Reusing Polyiso Foam for Basement Insulation

All,
Looking for some budget solutions to a basement insulation dilemma: Zone 6, NH, new construction. We’ve ended up into a full basement now, but the GC didn’t provide a strategy to insulate in the budget. Also basement ceiling requires sheetrock now due to i-joists. Now we’re struggling to get a plan together that makes sense ($$).
GC proposes least expensive options as:
1. insulate basement ceiling only, leaving the walls and slab uninsulated or…
2. Add R13 batts in a 2×4 wall (requiring drywall)
My thoughts were to:
1. definitely insulate under the slab (R10)
2. Skip the basement ceiling insulation (we want to condition the basement at some point down the road)
3. 2.5″ Thermax polyiso (R14) on the walls and leave well enough alone.
Another frugal (green?) option – What about used the 2.5″ roofing polyiso for the basement walls? Under the slab? It’s available right down the street from me. If I did that myself it would be VERY reasonable cost-wise, but do I de -rate is because it’s aged? Can it be used under a slab? I would still have to cover it with drywall for code.
Thanks,
GBA Detail Library
A collection of one thousand construction details organized by climate and house part
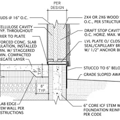
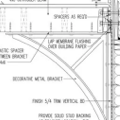
Replies
Re basement ceiling: if you haven't started construction, take a look at TRIFORCE open-web trusses instead of I-joists. These meet the 2015/2018 IRC R302.13 requirement for fire rating if the short trimmable section at one end of the truss is covered with 1/2" gypsum drywall. More details available at http://www.openjoisttriforce.com/fire-rated. Note sure of the cost compared to an I-joist, but eliminating the need for a drywalled ceiling probably saves a good part of the cost difference.
Joists are already up, unfortunately, but yes, it would have been nice to have had a few options to look at. I've seen the Triforce trusses recently as well, around the youtubes and such, and might have been a good option. Thanks for the suggestion.
I have always been intrigued by used foam insulation sheets. From an enviornemental point of view, and cost factor, this seems to be superior to buying new product. With roofing material, I have found that much of it being sold is tapered in thickness so it is a bit harder to work with (perhaps you can double it up, reversing the tapers), but there is material out there with uniform thickness.
One other concern I have had (which is not based in anything but my paranoia) is whether used material may have absorbed harmful chemicals depending on where it comes from and whether it was carefully covered (e.g., interior of a chemical factory or on a roof where it was exposed to a great deal of soot or fumes from exhaust vents or automobile traffic). I suspect this would be minimized if it was covered carefully, but I don't know. I wonder if testing can be done to ascertain if this is an issue or just my imagination. Of course, many of the people selling used sheet insulation also sell new "seconds" that eliminate this issue, and the issue of R value degredation you mention above.
Definetely insulate the basement walls and not the ceiling.
You can't use that roofing polyiso (or any polyiso) under the slab, but you sure can use it on the walls! No need to derate, you can use the listed R value. It's true that the R value does drop a little over time, but it's not severed, and the "derate for the cold" isn't an issue with basement walls that don't see the same severe cold that above grade walls will see.
I would use that roofing polyiso on the basement walls, then run 1/2" drywall right over it (no need for a studwall) to satisfy the thermal barrier code requirement.
BTW, 2.5" polyiso is usually rated R16. The "roofing" types are sometimes rated a little less, but you should still be at least about R14. Note that most areas are probably requiring R15 on the basement walls per code now, so you should check if what you propose will be acceptable. If they want a little more, add some 1/2" polyiso between the masonry and the 2.5" polyiso (this way the thicker sheet helps to hold the thinner sheet flat), which will bring you up to R16-R19 or so, and should satisfy the inspectors.
Bill
jimgove30,
Before contemplating laving the basement unfinished and insulating the floor above, make sure you understand the complications that my flow from that.
Services like water and sewer that have to enter the house below the frost level will need to be kept from freezing, and our code preludes having electrical panels in unconditioned spaces.
>"our code preludes having electrical panels in unconditioned spaces."
I wish our code had that requirement! Panels in garages, and, even worse, outdoors at the meter can, always get corroded inside. Electrical stuff lasts longer and is more reliable in conditoned spaces, and should always be placed in such spaces whenever possible regardless of it being a code requirement or not.
Bill
Thanks for the replies. The idea is that this is outside the original scope of the project, so trying to defer some spiraling costs (like the perimeter wall, more electrical work, etc., etc.) I'm definitely trying to avoid spending good $ after bad. Also, no inspections up there, so I'm the only one really driving code compliance as an issue.
