Basement with exterior rock wool (Comfort Board) and dampproofing

I am building a new construction home in northern New Jersey in climate zone 5.
On the exterior of the basement wall I plan on installing four inches of Rock Wool Comfortboard 80 to meet the R15 insulation requirements. The four inches would cover from the top of the footings to the top of the rim joists. On the remainder of the exterior framed wall, I plan on installing two inches of Comfortboard due to budget limits.
Question #1:
Since the Comfortboard is a draining rigid insulation,
does it alone satisfy the dampproofing requirements of the International Residential Building Code as “other approved methods”.
I obtained the idea from “Builder’s Guide to Cold Climates”, Joseph Lstiburek, 2016.
Figure 7.27 on page 213 shows a basement wall configuration
mentions this setup on page 189 under the “Moisture” section of Chapter 7.
I like this idea because the vapor pressure points to the exterior since the wall is warmer than
the outside; this may improve the air quality in the home.
Question #2:
I have considered using only two inches on the exterior of the basement wall, so that
the interface between the foundation wall and framed portion of the home is on the same plane.
However, his does not meet the R15 requirement for basements. Could I additionally use two inches of Comfort board on the inside without worrying about condensation just as on the above grade framed portion of the home. I prefer not to use rigid foam due to possibilities of off-gassing. The following article applies to framed walls:
Thank you.
GBA Detail Library
A collection of one thousand construction details organized by climate and house part
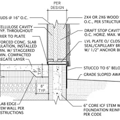
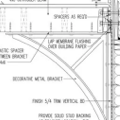
Replies
"the wall is warmer than the outside"
If you have no other insulation, what happens when the AC is on and the above grade portion of the wall is cooler than the outside dew point?
I agree with you, this part of the wall will be cooler when the AC is on.
But this is a small fraction of the wall (most of it is below grade)
for a smaller fraction of the year in this climate zone. My thinking is that the net vapor drive
is outward in a year.
Just be sure to select the outside covering for the insulation such that it doesn't allow air or much vapor to pass through to the cool wall. Vapor movement + condensation moves a lot of heat.
"I prefer not to use rigid foam due to possibilities of off-gassing."
What possiblities of outgassing?
Unlike site-blown spray foam, rigid foam is manufactured under controlled conditions, within a fairly narrow range of mixture levels & temperatures. This reduces the offgassing potential to a very miniscule amount.
OK, "miniscule" isn't precisely zero- you need to use a logarithmic scale to describe it, but it's never zero. But it continues to decline logarithmically from that already low level over time. If using foam that has been reclaimed from building re-roofing/demolition, the material has typically spent several years or even decades in service, and the bulk of any residual outgassing will have already happened.
In new construction the outgassing of turpenes from the framing lumber & wood sheathing are a FAR bigger health risks and indoor air quality issue than outgassing from new or used rigid foam located on the exterior side of the sheathing or foundation.
Above grade the direction of the vapor pressure changes with the season- it's not always from the interior toward the exterior, and it can be in the other direction even when the outdoor temperature is lower than the indoor temperature. The more relevant temperatures are the indoor & outdoor DEW POINT temperatures or wet bulb temps, not the air temperature. Below grade you don't really care about condensation/adsorption of moisture in the concrete- it can take it.
When installing insulation on a poured concrete foundation there is an energy use and peak load benefit to the thermal mass of the concrete, if at least half of the insulation is on the exterior side. If you installed 2-3" of reclaimed roofing EPS on the exterior side of the foundation (where any outgassing is to the soil outdoors, with very little coming through a mostly gas-tight concrete wall) and 1.5-2" on the interior it would perform slightly better than putting all of it on the exterior, or at a 50/50 split.
Using the same thickness foam on the exterior of the framed wall gives a continuous thermal break over the foundation sill & band joist. Wood sheathing with taped seams is nearly as gas-tight as a concrete wall, and any residual outgassing goes to the outdoors. Using reclaimed polyiso on the exterior of the framed wall is preferable to EPS, due to it's higher thermal performance, but also it's favorable performance in the event of a fire (though not as favorable as rock wool). Polyiso has a higher kindling temperature than EPS, and it doesn't melt even when fully engulfed. Using EPDM flashing tape to form Z-flashing at the transition from EPS to polyiso is a low thermal bridging way to divert any bulk water that makes it behind the polyiso to the exterior.
