rainwater collection tank to the outlet.
For the outlet, I purchased an inexpensive ($13) pop-up emitter at lowes, which has a large hole at the bottom to release most of the water into a drywell. The drywell will be about four feet cubed, filled with rocks surrounding an old trash can. My plan is to line the sides and top of the drywell, and the top of the last section of drain pipe, with 3 inches of EPS foam. I am hoping that this will allow the rocks to stay near ground temperature, so that the drywell will continue to accept runoff even in the winter. On the top I might use 6 inches of foam for added frost protection.
For the basement, I am leaning towards using just 2 inches of foam under slab, and opting for no radiant heat tubing. The bottom 12" of our basement is currently:
9 inches of soil (clay/sand rock mixture)
3 inches of concrete
I would like to replace this with:
5 inches of crushed stone
2 inches of foam
5 inch concrete
The main factor weighing against radiant heat in the basement is the cost; our house is not THAT big and we really don't want to heat the basement to room temperature. I am thinking it would take a lot of heating energy, or a lot of basement wall spray foam, to make a radiant system really work. Not to mention the upgrades in boiler capacity required. Furthermore, there is already a new support column and footing in the center of the room which we would have to work around.
The only way it might make sense to do radiant in the floor would be to do a small area of the basement that could more easily and economically be protected from the hulking masses of rock and steel surrounding it.
Does this all make sense?
I am also trying to find a contractor to put radiant heat on the ceiling of the basement (well, most of the basement, as there is a section in front that I don't really have to heat). I am still unsure whether this will be cost effective.
Because the fieldstone wall is 16 inches thick and because of a stone divising wall, we only have perhaps 600 square feet out of 900 which would be conducive to radiant heat. The heat will have to travel through two layers of 1 inch pine flooring, 1/2 inches of osb subfloor, and then 3/4 inches of oak to reach the living space above.
Quotes to upgrade the boiler and install radiant heating, thus far, have exceeded the entire heating bill of the house for 2010 (gas and forced hot air) by a factor of 20.
Suggestions and recommendations are welcome.
Rich,
It sounds like you are budget-conscious; most of us are. Improvements to insulation and airtightness are a much better investment than changes to your heating system -- especially if you are budget-conscious.
The details you provided are hard to follow, but it sounds as if you have introduced a system to address water entry into your basement. That's good. You don't mention basement wall insulation. In your climate, it is essential. So the next time your bank account allows it, hire a spray-foam contractor to install closed-cell spray polyurethane foam on the inside of your basement walls.
If you are pouring a new basement slab, of course you should install at least 2 inches of rigid foam under the slab. If I were you, I would reduce the thickness of the crushed-stone layer in order to gain more ceiling height.
thanks Martin --
I agree with you but I am delaying introduction of any spray foam on the walls or rim joists to allow the basement to continue to dry from the inside. If we add spray foam now while the floor is still wet, I am fearful of increasing humidity which is already two high.
On the slab issue I probably should have written this as:
12 inches of soil (clay/sand rock mixture)
3 inches of concrete
REPLACE WITH:
5 inches of crushed stone
2 inches of foam
5 inch concrete
This way we gain three inches. However I would like the ability to dig down less and reduce the risk of collapsing fieldstone!
My mason contractor is accustomed to using 6 inches of concrete and 6 inches of stone -- 1.5" bluestone. If I go with a 4 inch slab and 4 inches of concrete I could gain a lot of headroom but I would then need to provide the specs of the concrete for him, and also be able to justify that the drainage would still work with less rock.
Rich,
Reducing mass. If I were to design a cold climate basement that only is to be heated when rarely used, I would install insulation on top of a slab. And for heat have a radiant heat source that warms the occupants and the smaller amount of room mass that is now roomside of any and all insulation.
As to the cold first floors, an easy DIY project is to install staple up radiant tube heat. Very inexpensive when done via DIY. A water heater DIY installed in the basement run on natural gas would be very economical. As to the floor thickness, you still have your HVAC system providing the main source of heat.
Lastly I would maybe add a radiant feature to the center of the basement on its own circulator to use in bringing up the basement temp to a desired temp above its unheated temp.
Interesting thread....
Rich,
This is a helpful thread for me because I am planning to do similar work to my 1907 limestone foundation wall basement. I wish I had fieldstone ; )
In my area 4" slab pours are standard. If you want an extra inch could just require some extra reinforcing. I would think (or at least hoping for my own home) that creating a proper vapor barrier under the basement slab (a poly membrane on top your rigid foam layer) will reduce the humidity noticeably.
I would recommend insulating around the perimeter of your new poured slab. You'll need to think through how to accomplish this because you don't want the perimeter insulation exposed to damage.