Looks like the best balance of performance, cost and my labor would be:
1. I put down the 2" XPS under the slab and slab edge (Looking at the Foamular NGX 250)
2. I install the 2.5" used polyiso on the walls (adhesive? strap it? hilti-type fasteners or??)
3. skip the basement ceiling
4. build a wall later after construction, or cover with sheetrock as Bill describes above, either using strapping or 2Xs on the flat, or something.
I think I can get this done for under $5K, including poly sheeting, tape, adhesive etc. Seems like money well spent for a comfortable space later on.
As always, thanks so much for the advice.
You can also put drywall over the polyiso with long tapcons if you're careful, you don't need a studwall. If you want to frame the wall, I would use 2x3s on the flat to make room for electricals, use 4" square boxes and mudrings, then mount the drywall to those 2x3s. Secure the 2x3s through the polyiso to the masonry with long tapcons. Note that the drywall is for fire code requirements, so it's not just for a finished appearance here: you will likely be required to install it at the time you install the polyiso.
I like the tap-in hilti insulation fasteners, but there are cheaper options for similar products.
Bill
Understand on the firecode issues. And, we do want electrical in the walls at some point so maybe I can just push it towards the end of the build. It's a delicate balance of project creep and cash flow. Great idea on the 2x3s, thanks.
If you don't have inspections, and none of this is in the GC scope, you can just leave the poured basement wall as is.
Then as you have time, you can install the polyiso and gyp on the walls.
Alternatively, during construction, I'd get the number of one of the installers you meet who seems to care about what they are doing, and hire them to work with you to install the polyiso. Then when the gyp crew is there, find out how much they would charge you direct to come back and hang, tape & finish those basement walls... it is doable, but alot of work.
I installed 2 1/2" used polyiso on my basement wall. I nailed it on with hammer set anchors going thru fender washers to spread the load a little over the polyiso. I used ZipTape to seal all of the seams. I framed the interior with 2x4s ripped in half to give me a good frame for the drywall. The studs were attached to the concrete with long tapcons and screwed into the bottom and top plates with GRKs. The electrical was run using regular boxes with the foam cut out a little to allow them to be set at the right depth.
Your method sounds like a lot of extra work. If you use 2x3s (or 2x4s, but they aren't necassary here) on the flat, you avoid all the ripping, and you end up with a 1.5" deep cavity for electricals. If you now use standard 4" square electrical boxes with mounting wings, which are 1.5" deep, you don't have to carve out the insulation to make things fit. You can finish with mud rings on the 4" square boxes, which will bring single or double gang (either work with a 4" square box) device openings up flush with the surface of your drywall, and you can get those mud rings in a range of thicknesses to allow for different thicknesses of drywall.
There is no need to rip down lumber, and no need to carve the insulation. Anchoring the "studs" with long tapcons is the way to go though.
Bill
When my choice is 10 minutes with the Unisaw vs. spending almost 2x for materials, I'm choosing the Unisaw. Regarding the electrical, it is a finished space. I'd rather see a 2x4 cover on a single duplex receptacle or switch rather than a double cover for a single receptacle or switch and again, the time required if I need a larger 2x4 box based on the number of connectors in the box, I'm happy to carve out some foam, since it is my time is worth it to me. If I was hiring someone, the path forward would be very different.
You can get single gang mud rings for 4" square boxes. This means single gang devices still have single gang cover plates, even with a 4" square box. Pretty much every commercial building is wired this way, so whenever you see a single switch on the wall, if you took that out, you'd find a 4" square box behind it almost every time, just with a single gang mudring. What you end up with is a single gang opening in the wall, but you can reach around inside the box behind it. This gives more space for connections, so it's nicer to work with.
You do NOT have to use double gang plates everywhere. A mud ring is not a cover plate, it is a sort of adapter that goes on the 4" square box to give a device opening through the drywall. Very handy, used commercially nearly exclusively, but rarely seen in residential projects.
Bill
> Very handy, used commercially nearly exclusively, but rarely seen in residential projects.
Unless you're the sort of person who enjoys basking in the luxurious box fill of a 2 1/8" deep 4" box for a single receptacle. This is my personal equivalent of "I enjoy the finer things in life."
Standard 4" square boxes are only 1.5" deep, which is why I recommend them for these "studs on the flat" type walls. The 2-1/8" deep boxes are the so-called "deep" boxes. I wouldn't use those here, although they are common commercially. I tend to spec the deep boxes where there are multiple devices, since it makes things easier.
Ultimately you can build the way you want, but saving on labor is usually a good thing.
Bill
I will continue to recommend Insofast (https://www.insofast.com) for basement walls as it really is a time (and therefore money) saver.
For those that haven't seen it, it's an EPS product with embedded plastic "studs" for hanging drywall. It has integral channels for running electric, and it comes in interlocking panels sized small enough to be shipped via normal means.