Other considerations: The cost of used foam board is a small fraction of the cost of new foam and WAY cheaper than semi-rigid rock wool. Using reclaimed foam is also a lot greener than using newly manufactured insulation (of any type).
Dana,
Thank you for taking the time to respond.
I prefer the mineral wool because (1) it is vapor permeable, (2) it doesn't burn, (3) it is chemically stable, and (4) it doesn't have the flame retarding chemicals that the foam would need. I would like the home to be able to dry in both directions.
Concrete walls can never drys toward the ground- it's always the other direction, and foam can't burn when between soil & concrete.
With that much exterior-R above grade there is no need for the assembly to dry toward the exterior.
If used only on the exterior there is no way for any chemicals in the foam to end up indoors.
Re-using existing materials does less environmental damage than virgin-stock rock wool.
"Concrete walls can never drys toward the ground- it's always the other direction, and foam can't burn when between soil & concrete."
In my question above, I cited the following from Lstiburek's "Bulider's Guide to Cold Climates", page 189:
"This approach can also be applied to foundation walls that are insulated
on the exterior. By warming the foundation walls relative to the ground,
the moisture moves outwards into the ground. Again, the exterior insula-
tion must not be a major vapor retarder, and dampproofing cannot be
installed. The exterior insulation used must also be a capillary break and
provide drainage. Only rigid fiberglass, rock and slag wool insulation
have these two properties. All other rigid insulations used on the exte-
rior of foundation walls should be used with dampproofing."
David,
Joe Lstiburek has admitted that his statements in that book were erroneous. For more information on this topic, see "Joe Lstiburek Discusses Basement Insulation and Vapor Retarders."
A change in the vertical plane of the foundation vs. framed wall may not matter, depending on your finish materials, if they are different for foundation and framed wall.
I would worry about termites with continuous foam or rock wool from below grade all the way up the wall. At the top of the foundation you may need a termite barrier (e.g., flashing or termite screen products from the top of the foundation out to the exterior surface). Sometimes code or inspectors require a gap (or a removable band of insulation?) at the top of the foundation wall, to inspect for termite tunnels. You may have already planned something...what? I don't like the thermal bridge of flashing or a termite barrier product, but can't think of any better way to avoid it and stop termites.
Robert,
Thanks for responding.
I am aware that I need a termite shield at the top of the concrete wall.
I'm trying to figure out these details. I plan on installing cultured stone veneer on the bottom 2 feet of the wall; above the veneer I will have fiber cement cladding. I will use 1x4 furring between the exterior cladding/veneer and rigid rockwool. The veneer will overlap the concrete and framed portion of the wall. Any recommendations on the details are welcome.
I have looked at this site regarding the details for the foundation:
https://foundationhandbook.ornl.gov/handbook/section2-1.shtml
David,
Q. "Since the Comfortboard is a draining rigid insulation, does it alone satisfy the dampproofing requirements of the International Residential Building Code as 'other approved methods'?”
A. On this question, I advise you to read "Using a Dimple Mat to Keep a Basement Wall Dry." Specifically, you should scroll down to the section of the article with the heading, "If the concrete is covered by a dimple mat, do you also need asphaltic dampproofing?"
Some building scientists, including Joe Lstiburek, feel that asphaltic dampproofing is a waste of money if you have a dimple mat -- and functionally, exterior rock wool performs similarly to a dimple mat. But Joe Lstiburek's opinion (or my opinion) doesn't matter at all in this situation. The only opinion that matters is the opinion of your local code enforcement authority. Different code officials interpret the code differently.
Q. "Could I additionally use two inches of Comfort board on the inside without worrying about condensation just as on the above grade framed portion of the home?"