Is radon a problem in your area? You have an opportunity to install a passive vent stack that ties into your gravel drainage layer.
I think there is something to Roger's advice to lightly insulating the basement ceiling. I plan to try this but as you said its a little tricky to execute.
If you are only going to use the basement on a limited basis I think it is overkill to add a heating system. Dress warm and use a small space heater if needed. Another option that is costly but could add value to your home is to add a generous south facing high solar heat gain egress window. You would both improve the quality of the space and employ the thermal mass of slab and walls to your advantage.
hi AJ -- we need to replace the crumbling slab anyway... and if we can replace and insulate the sill I think that we address a major source of the basement cold. The center of the house also sits on a steel beam which is directly resting on the fieldstone wall so I guess we have to be careful about putting heating tubes near the center of the house -- so that heat generated in the floor is not sucked from the floor joists back into this beam!
I do think that radiant tube heat with some simple controls makes sense. I am thinking of cutting gaps in the lowest layer of pine flooring material (cut a 4-6" wide channel in basement ceiling, center of every other joist bay) in order to position the radiant heat tubes closer to the first floor. We would do this to seven joist bays, which means about 300 feet of upside-down cutting with a small circular saw. Then we could use thin reflective radiant material 12 inches wide to cover the channels, and finally insulate with R-15 or more in all of the joist bays.
Does this sound like it would work -- do we need to to include aluminum heat transfer plates and if so how to determine the number of these needed?
Finally, the idea of using a heat pump water heater came up ... I know that these will chill the air but if the air is chilled down in the "cold room" part of the basement which we have no plans to heat (and which has an uninsulated modern slab) then the massive fieldstone wall and the ground will warm that air back up. I know that heat pump water heaters are now coming out which can function in 46 to 50 degree temps (http://www.skylineenergy.com.au/our%20solution.php) but I don't know if this has been tried or is even available in the US. Finally it would be possible for us to move the tank upstairs to the conditioned space while keeping the condenser in the basement.
J Chestnut -- a radon test is something I should probably do, I already have the kit.
As for the poly vapor barrier I was planning to put it under the foam, to better protect the EPS from possible insect activity (termites are an issue but we had the soil treated so no signs of them now). I read elsewhere that it would not really affect the quality of the vapor barrier and as we are using cheaper (EPS) foam that can flake I want to do whatever would keep it intact for 30+ years. Interestingly, I saw a tomato hornworm trying to munch on my exposed foam yesterday when I was insulating the french drain outlet.
A limestone wall -- interesting. I just had the opportunity to examine my wall during excavation for the drain and I noticed that there are many layers to it. A concrete footing on the bottom 12" below the existing floor, with stacked stones almost 23" wide (no mortar on the outside) , and finally there is a 2" thick and 12" wide concrete ledge about a foot below grade where the wall is a mere 18" thick. I didn't excavate more than I had to to avoid collapsing stone, but it appears as if the mortar on the exterior of the wall starts only above this 2" ledge. The ledge happens to be about 30" from the top of the fieldstone in the area I dug up and I don't know if it is intact all the way around the house.
Rich,
Home archaeology is one of my favorite hobbies. Thanks for the description.
Agreed that the poly layer serves its function under the EPS.
Glad to hear you are using EPS versus XPS due to its lower global warming impact.
However if I recall correctly (and I've had these discussions recently) my structural engineer only advices Type IX EPS for use under slabs. It has a higher density and therefore better compressive strength. Type IX isn't the common off the shelf EPS you. Might want to verify this with someone.
The people I bought it from said it was fine for under slab... does it matter that we wont be putting any serious loads on it? The main support column is already on a fresh block of new concrete so it will just be the basement contents. According to insultch-eps.com: "For foundation and wall applications in which EPS bears a minimal load, ASTM C 578-92 Type I EPS material is adequate. The resilience of EPS insulation board provides reasonable absorption of building movement without transferring stress to the outer skins at the joints. In roofing, Type I EPS material provides the dimensional stability and compressive strength necessary to withstand light roof traffic and equipment weight at reasonably high surface temperatures. If greater rigidity and strength are needed, compressive strengths up to 60 psi are available. Please contact us for recommendations regarding your particular application"
Rich,
I'm laid off right now and don't have access to my reference materials at the office. I'm a designer at an architectural firm so structures is not my expertise but I think I might be worth further investigation because -
(1) The ASTM standard you are quoting I suspect is referring to the vertical install of EPS boards outside the foundation walls and not under the slab.
(2) If your mason concrete contractor is sourcing the material they are on the hook for its performance. If you are sourcing the material and you get unsightly cracks in the slab its on you.
