Barn floor without concrete

I’ll consider this a green question since it’s using recycled XPS. I scored 25 sheets of 3″ DOW Deckmate Plus last year. Here’s the thread. https://www.greenbuildingadvisor.com/community/forum/green-products-and-materials/60826/advice-needed-recycled-xps-rigid-foam
These were intended for a house but I only managed to erect a 36×56 pole barn with an aggregate “floor”. (house may start next spring) I’d like to section off a part of the barn to furnish as a shop and use the ceiling as a loft for storage of some light items.
Is it reasonable to simply tamp and level additional aggregate on the area of interest, place this DOW insulation down and stand a wall on top of it? Is the compressive strength strong enough to support a sill plate, wall, and loft above?
For those with inquiring minds, my plan is to finish off the interior space with interlocking garage floor tiles, maybe with a sheet of luan underneath to distribute the tile’s bite and prevent the tile ribs from cutting into the XPS.
GBA Detail Library
A collection of one thousand construction details organized by climate and house part
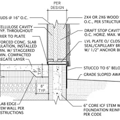
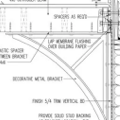
Replies
Drew,
It's an interesting question. Most XPS has a compressive strength of 25 psi, which is similar to good soil.
That said, most of us don't support walls on soil without a footing.
There are two issues here. One is frost heaving. You haven't told us your climate zone. Nor have you told us whether this barn will be heated. But you don't want the soil under the rigid foam to freeze, and you need a plan to prevent that.
The other issue concerns the weight that these walls will bear. If the loads are large enough, the bottom plate of the walls will dig into the rigid foam.
I'm in zone 6.
What intrigues me is that standard practice around here would be to add aggregate, tamp & level, then pour 4" of concrete without any foundational work. Individuals seem to do this in pole barns all around me without anything heaving. Some may add a "rat wall" around the perimeter but I believe that's for pest control concerns, but maybe I'm incorrect in my perception of this purpose.
So at this point, I am trying to understand why it would be different to substitute the concrete with foam? Is it because the ground soil will heave more unevenly than an entire concrete slab and if this happens under foam then the foam will break?
Here is a link to a previous thread where a home without a slab was briefly mentioned. There is a PDF link that shows the detail.
https://www.greenbuildingadvisor.com/community/forum/general-questions/100857/minnesota-architects
Very interesting, thank you for sharing. So it appears my concept is valid, but what happens without a frost wall? I won't have one. My walls will be in 16' from the exterior walls. I'm not sure if that helps though. I'll simply hang a ledger board along the inside of the exterior walls to complete the room.
In the Minnesota house example, i see the Interior wall is sitting on wood over foam. Although that wall isn't structural, I am beginning to believe that what I would like to accomplish is within reach if I install a vapor barrier and top everything with plywood. Does anyone agree?
Drew,
Check out this discussion: http://www.hansenpolebuildings.com/2011/10/preventing_frost_heaves_in_pole_building_construction/
It sounds like the safe approach is to install your poles starting below the frost line. It also seems prudent to remove any silty or expansive soils that are within the footprint. (Expansive soils may not be an issue in your area, of course.)
If you decide to go forward without a slab, you might want to incorporate a layer of geogrid into your aggregate layer. (This is just a WAG.) Geogrid can add a lot of strength to the aggregate layer and reduce the need for an excessive thick layer of stone. You might want to talk to a geotechnical engineer on this point and see what he/she says.