A. Yes. The article you cited ("Calculating the Minimum Thickness of Rigid Foam Sheathing") doesn't apply to your situation, since concrete isn't harmed by moisture. Your concrete will never rot. It doesn't matter one bit if your concrete wall is damp.
Martin,
Thank you for your answers.
I have read "Using a Dimple Mat to Keep a Basement Wall Dry" before posting my question. The dimple mats listed there are rated for dampproofing. I have called RockWool and spoke to the building scientist. His reply in an email is, "I did take a look at Joe’s detail. However, at this point, ROCKWOOL recommend the use of dampproofing". It seems that I will need to use the argument that Comfortboard drains in a similar way to a dimple mat in order to convince the local code enforcement official.
As a follow up to your answer on my second question, do you see a potential problem with mold / wall performance if I go with 2 inches on the exterior and 2 inches on the interior of Comfortboard? Or is it better to have all 4 inches on the exterior? I don't see much savings
by splitting the insulation, but it is aesthetically better to have the foundation wall
on the same plane as the framing on the exterior. In the future I plan on framing the basement with 2x4 walls.
I'm still seeking advice on the second part of my questions. Is it risky to use 2 inches of Comfortboard on the interior and 2 inches on the exterior of the basement wall
with 2x4 framed walls on the inside? That is a a ratio of .50; I understand that concrete and mineral wool can be wet, but any condensed water that passes through the insulation would be problematic. Is a dew point calculation needed to answer this?
The solution to keep all 4 inches on the outside is presenting problems with the
choice of exterior cladding over some of the exposed concrete wall. Splitting
the insulation might be easier to implement.
David,
In Climate Zone 5, you'll probably be OK if you split the insulation 50-50.
Thank you. I will leave the exterior : interior split of 2" : 2" as the highest ratio split.
Maybe 3" : 1 " will be possible which would perform better.
I would like to cover up the insulation with stucco / stone veneer; the thickness of insulation will depend on the length of concrete anchors that I can find for the cement backer board.
You don't have to use a cement backer board system. A wire mesh system can also be successful for the stucco/stone veneer portions. Reinforcement with plastic lath (Permalath) will prevent corrosion below grade. Of course, you still have to anchor it to the concrete. You can get Tapcons of just about any length, and they do come in 410 stainless steel (pricey) They would be suitable as-is for cement board, and with washers for Permalath.
Also be careful with your selection of cement backer board. Many of them are not rated for below grade use. Most synthetic stone veneers are also not rated for below grade use. Since the cladding is primarily a cosmetic covering and not part of the weatherproofing for the house, some local jurisdictions won't particularly care about this, but the products may not be entirely durable below grade. In my experience, ice melter exposure is far more of an issue with these products than soil moisture, so limit the use of these materials near your claddings.
It is also important to have a clean and well-drained break in the cladding systems at the top of the foundation. Above the break is your wall cladding. Below the break is "parging." Or at least that's the theory.
Thank you Peter.
Maybe I should start a thread on this topic.
I will consider your suggestion if I don't plan on using stone veneer.
What about a rainscreen for the Lathe system? Would it be better to have one,
even over the concrete? My thinking is that it's better to allow the cladding
and insulation dry for durability and effectiveness of the insulation.
For stone veneer, I would think that the backer board would provide strength for the cladding. I also thought the use of cement board could simplify the installation and would require less labor. Using cement fiber board for veneer, lathe is not required and only 1 coat of modified mortar is needed.
My plan is to maintain 4" clearance above grade of the cladding per installation guide for stone veneer; I don't know of any stone veneer that is rated for ground contact.
I could use flashing to cover up the 4" clearance.
I attached a top view of my current plan with furring over concrete.
Concrete anchors longer than 6 inches would be required for 4 inches of rigid insulation. the anchors must withstand the torque imparted by the weight of the cladding. To address this problem, I have 2x4 vertical lumber installed on the concrete
to provide the fastening base for the cladding and reduce the moment arm on the fasteners.
Any comments / suggestions are appreciated.
David, I found this thread very helpful. How did everything turn out for you?
David
How did the local inspector react to using the rockwool as drainage?