Again what I recall for underslab EPS is a recommendation from the structural engineer of type IX and 15psi rings a bell.
hi J Chestnut...
I am curious what the actual load on the EPS will be...
if you look at this, comment, the load on the EPS will be well less than 10 with a 5 inch slab:
passivehousecal.org/eps-not-allowed-under-slabs-cal-energy-code#comment-189
One cubic foot of concrete weighs 144.05 lbs. So a six inch thick block of concrete (1 ft square) would weigh 72 lbs. A 5 inch slab -- about 60 lbs.
I'm not a civil engineer, but I would guess that a square foot of EPS material -- 144 square inches, with density of 12 pounds per square inch, ought to be able to support a lot more than 60 pounds, if the weight is evenly distributed.
Rich: I have a similar basement situation and I shared the exact feelings you had about allowing your walls to dry. In my case, I elected to spray closed cell foam on the inside of my basement walls and rim joists using 2 different DIY foam vendors before modifing the slab. I used one vender to spray the rim joists and the other for the walls due to how each vendor’s spray guns work. Regardless, it was an AMAZING and IMMEDIATE improvement!! Within 24 hours, it dramatically improved the humidity levels where my dehumidifier is now barely running as opposed to almost continuously running. Not only that, but the exhaust from the dehumidifier practically heats the entire 30’ x 26’ basement now. In addition, the common basement musty smell is also gone – that’s a big bonus for my wife! I can’t say enough what an immediate and impactful difference the foam made. I am very glad that that I did this first. I am a true believer now in spray foam insulation and I assume that you will see the same results.
hi Ben -- I should mention that there is at present no access to my basement from the main house. Only an outside entrance. The humidity is well contained at this point, and my lot does not have drainage problems as the house is up on the hill.
There are some structural issues I must consider before spraying the walls... in particular, the east wall (which used to be a porch wall) does not seem solid - it is hollow inside and stones are loose at the top. I plan to add concrete and mortar to shore this up and after that I could use your approach. I still have an 18" "divising wall" in the midst of the basement so the spraying of that is not so simple. It is connected to the main wall at both ends and it is load bearing... It would use a lot of foam or complete removal of the divising wall to get the same results as you. Furthermore, if I do all the insulating from the inside I will lose some space in the basement.
In general, I have a concern that once I spray the walls -- especially the top of the walls -- I will not be able to easily access the sill for replacement of for jacking/leveling purposes.
Did you completely cover the top of the walls and how much spray foam did you use?
I am not against foam by principle, I have already put 5 inches on the roof deck as my post mentioned.
-rich
Hello Rich: Sorry for the delay as I have been consumed in my own excavation of 1800 cubic yards of earth… To answer your question – I completely covered the top of the walls. My mindset is that if I need to access the sill in the future, I’ll simple cut the foam away. For places where I had larger volumes that needed to be filled, I ended up creating a ‘frame’ (non-load bearing of course) using some polyiso from the local big box hardware store and then spraying my polyiso structures with the closed cell foam. I felt that was a good combination of materials to achieve my goals while not breaking the bank by creating a big, expensive pile of spray foam.
Hi Rich,
I have a nearly identical, but slighly older house in Cambridge MA and have undertaken a nearly identical project. It is almost scary how your descriptions and issues are so similar to the issues I have and the solutions I came up with. I had posted a plan with a side view of the wall ando old/ new floors on the plan review section a week before I stumbled upon this thread.
. A few questions: it appears you are (or have) removed about 12 inches of soil...did you get close to the bottom of the foundation? If so, we're you concerned about the structural integrity of the wall while you worked? I am considering putting a curb all around the interior perimeter before I did down..but it seems like such a waste since I will just build the height back up once stone, insulation and concrete are installed.
The other issue was the footings you have in the center. We had several 3x3x3 poured concrete footings poured to support the main beam that runs down the center of the house. Since we knew we were going to lower the floor these are 4-5 inches below the height of the current floor. If we oly lower the floor a net 3 inches these footings will be covered by the new slab. I'm a little concerned that at a minimum the slab will crack over them and worse I'm concerned that the new slab will put downward pressure on these footings. ow did you handle the intersection of the new slab and our older footings?
Jason -- finally, today, I finished adding my new slab. What I ended up doing was a bit atypical but I think people will appreciate some of my methods.
1) I had about 13 inches of material removed (the old 2" cracked slab plus 11" of soil)
2) I removed another 2-3 inches from the perimeter... just wide enough to stick a piece of foam up against the wall in the groove. I cut the sheets of EPS into 3 16" strips and put them against the wall to create a 2 inch buffer between the existing rough fieldstone walls (which were structurally sound and mortared even at this depth, I was surprised) and the new slab.
