Basement – calculating interior insulation R-Value with exterior foundation insulation

Newer home (less than 5 years old) on boarder of zones 6A & 7A. Has existing exterior foundation insulation of R10 that is a ridged fiberglass. Full basement (i.e. all underground) in expansive/poor draining soil. Foundation is around 8″ thick and slab is not insulated.
Plan is to attach foam board that is well sealed for air movement directly to the foundation.
I’m being particularly dense as the articles I’ve read so far have not “clicked” for me on how to consider exterior insulation along with interior. Thus far I’ve considered it one system R10 exterior + R5 interior = about R15 total. But I’m afraid that is naive and could lead to putting too little insulation on interior and lead to some sort of unintended consequence.
Finally to my questions:
A) Have I missed an article that spells this out?
B) If not, then can I consider the interior + exterior as one?
C) Or since interior insulation will move the foundation outside the envelope is it better to ignore the exterior insulation?
GBA Detail Library
A collection of one thousand construction details organized by climate and house part
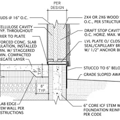
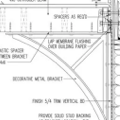
Replies
Adding interior insulation does not move the foundation outside the thermal envelope. If you added R10 to the inside, then the foundation would be in the middle of the thermal envelope. And yes, you can generally add R values, so if you added R-10 inside to the R-10 outside, you would get R-20. This is a simplification, but not too bad. There will be edge effects that slightly affect the overall R-value, but not too much in your case.
In your climate, another R-10 or so on the interior would be worthwhile. I generally specify Dow Thermax for this purpose, as the foil facing is air/vapor proof and Thermax doesn't require a fire barrier like most other foams do. A good quality foil tape also sticks really well to the Thermax for sealing the seams. You can use construction adhesive to glue it to the foundation walls, so you don't even need fasteners. One caveat: Thermax uses polyiso for its foam, and this will soak up water if it gets wet. If there's any chance that your basement will get water on the floor, it makes sense to use XPS or EPS foam like a "baseboard" for a few inches to keep the Thermax out of the range of minor flooding.
And finally, you should pay attention to the band joist and sill areas. Most builders do not treat this area very well, and most likely there is just some fiberglass batt stuffed into the cavities. If so, you should remove it and apply spray foam from the underside of the subfloor, across the band joist, and onto the top of the Thermax to make a continuous air/moisture barrier. Use at least 4" of closed cell foam for this area.
Does the existing, exterior insulation extend to the top of the foundation wall? Around here it's often cut off at grade, which makes for tricky calculations. But if the concrete is totally covered, then like Peter says, you just add the individual R-values. There is a slight thermal mass effect but it's not enough to justify thinking about.
If this is in Minnesota, be aware that MN code for foundation insulation is at odds with the IRC standard, putting limits on the amount of interior insulation allowed. It has changed a few times over the years, but I believe this is current:
http://www.dli.mn.gov/sites/default/files/pdf/section-R402-basement-walls.pdf
...or maybe this is:
https://www.revisor.mn.gov/rules/1322.0402/
...or this:
https://shop.iccsafe.org/media/wysiwyg/material/5356S20-Sample_Re_1.pdf (Note that per R402.1.1.5 interior rigid foam on foundations in MN have to be sealed with acoustic sealant, not polyurethane caulk, not can foam.)
If the exterior insulation doesn't reach all the way to the foundation sill plate, but stops at grade leaving the above-grade foundation exposed, it's worth installing R15 on the interior (assuming you don't end up picking a fight with code enforcers.)
Peter & Michael thank you for the replies!
Fortunately the band joist and sill areas are spray foamed. A visual inspection of visible areas implies it is continuous and sufficiently thick. That said I'll inspect closer when I drop the current ceiling to run utilities. Regarding exterior insulation, it does extend to top of foundation wall.
I had not considered Thermax but the benefits certainly seem appealing. Although water hasn't been an issue I'd probably run XPS/EPS as a baseboard for peace of mind.
Related question, if ~90% of the foundation is covered in well sealed continuous insulation on the interior will the last 10% which remains uninsulated be an issue other than for comfort and increased heat loss? For instance in a utility/storage room or behind stairs.
Insulation tends to improve things wherever it's added in this type of situation, so that uninsulated portion will still lose energy, but you'll reduce energy loss in all the areas that you DO insulate, so you'll come out ahead overall. You'll just end up with a colder area near the uninsulated part of the basement. The new insulation in some areas won't make the uninsulated areas lose any more heat than they did before.