3) Rather than put the low-quality EPS I purchased under the entire new slab, I just used 16" strips of it and placed them on the ground around the edges (with the smooth edge touching the EPS strips that are in contact with the wall) before the contractor added the crushed stone. So in effect I have an interior insulation skirt which means the slab WILL BE EXPOSED to the ground but the ground temperature it is exposed to will be 50-55 degrees, not the 40-45 degrees that can get into the exterior walls. My goal is to make this a workout and storage room so I don't care if it ends up at 55 to 60 degrees in the winter.
4) in the future I will be able to insulate the walls to remove the spring moisture from the basement if I decide I need to heat the basement further. The base of the walls are quite damp right now due to a problem with my external water tank (not a big deal, it is leaking a bit when it fills up and i can fix that) and the tops of the fieldstone walls are damp today because the due point is over 55 degrees. Summer moisture is less of a problem because the tops of the walls will warm up to 65 degrees
5) we put 3-4 inches of crushed stone, then a double-layer of 6mil polyurethane for a vapor barrier, and finally the contractor put in 5 inches of concrete.
6) I had an old stone wall (divising wall) that went across the entire basement, and which used to be the front of the house. It was a huge task but my contractor took out this entire wall... got rid of a lot of rocks on craigslist also which meant less had to go to the concrete dump.
Removing the old divising wall was critical in order to make it much easier to prevent the cold from the walls from penetrating into the house. Also, the wood on top of the divising wall and some of the wood touching it was rotted. IT is great to get rid of rotted wood.
Removing that wall also gives me some wall space that can be used to put in inverters and control hardware for solar panels, if we decide to move forward with that.
Having done all of this, now I am in a better position to dry-ice-blast my entire basement ceiling and replace some of the dry-rotted joists that contributing to a moldy smell in the basement.
It will be interesting to see if these steps make a big difference in basement temperatures...
7) I am planning to go through with replacement of the current electric resistance water heater with a heat pump version, the Geospring most likely. I know that a lot of people frown on this but the way my basement is currently set up it should work pretty well.
8) I will plan on installing, some time in December, insulation on my basement ceiling. This will give me a chance to see the effect of the insulation before and after. It is likely that I will spray foam the critical areas (including, perhaps, the rim joists and a colder section of the basement that will not sit atop the new slab) but not use spray foam for the entire basement, because there is a lot of wiring that is in the way that I don't want to bury in foam.
The cost of doing all of this work was well under $10,000 so far.
And yes, I do have a lot of photos which I can post if there is interest.
The main benefit, of course, will be additional square footage which is desperately needed because I haven't finished my attic or added a garage as of yet!
Rich,
Thank you for posting the details of your basement insulation. You know we always want to see pictures.
In response to Jason, we hired a structural engineer to advise us on the first footing. He looked at the weight of the house and recommended we use a 3 x 3 footing that is only 1 foot thick. I am guessing that a 3 x 3 x 3 footing was overkill ... unless you had unusually soft ground.
The contractor we hired sought to join the concrete floor with one of the footings, which was poured a bit too high (we didn't know then we were gonna lower the floor as much) but it is very stable because it has had 2 years to settle. The pictures I have will show the footing sticking up from the new slab.
My thinking (non scientific): the concrete as it dries is a very heavy mass and will push everything down. The purpose of the footing as I understand it is just to support the additional point load of your columns. If the floor as a whole is heavy and is tending to sink, well the point load would also push down so the two pieces of concrete mated together will most likely sink uniformly...
In my case the other footings ended up level with the top of the crushed stone... by design. The plastic we used covered the footings and the base of the steel -wrapped column. So in this case the concrete slab will sit on plastic and then the plastic is on top of the small footing which measures around 14" by 14" by 10 inches deep.
You may not care what the slab temp is in winter (despite what it represents in parasitic heat load), but you really should care what the slab temp is in summer, since that determines the mold hazard of anything resting on the slab.
Even 1" of EPS under the slab would have had a reasonable payback period on heating fuel use, and helped the moisture dynamics issue by keeping the slab temps higher during the humid summertime period. (There's a longer term rationale for 2" of EPS at 10 cents per R-foot, but using reclaimed foam even 3-4" is something of a no-brainer, even if your basement is coasting along as 55-60F in winter.) Unless your heat pump water heater is keeping the dew point of the basement air under 50F (the deep subsoil temp ) you'll still get mold on the bottoms of cardboard boxes stored on the uninsulated slab. In summer keeping the dew points that low will likely take more than just the water heater.