Bill
Bill, thank you for clarifying that point. Knowing that and after talking with the building inspector (more details in my reply to Dana below) my current plan is to add R10 to the majority of the perimeter of the interior.
Dana, yes this is in MN and I was disappointed when I realized MN did not adopt IRC standards. Particularly because none of the big, though not necessarily national, builders refused to exceed code when it came to insulation - even though I would pay.
The local building inspector has at least been responsive to me though my question about adding interior insulation only received a "you meet code and it's not needed". I'll try again now that I know what R value to go after and with your links (and this site) be a bit better informed.
Good luck!
A few years ago I was advising a MN dweller in a similar situation, where they had installed 1" of polyiso against the foundation trapped in place with a 2x4/R13 (kraft facers) studwall. He managed to get a variance, but only because the inspector was fairly cooperative. In his case the exterior R10 insulation stopped at grade, and it really NEEDED something above grade for comfort & thermal performance. Even though R13+ R6 doesn't cut it for dew point control at the polyiso's interior side facer in zone 6, inspection after the first winter season did not show any mold issues (YMMV).
If the above grade exterior on your house is uninsulated and they want to hold you to the letter of code, installing 1.5" of interior polyiso (R9-R10) up to about a foot below grade level, with 2.5" (R15-R16) or even 3" polyiso the rest of the way up to the top should still fly. The thermal bridge of a partially exposed foundation is significant, undercutting the overall heating season performance, but exterior-only-up-to-grade partial insulation still does a decent job of keeping the foundation wall above the summertime outdoor dew points, keeping the musty basement smell at bay. If you have at least R10 on the interior below grade, and R15-R20 on the interior above grade (the coldest part of the wall in winter), heating season thermal performance is still decent.
Follow up - Building inspector said R10 on interior is fine by them since the house already meets MN code minimum of R10 (in this case on exterior from footer to top of foundation including above grade portion). I also referenced the code sections you (Dana) supplied (thanks!) about use of acoustic sealant and how to deal with the fact that slab to top of foundation is 8’ 2”. Meaning there will be a 2” gap somewhere. Which either won’t be filled - such as leaving gap between slab and bottom of insulation and thus not being able to put acoustic sealant on slab and bottom edge of insulation as specified in code - or if I could simply fill that gap in with canned foam. They didn't directly answer my question but essentially stated it doesn’t matter to them what I do since, again, all they care about is that the R10 minimum is met.
So looks like I’ll be doing continuous R10-ish against the interior perimeter. Planning to glue the foam board with something like PL300. To address the extra 2" of foundation height does it seem reasonable just to fill in with canned spray foam?
2" is a pretty big gap to fill with just canned foam, but you could probably do it in several passes. If you try to fill the entire gap in one pass, the canned foam will probably not cure properly and will leave voids. I would try a pass along the top of the gap, and a bass along the bottom of the gap, then fill in the middle as needed. Be sure to use one of the "big gap" variants for this. I prefer Loctite's Tite Foam for this kind of thing, since it makes a denser finished product, but it is a good bit more expensive than great stuff. Tite Foam will probably do a little better with such a big gap too, based on my own experience with both products.
Another option would be to cut a strip of EPS or XPS to put in the middle of the gap, leaving around 3/8" or so gap on either side, then just fill those two gaps with canned foam to seal things. Either way works, just be careful if doing the entire gap with canned foam so that you can proper curing. A SLIGHT mist of water prior to foaming might help too.
Bill
jaykay,
You mentioned your band joist is already spray foamed? This doesn't lap onto the wall I assume, but does it completely cover the top of the foundation wall?
I would think about this transition from wall foam to the top-of-foundation/band joist foam s0 that it is continuous. Perhaps this has some bearing on how you handle your 2" gap.
If you do end up cutting strips of foam, there are lots of options out there, but one I liked that isn't often mentioned is to use a jigsaw with a smooth/wavy blade (soft materials blade such as BOSCH T313AW3). Worked well on EPS anyways. Probably not the method that will yield the squarest cuts, but for rough fill-in strips or any curved work it works quick and painless.
Bill & maine_taylor - thanks. I hadn't thought about gap size as it relates to canned foam.
I too had considered ripping strips but it sounded tedious compared to just canned foam. That said, with the size of the gap and the point maine_taylor made about band joist being covered but still needing to make a connection between that foam and the wall foam board - Maybe I leave the 2" gap (due to foam board vs foundation height) at the top of the wall and use a froth-pak to fill in that space between band joist and wall foam.