Summertime outdoor dew points in MA average in the mid-60s F, so any ventilation air would need to be conditioned for latent load to keep it the moisture levels at the slab reasonable. The basement will still have a mold risk if you allow any paper or wood to remain in contact with the slab, unless you mechanically dehumidify sufficiently to keep the dew point of the air well below the slab temp. Maybe the heat pump water heater will keep up, but I wouldn't count on it. Monitor the basement RH & temp, and track the dew point of the basement air.
Consider this an opportunity lost.
An update and a response to Dana
First, I don't expect much moisture or mold to come from the floor because a general principle we won't store stuff in cardboard boxes. And most of the containers will be up on plastic shelves. As long as we always have access to the floor to sweep or vacuum the dust, mold will not grow.
The bigger concern is the walls. All the way to the end of July they should be colder than the floor. The first 6 to 12 inches is still wet. It has been raining a lot. No moisture coming up from the slab any more, but a lot is coming from the bottom 2 feet of the wall. And the walls can collect dirt and mold spores because they are rough.
Here is my planned solution, already in progress.
a) I had the masons chip away loose mortar, which in one place had turned to sand so we had to make a mess and re-pack the joints with mason mix.
b) After this was done we pressure washed the bottom 3' of the wall, the part that had moisture, to remove some paint.
c) I went over the pressure washed wall and found a few more places needing loose mortar or stones removed. I used half of a 5 gallon bucket worth of mortar to fill these.
d) the very bottom of the wall (just outside or just above the foam bathtub for the concrete) may need to be packed with some hydraulic cement to stop a possible seepage point.
e) I am planning to apply around three 50-lb bags of ThoroSeal to the whole interior wall. This will be a lot of work so I am only planning to coat the lowest 3 feet of the side walls and the lowest 4 feet of the back wall, which are the moisture points. A lot of work, it will need 2 coats applied with a large stiff brush.
f) after this is done my plan is to add a coat of paint to the top portion of the wall just to make it more hygenic.
g) I have a cleaning company coming to cleanse the basement and encapsulate the joists so that they will not be a source of mold spores. I have removed some worst joists which were structurally unsound. The joists will replaced after the cleaners come.
h) epoxy basement floor paint will be applied to the slab to reduce dust. This will be done after the slab has a chance to dry for another day or two... either using the dehumidifier or if it is dry outside, by keeping some fans going continuously.
i) The heat pump water heater was installed yesterday. When we poured the concrete we put a pipe under slab for the condensate drain. You are right that we will still need the dehumidifier... but with the sealed up walls, I am hoping it won't need to run all the time.
You may be interested in the performance of this house, 6 years later...
1) The heat pump water heater definitely reduced the humidity. We run our humidifier for 4 or 5 days a year when there is a prolonged hot-humid spell. That's it.
2) Running the Geospring heat pump makes the basement colder in winter as predicted. From 2013 to 2018 I turned off the heat pump from December to March and used electric resistance heating for hot water. That has increased the electric bill but kept temps in the basement from going below 45 degrees.
The basement is used as storage there is no access from the main house, so the cold temps are not a big issue.
3) In 2018 was able to further separate the basement cold from the main floor, adding 2 inches of closed cell spray foam, and further insulating the ceiling with 3 1/2" batts and a sheet of fire-resistant poly in 2019. No more cold floors!
After doing this, the basement is STILL WARMER than it was in 2017. I am able to run the heat pump water heater in the most efficient mode even in the middle of the winter, with little to no impact on the first floor. The fieldstone walls and the ground are acting as a sink for the cold air, the ground temp on my basement floor seems to be 50 degrees in the winter. The basement floor is connected to the ground but it is separated from the colder walls by foam insulation. If I was in the Berkshires this might not work we are at an elevation of just 200 feet, so ground temps are adequate.
The benefits of sealing the rim joist and replacing my porous sill (on the west wall) have offset any heat loss from running the water heater as a heat pump. Also on very warm days I can open up the basement and run a fan. Back on January 11 we had two days with record temps (mid 60s here, 73 in Boston) and this is likely to happen again in March.
I put together numbers on our energy usage in a new thread. Gas usage continues to decline, though we are using a lot more electricity after installing a Mitsubishi heat pump on the first floor.
What is left is to full re-insulate the exterior of the house, mainly the first floor, because of some major links in the building envelope that allow cold air to penetrate into the floorboards on floor 1 and into the gap between floor 1 and floor 2.
Here is the a new thread with some numbers and a couple photos:
https://www.greenbuildingadvisor.com/question/update-on-1930-house-in-northern-ma-fieldstone-wall-insulating-heat-pump-water-heater-in-basement